Игорь Довлядов, Виктор Смирнов, Евгений Шахпазов, Эдит Франтова
Разработанный ЦНИИчерметом и ВНИИметмашем с участием Гипромеза процесс «руда сталь» комплексно решает задачу производства стали из железорудного сырья. Его особенностями являются непрерывность, применение рядовых некоксующихся углей взамен кокса или природного газа, минимальная материало- и энергоемкость производства. Последнее обеспечивается сочетанием противотока и конвертерного режима обработки жидкого металла.
Кардинально решается проблема защиты от загрязнения окружающей среды. Полностью ликвидируются коксохимическое и доменное производства, являющиеся основными источниками загрязнения в черной металлургии. Ликвидируются также пылегазовые выбросы сталеплавильного производства. Предусмотрено использование закрытого проточного оборудования и замкнутого газового цикла. Особенностями технологии является также исключение образования окислов азота, относящихся ко II высокоопасному классу токсичности. Отходами процесса, помимо шлака, являются лишь конденсат водяного пара и углекислота.
Технологическая линия агрегата «руда сталь» включает шахтную печь, плавильно-восстановительный конвертер, рафинировочный реактор конвертерного типа и миксер-копильник стали. В шахтной печи проводится частичная на 75 85 % металлизация железорудных окатышей или кусковой руды. Колошниковый газ шахтной печи подвергается отмывке от углекислоты и рециркуляции.
Горячая частично металлизованная шихта непрерывно поступает в проточную ванну конвертера, постоянно заполненную жидким углеродистым металлом-полупродуктом. В эту ванну вдуваются пылевидный уголь, кислород, а также известь для офлюсования породы шихты и золы угля. Здесь происходят расплавление шихты, довосстановление и науглероживание железа. Агентом-восстановителем служит растворенный в металле углерод. Расход вдуваемого угля отвечает потребности на довосстановление и науглероживание железа, а также на покрытие всех тепловых затрат процесса, включая расплавление шихты и нагрев металла и шлака. Эта часть угля сжигается кислородом в ванне в режиме газификации с образованием восстановительного газа (сумма содержания окиси углерода и водорода 85 90 %) для металлизации шихты. Степень металлизации регулируется по критерию минимального расхода энергоносителей в конвертере при замкнутой газовой схеме процесса.
Конструкция конвертера включает, кроме продувочной, также проточную ванну для разделения металла и шлака. Вследствие непрерывности процесса и интенсивности массообмена при продувке ванны работающего конвертера постоянно заполнены металлом и шлаком конечного состава и температуры (1500 1550 oС). Содержание углерода в металле-полупродукте составляет 2,0 3,5 %, а содержание закиси железа в шлаке не превышает 7 8 % при основности 1,2 1,5, что предопределяет благоприятные условия службы футеровки конвертера.
Металл-полупродукт из конвертера непрерывно передается в проточный рафинировочный реактор. Последний конструктивно подобен конвертеру, но отличается меньшими размерами. Здесь осуществляется передел полупродукта в сталь с заданным содержанием углерода, продувкой кислородом и известью. Газы из реактора, состоящие в основном из окиси углерода, смешиваются с конвертерными газами и также используются в шахтной печи. Шлаки конвертера и реактора подвергаются непрерывной мокрой грануляции.
В миксере с индукционным нагревом осуществляются накопление стали перед сливом в ковш, коррекция ее температуры и предварительное раскисление. Использование миксера позволяет переключать агрегат на выпуск стали другой марки без потерь металла промежуточного состава. Окончательное раскисление стали производится в ковше. В период слива в ковш подача ее в миксер не прерывается.
Процесс предусматривает возможность использования кусковой руды вместо окатышей, использование офлюсованной шихты и загрузку флюсов в шахтную печь с полным или частичным исключением вдувания извести в конвертерную ванну.
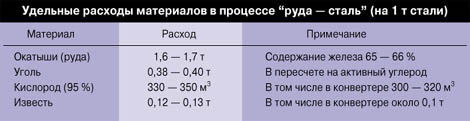
Предусмотрена также возможность использования сокращенной схемы процесса, предназначенной для производства жидкого чугуна для передела его в действующих агрегатах.
Каких-либо жестких ограничений качества железорудного сырья (в том числе по содержанию фосфора) и угля не имеется.
Единичная производительность агрегатов «руда сталь» оценивается величиной до 1 млн. т/год. В отличие от комплекса «домна-конвертер» они могут рационально использоваться при средних и небольших масштабах производства.
Исследование работы шахтной печи было проведено на Оскольском электрометаллургическом комбинате, где на промышленной печи произвели твердофазную металлизацию железорудного сырья до степени 80 85 % в соответствии с технологической схемой процесса «руда сталь». Установлено, что такой режим позволяет увеличить производительность печи на 30 45 %, снизить удельные энергозатраты на 20 25 %, увеличить степень использования газа за один проход с 30 до 50 %. Разработан технологический регламент подготовки и металлизации окатышей, обеспечивающий получение продукта основностью 1,2 со степенью металлизации 80 85 % и содержанием углерода не менее 3 4 %.
Исследование плавильно-восстановительного и рафинировочного процессов проводили на плавильно-восстановительном конвертере и рафинировочном реакторе производительностью 10 т/ч на опытном заводе ВНИИметмаша. Переработке подвергали холодные окатыши соответствующей степени металлизации (80 85 %). Были определены основные теплотехнические характеристики процесса и его основные расходные показатели применительно к промышленной реализации процесса. Эти показатели приведены в таблице.
Были отработаны аэро- и гидродинамика процессов в продувочной и отстойной ваннах, обеспечивающие достаточно совершенное перемешивание системы шлак металл при продувке, полное разделение и непрерывный выпуск ее компонентов. Проверены состав, запыленность и температура выделяющихся при продувке восстановительных газов, а также поведение вводимой с углем серы. Установлено, что примененный метод сжигания угля в погруженном кислородном факеле удаляет в газовую фазу около 80 % введенной с углем серы, оставшаяся часть серы примерно поровну распределяется в конвертере между металлом и шлаком указанной выше основности (1,2 1,5). При работе промышленного агрегата на углях с содержанием серы 0,5 - 0,6 % ее ожидаемое содержание в чугуне не превысит 0,035 %, в стали 0,015 0,020 %. Разработан и применен оригинальный технологический прием раздельного независимого регулирования температуры выпускаемого из конвертера металла (в пределах 1400 1550 oС) и содержания в нем углерода (в пределах 2,0 3,5 %). Установлено, что без принятия специальных мер все опробованные режимы исключают переход в металл кремния. Его содержание в чугуне было ниже 0,05 %. Содержание марганца не превышало 0,1 %.
На рафинировочном реакторе отработан прием регулирования консистенции десульфурирующего шлака при переделе чугуна в сталь без применения разжижающих добавок.
Проверены и уточнены основные решения конструкции конвертера и реактора, обеспечивающие стабильность протекания процесса с непрерывной выдачей металла и шлака.
В предварительном порядке определены темпы износа футеровки ванн конвертера и реактора. Установлено, что длительность кампании их непрерывной работы составит соответственно несколько месяцев и не менее 2 3 недель.
Главным параметром всего процесса, определяющим расход энергоносителей, служит реальный тепловой эффект обогрева барботирующей ванны погруженным углекислородным факелом, когда режим сжигания угля обеспечивает требуемый состав выделяющегося восстановительного газа. Этот эффект был проверен и уточнен в промышленных условиях на 300-тонной двухванной печи Череповецкого меткомбината, применяющего углекислородный обогрев ванны. Установлено, что при коэффициенте расхода окислителя 0,53 0,55, отвечающем технологии процесса «руда сталь», ванна воспринимает 1720 1730 ккал тепла от сжигания 1 кг углерода угля. На полупромышленных исследованиях этот показатель составил 1650 1660 ккал. Приведенные цифры близко соответствуют теоретическим при условии полного усвоения тепла ванной (уголь и кислород вдуваются холодными).
Перспективность процесса «руда сталь» ставит на очередь его предпромышленную комплексную доработку на агрегате достаточно представительного масштаба с возможностью проведения длительных непрерывных кампаний работы. С этой целью предлагается соорудить в существующем сталеплавильном цехе опытно-промышленный агрегат-стенд производительностью 15 20 т/ч.
|