Андрей Угаров Заместитель генерального директора ОАО "ОЭМК" по коммерции
Особое место Оскольского электрометаллургического комбината в российской металлургии объясняется отнюдь не количественными показателями производства. Наш комбинат не относится к числу супергигантов, как Магнитка или Северсталь, хотя 2 млн. т стали и более 1,5 млн. т проката в год не так уж мало даже по российским меркам. Специфика ОЭМК в технологических принципах, которые выводят наше предприятие в разряд уникальных производств. Здесь реализована концепция компактного высокопроизводительного металлургического производства, в котором прогрессивная технология основных переделов оптимально сочетается с высоким уровнем экологической чистоты. ОЭМК это первое и пока единственное в России предприятие бездоменной металлургии и крупнейшее производство подобного типа в Европе. Среди основных организационно-технологических особенностей Оскольского электрометаллургического комбината можно отметить следующие. 1. На ОЭМК впервые в российской металлургии в промышленном масштабе была использована технологическая схема, основанная на прямом получении железа из руды, что позволяет исключить из металлургического цикла достаточно сложные и капиталоемкие объекты коксодоменного передела (аглофабрику, коксохимическое производство, доменный цех), которые являются главными источниками атмосферных загрязнений. Это позволило существенно улучшить экологическую ситуацию в регионе и условия труда на предприятии за счет существенного сокращения выбросов серы, фенолов, цианидов и других вредных веществ. 2. Использование металлизованных окатышей в качестве основного шихтового материала в сталеплавильном переделе позволяет получать металл фактически нового качества, особой чистоты, с содержанием вредных примесей (в том числе цветных металлов) в два три раза ниже, чем в стали, выплавленной традиционными способами. Среднее содержание остаточных элементов в стали, изготовленной из металлизованной шихты, составляет, в %: серы 0,006, фосфора 0,008, никеля 0,05, меди 0,06. Используемая технология позволяет регламентировать содержание остаточных цветных металлов, в %: свинца менее 0,003, цинка менее 0,004, сурьмы менее 0,003, олова менее 0,01, висмута менее 0,005. Эти показатели особенно важны в связи с растущим загрязнением поступающего на комбинат металлолома. 3. Выплавка высококачественной стали осуществляется в сверхмощных электродуговых печах с последующей непрерывной разливкой металла на заготовку сечением 300х360 мм. Печь емкостью 150 т с трансформатором мощностью 90 МВА для снижения вредных воздействий заключена в специальный шумоизолирующий кожух, шихтовые материалы непрерывно загружаются в процессе плавки через отверстие в своде печи. 4. На комбинате используется уникальная для России система гидротранспорта для поставки железорудного концентрата в виде пульпы с Лебединского ГОКа, нашего сырьевого партнера. Кроме очевидного выигрыша в производительности и механизации труда, это позволило исключить железнодорожные перевозки с их зависимостью от колебаний погоды, необходимостью обслуживания вагонов и использования погрузочной техники. Процесс транспортировки сырья бесшумен, легко поддается контролю и регулированию. 5. Оригинальная система транспорта применяется для межцеховых и внутрицеховых перевозок в виде конвейерных систем и специального автотранспорта, что позволило сформировать более компактную планировку предприятия. В основных переделах используются, как правило, наиболее прогрессивные технологические приемы и рациональные параметры производства и контроля качества (внепечная обработка жидкого металла, защита от вторичного окисления металла на МНЛЗ, автоматическое поддержание уровня металла в кристаллизаторах, водовоздушное вторичное охлаждение заготовок, регулируемое охлаждение литой заготовки, неразрушающие методы контроля проката), что позволяет гарантированно получать металлопродукцию с заданными качественными характеристиками. Например, технологические, механические и физические свойства, в частности пластичность, усталостная прочность, прокаливаемость стали при горячей и холодной деформации, существенно выше, чем у металла других заводов. Это позволяет в 1,5 3 раза повысить стойкость и соответственно сократить износ волочильного инструмента и штампов при последующей обработке нашего металла у потребителей.
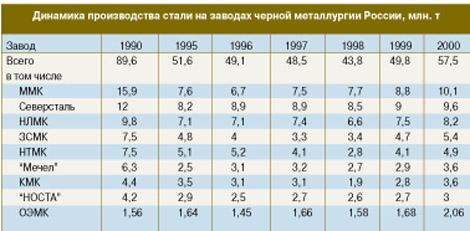
Основная продукция комбината сортовая и трубная заготовка из качественных, высоколегированных, в том числе никельсодержащих, сталей для машиностроительных, подшипниковых, автомобильных, тракторных заводов, предприятий ВПК. Среди трубных заводов основные потребители трубной заготовки Первоуральский Новотрубный и Синарский трубный заводы, предприятия украинской компании "Интерпайп" (Никопольский и Нижнеднепровский). Среди главных потребителей в машиностроении ГАЗ, ВАЗ, Липецкий и Владимирский тракторные заводы. Экспортная продукция включает поставки металлизованных окатышей (в прошлом году около 480 тыс. т), трубной заготовки в некоторые европейские страны (Германия, Румыния). Работа на зарубежных рынках сложна. Далеко не все потребители готовы покупать нашу продукцию, которая имеет значительно более высокие качественные параметры и стоит несколько дороже, чем у наших конкурентов. Существенной проблемой, препятствующей расширению экспорта, являются также антидемпинговые меры, которые активно применяются против российских металлургов. За 20-летнюю историю комбината прошлый год был самым удачным. По сравнению с 1990 годом выпуск товарной продукции увеличился на 27 %, производство окатышей на 8 %, стали на 32 %, проката на 11 %. Это свидетельствует прежде всего о том, что ОЭМК преодолел сложный период адаптации к рыночным условиям и вышел на новый уровень своего развития. Используя благоприятные внешние факторы, такие, как изменение валютного курса после дефолта, мы существенно улучшили финансовые показатели. Однако ситуация нынешнего года внушает определенные опасения. Совершенно непредсказуемо поведение энергетиков и МПС. В текущем году, например, уже два раза повышались тарифы на электроэнергию, что при нашем энергоемком производстве существенно влияет на себестоимость металлопродукции. Негативную роль сыграло и январское повышение цен на газ. Наконец, еще одним ударом по рентабельности производства стало повышение с 1 июля тарифов на грузовые железнодорожные перевозки. В подобной ситуации крайне трудно сохранить приемлемый уровень цен на металлопродукцию и не потерять своих постоянных потребителей в Уральском регионе. В последние годы заметно обострилась конкуренция на внутреннем рынке. Акционерные общества "НОСТА", НТМК, "Мечел" производят однотипную с ОЭМК сортотрубную продукцию, и, естественно, бороться приходится за получение заказов одних и тех же потребителей. В этом соперничестве наше главное оружие качество металлопродукции, которое, как правило, выше, чем у конкурентов. Главные экономические проблемы мы надеемся решить с вводом в эксплуатацию стана 350 осенью этого года. Пуск стана позволит комбинату выйти на российский рынок с высококачественным сортовым прокатом круглого, квадратного, шестигранного сечения размерами от 12 до 75 мм. Годовая производительность стана 1 млн. т, в том числе около 700 тыс. т прутков длиной до 12 м и 300 тыс. т металлопродукции в мотках массой до 2,5 т. Марочный сортамент включает конструкционные углеродистые и легированные стали, подшипниковые стали, рессорно-пружинные стали, а также стали для холодного выдавливания и высадки и инструментальные. По своим геометрическим и качественным параметрам эта металлопродукция будет превышать требования соответствующих российских ГОСТов и зарубежных стандартов (DIN 59110 и 59115). Установленное в линии стана оборудование позволяет реализовать передовые технологии деформации, отделки и контроля металлопродукции. В частности, предусмотрены поточный контроль и отделка исходной заготовки, ее нагрев в методических печах с шагающим подом с регулируемым температурным режимом и возможностью горячего посада. Прокатка осуществляется в непрерывном режиме в мелкосортной и среднесортной линиях. При этом высокая жесткость рабочих клетей, автоматическое согласование скоростей, система петлерегулирования, наличие калибровочного блока за мелкосортной линией позволят получать прокат высокой точности в пределах плюс-минус 0,1 мм. В процессе прокатки может контролироваться режим деформационно-термического упрочнения металла за счет установок ускоренного охлаждения. При необходимости прокат может поставляться в термообработанном состоянии термическая обработка может выполняться как в потоке стана, так и вне его, в печах с защитной атмосферой. Отделочные операции включают: правку, контроль, в том числе ультразвуковую дефектоскопию, абразивную зачистку, шлифовку, обточку и, в случае необходимости, полировку поверхности проката. Главными потребителями металлопродукции стана 350, скорее всего, будут автомобильные, подшипниковые и метизные заводы. Но следует сказать, что занять нишу на этом рынке и потеснить конкурентов будет весьма непросто. Расчеты показывают, что для полной загрузки нашего прокатного передела при выходе стана 350 на проектный уровень мы должны выплавлять около 2,5 млн. т стали в год, что почти на 25 % превышает сегодняшний уровень. Пуск стана 350 потребует значительно увеличить ежегодную выплавку стали. Это существенно повысит загрузку электросталеплавильного цеха, где мы в этом году предполагаем поставить на одной из печей газокислородный модуль, который за счет ускорения плавки может обеспечить прирост в 50 тыс. т на один агрегат. Комплекс мер по модернизации производства включает также установку первой в России машины электромагнитного перемешивания металла на МНЛЗ, что связано с требованиями рынка по качеству стали. В первичном переделе последовательно проводятся ремонт и обновление установок металлизации. Следует подчеркнуть, что финансирование всех программ модернизации комбината мы осуществляем за счет банковских кредитов (прежде всего Сбербанка) и собственных средств. Одним из важных событий последнего времени стало создание холдинга "Газметалл" для более тесной координации экономических и финансовых интересов ОЭМК и Лебединского ГОКа. Мы надеемся, что в результате удастся объединить производственные потенциалы наших предприятий, ежегодные обороты которых составляют около 10 млрд руб. и 7 млрд руб. соответственно, создать единую рациональную систему управления. Это существенно повысит экономическую эффективность интегрированной структуры и расширит инвестиционные возможности предприятий. Важнейшим уроком прошедшего десятилетия, по-видимому, можно считать, что мы сумели сохранить в целом свой уникальный технический потенциал, научились работать на рынке, опираясь в первую очередь на собственные силы, и создать неплохой задел для дальнейшего продвижения вперед.
|