|
|
Журнал |
|
Архив |
|
Подписка |
|
Реклама |
|
САММИТ |
|
Книжная полка |
|
Контакты |
|
В начало |
|
|
|
| |
|
|
 |
№5' 2004 |
версия для печати
|
|
МНОГО АМПЕР ДЕЛАЮТ ЛЕГКИЙ МЕТАЛЛ |
Производство первичного алюминия процесс весьма энергоемкий, но при этом отрасли удается неуклонно повышать эффективность использования энергии. Насколько еще можно снизить ее потребление за счет улучшения технологии электролиза? |
о сравнению с большинством других металлов алюминий плохо восстанавливается из природного сырья из-за его высокого сродства к кислороду. Поэтому требуются значительные энергозатраты, и промышленное производство алюминия не удавалось наладить до конца Х1Х века.
Система Холла-Херулта (Hall-Héroult), при которой глинозем растворяют в электролитной ванне в расплавленном криолите (алюминиево-натриевом фториде) и подают ток большой силы через электроды, по-прежнему составляет основу современной технологии производства первичного алюминия. Однако эта технологическая схема претерпела значительную эволюцию и продолжает совершенствоваться компанией Pechiney в процессе разработки технологии АР50 (Pechiney’s AP50). Ее планируют применить в новом комплексе с производственной мощностью 460 тыс. т в год на заводе Coega, ЮАР, хотя новый владелец, компания Alcan, пока еще не принял решения о продолжении этого проекта.
Потребность в энергии, необходимой для производства алюминия из сырья, конечно, существенно повлияла на выбор места, так как алюминиевые заводы, как правило, сосредоточены в районах, обеспеченных дешевой электроэнергией. По данным находящегося в Лондоне Международного института алюминия (IAI), более 55 % мирового производства первичного алюминия осуществляется с использованием экологически чистой и возобновляемой электроэнергии, производимой гидроэлектростанциями.
Наибольшая доля эксплуатационных расходов современного предприятия приходится на глиноземный передел около 4045 % текущих издержек, сообщает канадская консультационная компания Hatch Associates. Стоимость энергозатрат составляет не менее 2530 % расходов, а на долю углеродных анодов приходится примерно 15 %.
По мере развития электролизеров для производства первичного алюминия обозначились две основные, связанные с электроэнергией тенденции: неуклонно возрастает сила тока (в амперах), используемого в электролизных ваннах, что уже привело к сокращению удельных капитальных затрат на производство одной тонны алюминия. При этом объем электроэнергии, потребляемой для ее производства, постепенно снизился.
Технология Söderberg по оценке Международного института алюминия (IAI), на ее долю в 2002 году пришлось 25 % мирового производства первичного алюминия создавалась для работы при силе тока примерно в 75 kA, но, как сообщает компания Hatch Associates, в результате технологических улучшений в настоящее время этот показатель возрос примерно до 85 kA.
Совершенствования также привели к росту силы тока на анодных линиях различных типов: система HAL250 компании Hydro Aluminium увеличила сейчас силу тока в камерах с 250 kA до 300 kA, а технология AP18 компании Pechiney подняла силу тока со 180 kA примерно до 200 kA, тогда как ее технология AP30, первоначально рассчитанная на 300 kA, ныне оказывается эффективной при силе тока в 335 kA. Как подразумевает уже само ее название, система AP50 компании Pechiney рассчитана на 500 kA.
Для оценки эффективности процесса электролиза исключительно важен показатель стоимости удельных энергозатрат на один килограмм получаемого из глинозема металла. Самые первые элетролизеры, относящиеся где-то к началу прошлого века, потребляли более 50 кВт . час энергии на каждый килограмм расплавленного алюминия, но с тех пор эта цифра снизилась примерно на 70 % (см. диаграмму), и ныне, по данным IAI, средний мировой показатель составляет лишь немногим более 15 кВт . час/кг.
При этом самые современные элетролизеры потребляют примерно 13 кВт-час/кг, хотя компания Pechiney не разглашает данные об энергоэффективности системы AP50. (Для сравнения: по данным IAI, в 2002 году в мире на получение металлургического глинозема из боксита ушло в среднем 3,6 кВт . час/кг глинозема.)
Повышенная эффективность элетролиза печей было достигнута вопреки одному объективному факту более высокая сила тока на самом деле ведет к более высокому потреблению энергии на один килограмм, говорит Сигмунд Джорвен (Sigmund Gjørven), главный инженер по первичным металлам компании Hydro Aluminium. Увеличить силу тока на линиях электролизных ванн в принципе несложно, отмечает он, намного труднее повысить эффективность потребления энергии.
Определенно бросается в глаза то, что при неуклонном снижении потребления электроэнергии в расчете на один килограмм алюминия темпы этого снижения замедляются и, по-видимому, приближаются к своему пределу (см. диаграмму). Отчасти это объясняется уже самим процессом Холла-Херулта он осуществляется при температурах 950980°C, что определяет основную долю потребности в энергии.
Насколько еще можно сократить потребности в электроэнергии при производстве первичного алюминия? Теоретически минимальный объем энергии, требуемой для переработки глинозема в алюминий и отделения кислорода, составляет 6,34 кВт . час/кг металла. На практике, вероятно, невозможно обеспечить этот минимум, но варианты значительного сокращения потребления энергии все-таки существуют можно либо кардинально изменить процесс Холла-Херулта, либо разработать полностью новую технологию электролиза.
Обилие проектов
Министерство энергетики США сейчас занимается широким кругом проектов, направленных на то, чтобы помочь отрасли эффективнее использовать или, другими словами, сократить потребление энергии. Его портфель по алюминиевой отрасли содержит сейчас примерно 34 проекта, охватывающих весь спектр процесса: первичное восстановление, электролиз, экструзию, литье, прокат и пр.
«Мы стараемся поддерживать сбалансированный портфель, рассматривая технологии модифицирования существующих, а также разработку альтернативных систем», говорит Том Робинсон (Tom Robinson), посредник между отраслью и министерством, занимающийся вопросами технологий производства алюминия.
Что касается первичного электролитного восстановления, особенно выделяется разработка двух «палочек-выручалочек»: инертный анод и смачиваемый катод. Применение инертного анода вместо углеродного предотвращает возникновение углекислого газа с «парниковым эффектом», который в противном случае образуется, когда выделившийся из глинозема кислород вступает в реакцию со стандартным углеродным анодом. Инертный анод также устраняет возможность выбросов загрязняющих перфторированных побочных продуктов и других веществ, которые наносят серьезный вред окружающей среде.
Избавление от необходимости установки углеродных анодов является еще одним значительным плюсом, позволяющим сократить на 15 % эксплуатационные расходы и на 20 % капитальные издержки электролиза.
При использовании смачиваемого катода для поддержания нормального электрического контакта с катодом требуется лишь тонкая пленка расплавленного алюминия. При стандартном же углеродном катоде необходима более глубокая лунка для металла, которая затем подвергается воздействию электромагнитных колебаний. Эти колебания ограничивают минимально возможный промежуток между анодами и катодом, но при смачиваемом катоде разрыв может быть еще меньше, и никакой опасности короткого замыкания при этом не возникнет.
В свою очередь, меньший разрыв между анодами и катодом означает, что для поддержания силы тока требуется более низкое напряжение, и это тоже ведет к снижению потребляемой в ваннах энергии.
Согласно оценкам, использование смачиваемых катодов в сочетании с инертными анодами может сократить потребность в энергии для производства первичного алюминия на 2530 %. Однако достичь эту цель не так легко, как может показаться, при температуре в 950°C расплавленный криолит является весьма коррозионно агрессивным, и потому поиск подходящих материалов, наряду с поиском альтернативных электролитов, которые могут функционировать при более низких температурах, ведется уже многие десятилетия.
Один из связанных с первичным алюминием проектов, спонсируемых министерством энергетики США, осуществляется лабораторией Argonne National Laboratory в штате Иллинойс совместно с компанией Noranda Aluminum. Этот проект предусматривает применение электролита, основанного на кальцийалюминийфториде, который можно использовать при температуре в 700°C. При такой температуре электролит может растворять 4,5 % веса глинозема, что достаточно для работы в коммерческих масштабах.
Проведенные исследования показали, что в качестве инертных анодов в этой системе можно успешно использовать алюминиевую бронзу, тогда как титановые боридно-углеродные композитные материалы могут использоваться в качестве смачиваемых катодов. Алюминий производится с чистотой, превышающей 99,5 %, и, как сообщают, результаты выглядят довольно многообещающими, хотя проект и находится еще в начальной стадии осуществления. Более низкая температура делает возможным более широкий выбор материалов и, по сообщениям, имеет большой потенциал для улучшения и оптимизации условий выполнения процесса.
Примером кардинально нового процесса, разработку которого спонсирует министерство энергетики США, является низкотемпературное восстановление глинозема в ионных жидкостях, исследованием которого сейчас занимаются в университете штата Алабама в городе Тускалуса. В проекте участвуют пять партнеров, включая компанию Century Aluminum из города Хоусвилль, штат Кентукки.
Ионные жидкости содержат соли хлора и фтора, которые при комнатной температуре обычно находятся в твердом состоянии. При смешивании они образуют жидкости, которые стабильны при температуре до 350°C. Эти ионные жидкости способны заменить криолит для растворения глинозема, а потому могут послужить основой действительно низкотемпературного электролизного процесса, выполнять который будет возможно даже при температуре ниже 100°C.
Хороший прогресс
Работа «продвигается хорошо», говорит Рамана Редди (Ramana Reddy) из университета штата Алабама, по словам которого эта технология может обеспечить производство алюминия при расходе в 9,5 кВт . час/кг. Он отмечает, что процесс не приводит к появлению ни угарного, ни углекислого газа, а весь образующийся хлор может быть переработан в алюминиевый хлорид.
У разработчиков проекта, который был начат в марте 2003 года, есть еще два года, и партнеры сейчас занимаются поиском источников его дальнейшего финансирования, чтобы в будущем вывести процесс на уровень пилотных испытаний на заводе.
Между тем у ведущих производителей есть свои собственные научно-исследовательские программы. Компания Hydro Aluminium, например, занята исследованием многих аспектов элетролиза, особенно сосредотачиваясь на поиске способов увеличения электропроводимости стандартной линии ванн.
На протяжении последнего столетия повышение эффективности технологии происходило по нарастающей, и дальнейшие постепенные продвижения в этом направлении не удивят. Но возможен ли качественный прыжок к значительно более совершенной технологии? При наличии широкого набора проектов исключать это нельзя, но в то же время долговечность процесса Холла-Херулта указывает на то, сколь трудной является разработка альтернативных технологий.
Для ознакомления с портфелем министерства энергетики США по алюминию посетите вебсайт: www.oit.doe.gov/aluminum
Гистограмма:
Удельные затраты электроэнергии на один килограмм первичного алюминия
ENM_Primary-Electrical Energy for Electrolysis (1900-2001).eps
Источник: Международный институт алюминия (IAI)
Фото:
Основные компоненты производства первичного алюминия остаются неизменными уже более века
Источник: компания Pingguo Aluminium
ENM_Primary-Chalco_Pingguo potline.jpg
|
|
|
|
|
текущий номер

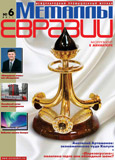
предыдущий номер

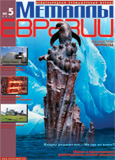
|
|