Дмитрий Темкин Директор департамента качества, новой техники и науки
Глубокая перестройка организма предприятия, объединение или концентрация производств, создание новых технологий, освоение новых видов продукции, снижение издержек все эти направления потребовали не только интеллектуальных усилий заводской команды, научных наработок или организационных мероприятий. Прежде всего выяснилось, что для решения серьезных проблем необходимо кардинально изменить взгляд на многие привычные вещи.
Начало системному подходу к этим вопросам было положено в 1997 году, когда руководство предприятия приняло решение создавать систему качества (СК) в соответствии с требованиями международного стандарта ИСО 9002-94. Никто не представлял тогда трудностей этого дела, но главная задача была сформулирована сразу система качества нужна прежде всего самому предприятию, поэтому никаких формальных, упрощенных и прочих "прямых" путей к сертификату, только реальная и полнокровная система.
Были сформированы соответствующие структуры, в частности департамент качества, новой техники и науки (ДКТН), куда вошли служба технического контроля, технический отдел, контрольно-испытательный центр и отдел систем качества. Эта структура полностью себя оправдала, позволяя решать большинство проблем, устранять несоответствия и проводить необходимые мероприятия в производственном треугольнике "технология испытания приемка продукции".
Первый шаг был традиционным для новичков пришлось вспомнить о базовых вещах: должностных инструкциях, положении о структурном подразделении и т.п. Следующий шаг был не так очевиден, потребовал настойчивости руководства и определенной смелости. Речь идет об информации. Можно сформулировать этот подход как "политику открытых глаз". Суть в том, что для решения любой проблемы надо как минимум эту проблему видеть и оценить количественно. Задача непростая многие проблемы в скрытом виде существовали десятилетия.
У металлургов, имеющих замкнутый плавильный и прокатный технологический цикл и широкую номенклатуру продукции (а у нашего завода перечень сплавов и их контрактных модификаций достигает 100, количество типоразмеров нескольких тысяч), появляются возможности выйти из положения в случае технологических неприятностей брак можно перекатать или перетянуть на другой размер, можно подогнать марку сплава и, наконец, литейный брак можно просто "утопить", т.е. переплавить. Такой скрытый брак может составлять десятки процентов, при этом в условиях неудовлетворенного спроса заказчиков, готовых взять что угодно, несоответствие годами не будет выявлено.
В условиях ограниченного и конкретного спроса такая ситуация недопустима. Была введена сквозная партионная система, призванная обеспечить не только прослеживаемость продукции, но сбор и регистрацию технологической информации для контроля выходов годного, соблюдения технологических регламентов, влияния набора параметров на качество готовой продукции. Партионная система помогает выявлять узловые технологические проблемы, незаменима при поиске причин несоответствий. Именно она дает возможность перейти на язык цифр. Так, в течение нескольких последних лет из-за снижения качества шихтовых материалов на одном участке брак стал "большим". После введения партионной системы определили количественно, схватились за голову брак до 60 % ! Важность проблемы сразу стала ясна всем, заводские специалисты и умельцы за месяц разработали и внедрили новую технологию брак исчез.
Вообще, наличие четкой партионной системы на предприятии сразу показывает, "по зубам" проблема качества коллективу или нет. Задача эта очень трудоемкая.
Еще одна проблема характерна для металлургов-обработчиков. Весь предшествующий период основное внимание уделялось главной задаче производству проката. Вопросы величины издержек, эффективной переработки отходов оставались в стороне. Например, выход годного составляет 60 %. Оставшиеся 40 % отходы разного вида и качества. Если технология производства готовой продукции прописана достаточно подробно, то до последнего времени эти 40 % не были избалованы вниманием инженеров и экономистов. Генеральный директор сформулировал и определил эту задачу как важнейшую, в результате создана единая сквозная система учета всех материалов в технологическом цикле предприятия, разработаны и утверждены базовые нормативные документы.
При анализе сбоев в работе акцент делаем на поиск причин. Не только ради "справедливости" (хотя наказание невиновного отбивает у него всякое желание работать), но и потому, что это самый эффективный и дешевый путь устранения несоответствия. Как правило, цепочка взаимосвязанных причин включает пять-шесть звеньев и приводит либо к недостаткам документации, либо к состоянию оборудования, либо к квалификации персонала. Вещи, в общем-то, известные, но каждый руководитель сегодня обязан эту схему держать в голове.
В процессе разработки и внедрения СК мы столкнулись с общей проблемой большинства российских предприятий низкий технологический уровень некоторых процессов. Вызвано это и моральным и физическим износом оборудования, сбоями в системе ППР из-за дефицита средств и, соответственно, необходимых запчастей, снижением требований к технологической дисциплине всего не перечесть. В этом случае, считают некоторые специалисты, систему качества лучше не создавать. Начать надо с наведения элементарного порядка и улучшения технологии. Иначе документированная система качества только зафиксирует сложившийся убогий уровень.
Наше мнение оба процесса должны идти параллельно. Именно при внедрении системы качества "с открытыми глазами" становятся видимыми все проблемы и, главное, их источники. Именно поэтому одновременно с внедрением СК можно совершенствовать техпроцесс и организацию производства. Именно поэтому СК не купишь и не создашь за полгода или год.
В рамках программы технологического перевооружения за последние годы основной упор сделан на обеспечение высокого качества продукции и снижение издержек. Высокотехнологичное оборудование линия финишной обработки медных труб или современные дефектоскопы было приобретено у зарубежных фирм. Одновременно приобретали упаковочную оснастку, поскольку упаковка продукции важнейшая часть обеспечения качества.
Многие работы оказались по силам специалистам завода. В частности, создан участок вакуумной термообработки медных труб в бухтах. Очень интересная, на наш взгляд, работа выполнена по отжигу латунных труб со сверткой в бухту, в результате чего сегодня завод выпускает только цельнотянутые трубы удовлетворяя требования заказчиков, мы отказались от сварки латунных бойлерных труб.
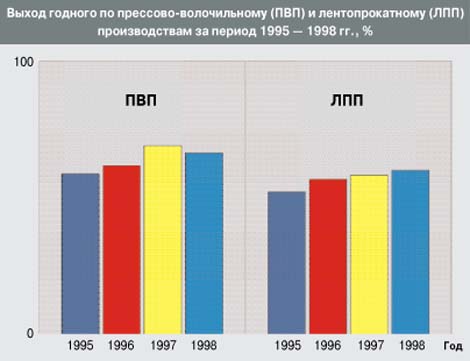 Большой комплекс работ ведется по утилизации и учету энергоресурсов.
Теснейшее взаимодействие на постоянной основе осуществляет завод с учеными московских отраслевых и учебных институтов, организациями Санкт-Петербурга, Екатеринбурга, Владимира. Направления самые разные от глубокой переработки отходов и решения экологических проблем до разработки новых сплавов. Эти контакты позволяют специалистам завода увеличить свой интеллектуальный потенциал, "чувствовать пульс" современных технологий. Этому же способствует систематическое посещение работниками предприятия металлургических выставок, где всегда участвует наш завод.
Технологическое переоснащение, происходящее на фоне концентрации и объединения производств, приносит конкретные результаты (см. рисунок), даже в условиях постоянного усложнения продукции и ужесточения требований к химическому составу. Так, создание единого лентопрокатного производства позволило на некоторых сплавах поднять выход годного на величину до 5% только за счет появления возможности доработки отходов. Кооперация в рамках единого прессово-волочильного производства дает возможность осуществлять программу капитальных ремонтов основного оборудования без серьезного ущерба производству, оптимизировать технологические схемы и загрузку оборудования, значительно снизить затраты на оснастку.
Огромная повседневная работа проводится по созданию облика современного предприятия, по повышению технологической культуры, по состоянию территории.
Все эти вопросы не случайно сведены вместе. Из решения каждой проблемы постепенно создается функционирующая система качества, которая "пропитывает" все предприятие. В рамках укрупненных подразделений и служб снимаются многие барьеры, одновременно четкое разграничение ответственности позволяет оптимально организовать работу и контролировать результаты на основе открытой и достоверной информации.
Большой объем работ предстоит провести с нормативно-технологической документацией. За последние годы сильно изменилась сырьевая база, постоянно растет доля низкокачественной засоренной шихты. Типичным стал "рваный" режим поставок сырья и загрузки производства отсюда изменение регламентов работы оборудования, особенно высокопроизводительного, рассчитанного на работу в непрерывном режиме. Отсюда и необходимость пересмотреть подходы к планированию снабжения и производственной деятельности, к работе с поставщиками. Актуальной остается недостаточное методологическое обоснование проведения маркетинговых исследований, статистической обработки результатов технологического контроля и испытаний готовой продукции. Над этими задачами сегодня работают и руководители, и сотрудники служб и производств.
Продукцию нового качества может выпускать только человек, впитавший новую идеологию и оснащенный новой технологией. То же касается всего коллектива завода. Современные технологии организации производства и управления, создание единой информационной системы, постоянное обучение кадров, совершенствование технологической и испытательной базы, освоение новых сплавов и видов продукции, ориентация на потребителя вот основные направления обеспечения качества во всех сферах жизни завода.
|