|
|
Журнал |
|
Архив |
|
Подписка |
|
Реклама |
|
САММИТ |
|
Книжная полка |
|
Контакты |
|
В начало |
|
|
|
| |
|
|
 |
№5' 2004 |
версия для печати
|
|
ДИНАМИКА РАЗВИТИЯ ОТРАСЛИ И ПУТИ РЕШЕНИЯ ПРОБЛЕМ |
|
АНАТОЛИЙ СЫСОЕВ
Генеральный директор Богословского алюминиевого завода
филиала ОАО «СУАЛ», президент АМРОС
сновой овладения разнообразными информационными технологиями и их эффективным использованием является образование. Профессиональная подготовка позволяет человеку утвердиться как личности, участвовать в приумножении культурных и научных ценностей. Главной же движущей силой, определяющей развитие постиндустриального общества, становится информация. Одним из способов ее донесения, приобретения дополнительных знаний является и наша постоянно действующая научно-практическая конференция «Алюминий Урала». За 9 лет на ней побывало более 3000 участников. Был представлен весь цвет металлургической науки России: 400 ученых, в том числе 60 академиков, профессоров, докторов и кандидатов наук из различных областей знаний техники, информатики, экономики и управления.
Алюминиевая отрасль России устойчиво развивается (табл. 1). Ее достижения стали возможны благодаря технической мысли инженеров и ученых. Рост объемов производства и технических показателей достигнут за счет совершенствования технологии, внедрения новой техники, роста квалификации управленцев, инженеров, рабочих, повышения технологической дисциплины.
С 1992 года по 2003 год добыча бокситов увеличилась 4578 тыс. т до 5442 тыс. т, производство глинозема с 2719 тыс. т до 3231 тыс. т, алюминия с 2745 тыс. т до 3478 тыс. т (рис. 1). Большинство заводов перекрыло проектные мощности по глинозему и алюминию. Резко вырос выход по току: верхний токоподвод с 8285 % до 88 %, боковой токоподвод с 85 % до 91,2 %, обожженные аноды с 86 % до 90,6 %. Снизились расходные коэффициенты: по анодной массе с 560 кг/т до 488490 кг/т, по свежим фторсолям с 60 кг/т до 24 кг/т, по технологической электроэнергии в постоянном токе с 16800 кВт . ч/т до 15400 кВт . ч/т. Отдельные заводы снизили расход до 14700 кВт . ч/т.
Постоянно наращивает свои показатели Богословский алюминиевый завод филиал ОАО «СУАЛ». Производство глинозема увеличилось с 914 тыс. т в 1997 году до 1078 тыс. т в 2003 году (рис. 2) при проектной мощности 930 тыс. т. А в 2004 году намечено выпустить 1100 тыс. т глинозема. За тот же период производство алюминия выросло со 146,6 тыс. т до 182,6 тыс. т (рис. 3) при проектной мощности 152,7 тыс. т. Выпуск алюминиевых порошков в 2003 году составил 9,7 тыс. т. В 2004 году этот показатель вырастет до 16,1 тыс. т.
БАЗ-СУАЛ достиг наивысших показателей по выходу по току и прочно удерживает первенство. За 2003 год выход по току составил 91,2 %. Для сравнения лучшие показатели по другим заводам: ИркАЗ (верхний токоподвод) 89,4 %, УАЗ (боковой токоподвод) 90,6 %, СаАЗ (обожженные аноды) 90,6 %.
Внедрение комплекса мероприятий в рамках интенсивной технологии электролиза дало возможность стабилизировать энергетический баланс на серии электролиза за счет внедрения АСУ «Ток серии», приборов Холла, АСУ ТП «Электра» и подбора состава электролита, благодаря чему удалось снизить температуру электролита и ликвидуса с одновременным увеличением перегрева электролита. Все это позволило поднять силу тока с 74,5 кА до 83 кА. При этом рост объема производства опережает рост электропотребления (рис. 4).
В истории алюминиевой промышленности это уникальный случай, когда одновременно с подъемом силы тока на 11,4 % увеличен выход по току с 85 % до 91,2 %, т. е. на 6,2 %.
Основные направления работ в глиноземном производстве:
получение крупнозернистого глинозема;
использование бокситов Тиманского месторождения;
снижение расходных коэффициентов;
совершенствование конструкций технологических аппаратов для увеличения единичной мощности.
Большое внимание уделялось повышению качества анодной массы. Проведена работа по подбору сырья и его оптимальной шихтовки. Это привело к снижению содержания примесей в алюминии-сырце и способствовало улучшению его сортности. Использование качественного сырья отечественных и зарубежных производителей позволило снизить разрушаемость анодной массы и соответственно ее расход в процессе электролиза.
В 2003 году достигнуты следующие качественные показатели: зольность 0,3 %, разрушаемость 35,0 мг/см2ч, механическая прочность 531 кг/см2. Вся анодная масса выпущена высшей маркой АМС-0.
Инвестиции в производство на Богословском алюминиевом заводе составили в 2003 году 433,2 млн руб., в 2004-м предполагается вложить 785,1 млн руб. (рис. 5). Разработана Программа технического развития до 2010 года. Она предусматривает коренную реконструкцию предприятия.
1. Перевод на обожженные аноды действующих мощностей электролизного производства с увеличением производственной мощности до 240 тыс. т.
2. Строительство БАЗ-2 с вводом новых мощностей производства алюминия (300 тыс.т.) и созданием общей мощности завода в 540 тыс. т алюминия в год.
3. Доведение мощностей глиноземного производства до 1500 тыс. т за счет строительства более мощных производств на декомпозиции, автоклавном выщелачивании, сгущении, выпарке, кальцинации с увеличением скорости потока.
Программа развития глиноземного производства предусматривает поэтапную реконструкцию. На первом этапе строятся новые мощности, затем сносятся старые и на их месте сооружаются аппараты с единичной мощностью в 23 раза больше существующих.
Высокой оценкой нашей работы стали награды, полученные предприятием. Характерная особенность деятельности Богословского алюминиевого завода его социальная ориентированность. Постоянно растет объем инвестиций на эти цели (рис. 6). БАЗ единственное в России предприятие, трижды в 2000, 2001 и 2002 годах победившее во Всероссийском конкурсе «Российская организация высокой социальной эффективности». Шесть лет подряд с 1995 по 2002 годы завод является победителем конкурса «Лидер в бизнесе» по Свердловской области. В 2003 и 2004 годах победитель конкурса «Евразия: лидер в бизнесе», проводимого на федеральном уровне. В 1998 и 2001 годах «Лучший российский экспортер» (Министерство внешних экономических связей и торговли РФ). В 2000 году получен «Золотой сертификат доверия» (Министерство РФ по налогам и сборам) за внесение весомого вклада в развитие экономики России и Свердловской области, как лучшему налогоплательщику Свердловской области. В 1999, 2000 и 2002 годах получен «Российский национальный Олимп» (Правительство РФ, РСПП) за успехи в экономической и социальной сферах.
Итоги работы алюминиевой промышленности в целом и Богословского алюминиевого завода в частности за последние 10 лет показали, что электролизное производство в рамках существующих конструкций электролизеров и электролизных серий добилось серьезных успехов прежде всего в росте технических показателей, таких, как выход по току, срок службы, качество алюминия-сырца, снижение расходных коэффициентов по электроэнергии, свежим фторсолям, анодной массе. Значительно улучшилась технологическая дисциплина, решены вопросы обработки электролизеров по потоку, улучшились условия труда, снизились выбросы в атмосферу, повысилась квалификация рабочих, мастеров и старших мастеров, руководителей цехов.
Практически не было серьезных ограничений по энергоресурсам, обеспечению сырьем, рабочей силой. Хорошей работе цехов электролиза способствовала система компромиссов между алюминщиками, энергетиками и администрациями регионов.
Цены на энергоресурсы в долларовом исчислении практически не росли или росли незначительно. Рынок сбыта алюминия был обеспечен, прежде всего, за счет экспортных и толлинговых операций.
Это в прошлом. Что нас ждет в будущем, через 510 лет? Прежде всего резкое изменение ценовой политики, приближение к мировым ценам и затратам на производство алюминия по основным составляющим себестоимости энергоресурсам, трудозатратам, сырью и материалам, штрафным санкциям за вредные выбросы.
В таблице 2 даны затраты в себестоимости алюминия отечественных предприятий и западных фирм. Если в декабре 2003 года российские компании в целом опережали зарубежные по уровню себестоимости, то в ближайшие годы этот показатель у нас значительно ухудшится по каждому из видов затрат: сырью, электроэнергии, трудозатратам, экологическим платежам и др. Таким образом, если мы не выработаем программу мер для решения этих проблем, то через 510 лет станем неконкурентоспособны западным фирмам. На сносное житье осталось не более 35 лет. Это время надо максимально использовать
На первый план выходят решения, которые лежат в области управления бизнесом. При этом надо понимать, что на фоне медленно растущей экономики в ближайшие 5 лет не будет никаких значительных изменений, как не будет и серьезных вложений в инвестиционные программы по переходу на обожженные аноды, строительству цехов по производству обожженных анодов. Последние потребуют инвестиции, исчисляемые в десятках миллиардов долларов.
Поэтому мы должны выработать систему небольших инвестиций и больших усилий по улучшению работы цехов электролиза, использованию человеческого фактора, внедрению информационных технологий, ориентации на людей, их профессионализм, коллективизм. Высокопрофессиональный работник должен стать «штучным товаром». Необходимо усиление процесса достижения лучших результатов на будущее, а не на кратковременную прибыль, иначе мы упустим время.
Первая проблема качество людских ресурсов. Для его повышения требуется провести комплекс важных мер.
1. Разработка общеобразовательных программ. Необходимо создать специализированные подразделения по переобучению кадров, повысив и как техническую подготовку, так и управленческую культуру, сформировать при компаниях преподавательские центры, используя дистанционное обучение работников.
2. Формирование идеологии, кодекса предприятия. Критерием оценки трудового коллектива должны стать дисциплина, управление во времени, развитие навыков, степень участия и вовлеченность в производство, моральные качества, коммуникабельность.
3. Улучшение способа мышления, связанного со стандартом качества производства, поддержания высоких результатов посредством мелких, но постепенных улучшений и нововведений. Рабочие отвечают за поддержание стандарта качества, управляющие за их улучшение.
4. Взаимосвязанная стимуляция труда при улучшении личной, домашней, общественной и рабочей жизни.
Надо твердо понять, что разваливают компании, заводы, корпуса, цехи, участки не какие-то внешние силы, а сами рабочие, причем себе во вред. «Враг сидит внутри нас» и люди теряют работу, останавливают производства, уменьшают себе доходы, так как не знают других способов решить свои проблемы. И никто не пытается их научить.
Коллективный договор на 20012003 годы и новый, на 20042005 годы на БАЗе приняты без обсуждения и практически единогласно, потому что в цехах с делегатами конференции была проведена большая работа, людям показали расчеты, объяснили последствия для завода и самих работников тех или иных принимаемых решений.
Поэтому главный фактор, который мы должны использовать, это люди. Необходимо, в частности, изучить опыт японцев, системы ремонта оборудования голландцев, алюминиевых заводов других западных фирм.
Здесь на первый план выходят информационные технологии в производстве и системе учета финансовых и экономических показателей.
Сегодня сделаны первые шаги в управлении сериями электролиза, однако мы значительно отстаем по управлению технологическим режимом глиноземного производства. Мы будем вынуждены через 35 лет платить электролизнику 10001500 долл. в месяц, а глиноземщику 6001200 долл. Но в себестоимости продукции резервов уже нет. Повышать зарплату можно только за счет сокращения численности работающих в 23 раза. Вообще, проблема стоимости трудовых ресурсов может быть решена только за счет уменьшения численности персонала, создания «безлюдных» технологий, уменьшения контрольных и наблюдательных функций. Словом, нужна новая система управления производством.
Вторая проблема рост цен на энергоресурсы. Для ее решения надо уже сейчас проводить анализ причин увеличения затрат, в том числе за счет роста цен, и находить пути снижения неэффективных издержек.
В ближайшие годы нас ждет энергетический кризис как по производству электроэнергии, так и по ее передаче. Раздробление РАО «ЕЭС России» приведет к смене владельцев, к непредсказуемости поведения участников рынка. Поэтому необходимо разрабатывать методики ценообразования, новые законы по защите потребителя от произвола новых акционеров энергетических компаний, проникающих в управляющие органы путем приобретения части акций. Нужны теоретические работы по энергетическим балансам систем (серий электролиза, производства анодной массы, глинозема). Сегодня составляются балансы по агрегатам, прежде всего по электролизеру, но практически отсутствуют тепловые энергетические балансы по глиноземному производству (автоклавные и выпарные батареи, печи спекания и кальцинации).
Третья проблема усиление контроля и увеличение доли штрафных санкций за вредные выбросы. Сегодня требуются новые методические разработки по расчетам вредных выбросов, их оперативная корректировка. Существующая методика в основе своей опирается на когда-то выполненные балансы по выбросам. Затем она определенным образом корректируется по мере снижения расходных коэффициентов и строительства газоочистных сооружений.
Принятая система газоочисток очень дорогая, сложно настраиваемая. Раньше, лет 50 назад, были методики расчета расходных коэффициентов, разработанные ВАМИ, но сегодня их на большинстве заводов нет.
Четвертая проблема совершенствование технологий, конструкции, способов обслуживания электролизных серий и глиноземного производства. Необходимы разработки методик диагностики и управления работой этих сложных систем.
Сегодня нет идеологии управления глиноземным производством. Еще спорим: надо или не надо рассчитывать потоки и дистанционно управлять ими, увеличивать единичную мощность аппаратов (автоклавные, выпарные батареи, декомпозеры, печи спекания и кальцинации).
В связи с распадом ВАМИ возникает серьезная проблема создания научных центров в компаниях и на предприятиях. Ядром этих центров должны быть настоящие профессионалы, хорошо оснащенные и оплачиваемые.
Мы потеряли стандарт проведения научно-исследовательских работ. Вначале всегда делался литературный обзор, программа, методика испытаний, обработка результатов методом математической статистики, выводы и предложения.
Требуется серия комплексных мероприятий по электролизному и глиноземному производствам:
состав электролита: кислые электролиты с содержанием CaF2 и MgF2 до 4 % и LiF до 22,5 % обеспечивают высокий перегрев и хорошую растворимость глинозема;
уровень металла и электролита с учетом чугунных флянцевых листов электролизера выбран нами правильно по расчету теплового баланса, что позволило поднять силу тока с 74,5 до 83 кА;
катодные кожуха с днищем без необходимости установки катодных кожухов с контрфорсами;
необходимо разработать программу по снижению плотности тока в алюминиевой ошиновке (в элементе цепи): ЦПП, межкорпусной и на электролизерах до уровня зарубежных заводов. Мы превышаем плотность тока примерно в 2 раза, отсюда высокое среднее напряжение;
новые футеровочные материалы, прежде всего на боковую футеровку. Просто надо закупать эти материалы за рубежом для того, чтобы иметь срок службы электролизера до 70 месяцев;
проблема песочного глинозема, его стоимость и согласие на приобретение алюминиевыми заводами. Разработка способа транспортировки глинозема от печи кальцинации в силос, в прикорпусные силоса и доставка на корку электролизера без истирания и потерь;
в выбросах в атмосферу содержится большое количество пыли и твердых отходов. Нет целевых программ по уменьшению пылевыделения и переработки твердых отходов глиноземного и электролизного производства (отработанная угольная огнеупорная футеровка, красные шламы);
нет серьезных работ и рекомендаций по уменьшению выброса смолистых,и бенз(а)пирена. Необходимо еще раз вернуться к «сухому» аноду, «сухой» анодной массе.
уже в этом году у нас появились проблемы по качеству углеродистого сырья: кокс, пек. Сегодня Россия не может себя обеспечить этим сырьем. Необходимо ежегодно делать балансы по сырью сроком на 5 лет, прежде всего по углеродистому. Такие же балансы надо делать по теплоэнергии и электроэнергии по региону и иметь долговременные контракты;
необходимо поставить вопрос о единых железнодорожных тарифах, как на экспортные, импортные, так и на российские товары и грузы;
требует научного осмысления технология ремонтов, технического обслуживания металлургических агрегатов и оборудования, как это делается на зарубежных алюминиевых заводах.
Необходимо шире изучать иностранную переводную литературу по производству алюминия, глинозема, анодной массы, алюминиевых порошков. Надо найти базовый институт, который на долговременной основе будет обеспечивать специалистов такой переводной литературой.
Если мы будем считать, что главное у нас только конструкция металлургического агрегата и его технология, то этого будет явно не достаточно для того, чтобы сохранить нашу конкурентоспособность.
Надо выработать меры и действия при встрече с будущими проблемами:
нестабильное и дорогое энергообеспечение;
нехватка квалифицированных кадров и рост затрат на оплату труда;
моральное давление общества за экологические выбросы и высокая цена платежей;
старым заводам в ближайшие 510 лет не приходится надеяться на большие инвестиции;
неконкурентная организация труда, управления, отсталая система обслуживания и ремонта оборудования;
мощности физически будут выходить из строя и не будут подлежать ремонту.
Все это надо осмыслить и максимально решить в ближайшие 5 лет, чтобы продлить жизнь заводам еще на 1015 лет, дождавшись, когда придут инвестиции. За 5 лет мы должны создать базу для инвестиций, не останавливая предприятия, найдя эффективные проектные решения. Надо делать ТЭО, проектную документацию, учиться работать с численностью персонала в 23 раза меньшей, чем сейчас, по-новому готовить кадры рабочих и управленцев. Без вовлечения работающих людей в этот процесс, без решения их социальных проблем эти задачи не решить.
Таблица 1
Основные показатели глиноземного и электролизного производств алюминиевой отрасли России, тыс. т
2002 2003 2003 к 2002, %
Добыча бокситов 4586 5443 118,7
Производство глинозема 3131 3231 103,2
Производство алюминия первичного* 3348 3478 103,9
Производство полуфабрикатов и изделий из алюминия 437,4 438,5 100,3
В том числе фольга 39,8 46,6 117,1
Производство катанки 226 231 102,4
______________________
* Без учета продукции ЗАО «Алюком-Тайшет»
Таблица 2
Затраты в себестоимости алюминия российских и западных алюминиевых фирм по состоянию на декабрь 2003 года, долл./т
Запад Россия
2003 2003 после 2005 (ожид.)
Цена алюминия на ЛБМ 1550 1550 1550
Себестоимость 1237 1164 1582
в том числе сырье (глинозем, фтор соли, анодная масса) 740 869 970
электроэнергия 274 156 312
трудозатраты 157 49 150
прочие 66 90 150
Рис. 1. Добыча боксита, производство глинозема и алюминия в 19902003 гг. в целом по отрасли, тыс. т
5500
4500
3500
2500
1500
1990 1991 1992 1993 1994 1995 1996 1997 1998 1999 2000 2001 2002 2003
5749 4808 4578 4300 3635 3740 3765 3826 3940 4382 5274 4955 4586 5442
3074 2693 2719 2568 1968 2254 2148 2380 2465 2657 2856 3047 3131 3231
2916 2735 2745 2818 2669 2789 2875 2906 3005 3146 3244 3300 3348 3478
Добыча боксита
Производство глинозема
Производство алюминия
Рис. 2. Производство глинозема на БАЗ-СУАЛ в 19972004 гг.
тыс. т
1200
1100
1000
900
800
700
600
1997 1998 1999 2000 2002 2003 2004 (ожид.)
914 957 979 1034 1049 1064 1078 1100
100 104,7 107,1 113,1 114,8 116,4 117,9 120,4
98,3 102,9 105,3 111,2 112,8 114,4 115,9 118,3
тыс. т
к проекту, %
к 1997 г., %
%
150
140
130
120
110
90
Рис. 3. Производство алюминия на БАЗ-СУАЛ в 19972004 гг.
тыс. т
200
190
180
170
160
150
140
130
120
1997 1998 1999 2000 2001 2002 2003 2004 (ожид.)
146,6 155,9 158,4 167,5 175,5 181,1 182,6 182,5
100 106,3 108 114,3 119,7 123,5 124,6 124,5
96 102,1 103,7 109,7 114,9 118,6 119,6 119,5
тыс. т
к проекту, %
к 1997 г., %
%
150
140
130
120
110
100
90
Рис. 4. Динамика относительного снижения потребления энергоресурсов при производстве алюминия на БАЗ-СУАЛ, %
130
125
120
115
10
105
1997 1998 1999 2000 2001 2002 2003 2004 (ожид.)
100 106,3 107,3 114,3 119,8 122,9 124,9 124,3
100 104,5 105,4 112,1 117,1 118,6 121,3 120,7
Выпуск алюминия
Потребление энергоресурсов
Рис. 5. Инвестиции БАЗ в производство, млн руб.
1000
800
600
400
200
|
|
|
|
|
текущий номер

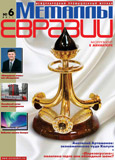
предыдущий номер

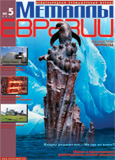
|
|