|
|
Журнал |
|
Архив |
|
Подписка |
|
Реклама |
|
САММИТ |
|
Книжная полка |
|
Контакты |
|
В начало |
|
|
|
| |
|
|
 |
№4' 2003 |
версия для печати
|
РЕЦИКЛИНГ АЛЮМИНИЯ СЕГОДНЯ И ЗАВТРА |
|
Михаил Локшин
Технический директор компании АЛЮСИЛ, кандидат технических наук
Геннадий Макаров
Профессор, доктор технических наук
началу нового века объем годового потребления алюминия и его сплавов в мире приблизился к 30 млн т/год, заняв второе место после стали (примерно 800 млн т) и значительно обогнав такие металлы, как медь (12 млн т), магний (400 тыс. т) и титан (60 тыс. т). Динамичный рост использования алюминия объясняется не только замечательным сочетанием его потребительских свойств, но и возможностью рециклинга, то есть утилизации и повторного применения в различных хозяйственных сферах. Производство первичного алюминия, как известно, требует высоких энергетических затрат до 60 МДж/кг. Однако нерастворимость оксида алюминия в расплаве позволяет проводить многократные переплавы «первородного» металла без ощутимой потери физико-механических свойств и, что самое главное, с низкими затратами энергии менее 3 МДж/кг. При этом существенно снижается негативное воздействие на окружающую среду и сохраняются невозобновляемые природные ресурсы.
В настоящее время рециклинг алюминия является одной из наиболее эффективных и динамично растущих подотраслей цветной металлургии (табл. 1). Например, за последние 10 лет доля вторичного металла на внутреннем рынке США достигла 32 %, в то время как сократилось производство первичного из-за роста цен на энергию, возросших затрат на экологию и оплату труда. Аналогичная тенденция наблюдается и в Германии. Что касается России, то затянувшийся кризис экономики существенно ухудшил ситуацию в переработке и использовании алюминия к 2000 году общее его потребление сократилось примерно в 3 раза, а производство вторичного снизилось на 24 %. При этом резко возросли поставки на внешний рынок (рис. 1).
Основное производство вторичного алюминия до последнего времени размещалось в развитых странах, где использование этого металла и, следовательно, образование амортизационного лома заметно превышает средний мировой уровень. Кроме того, здесь сосредоточена автомобильная промышленность до 80 % сырья, используемого в производстве вторичного алюминия, поступает из этой отрасли и ею же потребляется большая часть вторичных сплавов. Сегодня около 63 % алюминия, приходящегося на один автомобиль в США, рециклированный металл. В последние годы здесь расходовалось в среднем 112 кг алюминия на один автомобиль (на 42 % больше, чем в 1991 г), а общее использование этого металла в этой отрасли достигло 1,9 млн т. По оценкам фирмы Alcan, к 2010 году американский автомобиль будет содержать около 156 кг алюминия.
В Западной Европе, где использование алюминия в автомобилестроении пока отстает от США, в последние годы приходилось в среднем 75 кг алюминия на каждую машину, причем более 80 % получены из вторичного сырья. Ожидается, что к 2015 году европейский автомобиль будет содержать в среднем 200 кг деталей из алюминиевых сплавов (рис. 2).
Российское автомобилестроение от мирового уровня отстало примерно на 20 лет. При выпуске почти миллиона машин в год на каждую в среднем расходуется 44 кг алюминиевых сплавов.
В западных странах расширенное применение алюминиевых сплавов в конструкциях автомобилей стимулируют, в первую очередь, законодательные ограничения выбросов двуокиси углерода в выхлопных газах, заставляющие уделять большое внимание снижению расхода горючего и связанному с этим уменьшению массы транспортного средства. По данным IAI, каждый килограмм алюминия в автомобиле заменяет 1,78 кг стали и при пробеге в 200 тыс. км сокращает в среднем выброс двуокиси углерода на 21,5 кг. Этому же способствует острая конкуренция в мировом автомобилестроении с его избытком мощностей и постоянным стремлением к повышению технических характеристик, уровня безопасности, комфорта и пр.
Если 20 25 лет тому назад главным образом использовались алюминиевые литейные сплавы в виде отливок для деталей моторной группы и дисков колес, то в последнее время заметно возросло применение деформируемых сплавов в виде листов, труб и профилей: сначала для деталей трансмиссии и элементов отделки, а в последнее время для производства кузова. Это существенно осложнило процесс рециклирования алюминия из автомобильного лома. Дело в том, что литейные и деформируемые сплавы различны по химическому составу и, по сути, принадлежат к различным системам легирования. В алюминиевых литейных сплавах высокое (более 5 %) содержание кремния, а в отдельных еще и повышенный состав меди или магния и цинка. Деформируемые сплавы, как правило, отличаются пониженным (от сотых долей до 1 %) содержанием кремния, низким железа, а также умеренным (0,5 2 %) содержанием меди, никеля, марганца, магния. Эти сплавы, в отличие от литейных, должны обладать способностью к деформированию при обработке давлением, что ставит требования к их составу, структуре и, соответственно, к технологии производства на качественно иной уровень. Поэтому для получения из такого автомобильного лома (смесь литейных и деформируемых сплавов) вторичного металла с качеством на уровне первичного требуются дополнительные усилия.
Развитию процессов рециклирования на Западе способствует целенаправленная политика защиты окружающей среды. Уже к 2015 году в странах ЕС должна быть достигнута степень переработки отслуживших машин в 95 % с возвратом в производство 85 % металла. Для этого автомобилестроители должны принять меры, исключающие применение свинца, ртути, кадмия, шестивалентного хрома, а также взять на себя расходы по утилизации машин.
Использование в шихтовых материалах скрапа, более дешевого по сравнению с первичным алюминием (табл. 2), позволяет существенно снизить себестоимость изделий из сплавов и повысить конкурентоспособность продукции. До недавнего времени алюминиевый скрап (преимущественно амортизационный лом) использовался главным образом в производстве вторичных сплавов для изготовления отливок. Анализ показывает, что в мировой индустрии только 25 % лома составляют вторичные литейные сплавы, а 75 % деформируемые и первичные литейные. Однако в производство первичных сплавов вернулось только 15 % скрапа, а 85 % использовалось для выпуска вторичных. Вместе с тем ограничена доля отливок в структуре потребления алюминия. В США она составляет примерно 23 %, в Германии 24 %, что во многом определяется самой этой структурой. Так, доля отливок в общем количестве алюминия, используемого в автомобилях, достигает 80 % (в перспективе может снизиться до 60 %), в бытовой технике и других машиностроительных изделиях 30 %, в строительных конструкциях не превышает 3 5 %.
Увеличение доли деформируемых сплавов во вторичном алюминии привело к изысканию таких способов обработки скрапа, которые позволили бы сделать его пригодным в производстве сплавов в виде слябов для прокатки или слитков для прессования с качеством, не уступающим первичному алюминию. Это потребовало, с одной стороны, организации специальных систем сбора такого скрапа, установления прочных долговременных связей производителей сплавов, потребителей слитков (прокатные и прессовые заводы), сборщиков лома в рамках партнерских соглашений о вторичной переработке алюминия в замкнутом цикле и, с другой, создания высокоэффективных технологий и оборудования для подготовки скрапа, его плавления, обработки расплава и литья. В их числе:
лазерная сортировка скрапа, позволяющая эффективно разделять из фрагментированного в шредере автомобильного лома литейные и деформируемые сплавы. Создание таких установок начато в США;
обжиг скрапа с покрытиями, например баночного лома, окрашенных профилей и т.п.;
рафинирование алюминиевого расплава от растворенных металлов путем отделения при кристаллизации дендритов a-фазы от маточного раствора и производство на их основе сплавов для изготовления автомобильных деталей с применением деформации, что позволяет использовать смешанный алюминиевый автомобильный лом. Исследования в этом направлении ведутся в Японии;
плавление скрапа потоком расплавленного металла;
применение многокамерных плавильных печей;
бессолевая плавка низкосортных отходов в роторных печах;
применение устройств, экономящих не менее 50 % расходуемого топлива;
использование высокоэффективных неформованных монолитных огнеупоров;
внепечная обработка расплава, включающая при необходимости его модифицирование, непрерывную дегазацию и фильтрование с применением пенокерамических фильтров;
улавливание вредных выбросов при плавлении и обработке расплава;
автоматизированная разливка чушек или слитков с применением высокопроизводительного оборудования;
горячая обработка шлака;
поставка жидкого сплава заказчику, что находит все более широкое распространение на заводах США и Японии.
Американский опыт свидетельствует, что подобные технологии могут использовать только крупные компании, имеющие достаточный капитал для высокоэффективного ведения производства, выполнения строгих экологических требований, закупки современного оборудования, проведения маркетинговых кампаний и предоставления более качественных услуг потребителю. В США 60 % заводов вторичного алюминия имеют мощность более 50 тыс. т/год, из них третья часть более 100 тыс. т/год. Около 30 американских заводов производят 1,4 млн т/год вторичного алюминия, тогда как 210 заводов в Западной Европе 2 млн т/год. Но здесь тоже начался процесс укрупнения.
Что касается России, то прошедшее десятилетие характеризовалось нарастающим нерациональным использованием вторичного алюминиевого сырья. Некогда мощная подотрасль, включавшая более десятка металлургических заводов мощностью от 5 до 220 тыс. т/год, обеспечивала в 1990 году сбор 980 тыс. т скрапа и выпуск 778 тыс. т вторичных алюминиевых сплавов для внутреннего потребления, 92 тыс. т на экспорт и 100 тыс. т лома металлургическим заводам, производящим деформируемые сплавы. При многократном снижении отечественным машиностроением объемов производства и соответствующем уменьшении потребления алюминия количество заготавливаемого сырья за 10 лет сократилось всего на 8 10 %. Но зато существенно изменился его структурный состав: если в 1990 году доля отходов производства составляла 70 %, а амортизационного лома 30 %, то в 2000 году доля последнего возросла до 85 % при соответствующем уменьшении доли отходов. В то же время более 50 % собранного сырья ежегодно стало уходить за границу. Привлекательность этой деятельности способствовала ее криминализации. И только введение 30 %-ной таможенной экспортной пошлины в октябре 1999 года и 50 %-ной пошлины в сентябре 2000 года позволило несколько затормозить утечку: экспорт лома и отходов уменьшился с 408 тыс. т в 1999 году до 107 тыс. т в 2000 году. Экспорт вторичных алюминиевых сплавов за это же время увеличился с 436 тыс. т до 535 тыс. т.
Наряду с традиционными изготовителями вторичных сплавов, мощности которых загружены на 30 50 %, возникло множество мелких металлургических предприятий и участков с выпуском от 200 т/мес. В 2000 году более чем 135 производителей изготовили 660 тыс. т вторичных сплавов. Большинство этих заводов, используя примитивные технологии и оборудование, выпускают сплавы типа АК5М2 и АВ87 невысоких кондиций. На мировом рынке они проигрывают в цене 100 долл./т и более сплавам DIN 226 и рассматриваются в основном как дешевое сырье для производства качественной вторичной продукции. По оценкам зарубежных экспертов, лишь 30 % российских вторичных сплавов в 2000 году соответствовали мировому уровню. В числе производителей такой продукции следует назвать Подольский завод цветных металлов, выпустивший в 2001 году 51,7 тыс. т вторичных сплавов, 60 % из которых DIN 226 и только 0,6 % сплав АВ87, а также завод ВМС, увеличивший за последние три года свои мощности до 30 тыс. т, и Пермьцветмет, расширивший в 2001 году мощности до 40 тыс. т. Отличительной особенностью этих предприятий является модернизация оборудования и применение новых технологий, что позволило сертифицировать производство по ISO 9002. Все названные заводы основную массу выпускаемой продукции (75 85 %) отгружают на экспорт.
Недостаточная активность перерабатывающих алюминий предприятий в России и низкий душевой уровень потребления этого металла привели к тому, что замедлился процесс формирования ресурсов «нового» скрапа, и во вторичные сплавы превращается главным образом «старый». Преобладание же экспортной составляющей в работе заводов вторичного алюминия неизбежно будет способствовать постепенному исчерпанию сырьевых запасов. В перспективе следует ожидать все меньшего предложения этого скрапа на российском рынке и повышения цен на него, что существенно осложнит деятельность предприятий, занятых рециклированием алюминия.
А ведь рециклированный алюминий становится весьма значимым материалом. Постепенно стираются различия между первичным и вторичным металлом, и все меньшее значение имеет происхождение сырья для производства сплавов электролизный алюминий или же вторичный. К 2030 году, по оценкам специалистов, потребление алюминия в мире может достичь 50 млн т, из которых не менее 22 24 млн т составит рециклированный металл, что позволит уменьшить среднее потребление энергии на 1 кг алюминия с 13 до 8 кВт . ч.
Все это обусловливает вывод: назрела необходимость проводить целенаправленную государственную политику стимулирования роста внутреннего потребления алюминия и производства его вторичных сплавов. Российским предприятиям, помимо существенного улучшения качества и технического уровня производства, необходима системная работа по развитию рынка вторичных алюминиевых сплавов. Особенность тут в том, что в России требуется инвестировать средства не только в переработку скрапа, но и в отрасли, потребляющие вторичный алюминий, а также в маркетинг и подготовку кадров. Для решения таких задач необходимы консолидированные усилия различных предприятий, изыскание новых композиций сплавов и новых областей эффективного применения вторичного алюминия. Требуется содержательный информационный обмен, в том числе с ведущими зарубежными фирмами.
|
|
|
|
текущий номер

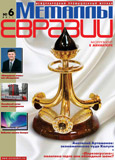
предыдущий номер

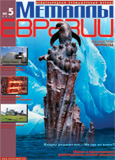
|
|