|
|
Журнал |
|
Архив |
|
Подписка |
|
Реклама |
|
САММИТ |
|
Книжная полка |
|
Контакты |
|
В начало |
|
|
|
| |
|
|
 |
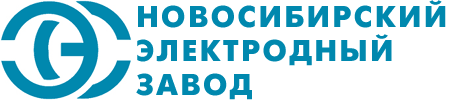 |
№5' 2003 |
версия для печати
|
|
ВОЗВРАЩЕНИЕ К СТАБИЛЬНОЙ РАБОТЕ |
|
Виктор Пирогов
Генеральный директор ЗАО «Новосибирский электродный завод»
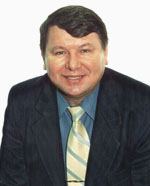 Виктор Пирогов |
|
истории нашего завода последние три года были, пожалуй, наиболее драматичными. Внешнее управление, а затем и конкурсное производство, направленное на ликвидацию предприятия, серьезно повредили репутации НовЭЗа. Потребители, особенно зарубежные, усомнились в нашей способности выполнять контрактные обязательства. Динамика объемов реализации с сентября 2001 года по апрель 2002 года, когда действовала процедура банкротства, снизилась на 26 %, появились убытки на сумму более 100 млн руб. Поэтому самым важным для нас событием стал конкурс по продаже имущественного комплекса завода, проведенный в марте 2003 года. Победителем торгов была признана группа «Энергопром», предложившая наилучшие условия ведения бизнеса и цену. Новосибирский электродный завод наконец-то обрел собственника.
Это сразу отразилось на результатах работы. Объем производства за первое полугодие вырос в 1,6 раза, а всего в 2003 году мы планируем выпустить продукции на 1,8 млрд руб. при уровне прошлого года 1,3 млрд руб. По физическим показателям мы приблизились к максимальным достижениям, какие были до начала рыночных реформ. Рекордным для предприятия считается 1989 год, когда было выпущено 98 тыс. т электродов и электродной массы. Затем наступил длительный спад, и в 1998 году он достиг нижней точки всего 37 тыс. т продукции. В прошлом году сделано 70 тыс. т. В этом году выйдем на 90 тыс. т.
Ситуация вокруг завода успокоилась, и стало значительно легче выстраивать отношения с потребителями. Но могу сказать, что эти три года не пропали даром: мы занимались внутренними преобразованиями, совершенствовали технологии, повышали культуру производства. Надо отдать должное коллективу НовЭЗа: люди с доверием отнеслись к обязательствам, которые взяло на себя руководство завода, и вопреки нестабильной, нервозной обстановке многое сумели сделать.
Характерный пример налаживание взаимовыгодного партнерства с ОАО «Мечел». Челябинские металлурги применяли в электросталеплавильных печах импортные электроды, но теперь переориентировались на нашу продукцию, которая показала себя вполне конкурентоспособной в сравнении с западными аналогами. Чтобы представить сложность выполненной работы, нужно иметь в виду специфику процесса. У нас производственный цикл длится в среднем почти 100 дней, а для отдельных видов продукции еще дольше. Выйти на рынок с новым изделием можно только после успешно проведенных испытаний, которые продолжаются как минимум 34 месяца. Здесь и технология, и напряженная мыслительная работа. И вот, пройдя через неизбежные затруднения и даже неудачи, получили в целом неплохой результат. Таким способом Новосибирский электродный завод постепенно отвоевывает свою долю рынка и начинает занимать позиции, соответствующие его потенциальным возможностям.
Для того чтобы завод мог успешнее развиваться, мы провели реорганизацию структурных подразделений. Укрупнили производственные цеха: вместо пяти ранее существовавших сделали три. Считаем, что это оправдано, поскольку более точно соответствует технологическому процессу. Например, смесильно-прессовый цех и цех прокалки представляют собой единый комплекс подготовки продукции. При таком подходе производственные циклы уже не только технологически, но и организационно выстраиваются друг за другом. Это облегчает функцию управления, позволяет сделать его более эффективным.
Основные цеха сегодня занимаются только производством. Функции ремонта, обслуживания переданы специализированным службам в управления главного механика, главного энергетика, автоматизации, строительства, экологии и т.д. Это дало возможность сконцентрировать силы ремонтников и повысить их квалификацию. Если раньше они занимались узкими вопросами каждый в своем цехе, то сегодня это специалисты высокого класса, способные решать универсальные задачи.
Численность занятых в результате структурных преобразований несколько сократилась, но при этом мы обновили и улучшили кадровый состав. За последние 23 года сменились почти все руководители подразделений. Сделана ставка на молодежь. Начальнику самого ответственного подразделения цеха механической обработки всего 26 лет. Потребность в квалифицированных, современно мыслящих специалистах все еще ощущается достаточно остро, поэтому НовЭЗ изыскивает средства на подготовку и обучение кадров: только в первом полугодии на эти цели выделено 2,6 млн руб. При Новосибирском государственном техническом университете специально созданы две группы для студентов, которые учатся по направлению нашего завода.
Завершение имущественных споров в отношении НовЭЗа позволило вырваться из порочного круга временных схем и перейти к осуществлению долгосрочных планов. Завод вступает в стадию комплексной модернизации и технического перевооружения производства.
В июне пустили обжиговую печь № 3, где использована новая система газоудаления с верхним газоходом. Через месяц начала действовать печь № 10. Построенная в 1989 году, она имела серьезные конструктивные недостатки, проработала всего 34 года, а затем была остановлена и бездействовала более 10 лет. Мы пустили эту печь по новой технологии обжига без пересыпки материалов и с использованием контейнерной загрузки. С вводом в сентябре второй очереди производительность печи возрастет в 2,5 раза, но, самое главное, мы поднимаем на новый уровень качество и культуру производства.
Следующий шаг более глубокие технические усовершенствования. В сотрудничестве с польской фирмой «Леграф», известной на мировом рынке своими разработками оборудования для углеграфитовой промышленности, заканчиваем проектирование узкокассетной 32-камерной печи. Это совершенно новая для России технология обжига, и она обещает целый ряд преимуществ. При общей температуре процесса 1250оС разница между температурами верхней и нижней частей печи не превысит 10оС. Вряд ли нужно пояснять, что это значит для качества будущей катодной продукции. Кроме того, мы существенно улучшаем условия труда, снижаем экологическое загрязнение. Если сейчас у нас применяется грейферная загрузка и выгрузка пересыпочных материалов, то система пневмоудаления полностью исключит их попадание во внешнюю среду. Ввести эту печь в работу мы планируем в первом полугодии 2004 года. А дальше отработав, как следует, технологию, начнем ее тиражировать, реконструировать и другие печи.
В цехе механической обработки электродов мы пока ограничиваемся усовершенствованием оборудования как говорят электронщики, меняем станкам «мозги». Но в следующие два года, очевидно, займемся заменой и самого станочного парка с расширением его возможностей и наращиванием мощностей. Количество заказов постоянно растет. При этом появляются новые потребители на зарубежных рынках, где требования к точности и чистоте обработки намного жестче.
Мы вплотную занялись комплексной автоматизацией предприятия. Причем речь идет обо всех видах деятельности и конкретных физических работах, и решении управленческих задач. Например, собираемся автоматизировать работу подъемных кранов. При этом достигаются две цели: освобождаем людей от нелегкого труда в загрязненных зонах и передаем дистанционное управление механизмами непосредственно тому, кто занимается выполнением соответствующей операции, будь то извлечение заготовок, складирование, упаковка. Ускоряется весь процесс и снижается вероятность ошибок.
Автоматизация цехов имеет целью централизацию управления производственным циклом и объективный, без влияния человеческого фактора, контроль технологических параметров. Так, на смесильно-прессовом участке в ходе модернизации оборудования автоматизируются процессы нагрева, смешивания, дозирования массы, ее прессования. В цехе обжига всем комплексом печей можно будет управлять из единого диспетчерского пункта. Уже сегодня специалисты завода по компьютеру в реальном времени следят за движением готовой продукции. Подобный режим мы хотим ввести на всех стадиях производства.
В целом программа технического развития НовЭЗа разработана на три года и предусматривает следующие ориентировочные объемы вложений: в текущем году 100 млн руб., в 2004 году 200 млн руб., в 2005 году 100 млн руб. Суммы расписаны под конкретные проекты, но рыночные возможности растут, и не исключено, что нашу программу придется дополнить.
Все больший интерес начинает представлять такой технологический передел, как прокаливание антрацита. Традиционно сосуществуют два способа: газокальцинирование во вращающихся печах при температуре 1350оС и электрокальцинирование при 2000оС, благодаря чему обеспечивается более глубокая степень прокалки, и на выходе получается материал практически готовый. Но мы смотрим дальше: каким путем получать электрокальцинированный антрацит в специально предназначенных для этого установках или попутно в печах графитации? Результаты получаются почти одинаковые. Все зависит от того, насколько успешно сумеем отработать технологические режимы.
Эта технология важна тем, что улучшает эксплуатационные характеристики продукции. Основную выгоду от этого получают, конечно, потребители. Известно, что катодные блоки в электролизном производстве крупнейших российских алюминиевых заводов БраЗа, КраЗа сегодня служат не менее 55 месяцев вместо 3842, как было сравнительно недавно. Продолжая повышать стойкость своих изделий, мы тем самым уменьшаем на них спрос. Казалось бы, какой в этом смысл? Но в действительности все не так просто. Есть рынок, на котором до 40 % продукции завозится по импорту, и значит, нужно вести конкурентную борьбу, предлагать изделия более высокого качества.
На заводе действует простое и обязательное для всех правило из двух пунктов. Первый пункт: потребитель всегда прав. Второй пункт: если потребитель не прав, читай пункт первый.
Чтобы лучше понимать потребности наших партнеров и подтвердить свою готовность к долгосрочному сотрудничеству, мы используем такую форму, как технический аудит. Представители компаний приезжают к нам на завод, проходят по всем переделам, делают замечания. Через полгода-год вновь проверяют, что исправлено, что нет. Подобная открытость не только помогает укреплять технологическую дисциплину, но и поднимает уровень взаимного доверия.
Ужесточение требований рынка заставляет искать новые возможности, в том числе экспериментировать с различными видами сырья. Теперь мы используем не только антрацит, нефтяной кокс, пеки, но и закупаемый по импорту игольчатый кокс, который производят в мире всего три страны: Англия, США и Япония. Электроды на игольчатом коксе были хорошо приняты рынком, и за год мы удвоили их производство с 500 до 1000 т в месяц.
В последнее время на НовЭЗе создано несколько новых видов продукции. Например, угольные электроды диаметром 960 мм. Их покупателем стала немецкая компания по производству кремния RW Silicium. Она наращивает объемы производства, и это мы видим по динамике заказов. Начав в прошлом году с 20 т в месяц, мы на сегодняшний день увеличили поставки в три раза. Появляются и другие потребители наших угольных электродов в Бразилии, Австралии.
В тесном контакте с потребителями проводим испытания так называемого безниппельного электрода. Опыт применения этих изделий на Кузнецком металлургическом комбинате и Новосибирском оловянном комбинате подтвердил, что мы выходим на весьма перспективное направление.
Еще один новый вид продукции электродная масса в цилиндрах, которую поставляем на Братский алюминиевый завод и в ОАО «Печенганикель». Прорабатывается вопрос о поставке электродной массы прямоугольного сечения на американский рынок для выплавки ферросплавов.
Начинаем развивать отношения с лидером мирового алюминиевого рынка компанией Alcoa. Американцев привлекает, что у нас используется очень хороший антрацит, из которого получается качественная и не слишком дорогая продукция. С прошлого года мы углубленно занимаемся параметрами качества для четырех типов катодных блоков и уже достаточно хорошо знаем, какой состав, какой компонент нужен каждому потребителю. Сейчас речь идет о новом виде этой продукции катодном блоке с высоким содержанием графита. Определились по составу, но для достижения стабильности качественных показателей еще необходимо отшлифовать технологию по всей производственной цепочке. Сотрудничаем с Челябинским электродным заводом, который, как и НовЭЗ, имеет в этой сфере перспективные наработки.
Взаимодействие электродных заводов в рамках ассоциации «Углеграфит» показало, что мы, несмотря на конкуренцию, можем координировать деятельность и укреплять свои позиции на рынках, максимально используя преимущества каждого предприятия. Сейчас думаем пойти по пути кооперации в производстве определенных видов изделий. Условно говоря, начнем комплектовать наши электроды ниппелями, изготовленными на другом заводе. Процесс производства ниппеля несколько длиннее, чем самого изделия. Если перевести эту деталь на отдельный поток, она будет получаться более качественной, а мы сбалансируем производственный цикл и повысим эффективность. Выпускать монопродукт всегда проще.
Конечно, жизнь нашего завода не исчерпывается проблемами производства. Как и большинство предприятий российского металлургического комплекса, НовЭЗ имеет развитую социальную сферу. Сейчас особый упор мы делаем на оздоровительную программу. Прежде всего собираемся расширять спортивную базу. Будем строить универсальный спортзал, затем бассейн. Хотим, чтобы работники завода и жители поселка Линево, где расположен НовЭЗ, имели достаточно возможностей укрепить здоровье и найти достойное занятие в часы досуга. Тогда и на работе дела пойдут успешнее.
|
|
|
|
|
текущий номер

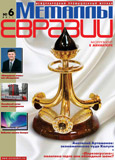
предыдущий номер

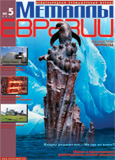
|
|