|
|
Журнал |
|
Архив |
|
Подписка |
|
Реклама |
|
САММИТ |
|
Книжная полка |
|
Контакты |
|
В начало |
|
|
|
| |
|
|
 |
№1' 2004 |
версия для печати
|
|
НА УРОВНЕ МИРОВЫХ АНАЛОГОВ |
|
Владимир Рождественский
Генеральный директор ОАО «ЧМЗ»
Александр Шиков
Заместитель директора ВНИИНМ им. А.А. Бочвара
Валентина Аржакова
Начальник лаборатории ВНИИНМ им. А.А. Бочвара
овременный технологический цикл производства циркония и его сплавов представляет совокупность последовательных химических и металлургических операций. Важнейшим переделом является выплавка исходного слитка, так как на этом этапе задается химический состав и формируются основные физико-механические свойства металла. На Чепецком механическом заводе в качестве исходных материалов для выплавки промышленных слитков циркониевых сплавов используются порошок циркония закрытого электролизера, йодидный цирконий в виде прутков, оборотные отходы циркониевых сплавов, а также легирующие добавки. Металлический порошок циркония реакторной чистоты в виде частиц от 100 до 1000 мкм производится методом электролиза расплавленных солей в герметичных электролизерах. Йодидные прутки диаметром около 20 мм получают в специальных вакуумных ретортах в процессе переработки оборотного металла. Количественное соотношение компонентов в шихте определяется материальным балансом, исходя из объема производства циркония и наличия оборотного металла. Сортамент циркониевой продукции ОАО «ЧМЗ» включает несколько сплавов, используемых в современной атомной энергетике (см. таблицу).
В процессе подготовки к плавке смесь порошка циркония и легирующих элементов, отрезки прутков йодидного циркония спрессовываются на гидравлическом прессе в полые брикеты, в отверстия которых вставляются штанги оборотного металла. Собранные таким образом цилиндрические электроды спекаются в вакуумной печи. Выплавка слитков производится в основном двукратным вакуумно-дуговым переплавом (ВДП) электрода.
Схема последовательных операций процесса производства слитков представлена на рисунке 1. Реконструкция плавильного передела, проведенная в последние годы, позволила повысить технический уровень производства, качество изделий и улучшить технико-экономические показатели:
масса слитка увеличилась с 1200 до 3500 кг, при этом повысилась его однородность (гомогенность структуры, распределение легирующих элементов);
за счет увеличения массы слитка и использования оплавления боковой поверхности взамен оболочки слитка значительно возрос коэффициент использования металла (КИМ);
выход годного при изготовлении изделий из сплава Э110 вырос практически до теоретического уровня.
В настоящее время в цехе используется высокопроизводительное оборудование, отвечающее самым высоким современным требованиям, в том числе:
вакуумно-дуговые печи VAR L 500 PZr фирмы «ALD-вакуумные технологии» (Германия) с глухим кристаллизатором и автоматизированной системой управления. Печи используются для первого и второго переплавов оборотного металла и штатных слитков;
электронно-лучевые печи с вытягиванием слитка для первого переплава оборотов и для первого переплава сплава Э125;
электронно-лучевые установки с автоматизированной системой управления для оплавления боковой поверхности слитков (взамен механической обработки) и сварки слитков первого переплава в электрод для второго переплава, также изготовленные фирмой «ALD-вакуумные технологии».
На заводе успешно используется высокоэффективная электронно-лучевая плавка. В электронно-лучевых плавильных установках формирование слитка производится в охлаждаемом кристаллизаторе методом непрерывной разливки. При этом поверхность жидкого металла постоянно находится у верхнего среза кристаллизатора, что создает благоприятные условия для его рафинирования. Изменением интенсивности электронного потока можно плавно регулировать скорость плавки в широком диапазоне, так что время выдержки жидкого металла в вакууме и степень его перегрева практически не ограничены. В производстве циркония переплав в электронно-лучевых установках кусковых отходов различной формы позволяет получить компактный расходуемый электрод для дальнейшего вакуумно-дугового переплава и при этом обеспечить их рафинирование от газовых и легколетучих примесей. Кроме того, на этих установках производится переработка стружки, которая сначала прессуется в брикеты или таблетки, а затем подается в кристаллизатор при помощи шнекового устройства.
Электронно-лучевой способ расплавления металла применяется также для оплавления боковой поверхности слитков перед их передачей на ковку. Использование этой технологии позволяет повысить коэффициент использования металла, что полностью исключает применение механической обточки и, соответственно, расход металла в стружку. Такие установки эксплуатируются в ОАО «ЧМЗ» около 20 лет. В процессе реконструкции в 1999 году на предприятии для оплавления боковой поверхности электронным лучом были смонтированы две новые современные установки фирмы «ALD вакуумные технологии». Уникальность этих агрегатов также в том, что в них можно сваривать брикеты при изготовлении электродов для вакуумно-дуговой плавки.
Среди последних технологических новинок можно выделить успешно решенную проблему повышения уровня содержания кислорода в слитках сплава Э110. Исследования показали, что кислород положительно влияет на физико-механические и эксплуатационные характеристики изделий из циркониевых сплавов, существенно повышая прочность и сопротивление ползучести. В ряде случаев, когда используемая шихта (электролитический порошок, обороты и йодидные прутки циркония) не обеспечивают требуемого содержания кислорода в сплаве, становится необходимым дополнительное микролегирование сплава кислородом. Поэтому для повышения уровня его содержания в сплаве Э110 специалистами ВНИИНМ им. А.А. Бочвара и завода была разработана технология выплавки промышленных слитков, легированных кислородом, путем введения в исходную шихту двуокиси циркония или пентаоксида ниобия. Исследования химического состава слитков и штанг показали, что распределение кислорода равномерное и разброс его содержания в объеме одного слитка не превысил 120 ppm.
Мощный производственный потенциал, широкое использование прогрессивных технических достижений, современные технологии и высокоэффективный жесткий контроль позволяют предприятию выпускать наукоемкую продукцию, отвечающую мировым аналогам, а по ряду признаков превосходящую их. От сырья до готовых изделий таков технологический цикл ОАО «ЧМЗ». Благодаря высокому качеству разработок выпускаемая продукция пользуется повышенным спросом на внутреннем рынке и успешно реализуется за рубежом.
|
|
|
|
|
текущий номер

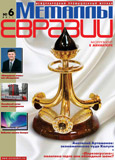
предыдущий номер

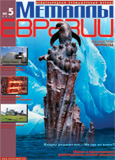
|
|