|
|
Журнал |
|
Архив |
|
Подписка |
|
Реклама |
|
САММИТ |
|
Книжная полка |
|
Контакты |
|
В начало |
|
|
|
| |
|
|
 |
 |
№3' 2004 |
версия для печати
|
|
КУДА ВПАДАЮТ СТАЛЬНЫЕ РЕКИ? |
|
Александр Лаврик
Директор ОАО «ЗСМК» по производственным вопросам
последнее время непрерывная разливка как основной технологический процесс определяет прогресс в черной металлургии. В настоящее время около 85 % всей производимой в мире жидкой стали разливается непрерывным способом. За последние 10 лет более половины всех действующих в мире МНЛЗ были либо реконструированы, либо построены заново. Надо полагать, что и в ближайшие 1015 лет создание высокоэффективных технологий и оборудования для непрерывной разливки продолжится ускоренными темпами. Это значит, что приобретение на западном рынке уже бывших в эксплуатации МНЛЗ вряд ли может способствовать преодолению технического отставания отечественной металлургии. Ведущие предприятия отдают предпочтение современным видам оборудования.
Еще в конце 80-х годов процесс непрерывной разливки стали получил всемирное признание и стал определяющим в сталелитейном производстве. В настоящее время непрерывная разливка освоена более чем в 90 странах мира, действует примерно 1750 МНЛЗ, что позволяет разливать на них более 85 % всей производимой стали. Ожидается, что к 2020 году практически все предприятия черной металлургии будут оснащены машинами непрерывной разливки стали.
Анализируя путь, который прошла эта технология в течение 4045 лет, можно выделить несколько этапов. На первом (1950-е середина 1960-х годов) осуществлялась теоретическая проработка и промышленное оформление способа непрерывной разливки стали, что позволило создать объективные предпосылки для уверенного выхода на рынок новых технологий. Второй этап (1960-е начало 1970-х годов) характеризуется быстрым внедрением МНЛЗ на многих металлургических заводах промышленно развитых стран мира. В этот период производителям МНЛЗ пришлось конкурировать с консервативным, но сравнительно дешевым процессом разливки стали в слитки. Потребовалось создание новой системы технологий в сталеплавильном переделе. В результате основные показатели, достигаемые при непрерывной разливке стали, заметно превзошли лучшие показатели слиткового передела.
Третий этап (1970-е 1980-е годы) характеризуется двумя основными моментами. Во-первых, окончательно оформилась тенденция реконструкции сталеплавильных цехов с целью их оснащения МНЛЗ. Кроме того, шла адаптация процесса непрерывной разливки к различным типам заготовок, используемых в прокатном производстве (сортовая, блюм, сляб, фасонная, круг и др.). Но стратегически более важным стало строительство новых сталеплавильных цехов и металлургических заводов со стопроцентной непрерывной разливкой, в первую очередь, на слябы и блюмы. На четвертом этапе, начало которого следует относить к концу 1980-х началу 1990-х годов, заметно снижение роста объемов производства стали в мире и практически полное его отсутствие в ведущих металлургических странах. Это явилось стимулом для создания новых эффективных технологических процессов внепечной обработки и непрерывной разливки. Характерно, что примерно 50 % всех МНЛЗ было либо сооружено, либо реконструировано именно в последние 10 12 лет.
В ККЦ-2 ЗСМК в начале 90-х годов построена восьмиручьевая МНЛЗ для производства круглой (150300 мм) и прямоугольной (150x200 мм) заготовки, спроектированная и изготовленная фирмой Danieli (Италия). Необходимость строительства машины непрерывного литья заготовок была вызвана значительным количеством товарных слитков, которые отгружались на другие заводы и только после транспортировок и переделов превращались в готовую продукцию. Чтобы исключить затраты на перевозки и последующие переделы было принято решение о строительстве трубной МНЛЗ. Производство таких заготовок дает наибольший технико-экономический эффект, поскольку они по своим размерам поперечного сечения и профилю наиболее близки к готовой продукции.
Поскольку в стране не было накоплено достаточного опыта производства, да и эксплуатации агрегатов для непрерывного литья мелкосортных заготовок в России работали всего четыре маломощных установки на «Сибэлектростали», «Амурстали» и «Серпе и Молоте» трубную МНЛЗ приобрели за рубежом. Это была одна из немногих в мире восьмиручьевых машин с разливкой 320-тонных плавок, производительностью до 1 млн т заготовок в год. Для отработки технологии и проверки работоспособности всех узлов и механизмов 13 февраля 1995 года в работу были введены четыре ручья. Разливка велась одиночными плавками в заготовку максимального сечения диаметром 300 мм. В 1995 году на трубной МНЛЗ разлито более 30 тыс. т стали и в декабре достигнут выход годного 91,8 % (в среднем за год 89 %). В 1996 1997 годах разлито более 35 тыс. т стали, выход годного в среднем за 1997 год достиг 95,8 %. Была освоена разливка стали 10, 20, 40, 45 по ГОСТ 1050-88 и ЗОГ2 по ГОСТ 4543-71.
Объем производства непрерывнолитых заготовок менялся из месяца в месяц. На это влияли различные факторы. В целом количество разлитого металла в 1996 году уменьшилось, в 1997-м несколько возросло, но уровня 1995 года не достигло. Это объяснялось неравномерностью поставок сырья, недостаточным обеспечением качественными огнеупорами, металлоломом, ферросплавами, запасными частями и т.д., а также организационными причинами: невысоким уровнем спроса, неясной ценовой политикой. Кроме того, литье в четыре ручья вместо восьми и отсутствие системы автоматического контроля уровня металла в кристаллизаторах не позволяли организовать серийную разливку плавок и освоить производство заготовок мелких сечений.
С октября 1997 года из-за все более усложняющегося финансового положения ЗСМК и по ряду других причин трубная МНЛЗ была фактически законсервирована. В период обострения экономического кризиса в России (с июня 1997 года по август 1998 года) программы развития комбината осуществлялись неудовлетворительно или не осуществлялись вовсе. С июля 1997 года на ЗСМК по решению арбитражного суда была введена процедура внешнего управления.
Ситуация изменилась после прихода на комбинат управляющей компании «ЕвразХолдинг». В ноябре 2001 года ей удалось вывести предприятие из состояния банкротства, расплатиться с кредиторами. В кратчайший срок удалось отремонтировать основные агрегаты и обеспечить их качественным сырьем, поднять производство на максимальный (при работе двух доменных печей) уровень и сделать предприятие прибыльным. Это произошло в основном за счет значительного роста выпуска основной продукции, снижения расхода кокса и чугуна, а также правильно выбранной маркетинговой стратегии увеличения доли поставок на внутренний рынок.
В то же время оставался нерешенным целый ряд проблем, обусловливающих сложное положение ЗСМК. К ним можно отнести диспропорции мощностей по выплавке стали и производству проката, слитковую технологию разливки, несовременный проволочный стан, монопрофильную специализацию комбината. Укрепление финансовой стабильности предприятия тесно связано со скорейшим переходом на непрерывную разливку стали. Это дало новый толчок развитию на комбинате этой технологии. Было принято решение о полном переводе на нее сталеплавильного производства с отказом от устаревшей технологии разливки в слитки. Для обеспечения высокого уровня качества стали предусматривается установка агрегатов «печь-ковш». Они предназначены для обработки металла перед МНЛЗ и позволяют сократить расход ферросплавов, обеспечить однородность химического состава и температуры металла в ковше, снизить удельный расход огнеупоров. Использование таких агрегатов повысит качество выплавляемой стали, сделает технологию производства стали более гибкой, расширит марочный сортамент сталей в сторону более качественных, в том числе предназначенных для глубокой вытяжки, улучшит условия труда.
Объем предстоящей реконструкции включает в себя строительство объектов в двух кислородно-конвертерных цехах.
ККЦ-1:
три сортовые шестиручьевые МНЛЗ для отливки заготовок сечением 100х100 и 150х150 мм производительностью от 900 тыс. т до 1,2 млн т в год;
двухпозиционный агрегат «печь-ковш» для ковша емкостью 140 т;
однопозиционный агрегат «печь-ковш» для ковша емкостью 140 т.
ККЦ-2:
двухручьевая слябовая МНЛЗ для отливки заготовки сечением 150-250х1050-1750 мм производительностью 1900 млн т в год;
двухпозиционный агрегат «печь-ковш» для ковша емкостью 320 т.
Пуск сортовых МНЛЗ в ККЦ-1 и слябовой МНЛЗ в ККЦ-2 позволит производить в год 1,8 млн т слябов из низколегированной стали, сократить количество обрези и отходов. В результате реализации проекта комбинат перейдет на выпуск спокойных марок стали, а в ККЦ-2 будет налажена выплавка низколегированной стали. Однако переход на технологию непрерывной разливки приведет к повышению требований как к исходному сырью агломерату, коксу, так и к последующему переделу прокатному. Предстоит реконструкция аглоизвесткового, коксохимического производств, прокатного передела. В качестве возможного варианта развития предусматривается сооружение на ЗСМК нового проволочного стана, изготовляющего катанку диаметром 5 5,5 мм для производства кордовой, катаной и пружинной проволоки, проката для холодной высадки. Возможности такого стана с позиций адаптации к требованиям рынка проката практически не ограничены.
На сегодняшний день Запсиб достиг проектной мощности в 1,3 млн т сортовой заготовки на введенной в прошлом году в действие МНЛЗ в ККЦ-2. Значительная часть продукции была продана внешним потребителям. Кроме того, пуск МНЛЗ позволяет нарабатывать технический и технологический опыт работы на агрегатах, готовить персонал. В этом же цехе уже ведутся работы по установке двухпозиционного агрегата «печь-ковш». Готовятся площадки под строительство слябовой МНЛЗ и новой опорной электростанции, которая обеспечит необходимой электроэнергией весь сталеплавильный комплекс. Выведена из консервации и продолжает строиться коксовая батарея №1, начат крупный капитальный ремонт доменной печи №2, ведется работа по контрактам для трех новых сортовых МНЛЗ в ККЦ-1.
Таким образом, ключевыми точками вложения инвестиций являются переделы, позволяющие с максимальной эффективностью использовать имеющиеся на комбинате металлургические агрегаты большой единичной мощности. После завершения модернизации Запсиб будет работать тремя доменными печами с производством чугуна 6,2 млн т в год. На машинах непрерывного литья станет разливаться 7,2 млн т стали. Полностью будут загружены прокатные станы, более 2 млн т заготовки мы предложим мировому рынку. Разумеется, введение новых технологий повлечет сокращение ряда переделов. Из технологической схемы исчезнут цехи изложниц и подготовки составов, блюминг.
Прогнозируемый экономический эффект преобразований складывается их двух частей. Во-первых, расходы снижаются за счет сокращения металлургических переделов и значительной экономии металла при разливке стали и перекате заготовки на готовый сорт. При традиционной разливке стали в изложницы в технологическую обрезь уходит более 0,5 млн т металла. Он, правда, возвращается в виде оборотного лома, но на это тратятся практически те же средства, что и на товарную продукцию, хотя в товарную часть этот металл не попадает. Как показывает мировой опыт, переход на непрерывную разливку позволяет снизить расходы в металлургических переделах до 10 12 долл./т. Во-вторых, дополнительную прибыль комбинат получит за счет увеличения объема продаж.
После реконструкции изменится и сортамент выпускаемой продукции. Кроме традиционного сортового проката, комбинат начнет выпускать 2,4 млн т слябовой заготовки. Введение в эксплуатацию агрегатов «печь-ковш» даст возможность значительно расширить марочный сортамент, а, следовательно, перейти от производства рядовых марок стали к легированным.
Кроме того, планами реконструкции предусматривается строительство нового проволочного стана, позволяющего расширить диапазон профилеразмеров горячекатаной проволоки, при этом мы будем иметь возможность минимизировать диаметр до 4,5 мм. Также планируем производство тонкого горячекатаного листа.
Уже сегодня рентабельность производства достигла 23,1 %, производительность труда более 200 т стали на одного работающего, а это третий показатель в отрасли. После реконструкции последний увеличится еще на 30 %.
|
|
|
|
|
текущий номер

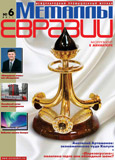
предыдущий номер

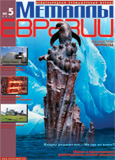
|
|