Елена Ремизова
Экономические и финансовые потрясения в различных регионах мира, начавшиеся в 1997 году и углубившиеся в 1998 году, привели к существенным изменениям на рынке черных и цветных металлов, к снижению спроса на них и сокращению производства металлопродукции.
Объем промышленного производства в России в 1998 году сократился на 5,2 % и составил 1658 млрд. руб. Предприятия металлургического комплекса произвели товарной продукции на 219,8 млрд. руб. (129,9 % к уровню 1997 года), в том числе в черной металлургии 113,3 млрд. руб. (104,1 %), в цветной металлургии 106,5 млрд. руб. (138,2 %). Рост объемов вызван в основном повышением цен, особенно начиная с августа 1998 года. При этом в цветной металлургии цены выросли в значительно большей степени.
По объему производства товарной продукции металлургический комплекс занимает четвертое место (13,9 %) в ряду ведущих отраслей экономики после топливной промышленности (18,6 %), машиностроения и металлообработки (18,1 %), электроэнергетики (16,7 %).
Загрузка имеющихся мощностей в ведущих отраслях экономики России в 1998 году оставалась на достаточно низком уровне, что видно из следующих данных (%):
Электроэнергетика
Топливная промышленность
Цветная металлургия
Черная металлургия
Химическая и нефтехимическая промышленность
Промышленность стройматериалов
Машиностроение и металлообработка
В среднем по промышленности
| 70 70 52 46 36 33 27 38
|
Металлургия находится в тесных взаимосвязях с машиностроением и другими отраслями, определяющими внутренний рынок металла. Постепенно снизилась доля отраслей, образующих инвестиционный сектор машиностроительного комплекса и являющихся наиболее металлоемкими (тяжелое, энергетическое и транспортное машиностроение, химическое, нефтяное и строительно-дорожное машиностроение, а также сельхозмашиностроение).
Сужение внутреннего рынка и невозможность сохранения ранее достигнутого уровня внешних поставок продукции машиностроения привели к значительному снижению производства в машиностроении и металлообработке и, как следствие, к сокращению потребления готового проката для этих целей. В целом внутреннее потребление стальной металлопродукции в России (прокат, трубы, метизы, изделия дальнейшего передела) сократилось за период 1991 1998 годов с 54 млн. т до 13,5 млн. т.
Деградация внутреннего рынка, постоянное снижение объемов экспорта привели к дальнейшему снижению объемов производства основных видов металлопродукции (кроме железорудного сырья) в 1998 году. Об этом свидетельствуют данные по производству, приведенные в таблице.
ЧЕРНАЯ МЕТАЛЛУРГИЯ
В 1998 году усилился спад производства готового проката и труб. В общем объеме готового проката продолжалось снижение производства листового проката: производство штрипсов составило 897,8 тыс. т, или 67,2 % от уровня 1997 г. (1337 тыс. т), холоднокатаного листа 4732,2 тыс. т, или 85,3 % (5544,5 тыс. т). Выросло производство холоднокатаного листа с защитными покрытиями 1316,3 тыс. т, или 107,4 % (1225,2 тыс. т).
Снизилось также и производство сортового проката. В 1998 году его произведено 17461,9 тыс. т, или 87,2 % (20030,5 тыс. т) к уровню производства 1997 года. Производство стальных гнутых профилей составило 308,2 тыс. т, или 96,4 % (319,7 тыс. т). На низком уровне оставалось производство проката из нержавеющих сталей всего 42,9 тыс. т, или 84,9 % (50,5 тыс. т).
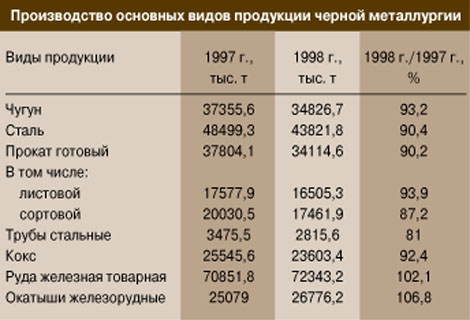 Производство готового проката в 1998 году выросло в акционерных обществах "Магнитогорский металлургический комбинат", "Западно-Сибирский металлургический комбинат", "Ревдинский металлургический завод", "Московский металлургический завод "Серп и молот". Практически на уровне 1997 года сохранилось производство готового проката в акционерных обществах "Северсталь", "Оскольский электрометаллургический комбинат", "Белорецкий металлургический комбинат". На остальных предприятиях черной металлургии наблюдалось значительное снижение производства готового проката. Основные причины кризис неплатежей, сопровождающийся отсутствием платежеспособного спроса на готовый прокат со стороны потребителей металлопродукции, дефицитом собственных оборотных средств у металлургических предприятий для приобретения сырьевых и материальных ресурсов, а также введение антидемпинговых санкций на российский прокат практически по всему мировому рынку. Тем не менее результаты работы металлургических предприятий в декабре 1998 года, в январе и феврале 1999 года дают основание предположить о некоторой стабилизации производства.
Производство жести и холоднокатаного металла с покрытиями в России находится на низком уровне по сравнению с зарубежными промышленно развитыми странами. Недопустимо мало листа с покрытиями применяется в производстве автомобилей, что является одной из причин их низкой конкурентоспособности. Металл с покрытием и белая жесть не сертифицированы. Многие виды металла с покрытием продолжают закупаться по импорту.
Перспектива развития производства качественного холоднокатаного листа с различными видами защитных покрытий открывается на Магнитогорском металлургическом комбинате в связи с успешным проведением реконструкции и установкой необходимого современного оборудования, а также на ряде других предприятий отрасли. Так, ОАО "НЛМК" имеет агрегаты покрытий (горячего цинкования и полимерных покрытий), поставленные японской фирмой "Кавасаки Стил". Созданы все условия для организации производства горячеоцинкованного автомобильного листа необходимого качества. Для этого нужно продолжить доработку сквозной технологии производства листа из стали IF, позволяющей получать высокие пластические свойства и осуществлять штамповку изделий сложной и особо сложной вытяжки. Новолипецкий комбинат также обладает самым современным оборудованием и наиболее совершенной технологией производства качественного холоднокатаного листа, а наличие в цехе холодной прокатки агрегата полимерных покрытий позволяет использовать его и для производства электрооцинкованного листа.
Акционерное общество "Северсталь", имеющее два агрегата защитных покрытий, способно произвести большое количество листа с защитными покрытиями различного вида, в том числе автомобильного листа. Отсутствие платежеспособного спроса сдерживает процесс освоения их производства. Согласованная программа работ с АО "АвтоВАЗ" должна способствовать ускорению решения этой проблемы, в том числе по производству листа с защитными покрытиями для бензобаков и выхлопных систем автомобиля (бескарбюраторных).
Лысьвенский металлургический завод также обладает широкими технологическими возможностями для производства листа с различными видами покрытий. Реализован проект по реконструкции одного из агрегатов электрооцинкования для организации производства освинцованной стали для бензобаков. Реконструкция другого агрегата позволяет производить электрооцинкованный лист шириной до 1200 мм для изготовления деталей кузовов современных автомобилей. В настоящее время с фирмой "Коккериль" (Бельгия) заключен контракт на дальнейшую реконструкцию этого агрегата под производство электрооцинкованного листа шириной до 1600 мм.
Ряд ведущих предприятий метизной промышленности расширяет свои потенциальные возможности для производства конкурентоспособной на мировом рынке металлопродукции. Белорецкий металлургический комбинат предусматривает строительство современного электросталеплавильного комплекса взамен морально и физически устаревшего мартеновского цеха. Орловский сталепрокатный завод совместно с Белорусским металлургическим заводом создали Межгосударственную финансово-промышленную группу (МФПГ "Межгосметиз"), которая консолидировала технические возможности этих двух предприятий в производстве высококачественного металлокорда. Магнитогорский калибровочный завод осуществляет реконструкцию кузнечно-прессового цеха с целью освоения производства железнодорожного крепежа современных модификаций.
В 1998 году произошло достаточно ощутимое снижение (на 19,4 %) производства стальных труб. Это обусловлено рядом причин. Основная из них заключается в отсутствии платежеспособного спроса на трубы различного сортамента на внутреннем рынке. Проблемы топливно-энергетического комплекса, связанные с падением мировых цен на нефть и, соответственно, снижением ее добычи, осложнили ситуацию. Нефтяные компании свернули свои инвестиционные программы, что привело к потере устойчивой базы постоянных потребителей трубной продукции, негативно отразилось на ее сбыте. Сокращение объема инвестиций в развитие трубной промышленности составило 12 % при уменьшении ВВП на 5 %.
Следствием августовского кризиса стал резко возросший объем экспорта металла. Это привело к дефициту металла для внутреннего рынка, в том числе для изготовления труб (трубной заготовки, штрипсов). Эта ситуация также отрицательно повлияла на объемы их производства.
На работу предприятий черной металлургии, в частности трубных заводов, большое влияние оказывает РАО "Газпром", занимая лидирующее положение в потреблении труб. Значительный объем поставок для РАО "Газпром" осуществляется по взаимозачетным схемам. Например, постоянная задолженность Украины за поставки природного газа компенсируется большим объемом поставок труб Харцызского трубного завода. Применение взаимозачетных схем внутри России также не стимулирует развитие производства.
Важным моментом для российских трубных заводов является то, что они в настоящее время не могут производить весь сортамент труб, который требуют потребители. Так, производство труб диаметром 1420 мм с трехслойным покрытием в основном сконцентрировано в Украине на Харцызском трубном заводе при том, что качество этих труб не всегда удовлетворяет требованиям потребителей.
Из российских трубных заводов трубы диаметром 1420 мм для строительства и ремонта магистральных трубопроводов может изготавливать только ОАО "Волжский трубный завод". Поскольку ВТЗ производит только спиральношовные трубы с дополнительным поперечным швом, имеющие пока ограниченный круг потребителей, то требуются кардинальные меры по повышению их качественных характеристик, особенно в части повышения коррозионной стойкости. В настоящее время на ВТЗ началась подготовка участка по изоляции труб. Себестоимость производства труб на ВТЗ значительно ниже, чем на других предприятиях отрасли, и это позволит заводу в ближайшее время значительно повысить конкурентоспособность своих труб на внутреннем рынке и выйти на внешний рынок.
Для выполнения крупного заказа Каспийского трубопроводного консорциума на ОАО "ВТЗ" фирмой "Бредеро Прайс" будут поставлены оборудование и технология для производства труб с трехслойным полиэтиленовым покрытием, освоение которых будет способствовать развитию отечественного производства труб различного сортамента, отвечающих современным требованиям российских и зарубежных потребителей, и позволит реально решить задачу импортозамещения.
В этом направлении актуальна задача и по производству бесшовных труб для нефтедобычи. По своим производственным возможностям российские трубные заводы в состоянии обеспечить всю потребность отечественных потребителей. Нарезные трубы в обычном исполнении могут быть изготовлены в акционерных обществах "Северский трубный завод", "Таганрогский металлургический завод", "Синарский трубный завод", "Первоуральский Новотрубный завод", "Волжский трубный завод", "Челябинский трубопрокатный завод" в необходимом количестве. Однако и здесь имеются "узкие места". Это нарезные трубы в хладостойком и антикоррозионном исполнении, с высокогерметичными резьбами, с высокопрочными замковыми соединениями для добычи нефти и газа и использования в средах с содержанием сероводорода до 26 %. Такие трубы в России не производятся.
Снижение производства готовой металлопродукции привело к соответствующему уменьшению выплавки чугуна и стали, производства ферросплавов, огнеупорных изделий, кокса. Но при этом возросло производство железорудного сырья: товарной железной руды и железорудных окатышей. Эта ситуация требует особого рассмотрения, так как происходит неуправляемый процесс проедания производственного аппарата черной металлургии, особенно ее ресурсной составляющей.
В течение 1990 1997 годов в России не вводились новые мощности по добыче железной руды. Наоборот, из эксплуатации за этот период выбыло более 15 % мощностей по добыче руды. Эта негативная тенденция усиливается: неуправляемая структурная трансформация металлургического производства привела к относительному росту спроса на железную руду. К тому же происходит увеличение экспорта ресурсов. Доля экспорта руды увеличилась с 10 % до 18 %, лома с 3 % до 30 %. Значительные объемы руды были затрачены на компенсацию потерь от снижения заготовки лома и сокращения ввоза руды из Казахстана и Украины.
Относительная нагрузка на добывающие подотрасли резко увеличивается. В период 1991 1998 годов при общем спаде производства металла на 40 % добыча руды уменьшилась только на 20 %. Уровень загрузки мощностей по производству готового проката составляет около 58 %, трубного производства примерно 30 %, а мощности по добыче и переработке железорудного сырья используются почти на 80 %.
Действующие и перспективные мощности по добыче железной руды в лучшем случае способны обеспечивать производство чугуна на существующем уровне. При неблагоприятном развитии ситуации уже в 2000 году производство чугуна из-за дефицита отечественной железной руды может сократиться до 28 млн. т.
Ни одну из нынешних проблем черной металлургии нельзя решить без соответствующей реорганизации сырьевой базы. От обоснованного выбора соотношения основных сырьевых ресурсов железной руды и металлического лома зависит развитие главных переделов доменного и сталеплавильного, их структурные пропорции и важнейшие показатели эффективности производства (энергоемкость, капиталоемкость, производительность) и уровень экологической безопасности. Эти соотношения повлияют на развитие черной металлургии в наступающем столетии, в частности на формирование региональной системы металлообеспечения, с учетом роли транспортной составляющей в структуре производственных затрат. Все это в конечном счете определит конкурентоспособность российской металлургии и на мировом рынке.
Для оценки экономических условий металлургического производства важнейшими являются цены на энергоносители, сырье, тарифы на транспорт, величина зарплаты. Меры по снижению цен на сырье и энергоносители, а также тарифов на транспортные перевозки, предпринимаемые Правительством РФ, могут обеспечить российской металлургии определенные преимущества перед зарубежными конкурентами, так как в России очень низкие издержки на оплату труда 1 2 долл/чел.-ч. В США этот показатель составляет 17, в Великобритании и Франции 12, в Германии 25 долл/чел.-ч. Однако уровень зарплаты должен рассматриваться совместно с показателями производительности труда. В 1997 году в черной металлургии России было занято 680 тыс. рабочих, при этом средний показатель человеко-часов на 1 т металлопродукции составил 19,5 по сравнению с 4,1 в странах-членах ЕС.
В настоящее время практически все металлургические предприятия имеют в своей номенклатуре продукцию, сертифицированную по международным стандартам. Но в основном сертифицированы такие виды проката, как катаная заготовка (доля ее в общем объеме составляет 29,4 %), толстый лист и горячекатаные рулоны (37,6 %), сортовой прокат (15,7 %), арматура периодического профиля (14,1 %), трубы нефтяного сортамента (90 %) и др. В 1998 году в России было изготовлено 8,7 млн. т сертифицированного проката (22,4 % от произведенного в отрасли) и 1,1 млн. т труб (31,5 % от общего производства).
Вступление России в ВТО вызовет необходимость цивилизованной защиты интересов российских производителей металлопродукции на мировых рынках. При этом чрезвычайно острый характер приобретают "технические барьеры", преодолеть которые предстоить при реализации следующих мероприятий:
согласование нормативной документации путем прямого применения в Российской Федерации зарубежных стандартов в качестве отечественных, гармонизации отечественных стандартов с зарубежными;
разработка государственных стандартов на продукцию и методы контроля, на которые действующие стандарты по объективным причинам не подлежат гармонизации или стандарты отсутствуют;
использование в стандартах на продукцию черной металлургии показателей свойств и требований, соответствующих директивам ЕС на обязательную сертификацию металлопродукции, применяемую на опасных промышленных производствах.
ЦВЕТНАЯ МЕТАЛЛУРГИЯ
В целом производство основных видов цветных металлов в России в 1998 году сократилось на 5 %. При этом выпуск никеля снизился на 2,9 %, титана на 5,6 %, свинца на 28,9 %, олова более чем в 2 раза. В то же время производство рафинированной меди увеличилось на 2,5 %, первичного алюминия на 3,4 %, цинка на 3,7 %.
Основным направлением реализации важнейших видов цветных металлов по-прежнему оставался экспорт, доля которого составила более 80 % от общего объема производства продукции цветной металлургии. И это при весьма неблагоприятной конъюнктуре на мировых рынках. В 1998 году на Лондонской бирже металлов произошло весьма ощутимое снижение цен практически на все виды цветных металлов. Так, цена на цинк снизилась на 13 %, меди на 12,7 %, алюминия на 35 %, никеля на 34,7 %.
С целью повышения конкурентоспособности продукции цветной металлургии ряд ее видов сертифицирован: алюминий марки А7Э, никель марок Н1, Н4, Н0, олово марки 01оч. Сертифицированы титановые полуфабрикаты: слитки, прутки под штамповку лопаток авиационных двигателей, штамповки деталей ракетных двигателей, полуфабрикаты из титановых сплавов (слитки, плиты, заготовки, поковки, листы, лента), титановая продукция для котлов, сосудов и трубопроводов высокого давления.
Спрос внутреннего рынка на основные цветные металлы в 1998 году оставался практически на уровне предыдущего года. При этом несколько возросло внутреннее потребление алюминия (на 3 %) в виде проката различного сортамента.
Наибольший прирост производства алюминия в 1998 году достигнут в основном на Богословском, Волгоградском и Братском алюминиевых заводах ( от 5,5 до 6,6 %). Среднегодовое использование производственных мощностей составило 98,3 %.
Высокий уровень производства и загрузки действующих мощностей алюминиевых заводов был обеспечен в основном за счет толлинговых операций по переработке импортного и отечественного сырья (бокситов и глинозема). В России добыча бокситов увеличилась на 4,3 %, выпуск глинозема на 3,6 %.
Удельный вес производства алюминия из давальческого сырья (толлинг) и поставок его на экспорт по прямым договорам в общем объеме производства алюминия в 1998 году находился на уровне 1997 года 88,9 % (89,4 %), при этом экспортные поставки алюминия, полученного из отечественного сырья, сократились с 17,9 % от общего объема производства до 8,1 %. Основная причина снижение цен на мировом рынке (с 1600 долл. за 1 т в 1997 г. до 1250 долл. в конце 1998 г.).
В крайне тяжелом состоянии продолжает оставаться прокатное производство алюминиевой промышленности России. Производственные мощности прокатных цехов загружены всего на 11 %. Основные причины такого состояния:
рост цен на первичный алюминий в 1,5 2,4 раза и соответственное повышение цен на полуфабрикаты из алюминиевых сплавов;
высокие тарифы на энергоресурсы, доля которых в затратах на производство составляет до 30 %;
низкий спрос на прокат из алюминия и алюминиевых сплавов из-за значительного снижения потребностей со стороны главных его потребителей (авиационной, автомобильной, электротехнической и строительной отраслей промышленности).
Прирост производства меди в 1998 году произошел в основном в РАО "Норильский никель" и ОАО "Уралэлектромедь" соответственно на 5,5 % и 12,3 %. На Кыштымском медеэлектролитном заводе в связи с недостатком оборотных средств для закупки сырья (черновой меди) производство меди снижено на 54,7 %. Стабильность производства меди и цинка на предприятиях цветной металлургии Урала по-прежнему в значительной степени зависит от поставок сырья иностранными фирмами по толлингу. В 1998 году из этого сырья произведено около 8,8 % меди и свыше 51,9 % цинка.
Произошел спад производства никеля. При этом если предприятия РАО "Норильский никель" увеличили его производство на 2,6 %, то на комбинатах "Южуралникель" и "Уфалейникель" объемы выпуска снизились соответственно на 46,7 % и 25,7 %.
Производство олова в 1998 году составило 44,7 % к уровню 1997 года. Основной причиной этого спада является снижение производства отечественных оловянных концентратов и прекращение толлинговых операций на Новосибирском оловянном комбинате из-за их убыточности.
Значительно снизилось производство свинца. Это вызвано главным образом уменьшением сбора и переработки вторичного сырья. Проблему решает акционерное общество "Рязцветмет", которое организовало сбор и переработку аккумуляторного лома и ввело в эксплуатацию цех по его разделке. В результате производство свинца на этом предприятии увеличено на 60,5 %.
Производство магния и его сплавов в 1998 году возросло и составило 105,2 % к уровню 1997 года. Из общего объема товарного магния, производимого на Соликамском магниевом заводе и в ОАО "Ависма", примерно 80 85 % экспортируется в страны дальнего зарубежья. При этом потребность внутреннего рынка обеспечивается полностью.
Производство губчатого титана в 1998 году составило 94,4 % к уровню 1997 года. Использование производственных мощностей в ОАО "Ависма" находится на уровне 62 %. Значительная часть произведенного губчатого титана экспортируется в страны дальнего зарубежья (США, Канаду, Германию, Францию, Японию и др.). Снижение производства губчатого титана вызвано сокращением его потребления основным производителем титанового проката Верхне-Салдинским МПО в связи с практически полным отказом компании "Боинг" (США) от ранее заключенных контрактов и ее переориентацией на потребление полуфабрикатов и слитков, производимых предприятиями США. В результате этого ведущее российское предприятие по производству слитков и проката в 1998 году снизило объемы производства титанового проката на 7,2 %, титановых слитков на 78,1 %. Перспектива сохранения устойчивой работы титановой промышленности России в развитии внутреннего рынка титановой продукции.
Более 60 % предприятий цветной металлургии являются убыточными. В 1998 году убытки в целом по предприятиям цветной металлургии составили более 3 млрд. руб., в то время как в 1997 году было получено 5,5 млрд. руб. прибыли.
Необходимо иметь в виду, что на большинстве предприятий цветной металлургии износ основных фондов составляет 50 70 %. Тяжелое финансовое положение предприятий не позволяет им целенаправленно проводить работу по модернизации производств, замене морально и физически устаревшего оборудования, внедрению прогрессивных технологий.
Первостепенной для цветной металлургии становится сырьевая проблема. Низкие темпы прироста запасов и отставание освоения новых мощностей по добыче руд цветных металлов от их выбытия могут в ближайшие годы стать главной причиной снижения производства основных видов продукции цветной металлургии. Это может произойти в тот момент, когда спрос на внутреннем рынке на эту продукцию начнет возрастать.
Оживление внутреннего рынка цветных металлов связано с увеличением их потребления в наиболее важных, социально значимых сферах, в том числе:
алюминия в производстве тароупаковочных материалов, строительных конструкций, транспортных средств;
меди в создании энергосберегающего безопасного оборудования и приборов, теплообменных аппаратов, прогрессивных видов медного и латунного проката для автомобилестроения, авиации, производства товаров длительного пользования;
цинка в производстве стальной оцинкованной продукции, резинотехнических изделий, лакокрасочных материалов.
Прогнозируемое увеличение спроса на цветные металлы определяется в основном расширением потребности в продукции четвертого передела. В первую очередь ожидается увеличение потребности в прокате из алюминия, меди, титана, латуни в среднем на 40 45 % к уровню 1998 года.
Металлургический комплекс России, переживающий в настоящее время трудную ситуацию, связанную в основном с рынками сбыта, имеет значительный потенциал для собственного развития и может стать локомотивом развития экономики России в целом. Ключ к этому в эффективной промышленной политике государства.
Важнейшая задача металлургической промышленности России ускоренное обновление и техническое переоснащение отрасли, реструктуризация металлургического производства на основе широкого использования новых технологий, обеспечивающих высокую эффективность производства, радикальное повышение качества и расширение сортамента металлопродукции, надежную охрану окружающей среды и решение социальных вопросов. При этом действующие металлургические предприятия должны следовать общемировой тенденции приведения своих производственных мощностей к наиболее эффективной и экономичной структуре.
Стратегия действий на рынке металлопродукции представляется в следующем виде.
На внутреннем рынке:
сохранение имеющихся потребителей металлопродукции;
углубленное изучение спроса на металлопродукцию с точки зрения сортамента и качества;
формирование спроса на новые виды продукции, пропаганда их эффективности;
проведение комплекса работ по снижению затрат на производство металлопродукции;
модернизация производств на базе прогрессивных технических решений;
формирование эффективных организационных структур в системе "производитель поставщик сырья и энергоресурсов потребитель металлопродукции";
постоянный мониторинг развития внутреннего рынка по видам металлопродукции.
На внешнем рынке:
сохранение и расширение имеющейся "ниши" в мировой торговле металлопродукцией;
расширение географических границ рынков для российской металлопродукции;
осуществление комплекса мер по снижению себестоимости экспортируемой металлопродукции;
стандартизация и сертификация российской металлопродукции по мировым стандартам;
увеличение доли продукции повышенной технической готовности в общем объеме экспорта;
рационализация транспортных маршрутов;
использование в практике российских предприятий системы бухучета, принятой в мире;
изучение практики и особенностей антидемпинговых расследований со стороны зарубежных стран во избежание их проведения по отношению к продукции конкретных российских предприятий;
активное сотрудничество с зарубежными организациями, контролирующими развитие соответствующих сегментов мирового рынка;
расширение сети представительств российских предприятий за рубежом.
Федеральная программа технического перевооружения и развития металлургии России (1993 2000 гг.) способствовала выработке стратегических и концептуальных подходов к перспективному развитию отрасли, выявлению "точек роста" металлургического производства, определению основных направлений государственной политики в области металлургии и разработки последующих этапов ее развития: проекта федеральной целевой программы "Структурная перестройка металлургии Российской Федерации до 2005 года" (долгосрочная социально-экономическая и инновационная программа).
Важным моментом является необходимость приведения производственных мощностей к гибкой, наиболее эффективной и экономичной структуре для быстрой реакции на запросы рынка при минимальных затратах на перестройку производства. При этом преследуется главная цель, оправдывающая затраты на реконструкцию и модернизацию производств, увеличить платежеспособный спрос на металл.
|