Сергей Литвин
Генеральный директор ОАО "КМК"
Вячеслав Павлов
Директор ООО "Сталь"
В 70-е годы стало очевидно, что дальнейшее развитие Кузнецкого металлургического комбината в рамках технических и проектных решений 30 - 50-х годов не имеет перспективы. К тому же резко обострились проблемы, связанные с вредным воздействием металлургического производства на состояние окружающей среды Новокузнецка.
Заменить устаревшее мартеновское производство можно было либо на конвертерное, либо на электросталеплавильное. В мировой электрометаллургии в этот период начинался бум, вызванный появлением сверхмощных дуговых печей. Развитие этогонаправления на КМК позволило бы осуществить быструю и относительно недорогую реконструкцию, коренным образом улучшить экологическую обстановку. Однако такое решение влекло за собой свертывание доменного производства, а также уход в тень молодого, набирающего силы Западно-Сибирского металлургического комбината. Это явно не подходило по причинам социального характера.
Чтобы сохранить на комбинате полный производственный цикл, нужен был кислородно-конвертерный цех. Но встраивать современную технологию в устаревшую технологическую цепочку при неопределенной ситуации с сырьевой базой и наличии двух только что построенных аналогичных цехов на Запсибе представлялось нецелесообразным.
В 1980 году на КМК был сдан в эксплуатацию не самый современный, даже по меркам того времени, электросталеплавильный цех № 2 (ЭСПЦ-2) проектной мощностью 500 тыс. т стали в год. Его пуск решал локальные задачи переработки избытка лома и сопряжения производственных мощностей. Однако ЭСПЦ-2 был не способен заменить мартеновские цехи, где выплавка стали составляла примерно 3 млн. т в год. Поэтому во второй половине 80-х годов было начато строительство комплекса кислородно-конвертерного цеха, прекращенное только в 1998 году в связи с банкротством комбината.
В 2001 году была разработана программа развития комбината на период до 2010 года и начата ее реализация. В основу положена задача адаптации КМК к требованиям рынка. Составными ее частями стали техническая, энергетическая и экологическая программы.
Техническая программа
Кузнецкий металлургический комбинат занимает устойчивые позиции по ряду видов металлопроката. В настоящее время КМК является основным поставщиком железнодорожных и трамвайных рельсов, рельсовых скреплений, выпускает крупный и мелкий сортовой прокат, большое количество фасонных профилей, горячекатаный толстолистовой прокат. Около половины продукции отгружается на экспорт. Прогнозируемые поставки проката на российский рынок составляют примерно 1 млн. 200 тыс. т год.
Интенсивное развитие технологии производства электростали привело к существенному увеличению производительности электропечей. В настоящее время модернизированная 100-тонная сверхмощная дуговая печь может выплавлять 1 млн. т стали в год. При работе двух дуговых печей организация работы в цехе усложняется. Тем не менее допустимо рассчитывать, что после его комплексной поэтапной реконструкции, при использовании 30 - 40 % жидкого чугуна и стабилизации плотности лома на уровне 0,7--0,8 т/м3 двумя дуговыми печами можно выплавлять 1 млн. 600 тыс. т стали в год.
Таким образом, весь объем проката как для поставок на российский рынок, так и для экспорта качественного металла, может быть произведен из электростали. Но с момента пуска в 1989 году машины непрерывного литья заготовка из электросталеплавильного цеха сечением 300?330 мм могла быть прокатана только в цехе сортового проката на стане 750 с годовым производством 300 тыс. т сортового и фасонного проката. Остальная непрерывнолитая заготовка отправлялась на экспорт. Поскольку ее реализация на мировом рынке убыточна, создалась нелепая ситуация: самый современный цех комбината становится обузой. И это на фоне того, что рельсы из мартеновского слитка перестали удовлетворять железнодорожников.
Первоочередной задачей становится организация технологической связи между электросталеплавильным и рельсобалочным цехами. Стандартным решением была бы установка нагревательной печи с шагающими балками в головной части рельсобалочного производства. Однако строительство печи "под ключ" требует не менее двух с половиной лет и значительных финансовых средств. Ни временем, ни деньгами комбинат в настоящий момент не располагает. Поэтому после ряда экспериментов принято другое решение. Производство на стане 500 в цехе сортового проката было существенно уменьшено, а в освободившихся нагревательных печах организован нагрев литой заготовки с последующей транспортировкой в рельсобалочный цех. Отработка этой технологии и реконструктивные мероприятия завершатся в 2002 году. В дальнейшем необходимо построить печь с шагающими балками. Это обеспечит не только качественный нагрев перед прокаткой, но и создаст технические условия для производительной и стабильной работы рельсобалочного цеха.
После организации в 2002 году производства рельсов и рельсовых скреплений из электростали металлопродукция комбината технологически распадется на два потока. Для технологической линии ЭСПЦ-2-рельсобалка основной задачей является модернизация копрового, электросталеплавильного и рельсобалочного цехов для удовлетворения современных требований к качеству продукции и эффективности производства.
В ЭСПЦ-2 целесообразно оставить в работе одну модернизированную электропечь и завершить строительство установки печь ковш. Устанавливается вакууматор. Производительность цеха увеличивается до 75 тыс. т непрерывнолитой заготовки в месяц.
Для обеспечения низкого содержания посторонних примесей в металле, повышения производительности электропечей и стабилизации снабжения металлошихтой потребуется довести долю использования чугуна в шихте до 30 - 40 %. С учетом угара металла при плавке электростали необходимо около 400 тыс. т чугуна в год. Примерно столько же составляет его товарная часть. Поэтому для обеспечения производства достаточно сохранить одну доменную печь.
При переводе предприятия на работу с одной доменной печью необходимо предварительно перевести нагревательные печи прокатных цехов с коксодоменной смеси на природный газ. Это - отдельная, трудная задача. Сейчас, в случае аварийной остановки одной из двух действующих доменных печей, большая часть тепловых агрегатов завода переводится на тихий ход (дежурное отопление) для поддержания необходимого давления в заводских сетях. При постоянной работе с одной домной (или ремонт 2-го разряда любой из них) до перевода нагревательных печей на природный газ могут возникнуть сложности. При аварийной остановке домны ее воздухонагреватели, а также все оставшиеся в работе печи прокатного производства и котлы ТЭЦ должны быть немедленно отсечены от доменного газа, согласно плану ликвидации аварии в газовом хозяйстве. Задержка может привести к образованию гремучей смеси в газопроводах и взрыву. К тому же заводские сети доменного и коксового газа эксплуатируются с 1932 года, находятся в аварийном состоянии и требуют перекладки.
Оптимальным вариантом является перевод печей прокатного производства на отопление природным газом. Оставленная в работе доменная печь должна быть по выходу газа замкнута на ТЭЦ и воздухонагреватели.
В 2004 году завершится первый этап реконструкции комбината. К этому времени будет увеличено производство литой заготовки до 900 тыс. т в год, переведено отопление печей на природный газ, осуществлен переход на работу с одной доменной печью и сформирована работающая в автономном режиме технологическая цепочка ЭСПЦ-2 - сортовые станы.
Начиная с 2004 года, для "старой" части предприятия (к ней относится производство проката из мартеновского металла) главной целью станет сохранение производства на социально приемлемый срок. В этот период необходимо решить следующие основные задачи:
прекратить всякое инвестирование в оборудование, планируемое к выводу из эксплуатации;
сосредоточить усилия коммерческих служб на увеличении объема продаж рентабельной продукции и снижении убыточной, при этом ориентироваться преимущественно на внутренних потребителей металлопродукции при сохранении определенного объема экспортных поставок;
сконцентрировать усилия работников технических и производственных служб на экономии всех видов ресурсов и сокращении затрат;
постепенно вывести из эксплуатации незагруженные мощности, обеспечив полное использование возможностей эффективно работающих производств;
оптимизировать численность работающих за счет естественного оттока персонала и реструктуризации производства.
В 2004 году станет технологически возможным вывести из эксплуатации мартеновские печи, блюминг, обслуживающие производства. Выпуск листа можно сохранить, прокатывая слябы Западно-Сибирского металлургического комбината. Другим вариантом является реконструкция в 2003 - 2004 годах одной МНЛЗ из блюмовой в блюмо-слябовую и модернизация второй электропечи. После завершения реконструкции цеха его производительность составит 1000 1200 тыс. т блюмов и 300 400 тыс. т слябов в год.
Таким образом, основной идеей реконструкции является трансформация комбината, ориентированная на выпуск качественных марок стали, прежде всего рельсовой (рис. 1, 2). Эта программа будет выполняться поэтапно, с сохранением рентабельности производства в целом. Многое зависит от состояния рынков сбыта и социальных факторов.
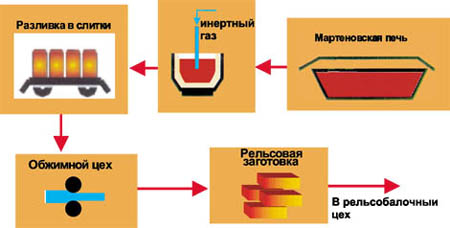
Рис.1. Существующая схема выплавки рельсовой стали на КМК
На комбинате исходили из сложившихся на мировом рынке цен на сырье и энергоресурсы. Определив рациональную структуру предприятия, весь процесс модернизации разбили на ряд отдельных проектов, которые высокоэффективны сами по себе и реализуются автономно. Первоочередной является реконструкция производства рельсов, поскольку Министерство путей сообщения является стратегическим партнером, определяющим на несколько лет вперед свою структуру заказов. Кроме того, комбинат имеет опыт поставок этой высокотехнологической продукции за рубеж в Европу, Азию, Латинскую Америку.
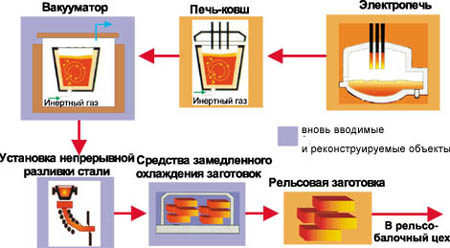
Рис.2. Сxема выплавки рельсовой стали на КМК после реконструкции
В последнее время требования к рельсам со стороны железнодорожников существенно возросли, и металлурги по ряду позиций не могут в полной мере удовлетворить потребности МПС. Исследования, обобщение опыта эксплуатации рельсов позволили сформулировать основные критерии, определяющие их надежность. Эти положения легли в основу нового государственного стандарта (ГОСТ Р-51685-2000), который вступил в действие 1 июля 2001 года. Выполнить требования ГОСТа для рельсов высшей категории "В", оставаясь в рамках действующей технологии, невозможно. Поэтому после модернизации в 2001 году освоен выпуск рельсов, промежуточных по свойствам между категориями "Т1" и "В". Налажено также массовое производство рельсов для смешанного скоростного движения (51220 т в 2001 году против 9750 т в 2000 году).
В полном объеме выполняются заказы МПС на рельсы низкотемпературной надежности (102400 т в 2001 году против 5700 т в 2000 году). Недавно начато производство рельсов из непрерывнолитой заготовки и осваивается выпуск рельсов повышенной износостойкости.
Требования к рельсам категории "В" находятся на уровне мировых стандартов. При этом дополнительно предъявляются требования к ударной вязкости, отсутствующие в большинстве зарубежных стандартов. Для освоения производства рельсов категории "В" разработана программа реконструкции рельсового производства, предусматривающая коренное изменение технологии выпуска рельсов и повышение их качества (рис. 3, 4). Необходимые мероприятия реализуются одновременно в электросталеплавильном и рельсобалочном цехах. Целями реконструкции являются:
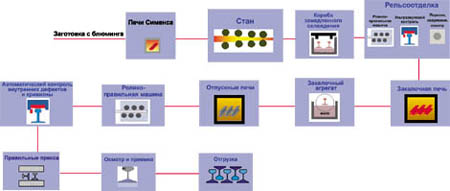
Рис. 3. Существующая схема производства рельсов в рельсосборочном цехе КМК
производство рельсов из непрерывнолитой электростали с достижением требований категории "В" по качеству поверхности, неметаллическим включениям, массовой доле кислорода, механическим свойствам;
обеспечение геометрических параметров рельсов на уровне категории "В";
увеличение объема контроля, внедрение инструментального контроля качества поверхности, внедрение средств автоматизации.
Программа реконструкции делится на два этапа. На первом этапе, заканчивающемся в 2004 году, планируется обеспечить объем производства рельсов высшей категории "В" из электростали на уровне 130 тыс. т в год при существенном повышении качества. Сумма затрат на реконструкцию составит 76 млн. долл.
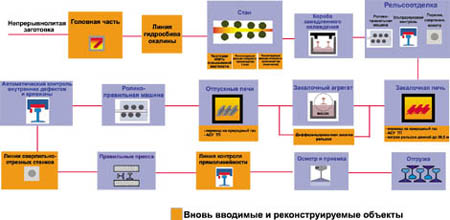
Рис. 4. Сxема производства рельсов в рельсосборочном цехе КМК после реконструкции
Энергетическая программа
Ключевой частью энергетической программы является поэтапное увеличение мощности ТЭЦ. Для заводских потребителей она является не только источником электроэнергии, горячей воды и пара, но также поставщиком химически очищенной воды. Кроме того, она снабжает теплом часть Новокузнецка. Комплекс мероприятий по техническому перевооружению ТЭЦ предусматривает обновление парка турбогенераторов станции, совершенствование систем водоснабжения и электрооборудования. В 2001 году мощность ТЭЦ была увеличена с 40 до 70 МВт. Это объясняется более низкой стоимостью собственной энергии. В дальнейшем мощность ТЭЦ будет повышена до 145 МВт.
На комбинате отсутствует собственное производство продуктов разделения воздуха (ПРВ). Начиная с 1984 года потребность потребителей комбината в ПРВ обеспечивается за счет кислородного производства ЗСМК. Для подачи кислорода и азота на КМК сооружена трасса подземных коммуникаций длиной 25 км с дюкерным переходом через р. Томь. Нормативный срок их эксплуатации истекает в 2004 году. До этого времени необходимо провести масштабные профилактические работы.
Реконструкции подвергнется система электроснабжения печей в ЭСПЦ-2. Она обусловлена необходимостью увеличения производительности печей, повышения надежности электроснабжения вновь вводимых агрегатов в ЭСПЦ-2 и улучшения качества электроэнергии. В настоящее время приобретен новый печной трансформатор мощностью 95 МВА, который будет установлен вместо трансформатора в 63 МВА. В дальнейшем планируется заменить существующие сетевые трансформаторы на оборудование металлургического исполнения и соорудить систему статической компенсации реактивной мощности.
Экологическая программа
Сокращение выбросов загрязняющих веществ в атмосферу и водоемы, выполнение экологических нормативов будет достигаться путем создания бессточной системы водоснабжения на промышленной площадке комбината, снижения объемов образования и складирования твердых отходов, их максимальной утилизации. Предусмотрено закрыть производства, например мартеновское, где нет системы газоочистки. Все вновь вводимые объекты будут оснащены современными газоочистными сооружениями. Планируется реконструировать или достроить существующие природоохранные объекты.
Намечено изменить технологию очистки коксового газа. В настоящее время аммиак выводят при помощи серной кислоты. При этом образуется сульфат аммония, который не находит сбыта. По новой технологии разложение аммиака термокаталическим способом исключает производство убыточного сульфата аммония и уменьшает выбросы в атмосферу в 2,5 раза. Ликвидируется также образование жидких отходов коксохимпроизводства, которые сегодня направляются в переполненное, не отвечающее нормам хранилище на территории шлакового отвала.
Строительство газоочистки литейных дворов и тракта шихтоподачи доменного цеха более 20 лет включалось в различные программы комбината, но до сих пор эти планы не выполнены. Близость к жилому массиву (как говорят в Новокузнецке, "домны на тротуаре"), обильное газопылевыделение при выпуске чугуна и шлака вызывают постоянное недовольство жителей города, создают комбинату постоянную головную боль во взаимоотношениях с властями и контролирующими органами.
Системы газоочистки электропечей ЭСПЦ-2, построенные в начале 80-х годов как опытные для электрометаллургической пыли, оказались неэффективными и не обеспечили необходимой степени очистки даже после их реконструкции. Электрофильтры по проекту должны допускать выброс не более 100 мг/м3, а фактически в период плавки дают значительно больше. За электропечами необходимо установить рукавные фильтры, которые обеспечивают очистку до 10 мг/м3.
Планы природоохранных мероприятий предусматривали строительство обектов по сбору и очистке промышленных, ливневых и талых вод, но из-за крайне ограниченных средств они превратились в долгострой. Окончание работ позволит прекратить сброс со сточными водами подавляющей части загрязнений.
Поскольку ниже по течению реки Томь располагаются крупные города Кемерово и Томск, проблемы ее загрязнения вредными выбросами Новокузнецка приобретают особую остроту. Выполнение водоохранных мероприятий на комбинате может и должно финансироваться из экологических фондов, которые формируются за счет платежей как КМК, так и других предприятий. Платежи комбината в экологический фонд составляют около 50 млн. руб. в год. Необходимо, чтобы затраты КМК на выполнение природоохранных мероприятий засчитывались в качестве платежей за загрязнение окружающей среды.
По предварительной оценке, в отвалах комбината находится до 20 млн. т сталеплавильных шлаков. В процессе производства стали ежегодно образуется и складируется в отвал еще около 0,5 млн. т (12 % объема выпуска стали). В этих шлаках содержится около 15 % металлического железа, до 80 % которого можно извлекать путем дробления и магнитной сепарации. Большинство металлургических комбинатов России и Украины в последние 10 лет построили такие установки с использованием зарубежного и отечественного оборудования.
В результате выполнения экологической программы не только значительно снизятся выбросы в окружающую среду, но и существенно повысится инвестиционная привлекательность КМК. В целом реконструкция Кузнецкого металлургического комбината позволит превратить его в экологически чистое и устойчиво работающее предприятие.
|