|
|
Журнал |
|
Архив |
|
Подписка |
|
Реклама |
|
САММИТ |
|
Книжная полка |
|
Контакты |
|
В начало |
|
|
|
| |
|
|
 |
№4' 2003 |
версия для печати
|
НАЙДЕТСЯ МЕСТО И МАРТЕНАМ |
КОМПЛЕКСНАЯ МОДЕРНИЗАЦИЯ СТАЛЕПЛАВИЛЬНОГО ПЕРЕДЕЛА |
Петр Югов
ФГУП ГНЦ РФ "ЦНИИчермет им. И.П. Бардина"
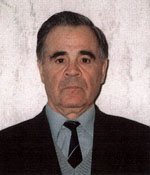 Петр Югов |
|
последнее десятилетие структура отечественного сталеплавильного производства значительно изменилась: доля стали, выплавляемой конвертерным и электросталеплавильным способами, возросла с 46,6 % в 1990 году до 73,7 % в 2001 году (см. таблицу). Доля непрерывно разлитой стали увеличилась за это же время с 23,1 % до 50,9 %. Кислородно-конвертерный процесс по-прежнему занимает ведущее место в мировом производстве: в 2001 году этим способом выплавлено 508,8 млн т стали, что составило 60 % общего объема.
Основным направлением дальнейшего развития конвертерного производства признано создание высокоэкономичных технологий выплавки качественных чистых сталей любой сложности. Подобные технологии носят комплексный характер и включают подготовку чугуна, конвертерное обезуглероживание, внепечную обработку стали и ее непрерывную разливку. Каждая из них обеспечивает высокую эффективность рафинирования металла. На этой концепции базируется разрабатываемый в России модульный принцип создания сквозного металлургического комплекса со всеми последовательными операциями от подготовки исходной шихты до получения готовой продукции.
Отечественное конвертерное производство состоит из 8 кислородно-конвертерных цехов с 23 конвертерами емкостью от 160 до 400 т. В этом переделе отчетливо наметилась тенденция к расширению сортамента высококачественных сталей ответственного назначения, особенно листовой (стали IF), что обусловило повышение требований по чистоте выплавляемого металла.
Одним из важнейших достижений последнего десятилетия является предложенная ЦНИИчерметом по результатам термодинамического и технико-экономического анализа сквозная комплексная энерго- и ресурсосберегающая технология аглодоменно-конвертерного производства высококачественных чистых сталей. Эта технология дает возможность:
перерабатывать бедные руды без применения марганцовистого сырья, расширить гамму коксующихся углей за счет вовлечения менее дорогих сернистых;
снизить расход кокса на 1 3 % и повысить производительность доменной печи на 3 5 %;
снизить расход извести в конвертерной плавке на 20 30 кг/т, уменьшить количество шлака на 25 30 % и потери железа с ним, повысить выход годного на 1 1,5 % и производительность конвертеров при высоком и стабильном качестве выплавляемого металла.
В настоящее время совместно с фирмой Voest Alpine институтом проводятся поисковые исследования по разработке технологических и конструктивных основ создания сталеплавильного комплекса с ориентацией на сочетание конвертерного процесса с технологией выплавки в электропечах.
Исключительно актуальным является применение в качестве чистой первородной шихты железоуглеродистого сплава синтикома, обеспечивающего также ряд технологических преимуществ в конвертерной плавке. Создание этого материала является серьезным научным прорывом фирмы «Интермет-Сервис и Ко». Этой компанией совместно с ЦНИИчерметом разработана комплексная технология конвертерного производства высококачественных суперчистых сталей на основе этой шихты, представляющей собой синтетический композиционный материал, состоящий из сплава и оксидов железа в виде окисленных окатышей агломерата, кусковой руды, окалины, шлакообразующих реагентов и восстановителя. В зависимости от состава металлургические свойства синтикома могут варьироваться в широких пределах, что позволяет уже на стадии изготовления программировать его использование в разных условиях производства.
В акционерных обществах «Северсталь» и «НЛМК» применение синтикома при выплавке особо чистых сталей позволило полностью заменить металлолом в конвертерной шихте и выпускать металл с предельно низким содержанием цветных примесей меди, никеля, хрома и др. Благодаря более низкой по сравнению с ломом температуре плавления синтикома (1200 1250 оС), процесс обезуглероживания ванны начинается раньше и обеспечивает спокойный ход реакции. При этом устраняются пиковые газовыделения, снижаются тепловые нагрузки на оборудование котла-охладителя. Наличие в шихтовой заготовке оксидов железа, калия, натрия и магния способствует ускоренному растворению извести и раннему формированию высокоосновного активного шлака.
Технико-экономическая эффективность использования синтикома в конвертерном производстве достигается увеличением выхода годного, улучшением стойкости футеровки, повышением производительности конвертеров, выплавкой высококачественных чистых сталей. Так, на Новолипецком металлургическом комбинате при производстве изотропной электротехнической стали снижается содержание хрома с 0,037 до 0,022 %, никеля с 0,046 до 0,027 %, меди с 0,064 до 0,026 %. Одновременно с этим отмечено увеличение выхода высших марок динамной стали по всем группам легирования соответственно на 24,4, 19,1 и 30 %.
Значительными представляются новые исследования эффективности конвертерной плавки. Так, Уральским институтом металлов совместно с акционерными обществами «ММК», «Северсталь», «НТМК» и «Комбинат «Магнезит» изучено влияние шлакового расплава с различным содержанием оксидов железа на условия службы огнеупоров. Выявлено, что повышенное содержание в них оксидов магния, а также присадка в шлак магнезиальных материалов позволяет снизить разрушаемость периклазоуглеродистых огнеупоров.
В настоящее время содержание оксидов магния в конечных шлаках достигает 10 12 %. Но при выплавке, например, низкоуглеродистых марок сталей, такого их количества может быть недостаточно для защиты футеровки. Положительного результата можно достичь присадкой материалов с высоким содержанием оксидов магния и с быстрым их растворением. Подобные материалы необходимы и для использования их в шлаковом расплаве, применяемом в виде гарнисажа, наносимого на футеровку азотом высокого давления.
Основными направлениями дальнейшего повышения эффективности электросталеплавильного производства являются совершенствование технологии плавки и модернизация конструкций печей, дальнейшее повышение качества металла, использование новых огнеупорных материалов. Выделим следующие основные тенденции технического прогресса в таком способе производства:
расширенное применение стеновых газо-кислородных фурм-горелок, обеспечивающих возможность ввода кислорода в шлак и металл удлиненной до 1,5 м жесткой струей;
предварительный нагрев металлолома не только в шахтных дуговых печах, но и в загрузочных бадьях (в том числе устанавливаемых в шахте), а также на конвейере;
совершенствование методов раскисления металла с целью минимизации конечного содержания неметаллических включений в стали;
дальнейшее совершенствование электрооборудования и методов управления электрическим режимом;
разработка новых малоинерционных методов непрерывного контроля состава отходящих газов;
освоение новых огнеупорных материалов и конструкций водоохлаждаемых элементов стен и сводов печей.
На Кузнецком металлургическом комбинате разработана технология выплавки высококачественной электростали для железнодорожных рельсов, предусматривающая использование в шихте повышенного количества жидкого чугуна (35 %), работу с «жидким стартом», т.е. с оставлением в печи после выпуска шлака 10 % металла, а также специальный режим конечного раскисления и непрерывную разливку. Качество рельсов из электростали КМК получило высокую оценку при испытаниях на экспериментальном железнодорожном кольце и при использовании на Восточно-Сибирской магистрали.
В ОАО «Мечел» проведена реконструкция электропечи 50-х годов (ДСП-80А) в современную 100-тонную дуговую печь. На ней достигнуты весьма высокие показатели, близкие к лучшим зарубежным: длительность плавки от выпуска до выпуска 77 мин. (под током 45 49 мин.), расход электроэнергии 330 кВт . ч/т (при мощности трансформатора 60 МВА), использование жидкого чугуна 250 кг/т. В ходе дальнейшей работы специалисты предполагают достичь на этой печи лучших в мире показателей плавки.
Ежегодно в мире значительно растет металлофонд. Это обусловливает чрезвычайную актуальность проблемы переработки накопленного лома. Поэтому большое практическое значение имеет использование энергетических преимуществ процессов разрядов плазменного, а также дугового постоянного тока. Исследования показали, что одним из наиболее рациональных направлений является создание технологических комплексов, сочетающих преимущества конвертерного и электросталеплавильного способов на постоянном токе. В результате появились как новые сталеплавильные технологии, например электроплавки с 50 % чугуна и конвертерные с 50 % лома, так и новые комбинированные агрегаты.
В концепцию комбинированной технологии вписываются и мартены. Эти печи способны перерабатывать низкосортную шихту на дешевом газовом топливе, поэтому могут быть эффективны в комплексе с конвертерами и электропечами, поставляя для них готовый плавленый полупродукт с определенными составом и температурой. Так, можно значительно упростить процесс выплавки стали, увеличив производительность конвертеров и электропечей за счет сокращения расхода жидкого чугуна и кислорода, увеличения общего выхода годного при улучшении качества металла и снижении общего количества вредных выбросов, т.е., в конечном итоге, при уменьшении расхода коксующихся углей на единицу готовой продукции и вовлечении в оборот газового и жидкого (смола, мазут) топлива.
Выплавленный в отдельном агрегате полупродукт из дешевого скрапа, шлаковых отвалов, окатышей и брикетов, а также стружки и других видов лома, затрудняющих конвертерное производство, можно доставлять в кислородно-конвертерные и электросталеплавильные цехи в утепленных ковшах-миксерах большой емкости.
Мартеновские подовые плазменные плавильные печи, имея высокие энергетические характеристики и способность легко перерабатывать трудную шихту, могут занять в производстве стали достойное место, снабжая плавленым железосодержащим полупродуктом определенного химического состава и температуры конвертеры и электропечи, как это показано на опытных плавках в ОАО «Северсталь».
Все более эффективным и важным технологическим элементом комплексного производства стали для любого сталеплавильного агрегата становится внепечная обработка. В ОАО "ММК" отрабатывалась технология циркуляционного вакуумирования особо низкоуглеродистой стали, идущей на изготовление оцинкованного автомобильного листа, с вдуванием кислорода через фурму, установленную в горячем газоходе вертикально по оси вакууматора. Исследованиями установлено, что содержание углерода в металле после обработки зависит от разряжения в вакуум-камере в конце обезуглероживания. На комбинате предусмотрена реконструкция вакуумной установки. При этом намечено оснастить ее средствами контроля и регулирования технологических параметров.
В ОАО «Северсталь» освоена технология с использованием установки ковшевого вакуумирования конвертерного металла. Объем стали, обрабатываемой в разливочном ковше, составляет 300 310 т. Установка включает две вакуум-камеры, пароэжекторный насос, систему подачи легирующих материалов, устройство для измерения окисленности металла (активности кислорода) и отбора проб металла под вакуумом, водоохлаждаемую кислородную фурму, трайб-аппарат, прибор для измерения содержания водорода в металле. Установка используется для получения стали IF с ультранизким содержанием углерода (<0,003 %), глубокой десульфурации при производстве трубных и судостроительных сталей, дегазации, получения металла, более чистого по неметаллическим включениям. Разработанная технология выпуска стали IF обеспечивает заданный химический состав, хорошие показатели микроструктуры и механические свойства, отвечающие требованиям потребителя.
Можно констатировать, что отечественное сталеплавильное производство остается одним из наиболее эффективных переделов черной металлургии и, несмотря на экономические трудности, динамично развивается в русле современных тенденций.
|
|
|
|
текущий номер

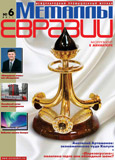
предыдущий номер

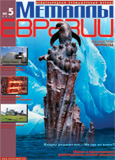
|
|