Николай Воробьев
Генеральный директор ОАО «Мечел»
Челябинский металлургический комбинат (с 1992 года ОАО «Мечел») всегда занимал особое место в металлургическом комплексе страны. В мировой металлургии вряд ли можно найти аналогичное предприятие по объему производственных мощностей, предназначенных для выпуска качественного и специального металла, по разнообразию марочно-профильного сортамента и составу оборудования основных переделов. Построенный в годы войны комбинат предназначался, в первую очередь, для выпуска металлопродукции для наукоемкого сектора экономики авиа-космического комплекса, оборонной промышленности, атомного машиностроения, судостроения, подшипниковой промышленности, приборостроения, медицинской техники и т.д.
И вот предприятие подошло к своему 60-летнему юбилею. За этот срок челябинскими металлургами произведено 150 млн т кокса, около 160 млн т чугуна, 218 млн т стали и около 145 млн т готового проката. На комбинате разработана и внедрена промышленная технология производства свыше тысячи марок сталей и сплавов. Из них более 130 носят фирменный знак «Мечела» «ЧС» (челябинская сталь).
Однако именно это сложное и капиталоемкое производство наиболее трудно адаптировалось к рыночным реформам. Это обстоятельство придало особую остроту кризису, в котором, как и вся российская металлургия, оказался Челябинский комбинат. Если к середине 90-х годов общероссийское потребление стали упало в 4 раза, то спрос на качественную металлопродукцию сократился в 8 10 раз. Но и в этот сложный период комбинат сумел выжить и даже расширить свою рыночную нишу в основном за счет так называемого «большого потока» производства массовой металлопродукции из углеродистых и низколегированных сталей.
Именно тогда решалась судьба «Мечела» как предприятия качественного металла с полным металлургическим циклом. В условиях сырьевых трудностей, бартера, дефицита финансовых средств выдвигались настойчивые предложения, в том числе и от собственников, о реструктуризации комбината, ликвидации полного цикла, т.е. фактически о закрытии «большого потока» и превращении предприятия в передельный электросталеплавильный завод. К счастью, здравый смысл восторжествовал нам удалось избежать скоропалительных решений, сохранить уникальный технологический профиль комбината, его технические традиции, квалифицированные кадры, социальную стабильность. При этом даже в самые сложные годы, думая о будущем, «Мечел» находил возможности для технического совершенствования производственного аппарата. В эти годы, например, был полностью ликвидирован устаревший мартеновский передел, введены в строй новые мощные электродуговые печи, установки непрерывного литья заготовок и внепечной обработки стали.
В последние годы ОАО «Мечел» за счет жесткой финансовой дисциплины, разумной рыночной политики, гибкого использования эффекта девальвации августа 1998 года и общехозяйственного подъема сумел перевести производство на ритмичную основу и добиться наилучших за последнюю пятилетку экономических показателей. Предприятие почти полностью рассчиталось с долгами перед местным бюджетом, энергетиками, транспортниками, проводит регулярную индексацию заработной платы. За 1999 2002 годы производство кокса увеличилось в 1,5 раза, чугуна и стали в 1,3 раза, товарного проката в 1,4 раза. Объем реализации продукции только за последний год вырос на 5,5 %.
Руководство комбината прекрасно понимает, что одним из главных факторов экономического роста является техническая политика, как важнейший элемент общей стратегии развития предприятия на перспективу. При этом мы стремимся оценить весь комплекс факторов, определяющих основные ресурсные потребности, производственную специфику, физический и моральный износ оборудования, новые технические решения, продуктовые возможности, а также спрос на конкретные виды металлопродукции на внешнем и внутреннем рынках. Основными принципами технической политики ОАО «Мечел» являются:
рациональное использование производственного аппарата основных переделов и расширение его технико-экономических возможностей главным образом за счет модернизации;
ресурсосбережение на всех этапах производственного цикла как главный технико-экономический критерий выбора и внедрения технических новинок; развитие производства качественной металлопродукции как основного профильного направления предприятия;
преимущественное использование собственных финансовых ресурсов и производственных возможностей при разработке и реализации конкретных инвестиционных программ и бизнес-планов.
Наиболее серьезные технические новшества, проведенные в последнее время и запланированные к вводу в эксплуатацию в 2002 году, таковы.
1. Ввод в строй действующих (после длительной консервации) коксовой батареи №5 с годовой мощностью 450 тыс. т кокса. Это позволяет увеличить его производство до 2,5 млн т в год. В перспективе после расконсервации батареи №2 общий объем выпуска кокса достигнет 3 млн т.
2. Строительство нового комплекса усреднения и подачи шихты на рудном дворе доменного цеха. Комплекс, общая стоимость которого составляет около 250 млн руб., позволит довести степень усреднения агломерационного сырья до 90 %. Реконструкция существующей аглофабрики позволит увеличить производство агломерата со 170 до 270 300 т в месяц, что полностью удовлетворит потребности комбината в этом сырье. Стоимость реконструкции оценивается в 1,2 млрд руб.
3. Продолжается капитальный ремонт а фактически реконструкция доменной печи №1 с увеличением полезного объема на 20 %. В ходе работ, оцениваемых в 500 млн руб., печь будет оснащена новым современным оборудованием, что даст возможность увеличить выпуск чугуна на 0,65 млн т в год. В перспективе комбинат планирует использовать все четыре доменных печи и увеличить производство чугуна с 8,5 тыс. т до 12 тыс. т в сутки.
4. Пуск нового агрегата комплексной обработки стали (АКОС) в кислородно-конвертерном цехе, который позволяет существенно снизить удельные затраты и улучшить качество металла. Производственная мощность агрегата около 1 млн т в год. При стоимости проекта 150 млн руб. годовой экономический эффект оценивается в 68,2 млн руб.
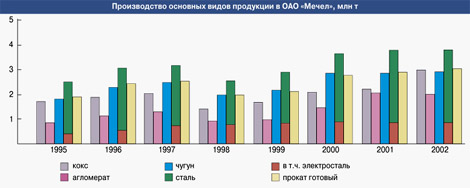 5. Модернизация печи ДСП-100И в электросталеплавильном цехе №6 в комплексе с машинами непрерывного литья слябов. Общий объем капитальных затрат 122 млн руб. Модернизация позволит увеличить годовой выпуск непрерывнолитых слябов с 390 тыс. т до 750 тыс т. Экономия оценивается в 180 млн руб. в год.
6. Ввод в эксплуатацию машины продольной газовой резки металла германской фирмы GEGА в прокатном цехе №1. Реализация этого проекта, общая стоимость которого составляет около 5 млн долл., является частью комплексной реконструкции ЭСПЦ-6. Она позволит ежегодно получать дополнительно до 250 тыс. т заготовки. Эта машина дополнит блюминг. Она предназначена для обеспечения заготовкой сортовых станов. Расчетный срок окупаемости проекта составляет полгода.
7. Освоение технологии использования жидкого чугуна вместо металлошихты в электропечах. «Мечел» является единственным предприятием в стране, использующим подобную технологию. Это позволит экономить около 100 кВт . ч/т стали, снизить расход электродов, увеличить производительность печи. Технология дает возможность снизить зависимость от дорого и дефицитного лома.
8. Ввод в строй действующих нового энергетического оборудования (турбогенератора, паровой турбины), что позволило повысить самообеспечение комбината электроэнергией до 70 75 %. Стоимость проекта около 200 млн руб. В ближайшей перспективе намечен пуск нового турбогенератора и увеличение производства собственной электроэнергии до 95 %.
Крупнейшим проектом ближайших двух лет является строительство в кислородно-конвертерном цехе сортовой МНЛЗ фирмы Danieli годовой мощностью 1 млн т заготовки сечением 100 мм. Шестиручьевая машина будет иметь самую высокую скорость разливки среди подобных агрегатов на российских заводах до 5,5 м/мин. Сметная стоимость этого проекта 1400 млн руб. Экономический эффект, который мы надеемся получить за счет снижения себестоимости товарного проката из рядовых и углеродистых сталей, составит более 500 млн руб. в год. С пуском в 2004 году новой МНЛЗ объем непрерывного литья достигнет 2 млн т. Кроме того, мы предполагаем, что металл после новой МНЛЗ без охлаждения через промежуточную печь будет поступать в прокатный цех. Экономия только за счет сокращения расхода газа составит 5 7 долл./т металла, не считая ликвидации адъюстажа, вспомогательного оборудования, сокращения трудозатрат, потребности в вагонах и т.д. В перспективе руководство «Мечела» планирует довести удельный вес непрерывного литья до 80 %. По сути, все проекты модернизации и реконструкции осуществляются комбинатом за счет собственных средств и собственными силами. Предприятие имеет хорошо оснащенный комплекс механических цехов, в которых занято более трех тысяч человек, что позволяет своими силами изготавливать значительную часть оборудования, экономя при этом немалые средства. Например, новый АКОС, оборудование которого изготавливалось с участием наших механических служб, обошелся предприятию втрое дешевле зарубежных аналогов.
Перечень всех объектов модернизации свидетельствует о том, что свой 60-летний юбилей «Мечел» встречает в хорошем технико-экономическом состоянии. В свое время, к сожалению, Челябинский металлургический комбинат в отличие от Магнитки не успел до начала реформ провести крупную модернизацию за счет средств госбюджета. Пережив весьма неприятную ситуацию в 1990 1997 годах, когда из-за дефицита финансовых средств инвестиционные возможности сократились более чем в пять раз, мы оказались вынуждены все свои проблемы решать в основном за счет собственной прибыли, благо последние годы в этом отношении были достаточно благоприятными, о чем говорит и динамика капитальных вложений: в 2001 году они превысили 500 млн руб., в 2002 650 млн руб., а в текущем году возрастут до 1200 млн руб., причем около 85 % составят собственные средства ОАО «Мечел». Кроме прибыли и амортизационных отчислений, мы используем принципиально новые для нас источники инвестиций. Так, ОАО «Мечел» в феврале 2003 года разместил облигационный займ на сумму 1 млрд руб., что свидетельствует, в частности, о нашем достаточно прочном финансовом положении.
В канун своего юбилея Челябинский металлургический комбинат переживает вторую молодость. Пройдя через нелегкие испытания последнего десятилетия, «Мечел» сумел найти свое место в новых экономических условиях, сохранив при этом специализацию ведущего российского производителя качественного металла. Товарный знак, или, по-нынешнему, брэнд предприятия по-прежнему высоко котируется на мировом и российском рынках.
|