Петр Югов
ГНЦ РФ "ЦНИИчермет им. И.П. Бардина"
Высокая производительность и технологическая гибкость, конструктивная простота, низкие капитальные затраты и расходы по переделу, хорошее сочетание с доменным процессом и машинами непрерывного литья заготовок обеспечили конвертерному способу широкое распространение. Доля конвертерной стали в мировом производстве, несмотря на весьма динамичное развитие электродуговой плавки, составляет в последние годы в среднем около 70 % (рис. 1).
Современное сталеплавильное производство располагает большим арсеналом модификаций кислородно-конвертерных технологий, обеспечивающих переплавку разнообразной по составу шихты (в том числе марганцовистых, фосфористых, хромоникелевых, ванадиевых и других чугунов с добавкой лома) с использованием большого спектра режимов плавки и получением сталей широкого марочного сортамента.
Среди основных тенденций развития конвертерного процесса в первую очередь следует выделить повышение чистоты металла, т.е. снижение содержания углерода, а также таких вредных примесей, как сера и фосфор. Необходимым условием является получение заданного химического состава стали, что требует выбора жестких температурных параметров продувки с высоким уровнем перемешивания и усреднения ванны и внедрения современных средств контроля и моделей управления плавкой. Технико-экономические показатели процесса в значительной степени связаны также с расходом огнеупоров.

Хотя удельный вес конвертерного процесса в черной металлургии России (около 62 % в 2000 г.) несколько уступает среднемировому показателю, технический уровень отечественных цехов является достаточно высоким. Лучшие из них по своей оснащенности в основном соответствуют мировому уровню. Конвертерные цехи в акционерных обществах "ММК", "Северсталь", "НЛМК", "ЗСМК" являются крупными сталеплавильными комплексами, оснащенными 350 400-тонными конвертерами, машинами непрерывного литья заготовок, установками десульфурации чугуна и внепечной обработки стали, а также автоматическими системами управления технологическими процессами.
На базе новейших научных разработок в конвертерном производстве достигнуты значительные успехи: освоена технология передела чугунов различного состава (фосфористого, ванадиевого, низкомарганцовистого и др.), а также выплавки качественных сталей широкого сортамента, повышена интенсивность продувки до 4 5 м3/т; увеличена стойкость футеровки до 4000 5000 плавок; созданы новая технологическая схема плавки с вынесением подготовительных и корректировочных операций из конвертера, технологические процессы с комбинированной газо-кислородной и кислородно-топливной продувкой; широко внедряются методы внепечной обработки чугуна и стали.
Многие конвертерные цехи оснащены агрегатами комплексной обработки металла в ковше, в том числе с использованием установок циркуляционного или порционного вакуумирования с предшествующей доводкой металла, что особенно эффективно при выплавке конструкционной и инструментальной стали. Вакуумирование позволяет получать металл с содержанием кислорода менее 20 ppm, на 70 % снизить содержание водорода и значительно уменьшить загрязненность стали неметаллическими включениями. Технология конвертерной плавки на ведущих предприятиях России имеет свою специфику, связанную с составом исходной шихты, сортаментом выплавляемых сталей, техническими традициями. При этом проблема снижения содержания серы является общей для всего сталеплавильного передела.
На Магнитогорском металлургическом комбинате главная задача конвертерного производства в условиях роста его объемов определяется расширением сортамента сталей с низким содержанием серы. Источники ее попадания в конвертерную ванну чугун, лом, шлак из заливочного ковша, углеродсодержащие и шлакообразующие материалы. Доля серы, поступающей с чугуном, составляет 30 55 %, с другими материалами 45 70 %. Возможности удаления этой примеси в конвертерах ММК определяются в 30 35 %. Влияние технологических факторов выплавки на концентрацию серы в металле перед выпуском из конвертера весьма ограничены: увеличение массы шлака на 10 т ведет к снижению концентрации серы на 0,002 %, а повышение его основности на единицу на 0,001 %. Поэтому выплавка низкосернистых марок стали в конвертерном цехе ММК возможна только при использовании десульфурированного чугуна и чистого оборотного лома. Но даже при этом не всегда удается получить низкую концентрацию серы в металле перед выпуском из конвертера. Требуется проведение внепечной десульфурации.
Производственная программа конвертерного цеха ММК (8 млн. т в год) с учетом сортамента прокатных станов включает стали: для тонкого листа и белой жести (около 40 %), качественные конструкционные, легированные и низколегированные, а также для судостроения. Кроме того, освоено производство стали электротехнических марок динамной и трансформаторной.
На "Северстали" применяется специальная шихта на основе чугуна с добавками железорудных материалов. Это уменьшает цикл плавки и снижает содержание хрома, никеля и меди в готовом металле на 0,03 0,05 %, благодаря чему на 10 % повышается выход высших категорий автолистовой стали, а также компенсируется нехватка чистого металлолома. При производстве марок стали с содержанием серы не более 0,01 % желательна, а с ее примесью не более 0,005 % необходима внепечная десульфурация чугуна. В конвертерном производстве "Северстали" опробована обработка жидкого чугуна гранулированным магнием, вводимым в виде порошковой проволоки. При его расходе в 1 кг/т степень десульфурации составляет 70 %, конечное содержание серы в чугуне 0,005 0,006 %.
Основная проблема конвертерного передела Западно-Сибирского металлургического комбината связана с переработкой низкокремнистого (менее 0,4 %) чугуна с повышенным содержанием фосфора (до 0,3 %). Применяемая здесь технология позволяет при массовом производстве металла снизить расход извести, увеличить выход конвертерной стали, в процессе продувки получать шлак с заданными свойствами для выплавки стали требуемого качества.
В современном кислородно-конвертерном процессе, в принципе, можно переработать чугун любого химического состава. Однако в массовом крупнотоннажном производстве для обеспечения стабильных технико-экономических показателей важнейшим требованием является низкое содержание серы в исходном чугуне (менее 0,03 %), обусловливающее повышенное содержание кремния (0,7 0,9 %) для десульфурации. При этом для оптимизации шлакообразования (а шлак, как известно, является основным фактором всех сталеплавильных процессов) содержание марганца должно составлять не менее 0,8 1 %.
Анализ процессов десульфурации показывает, что реакция вытеснения серы энергетически гораздо легче обеспечивается в чугуне, чем в стали. Однако в процессе доменной плавки это затруднено, поскольку из-за комплекса сложных окислительно-восстановительных реакций энергетика термодинамических условий глубокой десульфурации обусловливает повышение содержания кремния и, как следствие, больший расход извести и кокса, снижение производительности. Поэтому плавка низкосернистого чугуна в домне требует тщательно отработанной сложной технологии, шихтовых материалов с минимальным содержанием серы, высокоосновных шлаковых смесей. Снижение содержания серы в чугуне при его выплавке приводит к снижению производительности печи, большему расходу кокса, росту эксплуатационных затрат.
В конвертере глубокая десульфурация металла также неэффективна, поскольку система металл-шлак не достигает равновесия. Низкий коэффициент распределения серы между шлаком и металлом затрудняет ее удаление и вызывает рост затрат.
Таким образом, как в доменной, так и в конвертерной плавке не обеспечиваются термодинамические условия для эффективной десульфурации металла. Следовательно, оба процесса с этой точки зрения технологически неэффективны, а экономически они невыгодны. Поэтому целесообразно вынести удаление серы из этих агрегатов, внедрив внепечную десульфурацию и чугуна, и стали. Это позволяет упростить и удешевить сквозную технологию аглодоменного и конвертерного производства.
В условиях острого дефицита марганцовистого сырья особое значение приобретает режим использования марганца в конвертерной плавке. Исключительно важная его роль в этом процессе, определяющая условия раннего шлакообразования и регулирования окисленности конечного металла перед выпуском, в течении долгого времени диктовала необходимость получения 0,8 1 % марганца в чугуне, а значит дополнительного введения марганцовистых материалов в доменную аглошихту, что удорожает выплавку. Однако низкое исходное содержание кремния в чугуне позволяет выплавлять низкомарганцовистый чугун и перерабатывать его в конвертере с использованием марганцевой руды в качестве раскислителя. Практика показала, что это дает возможность улучшить показатели и доменного (снизить расход кокса на 3 5 %, повысить производительность печи на 3 4 %), и конвертерного передела (уменьшить расход Mn-ферросплавов на 1 1,5 кг/т, повысить выход годного на 0,5 1 %).
Таким образом, технико-экономический и термодинамический анализ процессов рафинирования металла (десульфурация, дефосфорация, десиликонизация, режим марганца) на всех стадиях металлургического производства, включая подготовку аглошихты, выплавку чугуна, конвертерную плавку с внепечной обработкой, позволяют определить основные параметры сквозной энерго- и ресурсосберегающей технологии агло-доменно-конвертерного производства, рассматривая его как единый комплекс производства чистых сталей с супернизким содержанием вредных примесей, прежде всего серы (0,001 %).
Кстати, по мнению японских специалистов, по сравнению с классическим конвертерным процессом 50 60-х годов, в настоящее время доля собственно конвертера в распределении рафинировочных функций составляет не более 20 %, т.е. рафинирование в основном осуществляется вне агрегата.
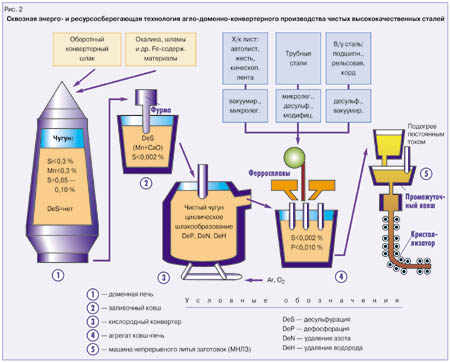
Базовыми принципами сквозной технологии, предложенной ЦНИИчерметом, являются дифференциация основных технологических и рафинировочных функций металлургического цикла и использование специализированных агрегатов для их реализации (рис. 2). Эта технология включает:
выплавку из безмарганцовистой шихты низкомарганцовистого и низкокремнистого чугуна (менее 0,3 % того и другого) с нерегламетированным содержанием серы (0,3 % и более) в доменной печи;
внедоменную десульфурацию чугуна (менее 0,005 % серы) в заливочном ковше;
высокоэффективный и экономичный конвертерный передел чистого чугуна с малошлаковой технологией и многократным использованием конечного шлака в самой конвертерной плавке, а также глубокую дефосфорацию низкокремнистого и низкомарганцовистого металла высокоосновным окисленным шлаком в конвертере и выплавку чистого стандартного металлического полупродукта;
получение методами внепечной обработки в агрегате ковш печь качественной чистой стали любого сложного состава в рациональном объеме.
Предложенная комплексная технология позволяет в агло-доменном переделе:
перерабатывать бедные руды без применения марганцовистого сырья, расширить гамму коксующихся углей за счет вовлечения более сернистых;
снизить расход кокса на 1 3 % и повысить производительность доменной печи на 3 5 %.
В конвертерном переделе эта технология дает возможность:
снизить расход извести на 20 30 кг/т, уменьшить количество шлака на 25 30 %, а также потери железа со шлаком, повысить выход годного на 1 1,5 % и производительность конвертера;
обеспечить высокое и стабильное качество выплавляемого металла.
Наиболее ответственным звеном в промышленной реализации предлагаемого технологического комплекса является внедоменная десульфурация чугуна. ЦНИИчермет с участием фирмы "Альмамет-Ремакор" разработал технологические основы процессов глубокой десульфурации чугуна и десульфурирующих реагентов. С участием Соликамского магниевого завода создано совместное специализированное предприятие по производству магниевых десульфураторов применительно к конкретным условиям металлургических предприятий России.
Конечным этапом предложенной технологии является машина непрерывного литья заготовок, в которой использован нагрев жидкого металла в промежуточном ковше разрядом постоянного тока, что повышает технологическую гибкость всей схемы и позволяет существенно улучшить качество стали.
Основным недостатком разработанного конвертерного процесса является низкая энергоемкость и, в связи с этим, ограниченные возможности переработки лома не более 25 27 % в шихте.
Постоянный рост мирового металлофонда, увеличение оборота лома делают весьма актуальной проблему переработки в сталеплавильном производстве вторичного металлического сырья. Ее решение предполагает использование энергетических преимуществ электросталеплавильных процессов плазменного и дугового разряда постоянного тока в конвертерной плавке. По мнению специалистов, одним из наиболее рациональных направлений развития сталеплавильного производства является создание технологических комплексов, сочетающих преимущества обоих процессов конвертерного и электросталеплавильного, работающего на постоянном токе.
Теоретический анализ и экспериментальные исследования показывают, что технологический сталеплавильный модуль "дуговая печь постоянного тока конвертер" при определенных условиях может быть эффективно использован как на предприятиях с полным металлургическим циклом, так и на мини-заводах без коксодоменного передела. Особым достоинством этой схемы является возможность получения качественной стали, в частности, с очень низким содержанием азота, что существенно повышает пластические и технологические свойства металла.
В настоящее время кислородный конвертер является основным сталеплавильным агрегатом практически всех крупных металлургических предприятий и, скорее всего, не утратит своего значения в обозримой перспективе. Хотя за полтора столетия своего существования этот способ претерпел огромные изменения, он и сегодня сохраняет существенные резервы технологического и конструктивного совершенствования.
|