Валерий Борисов
Заведующий лабораторией композиционных материалов АО «ВАМИ», генеральный директор фирмы «СИНТАЛКО»
Ключевым условием развития машиностроения, в особенности транспортного, является разработка новых конструкционных материалов с технологическими и служебными свойствами, необходимыми для реализации новых конструктивных решений с приемлемыми производственными затратами. Один из наиболее ярких примеров автомобилестроение. Основная концепция создания машин новых поколений предусматривает снижение расхода топлива и вредных выбросов в атмосферу, улучшение эксплуатационных и ресурсных характеристик. А для этого требуется снижать массу автомобиля при сохранении или увеличении мощности двигателя. Многие крупные автомобилестроительные фирмы, такие как «Форд», «Дженерал Моторз», «Фольксваген-Ауди», работают над программой «Легкий автомобиль», цель которой поиск необходимых по свойствам и приемлемой стоимости материалов на основе легких сплавов.
Возможности традиционной технологии получения сплавов давно исчерпаны. Новые материалы для применения их в конструкции автомобилей или летательных аппаратов могут быть получены методом порошковой металлургии, т.е. смешением порошковых компонентов с последующим компактированием, дегазацией и термической обработкой. Однако производственные затраты при этом настолько велики, что использование полученных материалов в массовом производстве оказывается экономически нецелесообразным.
В последние годы машиностроители проявляют особый интерес к материалам нового класса, называемым композиционными и представляющим собой металлические материалы, упрочненные частицами интерметаллидных фаз или керамики, например, карбидов, оксидов, нитридов кремния, титана и других металлов, обладающих высокой твердостью. В литературе они известны под названием ММС metal matrix composites. Материалы такого типа по сравнению с известными сплавами обладают повышенными механической прочностью, жаропрочностью, износостойкостью, модулем упругости.
Проблемы производства композиционных материалов связаны с трудностью введения порошкообразных компонентов в матричные расплавы, в особенности в расплавы активных к кислороду металлов, таких как алюминий и магний. Имеющегося на поверхности частиц любых веществ адсорбированного кислорода достаточно, чтобы образовалась окисная пленка, препятствующая прямому контакту веществ частиц и матричного расплава.
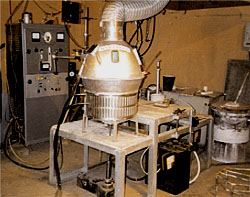 | Крупнолабораторная установка синтеза ММС на алюминиевой основе |
Фирма «Алкан», единственная в мире освоившая коммерческое производство композитов на основе алюминиевых сплавов, упрочненных частицами карбида кремния и оксида алюминия, использует специальные методы удаления кислорода с поверхности частиц перед их механическим замешиванием в матричный расплав. По-видимому, достаточно высокие производственные затраты при этом препятствуют широкому применению получаемых материалов в автомобильной промышленности.
В то же время только применение композиционных материалов может способствовать развитию транспортного машиностроения в будущем. Именно по этой причине в США в 1997 году под патронажем правительства создан консорциум разработчиков технологии, производителей и потребителей композиционных материалов на алюминиевой основе, в который вошли такие фирмы, как «Форд мотор», «Пратт энд Уитни», «Локхид». Основная задача консорциума резкое расширение применения композиционных материалов в ближайшем будущем за счет снижения производственных затрат и, соответственно, цен на эти материалы.
Важным звеном в технологической цепи производства изделий из алюминиевых сплавов является метод формовки исходного материала в изделие требуемой формы. Применительно к литейным сплавам такими методами могут быть литье в песчаные и металлические формы, литье под давлением и другие известные способы литья. В последние годы появилась и получила применение новая эффективная технология жидкотвердой формовки, реализация которой возможна только в том случае, если сплав перед формовкой имеет так называемую тиксотропную структуру. Такая структура может быть получена в процессе непрерывного литья слитков с электромагнитным перемешиванием затвердевающего расплава. К настоящему времени технологией МГД-литья владеют несколько фирм в мире, в том числе «Алюмакс» и «Ормет» (США) и «Пешине» (Франция). В то же время благодаря очевидным преимуществам интерес к этой технологии велик во всем мире.
Разработка эффективных технологий производства новых необходимых для развития машиностроения материалов, в том числе композиционного типа, стала стержневым направлением в деятельности фирмы «СИНТАЛКО».
Принципиальное отличие и преимущество технологии СИНТАЛКО состоит в использовании для введения порошковых компонентов в матричные расплавы метода плазменной инжекции через плазматрон специальной конструкции. Плазматрон представляет собой достаточно простое устройство в виде камеры с соплом, в которой имеется катодное устройство, а анодом является стенка камеры. Между катодом и анодом зажигается электрическая дуга, и в камеру подается плазмообразующий газ. В зоне дуги газ разогревается до нескольких тысяч градусов и ионизируется, в результате чего скорость истечения ионизированного газа из сопла достигает скорости звука. Корпус плазматрона и сопло охлаждаются водой.
Если в активную зону плазменного факела подать порошок какого-либо компонента, поверхность частиц будет подвергаться ионному травлению с удалением адсорбированного кислорода. Кроме того, частицы будут нагреваться и разгоняться до скорости газового потока, близкой к скорости звука.
Таким образом, применение плазматрона позволяет реализовать три основных условия введения частиц в матричный расплав очистку поверхности частиц, необходимую скорость частиц для внедрения их в расплав и нагрев частиц, необходимый для осуществления реакций синтеза композиционного материала.
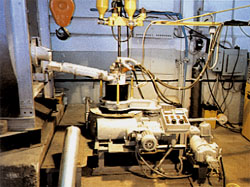 | Установка совмещенного синтеза и МГД-литья слитков композиционных материалов СИНТАЛКО |
Равномерное распределение частиц в объеме синтезируемого материала обеспечивается электромагнитным перемешиванием расплава в процессе инжекции компонентов.
Процесс синтеза материалов типа ММС по технологии СИНТАЛКО реализован на крупнолабораторной установке. Получены композиционные материалы на основе алюминиевых сплавов, в том числе новые материалы, производство которых известными методами невозможно. К ним относятся композиты типа «металл металл», получаемые инжекцией частиц железа, хрома, циркония и других малорастворимых металлов в алюминиевый расплав при температуре, близкой к температуре затвердевания матричного расплава. В результате химических реакций в матричном расплаве образуются частицы интерметаллидных фаз упрочнителей с управляемой морфологией и величиной частиц фаз, что позволяет получать материалы с заданной структурой и свойствами.
Плазматроны обеспечивают возможность введения любых порошковых материалов в любые применяемые матричные металлические расплавы. Таким образом, технология СИНТАЛКО является универсальной и может быть использована для производства композиционных материалов широкого ассортимента на любой основе.
Процесс синтеза может быть по различным вариантам совмещен с процессом непрерывного МГД-литья слитков. При этом достигается уникальная возможность получения слитков из композиционных материалов с тиксотропной структурой матрицы с последующим использованием исключительно эффективной технологии полутвердой формовки готовых изделий. Совмещенный процесс синтеза и литья слитков реализован на установке непрерывного МГД-литья промышленного типа.
Технология СИНТАЛКО защищена патентами России, США, Канады, Германии и патентными заявками в других странах.
Анализ затрат, выполненный в процессе производства опытных партий материалов по заказам нескольких фирм, показал, что за вычетом стоимости сырьевых материалов производственные затраты на 1 т материалов на алюминиевой основе составляют около 100 180 долл., что в несколько раз ниже затрат на производство подобных материалов методом порошковой металлургии.
Поставка технологий синтеза композиционных материалов и МГД-литья слитков, осуществляемая фирмой «СИНТАЛКО», подразумевает реализацию комплекса услуг, включающего поставку оборудования, осуществление проектных работ и авторского надзора, монтажные и пуско-наладочные работы, обучение персонала заказчика и сдачу производственных объектов на условиях «под ключ».
|