|
|
Журнал |
|
Архив |
|
Подписка |
|
Реклама |
|
САММИТ |
|
Книжная полка |
|
Контакты |
|
В начало |
|
|
|
| |
|
|
 |
№4' 2003 |
версия для печати
|
|
ТРЕБОВАНИЯ КОНЕЧНЫХ ПОТРЕБИТЕЛЕЙ: НОВЫЕ ВОЗМОЖНОСТИ |
|
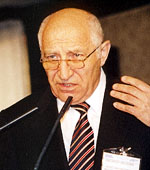 Георгий Скударь Президент ЗАО «Ново-Краматорский машиностроительный завод» |
|
«Стать равными среди лучших»
роблемы, которые есть в металлургии, созвучны и нам, машиностроителям. Многие украинские заводы и сегодня находятся в плачевном состоянии, хотя есть примеры довольно активной деятельности, когда за короткое время удалось провести диверсификацию производства, создать новые инжиниринговые разработки, поднять объемы производства. В 1994 году с полным завершением приватизации НКМЗ полностью выкуплено у государства. На первом этапе была внедрена дивизиональная структура управления, разработаны новые мотивационные системы оценки труда. Стратегический менеджмент стал важнейшим инструментарием для разработки комплексных программ развития.
В соответствии с требованиями рынка своевременно был взят курс на экспортную ориентацию, агрессивный маркетинг, гибкую ценовую политику, техническое перевооружение, внедрение ресурсосберегающих технологий, диверсификацию производства и модернизацию выпускаемого оборудования, разработку новых экономических методов хозяйствования. С 1998 года наблюдается рост основных показателей. Достигнутые успехи, высокая эффективность функционирования это закономерный результат реализации стратегии ускоренного эволюционного развития на основе биореинжиниринга, включающего технические, технологические, организационные и индивидуальные преобразования.
На основе комплексных стратегических планов развития созданы исключительные возможности в металлургическом, механосборочном и сварочном производствах. Только за последние 4 года в развитие предприятия инвестировано более 240 млн гривен.
В инжиниринговом центре НКМЗ трудятся около 1800 конструкторов и технологов. Мы создали у себя на предприятии специальный центр «НКМЗ-Автоматика», где проектируются и изготавливаются силовые системы агрегатов, системы управления всех уровней на основе современной элементной базы с использованием собственного программного продукта. С 1994 года ежегодно подтверждаем соответствие НКМЗ международным стандартам ISO 9001. Это обеспечило доступ на мировой рынок интеллектуальной техники. В 2003 году выполнены работы для сертификации на соответствие новому международному стандарту ISO 9000 версии 2000 года.
На базе собственных инжиниринговых разработок, а также совместно с рядом украинских и российских институтов создано качественно новое оборудование с высокими ценностными характеристиками для добывающей и металлургической отраслей, успешно конкурирующее с лучшими мировыми аналогами. В области металлургического оборудования созданы и поставляются:
совместно с Молдавским металлургическим заводом и ВНИИметмашем металлургический комплекс для реконструкции кислородно-конверторных цехов в составе установки «печь-ковш», сортовой машины непрерывного литья заготовок производительностью 1 млн т проката в год;
совместно с фирмой VAI (Австрия) слябовые машины непрерывного литья заготовок;
установки глубокого вакуумирования стали с разрежением до 0,5 мм рт. ст. (0,67 мБар);
уникальные листоправильные машины;
системы ламинарного охлаждения полосы;
теплосохраняющие экраны;
комплекс оборудования для смотки рулонов.
НКМЗ может предложить конкурентоспособную продукцию взамен устаревшего и изношенного оборудования для добычи и обогащения руд. Мы предлагаем роторные экскаваторы, новые буровые станки, экскаваторы карьерные и вскрышные гусеничные, дробильно-перегрузочные установки, конвейеры наклонные, отвалообразователи. Создаем новейшие виды прессов, в частности, комплекс оборудования по формовке трубной заготовки диаметром от 500 до 1420 мм. Для угольной промышленности созданы высокопроизводительные проходческие комбайны, скребковые конвейеры, машины поддирочно-погрузочные с резцовым и ковшовым исполнительными органами.
Рынок уже сегодня требует высокоэффективные машины с новыми параметрами качества и производительности. НКМЗ готов реализовать следующие проекты:
литейно-прокатный агрегат и прокатный стан с моталками в печах производительностью до 1,5 млн т продукции в год, с толщиной горячекатаного листа до 1 мм;
освоение дуговых сталеплавильных печей нового поколения, которые совмещают в себе элементы кислородного конвертера, мартеновской печи, электродугового агрегата и являются универсальными по использованию в металлошихте от 100 % скраба до 100 % железа прямого восстановления и 40 % чугуна в любом соотношении;
разработанный на базе дуговых печей совмещенный способ выплавки стали, приспособленный к любому виду шихты.
Создание наукоемкой продукции это не только разработка и внедрение прогрессивных ресурсосберегающих технологий и применение высокопроизводительного оборудования, но и наличие высококвалифицированного персонала, являющегося главным стратегическим ресурсом фирмы. На НКМЗ разработана и внедрена комплексная система подготовки и переподготовки кадров, позволившая трансформировать предприятие в самообучающуюся организацию с охватом всеми формами обучения и переподготовки более 5 тыс. человек.
Новые технические возможности, эффективные системы управления и мотивации труда, постоянно повышающий квалификацию персонал позволяют НКМЗ с оптимизмом смотреть в будущее, ускоренно пройти этапы развития, чтобы к 2015 году приблизиться к европейскому уровню и стать равными среди лучших на мировом индустриальном рынке. 
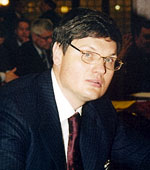 Анатолий Седых Президент ЗАО «Объединенная металлургическая компания» |
|
«ОМК заинтересована в создании реальной конкуренции»
а долю трубной промышленности России приходится более 22 % внутреннего потребления стали. Производственные мощности российских производителей составляют 1314 млн т труб в год. В 2002 году внутренний рынок потребил 4,9 млн т труб. Часть их импортируется. В основном это высокопрочные, коррозионностойкие и одношовные трубы диаметром 12201420 мм как с наружным, так и с внутренним покрытиями.
Вместе с тем в России все больше производится импортозамещающей продукции. Одним из таких производителей является ОМК. Объем продаж компании в 2002 году превысил 600 млн долл. Среди основных производителей труб на долю ОМК приходится 20 % объемов продаж. Компания ежегодно закупает 900 тыс. т плоского проката, что составляет около 10 % внутреннего потребления.
Нефтегазовая отрасль России это 225 тыс. км магистральных трубопроводов, причем этот показатель постоянно растет. В 2003 году спрос на трубы большого диаметра в России должен увеличиться до 1,1 миллиона тонн. Наш прогноз основан на активизации нефтегазовых компаний в строительстве нефте- и газопроводов. На сооружении Балтийской трубопроводной системы ожидаемое потребление труб в 2003 году составит 270 тыс. т. Должны быть реализованы сахалинские проекты.
Основные преимущества будут иметь те производители, кто поставляет продукцию с лучшими качественными характеристиками. ОМК готова к такой конкуренции. Мы планируем увеличить экспорт труб большого диаметра до 25 % от общего выпуска. Компания ведет активную экспортную политику, участвуя в международных тендерах в странах СНГ, в Индии, на Ближнем Востоке и др. В проектах Сахалин-1 и Сахалин-2 ОМК одержала победы в трех тендерах, часть продукции по которым уже поставлена. Внедрение новейших технологий в производство труб, большие производственно-технические и экономические возможности ОМК, а также наличие сертификатов и лицензий ISO 9001, API основа для расширения деятельности компании на международном рынке.
В 2003 году ОМК планирует увеличить объемы продаж труб большого диаметра до 330 тыс. т, в том числе на внутреннем рынке до 285 тыс. т. Для удовлетворения возрастающих требований заказчиков на Выксунском металлургическом заводе идет модернизация основного и вспомогательного оборудования, внедряются передовые технологии сварки, неразрушающего контроля. Уже в ближайшее время должен быть освоен выпуск труб диаметром 813 мм и 1067 мм по стандарту API.
Основными поставщиками на российский рынок труб диаметром 12201420 мм являются Волжский трубный завод, Харцызский трубный, Еuropipe. Между ними идет острая конкуренция за заказы Газпрома. Cитуация на рынке осложняется тем, что Газпром до сих пор четко не заявил о своих потребностях в трубах даже на среднесрочную перспективу. Это делает рынок малопредсказуемым. Дополнительную нестабильность на рынок труб большого диаметра вносят и заявления «Северстали» и НТМК о собственных проектах по выпуску труб 1420 мм.
Почему же ОМК, несмотря на все сказанное, приняла решение инвестировать в производство труб 1420 мм. Есть несколько причин. Качество наших труб будет принципиально иным. Предусмотрено производство одношовных прямошовных труб из хладо- и коррозионностойких марок стали высоких групп прочности до Х80, с толщиной стенки до 47 мм, длиной до 24 м. Эти трубы можно использовать для подводных переходов и в сейсмоопасных районах. Линия, которую мы строим, будет способна выпускать трубы не только диаметром 12201420 мм, но и других диаметров, начиная с 530 мм. Причем трубы диаметром 530 мм могут выпускаться с толщиной стенки 26 мм. Такие трубы в России еще не производят. А спрос на них будет возрастать в связи с развитием добычи нефти и газа в шельфовых зонах.
После завершения строительства комплекса производство труб большого диаметра будет состоять из двух независимых линий. Это даст возможность одновременно выполнять несколько заказов на трубы разных диаметров и значительно ускорить их производство.
Рынок труб большого диаметра характеризуется цикличностью, связанной с конъюнктурой нефтегазового рынка. Периоды, когда спрос находится на очень низком уровне, сменяются периодами, когда мощности заводов загружены на 100 %. Мощность линии 1420 на Выксунском заводе 570 тыс. т в год. Имея максимальную производительность, мы сможем значительно увеличивать объемы производства труб в периоды наибольшего спроса и высоких цен. Текущие затраты на передел штрипса в трубу в ОМК наименьшие в СНГ.
На рынке обсадных труб будет усиливаться конкуренция между основными его участниками крупнейшими российскими и украинскими компаниями. ОМК надеется сохранить ведущее место на этом рынке. Одновременно в 20032004 годах будет повышена конкурентоспособность труб за счет их выпуска из низколегированных марок стали с повышенной коррозионной стойкостью, повышения качества резьбового соединения, выпуска труб с высокогерметичным резьбами и др.
Мировая конъюнктура способствовала увеличению экспортных поставок металла при одновременном росте цен. При этом качество штрипса зачастую не соответствовало даже российским стандартам, не говоря о зарубежных. Чтобы не работать в убыток, трубные предприятия были вынуждены поднять цены на трубы. В связи с этим произошло некоторое снижение платежеспособного спроса потребителей. Такая недальновидная политика металлургов привела к тому, что некоторые компании хотят приобрести за рубежом такие трубы, которые до сих пор покупали в России. Дальнейший рост цен может быть опасен для экономики страны.
Как известно, планируется создание единого экономического пространства России, Украины, Белоруссии и Казахстана. Эта проблема носит многогранный характер. Что касается трубной подотрасли, в настоящий момент конкуренция на этом рынке достаточно жесткая. Хотя российские производители практически на 100 % готовы обеспечивать внутренний рынок трубами необходимого качества, тем не менее поставки продукции по импорту пока не снижаются. Сейчас наплыв импорта несколько сдерживается государственными границами и межгосударственными договоренностями. Единое пространство, снимая подобные барьеры, скорее всего еще больше усилит конкуренцию. При этом не исключено снижение загрузки производственных мощностей и сокращение рабочих мест. Объединение также может негативно сказаться на состоянии трубной промышленности России, если на экономическом пространстве не будет создана единая система налогов, сборов и льгот. Но, конечно, существуют и выгоды от экономического объединения. Так, ОМК заинтересована в создании реальной конкуренции между производителями штрипса металлургическими комбинатами России, Украины и Казахстана. 
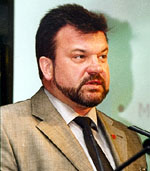 Александр Путноки Первый заместитель председателя правления, технический директор ОАО «Запорожсталь» |
|
«Производство плоского проката является инвестиционно перспективным»
еталлургический комбинат «Запорожсталь» это предприятие с полным металлургическим циклом. Его специализация горячекатаный и холоднокатаный плоский прокат толщиной 0,58 мм. Комбинат единственный на Украине производитель тонколистового проката из нержавеющих и легированных сталей, а также консервной жести. Годовой объем производства стали составляет 3,97 млн т.
Сегодня «Запорожсталь» подтвердила свою жизнеспособность, умение адаптироваться к переменам макроэкономической среды. Основными потребителями продукции комбината являются производители сварных труб, предприятия автомобильного, транспортного и сельскохозяйственного машиностроения. Акционеры и менеджеры «Запорожстали» в качестве своей стратегической цели видят дальнейшее развитие и укрепление предприятия на основе:
организации эффективного управления подразделениями комбината;
совершенствования технологий и реконструкции производства;
сертификации системы управления качеством;
освоения новых видов продукции;
укрепления конкурентных позиций на внутреннем рынке и за пределами Украины, а также региональной деверсификации экспортных поставок.
Следует отметить высокий уровень конкуренции на внутреннем рынке. Доля «Запорожстали» в производстве чугуна, стали и проката составляет 12 % в каждом сегменте, а по горячекатаному прокату 31 %, холоднокатаному 57 %.
Успешная экспортная деятельность комбината подтверждение того, что его продукция правильно позиционируется на рынке и соотношение цена/качество удовлетворяет требованиям потребителей. Для различных покупателей за одни и те же условия поставки устанавливается разная цена. Это вынужденная мера, связанная с очень быстрым изменением конъюнктуры.
На комбинате разработана программа дальнейшего технического перевооружения основных агрегатов, что обеспечивает снижение энергоемкости и металлоемкости производства, улучшение качества и выпуск конкурентоспособной металлопродукции. Основными задачами являются первоочередное обновление прокатного оборудования, радикальная модернизация доменного производства, замена сталеплавильных и разливочных мощностей. Особое значение имеет вертикальная интеграция, приобретение корпоративных прав в сфере снабжения (железорудное сырье, кокс, флюсы), включение предприятий потребляющих отраслей в интегрированные компании.
Специалистами комбината разработаны и внедрены в производство новые прогрессивные технологии и оригинальные инженерные решения, позволившие снизить расход сырьевых, материальных и топливно-энергетических ресурсов, освоить новые виды прокатной продукции. Внедрение оригинальных технических решений позволило освоить выпуск нового вида продукции жести белой шириной 512 мм на имеющемся оборудовании без значительных капитальных затрат.
Особое значение мы придаем повышению мотивации персонала и укреплению социальной сферы, что, в частности, включает контрактную систему найма, оплату труда с учетом результатов трудовой деятельности, обязательное медицинское страхование трудящихся, социальную защиту пенсионеров и ветеранов, подготовку кадров и др.
Стратегия развития металлургической отрасли на Украине предусматривает оптимизацию производства, сбережение экспортного потенциала с целью обеспечения валютных поступлений, повышение конкурентоспособности продукции. Последнее может быть достигнуто за счет уменьшения затрат на ее производство, снижения его энергоемкости, сокращения и вывода из эксплуатации избыточных мощностей и устаревших агрегатов, проведения реструктуризации предприятий, создания промышленно-финансовых групп, обновления производственных фондов.
Таким образом, производство плоского проката на Украине является инвестиционно перспективным направлением. Выработанные стратегии обеспечивают в настоящее время конкурентоспособность этой продукции на внутреннем и внешнем рынках. Дальнейший прогресс будет определяться темпами технических и корпоративных преобразований. 
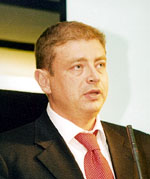 Дмитрий Тарасов Директор службы стратегического развития холдинга «Газметалл» |
|
«В центре России может быть создана мощная база отечественной металлургии»
сновными предприятиями горно-металлургического холдинга «Газметалл» являются Лебединский горно-обогатительный (ЛГОК) и Оскольский электрометаллургический (ОЭМК) комбинаты. ЛГОК крупнейшее в Европе предприятие по добыче и обогащению железной руды и производству высококачественного сырья для черной металлургии. Минерально-сырьевой базой комбината являются железистые кварциты Курской магнитной аномалии. Разработка месторождения ведется с 1971 года открытым способом. Прогнозные запасы оцениваются в 5,5 млрд т, что гарантирует долгосрочную устойчивую работу предприятия.
Оскольский электрометаллургический комбинат первое и пока единственное в России предприятие, где реализованы технологические принципы бездоменной металлургии. Продукция этого крупнейшего производственного комплекса отвечает международным стандартам и сертификатам. ОЭМК является одним из самых молодых металлургических предприятий страны: первая промышленная продукция окисленные железорудные окатыши произведена в 1982 году, первая промышленная плавка электростали в 1984 году, первый прокат получен в 1986 году. В проектировании и строительстве ОЭМК участвовали ведущие фирмы Германии, США, Франции, Италии, в том числе «Мидрекс», «Зальцгиттер», «Лурги», «Корф», «Крупп», «СМС Шлеманн-Зимаг», «Сименс», «АСЕА» («АББ») и др.
За годы своего существования комбинат подтвердил высокую эффективность технологической схемы, основанной на использовании прямого восстановления железной руды и электродуговой плавки стали. При разработке базовой концепции перспективного развития ОЭМК руководство холдинга исходило из собственного практического опыта и основных направлений развития современной металлургии:
динамичного развития концепции мини-заводов полного цикла на основе использования продуктов прямого восстановления железной руды, что позволяет говорить о создании высокорентабельной маломасштабной металлургии, являющейся в некоторых странах основой крупных территориально-промышленных комплексов;
ускоренного развития электрометаллургии в качестве базовой технологии мини-металлургии;
опережающего роста производства качественной металлопродукции в соответствии с развитием спроса на мировом рынке. По-видимому, замедление роста абсолютных объемов производства стальных полуфабрикатов в ближайшей перспективе будет компенсироваться повышением качественных характеристик;
очевидной необходимости корректировки размещения производственных мощностей российской черной металлургии, вызванной непрерывным ростом транспортных и сырьевых затрат в себестоимости продукции ведущих металлургических предприятий Урала и Сибири в долгосрочной перспективе.
Поэтому наиболее перспективным регионом развития является Центр, где на основе существующих предприятий НЛМК, ОЭМК, крупных ресурсов железорудного сырья и относительно доступного энергоносителя природного газа может быть создана мощная база отечественной металлургии с использованием эффективных и экологически безопасных бездоменных процессов
Исходя из этого, основными задачами перспективного развития холдинга «Газметалл» на ближайшее десятилетие являются:
дальнейшее развитие мощностей по производству металлизованного сырья с применением новых прогрессивных технологий;
модернизация цеха прямого восстановления ОЭМК и строительство II, III, IV очередей завода по производству горячебрикетированного железа (ГБЖ) на Лебединском ГОКе;
дальнейшее развитие электросталеплавильного передела ОЭМК с использованием новых технологий и оборудования для непрерывного литья и внепечной обработки с целью увеличения объемов годовой выплавки до 3 млн т и повышения качества металла.
Программу стратегического развития основных предприятий холдинга планируется осуществить в несколько этапов, каждый из которых будет представлять технологически независимый проект, имеющий свое технико-экономическое обоснование, бизнес-план, схему финансирования. Это позволит осуществлять каждый этап с учетом финансово-экономической ситуации и рыночной конъюнктуры.
На первом этапе планируется реализация следующих мероприятий:
увеличение производительности завода ГБЖ Лебединского ГОКа на 20 % за счет внедрения технологии кислородного дутья, предложенной компанией HYL;
увеличение производительности одной установки металлизации ОЭМК на 20 % и достижение годового производства металлизованных окатышей до 2,2 млн т;
строительство новой машины непрерывного литья заготовок (МНЛЗ № 6).
Кроме того, представляется, что в более отдаленной перспективе продукция двух последних мегамодулей ГБЖ будет пневмотранспортом подаваться на расположенный рядом сталеплавильный комплекс, ориентированный на производство тонких слябов, который планируется построить.
Реализация стратегии развития холдинга «Газметалл» обеспечит предпосылки возможного создания к 20122015 годам в центре страны нового горно-металлургического комплекса на базе бездоменной металлургии. 
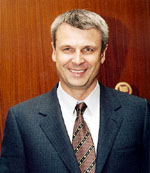 Сергей Носов Управляющий директор НТМК и ЗСМК, старший вице-президент компании «ЕвразХолдинг» |
|
«Стратегия развития группы комбинатов как единого комплекса»
омпания «ЕвразХолдинг» это вертикально интегрированный горно-металлургический комплекс, созданный по отраслевому принципу в 1999 году. В сферу управления «ЕвразХолдинга» входят горнорудные и угольные предприятия, Находкинский морской порт; основу производственной деятельности составляет металлургический комплекс, в который входят Нижнетагильский и Западно-Сибирский металлургические комбинаты и предприятия Кузнецкого металлургического комбината. Сегодня эти заводы производят около 12 млн т товарного проката, включая заготовку для переката, то есть более четверти всей металлопродукции России. В настоящее время 40 % металлопродукции компании поставляется на экспорт. Наш консолидированный оборот составляет более 2 млрд долл. в год.
Все металлургические комбинаты НТМК, Запсиб и КМК вошли в «ЕвразХолдинг» в стадии острого экономического и производственного кризиса, находясь в состоянии банкротства. Успешный вывод этих предприятий на устойчивые производственные и экономические показатели работы позволил руководству компании переключить усилия на решение коренных проблем их реконструкции и перспективного развития.
Всем трем комбинатам, которые в основном близки по своему состоянию, можно дать следующие обобщенные характеристики:
значительный физический износ основных фондов;
использование устаревших, энергоемких и экологически неблагоприятных технологий, к числу которых, в первую очередь, следует отнести мартеновское производство, разливку стали в изложницы, что влечет двойной передел (с использованием обжимных станов) при производстве проката с соответствующим увеличением материальных, топливно-энергетических и трудовых затрат;
специфичность сортамента и, как следствие, высокая зависимость от рыночной конъюнктуры;
сложная экологическая обстановка, обусловленная эксплуатацией устаревшего оборудования, не соответствующего современным требованиям к уровню выбросов в атмосферу.
Таким образом, «ЕвразХолдингу» достались не только признанные российские лидеры черной металлургии, но и тяжелое наследство в виде изношенных и стареющих основных фондов, требующих незамедлительного обновления.
Впервые за последние 10 лет в России в рамках «ЕвразХолдинга» разрабатывается стратегическая концепция развития трех крупных металлургических предприятий как единого комплекса. Глобальной задачей является увязка реконструкции НТМК, Запсиба, КМК не только в техническом плане, но также в плане их кооперации, согласования мощностей с целью их рационального использования, оптимизации балансов металла, финансового и материального обеспечения.
Стратегия развития каждого предприятия, его финансовая и инвестиционная политика, снабжение и сбыт увязываются в единый план всех металлургических комбинатов холдинга. Согласование инвестиционных программ в рамках единой концепции позволит уменьшить финансовые риски, обеспечить привлечение заемного капитала на выгодных условиях и повысить эффективность его использования.
Можно выделить следующие основные этапы программы развития и реконструкции комбинатов:
закрытие устаревших и нерентабельных производств, включая вывод из эксплуатации мартеновских и обжимных станов;
реконструкция сталеплавильного производства, полный перевод всех предприятий на непрерывную разливку стали, обеспечение на основе внепечного рафинирования ее высоких потребительских характеристик;
стабильное обеспечение чугуном развивающегося сталеплавильного производства за счет капитальных ремонтов или реконструкции агрегатов доменного и коксохимического производства;
существенное повышение качества металлопродукции, чтобы успешно конкурировать на всех мировых рынках черных металлов;
создание конкурентоспособного листопрокатного производства на основе использования собственной слябовой заготовки.
Перечисленные кооперационные мероприятия не могут быть осуществлены без использования принципиально нового подхода к управлению производством, тем более что комбинаты находятся на большом расстоянии от центрального офиса холдинга. Поэтому осуществляется переход на современные информационные технологии, позволяющие управлять предприятиями в режиме реального времени (on-line) как из Москвы, так и из Нижнего Тагила или Новокузнецка. В качестве базы взят опыт НТМК, признанного лидера отрасли в разработке и использовании информационных технологий, который располагает крупнейшей в России системой управления ресурсами SAP R\\3.
Хотел бы подробнее осветить отдельные ключевые этапы программы реконструкции, намеченной к осуществлению в ближайшие годы.
Прежде всего горнорудное производство.
В настоящее время используется железорудное сырье с восьми рудоуправлений и четырех горно-обогатительных комбинатов. Общее производство агломерата для доменного производства составляет 12 485 тыс. т. В период до 2007 года на ЗСМК и КМК объемы производства чугуна, стали и готового проката увеличивать не планируется, а в отдельные годы даже будет иметь место их сокращение. В связи с этим реконструктивные мероприятия в основном направлены на поддержание сложившихся объемов производства агломерата, а также на повышение качественных характеристик.
В коксохимическом и доменном производствах в этот период запланированы:
капитальные ремонты и реконструкция коксовых батарей на НТМК и Запсибе;
реконструкция трех доменных печей на НТМК и ремонт второго разряда двух печей на Запсибе, в связи с чем предусмотрена поставка на эти комбинаты чугуна в твердом виде с КМК.
Одна доменная печь КМК выводится из эксплуатации. В работе останется меньшее количество печей, но объемы выпуска чугуна сохранятся на прежнем уровне, в результате снизятся эксплуатационные затраты и расход кокса на его производство.
Наиболее заметные изменения произойдут в сталеплавильном производстве.
В 20042005 годах:
на НТМК будет введена самая крупная в России по отливаемому сечению слябовая МНЛЗ № 4 в комплексе с агрегатом «печь-ковш» и установкой обессеривания (эта установка вводится в эксплуатацию в июле с. г.). Будет проведена реконструкция двух конвертеров и МНЛЗ № 3. Снижение производства жидкой стали в период реконструкции конвертеров предусмотрено компенсировать поставкой заготовки с КМК с целью обеспечения производства дефицитных специфических видов проката на НТМК;
на КМК завершится первый этап реконструкции ЭСПЦ-2 с увеличением производства цеха до 1,2 млн т в год и существенным повышением качества выпускаемой стали. Это позволит вывести из эксплуатации устаревшие сталеплавильные мощности (ЭСПЦ-1 и мартеновский цех);
на Запсибе вводятся слябовая МНЛЗ и агрегат «печь-ковш» в ККЦ-2.
В 20062007 годах:
в ККЦ НТМК пройдет реконструкция двух оставшихся конвертеров и МНЛЗ, что позволит полностью вывести из эксплуатации мартеновский и обжимной цеха комбината. Как и в предыдущие годы, кооперация с КМК по литой заготовке позволит минимизировать снижение выпуска товарной продукции;
на КМК завершится второй этап реконструкции ЭСПЦ с доведением его мощности до 1,5 млн т в год;
в ККЦ-1 Западно-Сибирского металлургического комбината будет введен комплекс из трех сортовых МНЛЗ и агрегатов «печь-ковш». Это завершит полный перевод всех предприятий холдинга на непрерывную разливку стали.
В прокатном производстве планируется сделать следующее.
В 20042005 годах на КМК завершится реконструкция головной части рельсобалочного цеха с сооружением новой нагревательной печи с шагающими балками, а также первый этап реконструкции собственно рельсобалочного цеха. Планируется также вывести из эксплуатации обжимной цех и стан 500, а листовой стан будет обеспечиваться слябовой заготовкой с Запсиба. На Запсибе в этот период намечено осуществить реконструкцию сортопрокатных цехов, предусмотрев их перевод на прокатку непрерывно-литой заготовки. На НТМК будут завершены реконструкция колесобандажного и первый этап модернизации рельсобалочного цеха. Это позволит производить транспортный прокат, соответствующий всем требованиям российских и международных стандартов.
Хотел бы отметить, что реконструкцию рельсобалочных цехов КМК и НТМК мы рассматриваем в едином комплексе и намерены поделить рыночные ниши между ними таким образом, чтобы убрать внутрифирменную конкуренцию. В 2008 году намечено перейти ко второму этапу реконструкции рельсобалочного цеха НТМК: реализация этой программы позволит производить рельсы длиной до 50 метров для высокоскоростных железных дорог России.
В результате осуществления первоочередных мероприятий при сохранении общего объема выпуска товарной продукции предприятиями холдинга на уровне 12 млн т в год повышается качество сортового проката, рельсов, колес и бандажей; увеличивается выпуск товарных слябов, которые пользуются устойчивым спросом; снижаются эксплуатационные затраты предприятий. Реструктуризация сбыта в сторону увеличения выпуска более рентабельной продукции приведет к росту выручки от реализации на 12 %. Внедрение ресурсо- и энергосберегающих технологий на 17 % снизит затраты на 1 руб. товарной продукции. Все это к 2010 году приведет к увеличению прибыли от реализации продукции на 370 млн долл. в год. Коренное повышение технического уровня предприятий приведет к существенному улучшению не только экономической, но и экологической ситуации. В результате закрытия наиболее неблагополучных производств на треть снизятся валовые выбросы вредных веществ в Новокузнецке и на 40 % в Нижнем Тагиле.
Представляется важным отметить результат, который мы достигаем за счет координации программ реконструкции и кооперации поставок:
поставка кокса КМК на Запсиб, начиная с 2006 года, позволяет покрыть его дефицит и отсрочить завершение работ по реконструкции комплекса коксовых батарей;
чушковый чугун КМК, направляемый в Нижний Тагил в 20052006 годах (в объеме 120160 тыс. т), позволит преодолеть дефицит, обусловленный реконструкцией доменных печей. Увеличение твердой завалки чушкового чугуна позволяет увеличить производство стали или поддержать его на соответствующем уровне;
поставка слябов с Запсиба в листопрокатный цех КМК обеспечит его стабильное снабжение после закрытия обжимного стана;
наконец, поставка литой заготовки КМК на НТМК позволит сохранить объемы проката в период реконструкции конвертерного цеха и после вывода из эксплуатации мартеновского цеха.
Таким образом, реальное объединение в рамках «ЕвразХолдинга» трех комбинатов обеспечивает наиболее благоприятные условия их работы в период проведения реконструкции и тем самым позволяет осуществить крупные инвестиционные программы.
Капитальные затраты на осуществление программы мероприятий в период 20032009 годов по трем предприятиям оценивается в 840 млн долл. 2003 год уже на половине пути, и 109 млн долл. осваивается на важных и крупных объектах. Однако наибольшая нагрузка падает на следующие четыре года.
Сегодня мы взаимодействуем с крупными зарубежными партнерами и имеем кредитные соглашения по линиям Фест-Альпине, CMC Демаг, Тиссен-Крупп с банками Австрии, Германии, Бельгии, Польши, Чехии.
К сожалению, российские кредитные организации пока не могут похвастаться активным участием в реализации схем проектного кредитования. А это, в свою очередь, ставит в неравные условия российские машиностроительные предприятия. Хочу напомнить, что это происходит на фоне возрастающей потребности металлургического комплекса в модернизации и при огромном потенциале российских производителей.
В такой ситуации отечественным кредитным организациям следовало бы обратить особое внимание на устойчиво работающие, платежеспособные предприятия, выпускающие высоколиквидную продукцию, имеющие высокую репутацию и стабильные рынки сбыта. Особую роль должны сыграть целенаправленные усилия органов государственной власти, согласованные с финансово-кредитными учреждениями.
Мы считаем это началом новой кредитной истории в российской металлургии и убеждены, что в лице «ЕвразХолдинга» и российские, и зарубежные инвесторы найдут достойного партнера, четко выполняющего свои обязательства.
И еще несколько слов по тем выступлениям, которые прозвучали.
Мне представляется наиболее серьезным вопрос о сырье для металлургических предприятий. Не секрет, что ресурсы магнетитовых месторождений, на которых мы сегодня работаем, давно определены и известны. От геологов революционных открытий в этой области ожидать не следует. Так что отечественную металлургию ожидают серьезные проблемы. Все наши предприятия находятся не на побережье морей, а в центре страны, куда в необходимом количестве импортную руду не привезешь. Мы обречены работать на российском железорудном сырье. А перспектива у нас или бурые железняки, или титаномагнетиты. По-моему, не стоит уходить сегодня от этой проблемы, которая наиболее остро встанет пусть не через 10, так через 20 лет.
В отличие от железорудного сырья, проблемы металлолома еще более острые, потому что это проблемы ближайших лет. В свое время Советский Союз, производя 150 млн т стали, практически всю ее осаждал в стране. Экспорт был в пределах стран СЭВ, более того, мы больше металла импортировали, чем вывозили. Вовсю работало металлоемкое машиностроение. В течение последних 10 лет машиностроение практически мертво. И производство стали со 150 млн т упало до 70 млн т, из них половина вывозится. Вывозится и тот металлоломом (будет 35 млн т по году), который мог бы стать ресурсом для металлургических заводов завтра. Мы катастрофически теряем металлофонд. В такой ситуации пусть это кому-то не нравится, но здесь высказываю личное мнение нужны протекционистские меры.
И еще несколько слов о кооперации в отрасли. Магнитогорск вводит мощности по цинковому листу, следом фактически идет Череповец. У Новолипецкого комбината есть, как мне известно, программа по строительству линии жести. Да, это более глубокая переработка продукции. Но ведь после колоссальных инвестиций наступит жесточайшая конкуренция между предприятиями. Насколько эффективными тогда будут эти вложения, как они смогут окупиться, насколько это целесообразно для металлургии в целом это большой вопрос.
|
|
|
|
|
текущий номер

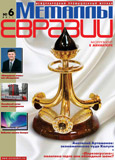
предыдущий номер

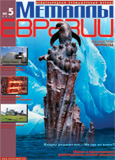
|
|