|
|
Журнал |
|
Архив |
|
Подписка |
|
Реклама |
|
САММИТ |
|
Книжная полка |
|
Контакты |
|
В начало |
|
|
|
| |
|
|
 |
№5' 2003 |
версия для печати
|
ГИГАНТ МОГУЧ И ПОСЛУШЕН |
НКМЗ МОДЕРНИЗИРОВАЛ ПРЕСС-75000 ДЛЯ ВСМПО |
Владимир Невидомский, Виктор Граматный, Генрих Смородинский, Виталий Дзержинский
АО «Ново-Краматорский машиностроительный завод»
азвитие ряда отраслей промышленности в 50 60-х годах авиационной, энергетической и других потребовало получения ответственных крупногабаритных точных цельноштампованных поковок из высоколегированных жаропрочных, титановых и других труднодеформируемых металлов и сплавов. Бывшим Министерством тяжелого машиностроения СССР задача по созданию необходимого оборудования мощного гидравлического штамповочного пресса была возложена на два коллектива Уралмашзавод и Ново-Краматорский машиностроительный завод (НКМЗ). После рассмотрения проектов на техническом совете министерства проект пресса, созданный на НКМЗ в содружестве с ВНИИМетмашем и другими научно-исследовательскими институтами, принес заводу победу в творческом соревновании с конструкторами Уралмашзавода.
Главным инженером проекта этой машины на НКМЗ был главный конструктор завода Н.И. Киселев. Для выполнения проекта потребовалось создать специальное бюро во главе с начальником С.С. Гржибовским и ведущим инженером М.Л. Беккером, в которое вошли опытные конструкторы Ю.Н. Карзов, Ф.И. Кагановский, М.Д. Лаптев, М.И. Будман, В.В. Левченко, Г.Л. Винник, В.А. Новоселов.
Вскоре после этого проект претворился в машину, в которой новым и оригинальным являлся и каждый узел, и каждая деталь узла. Например, впервые для таких мощных прессов была применена силовая рама из толстолистового проката. Этот пресс-гигант, выпущенный НКМЗ в 1959 году, как и его младший брат 1961 года рождения, занесены в Книгу рекордов Гиннеcса как самые мощные гидравлические штамповочные механизмы своего времени.
Об этих прессах высотой в 37 м и весом в 25 тыс. т каждый история НКМЗ долгое время умалчивала, потому что оба работали (и работают) на предприятиях стратегического значения, о которых по объективным причинам в советское время в средствах массовой информации не говорилось. Отца-прародителя братьев-гигантов ни Самарский металлургический завод, ни Верхне-Салдинское металлургическое производственное объединение (ВСМПО), обрабатывающие алюминиевые и титановые сплавы, не афишировали по той же причине. Да и упоминание об НКМЗ, достаточно закрытом предприятии особого значения, можно было найти разве что в специальной литературе.
На ВСМПО пресс ласково называли «семидесяткой». Ласково потому что агрегат, точный в штамповке и надежный в управлении, был и остается кормильцем металлургов, а «семидесяткой» потому что изначально он не выжимал свои проектные 75 тыс. т.с.
Более сорока лет пресс интенсивно эксплуатировался, как, собственно, и должно быть на предприятии, специализирующемся на выпуске штамповок для самолетов, космических кораблей, подводных лодок и атомных реакторов. Может быть, все продолжалось бы еще не один год, но время изменилось, как изменились в авиационной промышленности требования к качеству штамповок, да и заказчики стали иными. Сейчас ВСМПО имеет дело с компаниями Boeing, Rolls Royce, General Electric, Airbus Industrie.
Одним из требований заказчика авиастроительной компании Boeing, предъявленное к ВСМПО, было такое: предоставить полный протокол технологического процесса штамповки каждой детали с указанием всех его параметров. В мировой практике при изготовлении столь ответственных деталей для авиастроения это обязательное условие. На ВСМПО поэтому было принято решение полностью модернизировать на прессе систему управления и контроля технологических процессов, а также довести его до паспортных данных усилия 75 тыс. т.с.
Специалисты НКМЗ выделили главные направления работ при модернизации пресса. Это снижение чечевичности штампуемой заготовки за счет точного дозирования технологического усилия; устранение клиновидности посредством внедрения системы синхронизации пресса; повышение точности геометрических размеров за счет внедрения системы позиционного останова подвижной траверсы на заданный размер; достижение высокого качества структуры металла за счет возможности оптимального выбора регулируемых скоростей штамповки. Все это обеспечил созданный регулятор адаптивного управления принципиально новой конструкции.
Комплект смонтированного оборудования включает уникальную эмульсионную аппаратуру производства НКМЗ, маслосистемы с элементной базой известной фирмы Rexroth и систему автоматизированного управления с элементной базой фирмы Siemens. Таким образом, была создана возможность автоматического регулирования скоростных и силовых параметров, необходимых для ведения качественного технологического процесса получения штамповок с обеспечением его повторяемости. При этом были обеспечены электронный контроль и диагностика технологического процесса штамповки с отражением всей необходимой информации на экране монитора. После модернизации на монитор выводятся все показания механических перемещений пресса, и оператор видит, какое перемещение совершил каждый рабочий орган и с какой скоростью.
В АСУТП пресса применены самые современные и точные датчики, которые позволили уточнить линейные параметры подвижной части пресса. Датчики позволяют контролировать почти 1000 различных параметров, характеризующих состояние пресса. Во-первых, система фиксирует все параметры технологического процесса и, получив распечатку их графиков, можно полностью восстановить каждую технологическую операцию. Во-вторых, она позволяет диагностировать состояние пресса при его внезапной остановке вследствие какой-то неисправности. И теперь информация о любой ее причине будет выведена на экран монитора практически мгновенно, даже если это неисправность датчика самой системы. До модернизации на ее поиск уходило достаточно много рабочего времени. Если перед началом работы пресса оператор забудет включить какой-то автомат, система также выведет на экран монитора соответствующее сообщение, и до выполнения рекомендации системы включение пресса будет невозможным.
После завершения монтажных работ, продолжавшихся без малого два месяца, 20 января 2003 года ВСМПО приняло пресс. За это время было смонтировано более 500 т оборудования. Но началом жизни гиганта уже в новом, модернизированном обличье стало 31 декабря 2002 года. Именно тогда на обновленный пресс впервые было подано давление, первое движение совершила его траверса и была получена первая штамповка. Таким образом, все идеи, заложенные разработчиками в проект модернизации, себя оправдали.
При пуске прокатного стана, например, в Индии, разбивают о рабочую клеть кокосовый орех. 27 лет назад Франция с замиранием сердца следила, как выполняет первую операцию самый младший из семьи гигант-пресс усилием 65 тыс. т.с., а затем услышала хруст и увидела распавшуюся на две аккуратные половинки скорлупу грецкого ореха и его чистое целое ядро.
Когда на испытаниях пресса в Верхней Салде за новый пульт управления сели те же операторы, которые работали на прессе несколько месяцев назад, они были просто ошеломлены новыми возможностями, послушностью пресса-гиганта. Так, его траверса весом 5 тыс. т чутко реагировала даже на самые незначительные движения джойстика на пульте управления, с высочайшей точностью отрабатывая все команды. После пуска пресса уже по управляющей программе массивная траверса должна была выполнить операцию, считающуюся верхом кузнечного искусства, плавно закрыть спичечный коробок. Кто-то поставил на подштамповую плиту рядом с открытым спичечным коробком свои наручные часы. Раз поставил значит, был уверен в успехе.
И действительно, все получилось: пресс послушно закрыл миниатюрную коробочку, а хозяин обрел свои тикающие, теперь уже исторические часы.
До модернизации выполнить эту технологическую операцию при помощи рычагов могли только специалисты высочайшего класса, обладающие к тому же огромной физической силой. Теперь закрыть спичечный коробок, используя джойстик, смогла бы даже хрупкая девушка-оператор.
В результате модернизации количество ступеней усилий штамповки на прессе было увеличено с 4 до 13, и сегодня он выполняет более широкий спектр технологических операций, работая в экономичном режиме. Точный выбор усилия штамповки позволяет рационально расходовать электроэнергию, резко повысить точность изготавливаемых штамповок, получить меньший радиус их деформации и, самое главное, обеспечить высокое качество штамповок с заданной структурой и свойствами. Последнее на 1020 % уменьшает толщину слоя металла, снимаемого впоследствии при механической обработке штамповок.
Специалисты Верхне-Салдинского производственного металлургического объединения, имеющие большой опыт эксплуатации пресса, по достоинству оценили все идеи, реализованные новокраматорцами при его модернизации, и остались удовлетворены результатами испытаний.
|
|
|
|
текущий номер

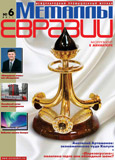
предыдущий номер

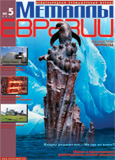
|
|