Андрей Груздев
Генеральный директор ОАО «Качканарский ГОК «Ванадий»
Минувший 2002 год подтвердил наметившуюся в конце 90-х тенденцию к оздоровлению производства и экономики комбината. Более того, второе полугодие стало в своем роде этапным: через одиннадцать лет Качканарский ГОК снова вышел на проектную мощность. Факт сам по себе отрадный. Однако было бы неправильным на этом основании делать вывод, что комбинат уже окончательно преодолел последствия прошедших лет. К примеру, главное наследие того времени существенное нарушение сроков обновления основных фондов еще долго будет влиять на работу предприятия.
Именно поэтому достижение проектной мощности пока нельзя расценивать как безусловную, окончательную победу. Предстоит затратить немало усилий, чтобы стабильно и ритмично работать в режиме добычи и переработки 45 млн т сырой руды в год (рис. 1). Задача чрезвычайно сложная, но при выполнении ряда условий вполне решаемая.
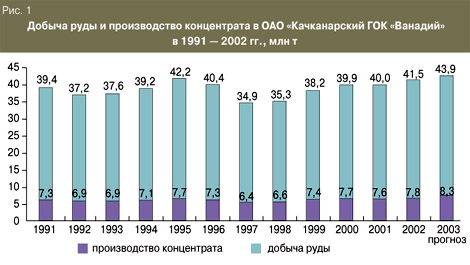
Одновременно мы обязаны, учитывая возрастающую конкуренцию на рынке металлургического сырья, предельно серьезно и последовательно снижать издержки производства и улучшать потребительские свойства выпускаемой комбинатом продукции. Решать эти задачи нужно в комплексе. К этому принуждает, прежде всего, ограниченность в средствах, которые мы можем направить на модернизацию оборудования и совершенствование технологии добычи и переработки руды. В последние два года на это расходовалось по 130 млн руб.
Средства направляются туда, где они принесут наибольший эффект. В 2000 году нам предложили испытать новый способ дробления руды с использованием принципа свободного удара в инерционно-ударной дробилке. Испытания, проведенные совместно с институтом «Уралмеханобр», показали обнадеживающие результаты. Можно ожидать, что применение принципиально новой дробилки позволит, во-первых, выделять до 40 % сухих хвостов вместо 4 10 % при нынешней технологии. При этом потери магнитного железа останутся на том же уровне, что и в мокрых хвостах. Но мокрые складировать во много раз дороже, чем сухие, которые к тому же более экологичны, поскольку исключают использование огромного количества воды.
Во-вторых, в новой дробилке «Титан-250», которая уже смонтирована на обогатительной фабрике, щебень получается кубовидным, пользующимся повышенным спросом, что сулит дополнительные доходы в будущем. И третье немаловажное обстоятельство: инерционно-ударная дробилка потребляет электроэнергии вдвое меньше стержневой мельницы, что в условиях Качканарского ГОКа приобретает решающее значение.
Приведенный пример примечателен тем, что отражает суть проводимой на комбинате политики снижения издержек производства. Так, в себестоимости продукции горнорудных предприятий доля затрат на взрывчатые вещества всегда была довольно значительной. Но это еще полбеды. Можно вспомнить десятки случаев, когда из-за неритмичной поставки штатных ВВ нарушалась последовательность отработки забоев, что нередко вело к снижению качества руды. Когда принималось решение о строительстве собственного завода взрывчатых веществ, это обстоятельство сыграло не последнюю роль. И сегодня смело можно утверждать, что мы не ошиблись, вложив средства в новое производство.
Что же дал новый завод комбинату?
1. Почти троекратное снижение затрат на приобретение взрывчатки. Учитывая, что на проведение взрывных работ используется около 400 т ВВ в неделю, а стоимость тонны гранулотола составляет около 20 тыс. руб., можно говорить о серьезном экономическом эффекте от применения собственных ВВ.
2. Взрывные работы стали более прогнозируемыми, а объемы полученной массы более стабильно обеспечивают ритмичную работу экскаваторов. В длинной технологической цепочке ликвидировано еще одно узкое место.
3. Применение штатной взрывчатки ведет к серьезным экологическим последствиям: гранулотол выделяет большое количество вредных веществ и небезопасен для работающих с ним людей. В течение года в атмосферу выбрасывалось около 75 т азота нитратного и более 200 т аммонийного. Мы на заводе «Поремит» производим эмульсионные ВВ, которые при изготовлении безопасны и более чисты экологически.
Уже в 2003 году запущена еще одна линия по производству эмульсионных ВВ. Завод выходит на проектную мощность, и мы сможем поставлять взрывчатку другим горнорудным предприятиям региона, получая дополнительный доход.
Если есть возможность снизить себестоимость продукции, мы стремимся использовать ее с максимальной отдачей. Подсчитали, что тонна завозной модифицированной глины, используемой в качестве связующей добавки при производстве подготовленного сырья, обходится комбинату дороже тонны окатышей. Расчеты показали, что собственный участок по производству модифицированной глины снизит себестоимость окатышей на 3 рубля, а годовой экономический эффект составит от 17 до 20 млн руб. В декабре 2002 года новый участок выпустил пробную партию глины, а в январе 2003 года надежно вписался в технологическую цепочку.
Подобный подход характерен для многих цехов комбината. Вот пример из автотракторного: ремонтники так искусно восстанавливают старые автобусы и трактора, что они и выглядят, как новые, обеспечивая немалый экономический эффект.
В структуре себестоимости выпускаемой комбинатом продукции львиную долю занимают энергоресурсы (рис. 2). В отличие от родственных предприятий, работающих в более комфортных климатических условиях, мы вынуждены огромное количество тепла тратить на обогрев производственных помещений. В 2002 году на эти цели было израсходовано 107 млн руб. И это при том, что на обеих агломашинах успешно действуют утилизаторы тепла. Два экономайзера частично сняли проблему обеспечения теплом и горячей водой нижних фабрик, но этого недостаточно. Техпромфинпланом 2003 года предусмотрено строительство третьего экономайзера, который будет использовать отводящиеся газы одной из четырех обжиговых машин в цехе окатышей. Для обеспечения надежной работы дробильной и обогатительной фабрик в зимних условиях совместно с фирмой «Газинжиниринг» мы устанавливаем здесь газовоздушные отопительные системы, которые намного эффективнее традиционных способов теплоснабжения. Достаточно сказать, что корпус среднего и мелкого дробления объемом 450 тыс. м3 уже обогревается одной установкой мощностью 10 МВт. На комбинате их действует четыре, еще две мы намерены пустить в 2003 году. Кстати, каждый утилизатор тепла снижает выбросы неорганической пыли в атмосферу более чем на 100 т.
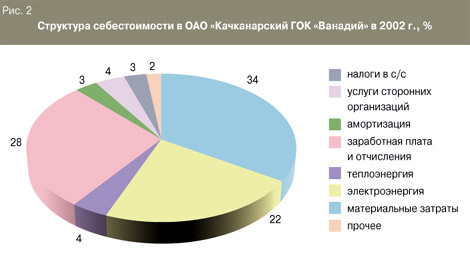
Хоть и не без труда, находим общий язык со «Свердловэнерго» в определении цен на электроэнергию, ведь Качканарский ГОК является одним из крупнейших в области ее потребителей. Сложнее с теплом. Одна гигакалория нам часто обходится дороже, чем многим другим предприятиям. А комбинат скоро исчерпает возможность и дальше снижать потребление тепла. Расчеты показывают: чем покупать тепло у энергетиков, намного выгодней построить свою котельную. Она окупится за полтора-два года, а потом будет приносить комбинату прибыль.
Мы прекрасно понимаем, что снижение доли электроэнергии в себестоимости металлургического сырья одно из главных условий стабильного развития комбината, укрепления позиций нашей продукции на рынках. Именно поэтому в комплексную программу перспективного развития Качканарского ГОКа на 2001 2005 годы закладывались мероприятия, многие из которых, наряду с ростом качественных или объемных показателей, должны работать на снижение расходов электроэнергии, воды и других потребляемых ресурсов.
Все сказанное выше укрепляет уверенность в том, что в развитии комбината начинается новый этап. Ведь последняя серьезная модернизация производства проводилась еще в 80-е годы. Именно тогда было обновлено оборудование мелкого и среднего дробления, осуществлена коренная реконструкция на обеих фабриках окускования, с заменой всех обжиговых машин. Шла массовая замена карьерных экскаваторов, буровых станков.
Кризис 90-х годов сказался на работе оборудования всех подразделений комбината. Особыми последствиями это обернулось для парка тяговых агрегатов, большинство из которых полностью отработали нормативный срок. А работа усложнялась из-за понижения карьеров. Затраты на откатку горной массы стали увеличиваться. Железнодорожный транспорт достиг предельного эффективного уровня грузооборота.
Ясно, что нужны новые технические решения. Речь, в частности, идет о качественно новом использовании карьерных самосвалов повышенной грузоподъемности в связке с 12-кубовыми экскаваторами. Четырехкратный рост объемов автомобильных перевозок позволит оптимизировать работу железнодорожного транспорта, повысить оборачиваемость «вертушек», снизить нагрузку на тяговые агрегаты (рис. 3).
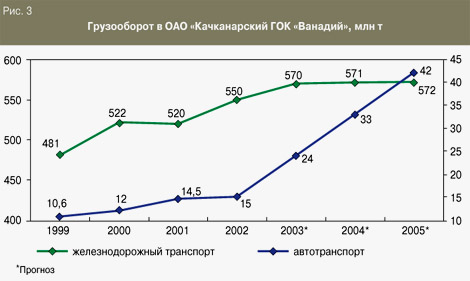
Одновременно мы вплотную приблизились к решению проблемы тяговых агрегатов. Когда не стало ГДР, прекратилось производство дизель-электровозов EL-20, которые должны были составить основу тягового парка Качканарского комбината. В России подобные машины никогда не производились. В то же время отечественные машиностроительные мощности многие годы остаются недогружеными. Поэтому в 2001 году наши специалисты вместе с коллегами из акционерных обществ «ВЭЛНИИ» и «Новочеркасский электровозостроительный завод» предприняли меры по созданию первого российского тягового агрегата НП-1. Основную тяжесть финансирования проектных работ и строительства опытного образца принял на себя Качканарский ГОК. Новый локомотив уже построен, в ближайшее время начинаются его испытания на нашем комбинате.
Локомотив НП-1 создавался на основе узлов и деталей хорошо зарекомендовавших себя электровозов ВЛ-60, ВЛ-80, ВЛ-82 и ОПЭ-1. Агрегат состоит из электровоза управления и двух моторных думпкаров, предназначенных для работы в условиях открытых горных разработок. Он способен водить поезда массой более 2000 т на участках с уклоном до 60 промиль со скоростью 25 30 км/ч. На локомотиве установлены новые тяговые двигатели НКТ-650. Система управления выполнена с использованием микропроцессоров. Все шесть токоприемников (четыре боковых и два центральных) размещены на кабине машиниста. Серьезное внимание уделено безопасности, в частности электровоз оснащен пятью тормозными системами. В кабине установлены два виброгасящих кресла, отопительно-вентиляционная установка, кондиционер, холодильник, электроплитка, шкафы для одежды.
Есть надежда, что новый электровоз станет основой локомотивного парка нашего предприятия. Уже размещен заказ на строительство второй машины. Партнерские отношения с Новочеркасским заводом мы готовы продолжать.
Усложнение горных работ потребовало более точной и достоверной оценки разрабатываемых рудных залежей. Здесь важно подчеркнуть, что ошибки в работе геологов напрямую влияют на качество конечной продукции, что недопустимо в условиях жестокой конкуренции. Чтобы исключить такую зависимость, мы внедряем горно-геологический программный комплекс Surpac. Его использование значительно повышает достоверность оценки качества добываемой руды, решает ряд других задач, прямо влияющих на себестоимость продукции.
Широкое внедрение в производство компьютерных технологий открывает новые возможности, связанные, прежде всего, с ростом качественных показателей. Принципиально новые системы контроля за содержанием железа позволяют в любой момент с высокой точностью определять качество концентрата, своевременно принимать корректирующие решения. Поставлена задача: на всех этапах рудоподготовительного и обогатительного производства создать автоматизированные системы управления технологическим процессом. Работы уже ведутся на аглофабрике и фабрике окатышей. Затраты будут значительными, но, как показывает практика, они быстро окупятся. К слову, только от внедрения автоматизированной системы учета и контроля энергоресурсов ожидается годовой экономический эффект около 25 млн руб. Серьезную отдачу сулит и создание корпоративной информационной системы управления комбинатом, над которой работают специалисты отдела АСУ.
В конце января 2003 года обогатительная фабрика выпустила 250-миллионную тонну концентрата. Вообще для комбината нынешний год пора многих юбилеев. В июне исполнится сорок лет со дня выпуска первого качканарского концентрата. В сентябре комбинат официально вступил в строй действующих предприятий. Есть что вспомнить и праздновать. Даже в 90-е годы, когда уровень добычи и переработки руды опустился до 35 млн т в год, горняки учились работать в иных экономических условиях, по-новому выстраивать отношения с партнерами.
Особой страницей в истории Качканарского ГОКа стал приход Уральской горно-металлургической компании в качестве стратегического партнера. Именно УГМК помогла комбинату в короткий срок решить ряд сложных финансовых и сбытовых проблем, мешавших его развитию. Сегодня появились дополнительные возможности для решения и технических и социальных задач. Думаю, что стабильно работая на уровне проектной мощности, мы через несколько лет станем расширять производство. Ведь качканарские железо-ванадиевые окатыши востребованы, спрос на них растет, и его надо удовлетворять.
|