|
|
Журнал |
|
Архив |
|
Подписка |
|
Реклама |
|
САММИТ |
|
Книжная полка |
|
Контакты |
|
В начало |
|
|
|
| |
|
|
 |
№6' 2004 |
версия для печати
|
|
СТАЛЬНЫЕ РУЧЬИ |
О ТЕНДЕНЦИЯХ РАЗВИТИЯ НЕПРЕРЫВНОЙ РАЗЛИВКИ СТАЛИ |
Алексей Смирнов
Профессор
Донецкий национальный технический университет (Украина)
епрерывная разливка стали относится к крупнейшим технологическим достижениям современной металлургии, органично связывающим процесс получения жидкой стали и ее трансформацию в деформированные полуфабрикаты заданных размеров и формы. За относительно короткий период с начала 60-х годов эта технология прошла путь от первых небольших полупромышленных агрегатов до современных высокопроизводительных машин непрерывного литья стальных заготовок (МНЛЗ). Сегодня более 80 % всей производимой в мире стали разливается этим способом. В черной металлургии большинства развитых стран удельный вес непрерывного литья превышает 95 %. К началу текущего столетия были сформированы основные положения, определяющие состояние и динамичное развитие этого способа:
разработана теория непрерывной разливки, которая располагает всем необходимым комплексом решений для создания высокоэффективных технологических систем для получения стальной заготовки традиционных сечений;
создана развитая машиностроительная база для изготовления оборудования, отвечающего требованиям конкретного сталеплавильного цеха и концепции его развития;
создан комплекс автоматизации процессов непрерывной разливки стали, включающий систему автоматического поддержания уровня металла в кристаллизаторе, систему контроля уровня и кондиций металла в промковше, систему динамического охлаждения заготовки в зоне вторичного охлаждения, систему диагностики качества заготовки и пр.
в настоящее время для большинства сталеплавильных цехов основной акцент делается на реконструкции действующих МНЛЗ с целью повышения качества заготовки, производительности оборудования и наиболее полного совмещения сталеплавильных агрегатов и МНЛЗ в единый квазинепрерывный процесс.
Весьма характерно, что примерно 5055 % всех МНЛЗ были сооружены либо реконструированы в последние 1012 лет. Прогрессивные изменения касаются практически всех основных технологических и конструктивных аспектов и носят взаимосвязанный характер. Поэтому целесообразно дать дифференцированный анализ тенденций развития основных технологических и конструктивных решений, используемых в современных сталеплавильных цехах с непрерывной разливкой стали.
Непрерывная разливка плоской заготовки. Основное производство плоской непрерывнолитой заготовки (сляба) осуществляется в рамках «классической» технологической схемы: доменная печь конвертер внепечная обработка непрерывная разливка прокатный стан. Сейчас в мире насчитывается чуть более 500 слябовых МНЛЗ разных фирм (рис. 1) с общим числом ручьев свыше 700 (рис. 2), которые работают на заводах Японии, США, КНР, Германии, Кореи и России. На их долю приходится более 2/3 общего объема производства слябов в мире. При этом получают, главным образом, сляб толщиной 180300 мм. Слябовые МНЛЗ претерпевают значительные конструктивные изменения:
в большинстве случаев предпочтение отдается машинам с вертикальным кристаллизатором и вертикальным участком (1,52,5 м) под ним, что обеспечивает повышение качества заготовки при одновременном увеличении производительности в 1,41,5 раза;
применяется криволинейная схема технологической линии МНЛЗ с многоточечным загибом и разгибом заготовки, что в совокупности со значительным уменьшением диаметра поддерживающих роликов и более плотным их расположением позволяет уменьшить деформации в твердой корочке;
предусматривается возможность изменения ширины заготовки непосредственно в ходе разливки;
увеличивается емкость промежуточного ковша до 4560 т, что обеспечивает большее время пребывания в нем металла и более устойчивую его подачу в кристаллизатор, в том числе и при замене сталеразливочных ковшей;
часть операций по доводке стали переносится в промковш (продувка аргоном, обработка порошковой проволокой, подогрев металла и т.п.);
ужесточаются требования к защите стали от вторичного окисления на всем протяжении движения стали от ковша до кристаллизатора;
обязательно используется непрерывный замер температуры металла в промковше и в отдельных зонах движения заготовки;
применяется электромагнитное перемешивание металла ниже кристаллизатора;
обязательно используется система автоматического поддержания уровня металла в кристаллизаторе;
обязательно используется система автоматической подачи шлакообразующей смеси в кристаллизатор.
В результате применения этих решений достигается существенный рост производительности МНЛЗ, улучшение качества поверхности и внутренней структуры сляба, снижение затрат на строительство машины и ее обслуживание и т.п. Например, современные МНЛЗ имеют производительность в 1,51,8 раза выше, чем машины, построенные 15 лет назад. Это позволяет предположить, что существенного роста числа МНЛЗ в мире не будет, поскольку возрастет их удельная производительность.
Генеральным направлением развития технологии и конструктивного оформления МНЛЗ для получения плоской заготовки является уменьшение ее толщины, что обеспечивает снижение затрат на последующую прокатку, уменьшение базового радиуса машины и создание условий для совмещения разливки и прокатки в единый технологический цикл (например, посредством стана Стеккеля). В последнее десятилетие все большее применение получают МНЛЗ для отливки слябов средней (100150 мм) толщины, тонких слябов (около 5060 мм и меньше), а также полосы толщиной 610 мм.
Наиболее серьезным научным прорывом представляется создание рядом западных фирм МНЛЗ для разливки тонкого сляба, обеспечивающей качество на уровне листа из традиционного сляба. Преимуществами такой технологии является также возможность получения слябов шириной свыше 3000 мм, уменьшение потерь энергии и металла в ходе последующего прокатного передела и пр. Отличительной особенностью таких МНЛЗ является принципиально новая конфигурация внутренней полости кристаллизатора, имеющей так называемую чечевицеобразную форму. При этом толщина сляба в осевой зоне у мениска составляет, как правило, 150170 мм при толщине на выходе из кристаллизатора 5570 мм. Такая конфигурация кристаллизатора позволяет не только обеспечить подвод металла с помощью погружного стакана специальной плоской формы («бобровый» хвост), но и улучшить питание жидкой сердцевины заготовки за счет обжатия твердой корочки в нижних горизонтах.
В целом же в этом случае в основу технологии получения листа положена концепция литейно-прокатных модулей, промышленная реализация которой позволила обеспечить все необходимые условия для строительства металлургических мини-заводов для производства листа, которые конкурентоспособны по ряду параметров с интегрированными металлургическими предприятиями с традиционной технологией. Литейно-прокатные модули, созданные на базе непрерывной разливки стали на тонкий сляб, в настоящее время получают все большее распространение в развивающихся странах, где растет потребность в листовом прокате. По оценкам, во многом благодаря использованию наиболее современных достижений в области непрерывной разливки стали (электромагнитное перемешивание, «мягкое» обжатие, погружной стакан типа «бобровый» хвост и пр.) эти модули будут использоваться и в перспективе
Технология непрерывной разливки с прямым получением листа (полосы) является едва ли не самым последним концептуальным решением в области литья стали, направленным на кардинальное снижение производственных затрат. Сама идея отливки тонкой полосы между двумя вращающимися водоохлаждаемыми валками была запантентована еще в 1866 году Г. Бессемером. Однако понадобилось более 130 лет для того, чтобы перейти к промышленной реализации способа. Эта технология имеет вполне очевидные преимущества и удачно совмещает дискретный процесс выплавки стали с процессом непрерывной разливки и прокатки. При этом она исключает из производственной цепочки дорогостоящие операции повторного нагрева заготовки и многократного обжатия сляба.
Существо процесса заключается в том, что сталь поступает из промежуточного ковша в пространство между валками, которые вращаются в противоположных направлениях (рис. 4). При контакте с поверхностью валков образуются твердые корочки, которые двигаются вместе с поверхностью и выходят из валков в форме листа, толщина которого определяется расстоянием между валками, а ширина боковыми стенками кристаллизатора. По данным различных разработчиков, в процессе непрерывной разливки с прямым получением листа применяются скорости 25100 м/мин при толщине листа 1,56 мм и ширине 12001700 мм. Предполагается, что на базе этой технологии можно будет создать вполне рентабельные мини-заводы с годовым производством 200300 тыс. т. При этом продукция сможет заменить и обычную горячекатаную полосу, и часть холоднокатаной.
Для практической реализации этого способа необходимо решение ряда достаточно сложных проблем. В первую очередь, требуется дальнейшее развитие теории процессов быстрого затвердевания стали, а также создание системы измерений переменных технологических параметров с повышенной точностью, обеспечение точности работы системы дозирования стали и поддержания уровня металла в кристаллизационной ванне, использование новых конструкционных материалов и покрытий для повышения эксплуатационной стойкости разливочных валков.
Непрерывная разливка блюмов и фасонных заготовок. Производство крупных заготовок прямоугольного, квадратного, круглого и фасонного (балка) сечений развивается в последние годы в направлении повышения качества при повышении производительности МНЛЗ. Мировой объем выпуска этих полуфабрикатов 130135 млн т в год. На начало 2003 года в мире насчитывалось 285290 блюмовых МНЛЗ (10501070 ручьев), около 50 машин для разливки крупной фасонной заготовки и около 100 для получения круглой заготовки. При этом средняя производительность одного ручья блюмовой машины составляет примерно 125130 тыс. т стали в год, при максимальных показателях на ряде японских и австралийских заводов до 300400 тыс. т. Находящиеся в эксплуатации МНЛЗ отличаются значительным разнообразием конструктивных и технологических признаков.
Для разливки рядовых и качественных сталей общего назначения используются, как правило, МНЛЗ радиального и криволинейного типа. При этом сечение заготовки определяется, главным образом, требованиями сопряженных прокатных цехов. Для машин этого класса характерна возможность получения заготовок нескольких сечений при высокой производительности процесса.
Задача повышения производительности блюмовой МНЛЗ за счет повышение скорости разливки имеет свои технологические и конструктивные ограничения. Очевидно, дальнейшее повышение скорости разливки может быть достигнуто только при применении кристаллизаторов усовершенствованной конструкции в совокупности со специальными методами подвода и перемешивания металла.
На практике для обеспечения высокой производительности применяются многоручьевые машины. Основная часть блюмовых МНЛЗ имеет 24 ручья (рис.3). На долю 6-ручьевых приходится не более 1/5 всего количества ручьев, что связано с ограниченным числом сталеплавильных цехов, где возможно применение таких МНЛЗ (большая единичная мощность сталеплавильного агрегата, необходимость использования промковшей большой емкости, повышенные требования к температурной однородности стали и пр.).
В последнее десятилетие обновление производства блюмовой заготовки в основном обеспечивается за счет реконструкции действующих агрегатов при весьма ограниченном строительстве новых, что, вероятно, объясняется насыщенностью рынка этих полуфабрикатов. В процессе реконструкции широко используются такие конструкционные решения, как применение прямолинейного кристаллизатора с вертикальным участком под ним (взамен радиального), системы многоточечного загиба и разгиба заготовки, промковшей с высоким уровнем зеркала металла, повышение скорости и серийности разливки, широкое использование автоматических систем управления процессом, применение систем гидравлического качания кристаллизатора и системы «мягкого» обжатия заготовки.
Для разливки высококачественных сталей используются МНЛЗ криволинейного типа с вертикальным кристаллизатором, а также вертикального типа с загибом твердой заготовки. Как правило, это одно-, двух- или четырехручьевые МНЛЗ, которые расположены в электросталеплавильных цехах, оснащенных вакуумными станциями и агрегатами ковш-печь. На таких МНЛЗ разливают высоколегированные и нержавеющие стали, а также стали с особыми свойствами. Скорость вытягивания заготовки при этом оказывается достаточно низкой 0,350,5 м/мин.
Чисто вертикальные блюмовые МНЛЗ имеются в настоящее время во многих странах Франции, Германии, Японии, Италии, США и др. Однако вертикальных машины достаточно мало в последнее время большее распространение получили МНЛЗ с вертикальным кристаллизатором и многоточечным загибом и разгибом заготовки.
Наиболее перспективным направлением при производстве широкополочных балок является применение фасонных двутавровых заготовок, получаемых на МНЛЗ. Использование непрерывной разливки стали для получения фасонной заготовки позволяет сократить удельный расход металла, исключить обжатие на обжимных станах, что существенно снижает себестоимость готового проката. Тип фасонной заготовки определяется минимальным числом проходов при прокатке, необходимым для получения заданной микроструктуры.
Непрерывная разливка фасонных заготовок получила в мире широкое распространение. Ведущими производителями таких МНЛЗ являются фирмы SMS-Concast (Германия-Швейцария), MDM (Германия), а также японские концерны Mitsubishi и Sumitomo. Наиболее широко эта технология используется на заводах США, Японии и Южной Кореи. Практически все МНЛЗ для производства балочных фасонных заготовок в конструкционном плане являются комбинированными и могут быть использованы для разливки прямоугольных заготовок.
Основные преимущества разливки балочных фасонных заготовок заключаются в экономии капитальных затрат для нового балочного стана до 2530 % за счет исключения черновой клети, повышении производительности на 15 % за счет исключения черновых проходов, снижении энергозатрат на 50 % за счет уменьшения числа обжатий, повышении выхода годного на 11,5 %. Эти преимущества подходят для создания нового производства и гораздо менее очевидны при использовании непрерывнолитых балочных фасонных заготовок в существующем. В любом случае это требует существенной коррекции режимов прокатки, а также адаптации оборудования к прокатке непрерывнолитой заготовки. Наиболее эффективным оказывается технологическое построение, в котором машина для литья балочных заготовок непосредственно совмещена с прокатным станом.
Непрерывное литье круглых заготовок, являющихся исходным продуктом для производства бесшовных труб, колес, бандажей, колец различных назначений и катанки, получило наиболее широкое развитие в последние два десятилетия, чему способствовали достижения в области внепечной обработки, а также совершенствование агрегатов и процесса непрерывной разливки. Основными производителями машин для разливки круглых заготовок являются фирмы MDM (Германия), Concast (Швейцария) и Danieli (Италия».
Исследованиями в ФРГ, США, Японии и бывшем СССР установлено, что использование круглой заготовки по сравнению с непрерывнолитыми блюмами при производстве труб имеет определенные преимущества. Круглая форма способствует рассредоточению возникающей в осевой зоне центральной пористости и ликвации. Поверхность заготовки более высокого качества (нет продольных и угловых трещин). В результате качество труб, изготовленных из круглой непрерывнолитой заготовки, обычно выше, чем из квадратной, повышенная плотность равноосной структуры в осевой зоне заготовок обеспечивает снижение количества микродефектов, обычно образующихся на внутренней поверхности трубы из-за наличия осевой пористости.
Размерный сортамент литых круглых трубных и колесных заготовок довольно широк: от 150 до 500 мм. Качественные трубные марки сталей разливаются преимущественно на радиальных или криволинейных МНЛЗ с многоточечным загибом и разгибом, что позволяет получать заготовки диаметром 300400 мм. Базовый радиус на этих машинах колеблется в пределах 1214 м в зависимости от максимального диаметра отливаемой заготовки. Исключение, видимо, составляет пятиручьевая МНЛЗ № 7 на заводе Mannesmann (Дуйсбург, Германия), имеющая базовый радиус 10,5 м и три последующих радиуса выпрямления (13,5, 18 и 36,6 м). На этой МНЛЗ отливают заготовки диаметром от 177 до 435 мм.
В целом же МНЛЗ для получения круглой заготовки получают все большее распространение в странах с развитым металлургическим и машиностроительным комплексом, в том числе в Восточной Европе. Так, в последние годы для разливки круга диаметром 160320 мм в Польше сооружено 4 МНЛЗ (18 ручьев), в Чехии 6-ручьевая МНЛЗ для разливки круга диаметром 210 мм, в Румынии 3-ручьевая МНЛЗ для разливки круга диаметром 250280 мм, в КНР 4-ручьевая МНЛЗ для разливки круга диаметром 180350 мм, 3-ручьевая и 2-ручьевая МНЛЗ с максимальным диаметром заготовки, соответственно, 430 и 500 мм, в России на Нижнетагильском металлургическом комбинате 4-ручьевая радиальная МНЛЗ с диаметром заготовки 430 мм.
Общие тенденции развития технологии непрерывной разливки стали на блюмовых МНЛЗ можно сформулировать следующим образом:
повышение удельной производительности за счет реконструкции уже существующих машин и создания новых высокоэффективных комплексов;
развитие системы подготовки стали к непрерывной разливке и согласование работы сталеплавильных агрегатов с МНЛЗ путем использования агрегатов типа «печь-ковш»;
развитие функциональных возможностей промковша в части повышения его эксплуатационных показателей (стойкость) и возможностей по доводке стали (рафинирование и регулирование температуры);
система мероприятий по предотвращению загрязнения стали в промковше (эмульгирование с покровным шлаком) и в ходе перелива в кристаллизатор (вторичное окисление);
применение вертикального кристаллизатора, а также полностью вертикальных МНЛЗ для получения высококачественной заготовки;
применение новых конструкций кристаллизаторов и механизмов качания кристаллизаторов с гидроприводом;
применение электромагнитного перемешивания в нескольких уровнях по длине заготовки;
обеспечение эффективной защиты стали от вторичного окисления на участке «сталеразливочный ковш промковш»;
создание оптимальных условий для работы кристаллизатора путем подвода стали под уровень с помощью погружных глуходонных стаканов с боковыми отверстиями, автоматического контроля и поддержания уровня металла в кристаллизаторе;
использование метода «мягкого» обжатия заготовки с жидкой сердцевиной с целью подавления осевой пористости и ликвации.
повышение степени автоматизации работы МНЛЗ с включением в единую систему всех параметров жидкой стали, условий ее охлаждения в кристаллизаторе и зоне вторичного охлаждения при наличии обратной связи.
В последнее время также полностью оформилась тенденция создания комбинированных МНЛЗ, которые позволяют разливать несколько различных сечений блюмов, а также круглых или фасонных заготовок.
Непрерывное литье сортовой заготовки сечением квадрат 100180 мм, в первую очередь, связывается с распространением концепции мини-заводов. Инновационные решения в области интенсификации работы электросталеплавильной печи (плавка менее чем за 60 мин.) и применение в технологической системе агрегатов «ковш-печь» обусловили в начале 90-х годов целесообразность создания высокопроизводительных многоручьевых сортовых МНЛЗ для динамично растущих мини-заводов. На начало 2003 года в мире насчитывалось свыше 3900 ручьев сортовых МНЛЗ, что обеспечило разливку примерно 185190 млн т стали. Однако из этого количества только 1518 % можно считать современными высокоскоростными агрегатами.
Наибольший практический интерес представляет создание высокопроизводительных технологических модулей «дуговая сталеплавильная печь ковш-печь сортовая высокоскоростная МНЛЗ». Годовое производство такого модуля составляет 0,91,2 млн т для 6-ручьевой машины. Получаемая при этом сортовая заготовка, как правило, является конечным продуктом, поставляемым на внешний рынок, где эта металлопродукция в последние годы имеет хороший спрос и стабильно высокую цену.
Примером такого построения является ЗАО «Миниметаллургический завод «ИСТИЛ (Украина)» (г. Донецк). Этот мини-завод создан на базе ЭСПЦ Донецкого металлургического завода в начале нового века. В его состав входит высокопроизводительная 120-тонная дуговая сталеплавильная печь, установка «ковш-печь», вакууматор VD/VOD и 6-ручьевая высокоскоростная сортовая МНЛЗ. Вся непрерывнолитая заготовка реализуется на внешнем рынке. По результатам 2003 года этот завод практически вышел на проектные показатели, что позволяет назвать «ММЗ «ИСТИЛ (Украина)» одним из наиболее современных мини- заводов, по крайней мере, в странах Восточной Европы.
Развитию и тотальному применению метода непрерывной разливки сортовой заготовки способствовали следующие достижения:
радикальное повышение производительности МНЛЗ за счет увеличения скорости вытяжки заготовки до 56 м/мин в совокупности с увеличением числа ручьев до 68;
разработка высокостойких огнеупорных материалов, используемых для дозирования стали (стаканы-дозаторы) и для рабочего слоя футеровки промковша, что обеспечивает разливку сериями 2030 плавок из одного промковша с последующей его заменой без остановки МНЛЗ;
кардинальное повышение товарного качества непрерывнолитой заготовки за счет автоматизации процесса разливки и порезки;
создание и конструктивное оформление концепции универсальных высокоэффективных технологических модулей для выплавки и разливки стали.
Тенденция увеличения производительности сортовой МНЛЗ путем повышения скорости разливки продолжает развиваться. Поэтому многие научно-технические разработки в этой области направлены на усовершенствование конструкции кристаллизатора за счет повышения интенсивности и равномерности теплоотвода. Это требует детального анализа процессов, проходящих на границе металл-стенки кристаллизатора. Поскольку отвод тепла в значительной степени зависит от наличия воздушного зазора между стенками кристаллизатора и коркой непрерывного слитка, то теплопередача может быть оптимизирована в том случае, если контур внутренней поверхности кристаллизатора будет в максимальной степени соответствовать контуру твердой корочки непрерывного слитка. Этот контур в значительной мере определяется ее первичным формированием на мениске и характеризуется изменением объема металла под влиянием температуры и ферростатического давления во время прохода через кристаллизатор. Поэтому ведущие фирмы-производители кристаллизаторов стремятся делать поправку на естественную усадку непрерывнолитого слитка и выполнять внутреннюю поверхность кристаллизатора в виде так называемого параболического профиля.
Промышленное использование таких кристаллизаторов показало, что они позволяют в 2,53 раза увеличить скорость литья для заготовок малого сечения (до 5,56,5 м/мин). Обычно рабочая поверхность этих кристаллизаторов имеет специальное многослойное покрытие, обеспечивающее повышенную эксплуатационную стойкость. Благодаря улучшению условий теплопередачи по всей длине кристаллизатора его технологическая длина увеличивается до 10001200 мм. Вместе с тем следует отметить, что при использовании параболических кристаллизаторов может наблюдаться повышенное трение заготовки на выходе из него. Это приводит к повышенному износу стенок кристаллизатора в нижней части, что обусловливает ухудшение условий теплоотвода и появление дефекта геометрической формы заготовки в виде ромбичности.
Альтернативной конструкцией кристаллизаторов для высокоскоростной разливки является технология «Конвекс» (фирма Concast). Она предполагает использование кристаллизатора переменного поперечного сечения: в зоне мениска поверхность заготовки имеет ярко выраженную выпуклую форму, что улучшает условия теплоотвода через стенки кристаллизатора. По мере опускания заготовки выпуклость боковых граней, которая формируется стенками кристаллизатора, плавно уменьшается, и в нижней части кристаллизатора заготовка приобретает строго квадратную форму. При этом толщина твердой корочки по всему поперечному сечению заготовки сохраняется постоянной. Использование технологии «Конвекс» позволило повысить скорость разливки до 6,4 м/мин (квадрат 108 мм) на сортовой МНЛЗ металлургического завода «Тршинецке Железарни» (Чехия).
Таким образом, бурное развитие техники и технологии позволили ведущим производителям сортовых МНЛЗ существенно повысить их производительность и обеспечить высокое качество заготовки. Современная сортовая МНЛЗ обязательно несет в себе следующие конструктивные и технологические решения: производительность одного ручья до 250 тыс. т стали в год, скорость разливки до 66,5 м/мин, разливка осуществляется как открытой, так и закрытой струей, кристаллизатор удлиненный параболический или другой специальной геометрической формы, способствующей эффективному формированию качественной твердой корочки, предпочтительное число ручьев 46 (иногда 78), автоматический контроль уровня металла в кристаллизаторе, электромагнитное перемешивание в кристаллизаторе и т.п.
В целом процесс непрерывной разливки стали, как один из наиболее молодых технологических процессов, сохраняет значительный запас совершенствования и развития.
Рис. 1. Количество слябовых МНЛЗ разных фирм
Sumitomo
5 %
SMS
6 %
MDM
44 %
VAI
33 %
Другие
12 %
VAI
MDM
SMS
Sumitomo
Другие
Рис. 2. Долевая оценка современных слябовых МНЛЗ разных фирм
1-ручьевые машины
VAI
33 %
MDM
33 %
SMS
5 %
Sumitomo
10 %
Другие
19 %
VAI
MDM
SMS
Sumitomo
Другие
2-ручьевые машины
VAI
40 %
MDM
38 %
SMS
8 %
Sumitomo
3 %
Другие
11 %
VAI
MDM
SMS
Sumitomo
Другие
Рис. 3. Доля блюмовых МНЛЗ с различным количеством ручьев
5,9
11
0,7
6,6
23,1
14,7
38,1
1
2
3
4
5
6
7
8
|
|
|
|
|
текущий номер

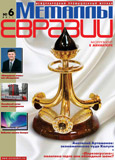
предыдущий номер

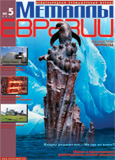
|
|