|
|
Журнал |
|
Архив |
|
Подписка |
|
Реклама |
|
САММИТ |
|
Книжная полка |
|
Контакты |
|
В начало |
|
|
|
| |
|
|
 |
№1' 2004 |
версия для печати
|
|
ИСТОЧНИК ИНВЕСТИЦИЙ ВНУТРЕННИЕ РЕЗЕРВЫ |
О ПЕРСПЕКТИВАХ РАЗВИТИЯ ПОДЗЕМНОЙ ДОБЫЧИ ЖЕЛЕЗНОЙ РУДЫ |
Валерий Кирпиченко
Начальник отдела научно-технического развития ОАО «Рудпром», кандидат технических наук, заслуженный шахтер России
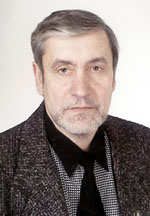 Валерий Кирпиченко |
|
елезная руда добывается подземным способом в России и за рубежом, в частности, в Швеции, Франции, Канаде, США. На эти страны приходится около 80 % такой добычи в дальнем зарубежье, причем в Швеции находятся самые крупные подземные рудники.
В бывшем Советском Союзе подземная добыча железной руды велась на шахтах 21 горнорудного предприятия, при этом доля такого способа общесоюзном объеме составляла в 1990 году 11,2 %. К 2000 году предполагалось даже увеличить долю подземной добычи железной руды по мере отработки запасов ряда крупных карьеров.
В настоящее время часть рудников оказались на Украине и в Казахстане.
В России добыча подземным способом сосредоточена в основном на 9 железорудных предприятиях, эксплуатирующих 11 шахт. Кроме того, на двух предприятиях строятся две новые шахты, а на третьем проектируются подземные работы. Все эти предприятия курирует ОАО «Рудпром». Несмотря на уменьшение числа рудников в России, доля добычи железной руды подземным способом оставалась на уровне 1011 %, но с 1996 года началось ее снижение, и в 2002 году этот показатель составил 8,2 %.
Подземные предприятия расположены в разных регионах страны. В Центральном находится акционерное общество «Комбинат «КМАруда», обеспечивающее 22 % всей подземной добычи предприятий «Рудпрома», на Урале (33,5 % добычи) акционерные общества «Бакальские рудники», «Высокогорский ГОК», Богословское и Гороблагодатское рудоуправления, в Западной Сибири (44,5 %) ООО «КузГОК» (в составе Таштагольского и Казского рудников), Абаканское и Шерегешское рудоуправления.
Предприятия Западной Сибири и Урала добывают в основном магнетитовые руды с примесью гематита и сидериты (Бакальские рудники) с содержанием железа в Западной Сибири от 35 % до 49 %, на Урале от 32 до 46 %. В центре России разрабатываются железистые кварциты с качеством 3234 %.
Месторождения железных руд по геологическим условиям относятся в основном ко 2-й группе сложности. Таштагольское в Горной Шории отнесено к удароопасным, а Абаканское, Естюнинское, Песчанское, Высокогорское, Гороблагодатское, Шерегешское и Казское склонны к горным ударам. Глубина разработки от 325 до 900 м. Общие балансовые запасы месторождений, разрабатываемых подземным способом, составляют на 1 января 2003 года 800 млн т.
Основная особенность месторождений России в сопоставлении с дальним зарубежьем низкое качество руд, большая глубина горных работ и достаточно сложные горно-геологические условия. На предприятиях ОАО «Рудпром» разработка производится в основном системами этажно-камерной, принудительного подэтажного и этажного обрушения. В 2002 году подземным способом добыто 17925,5 тыс. т железной руды со средневзвешенным качеством 30,8 %.
В годы реформ на подземных предприятиях России произошел резкий спад производства: в 1998 году добыча составила лишь 46,7 % уровня 1990 года (рис. 1). Падение объясняется двумя взаимосвязанными причинами снижением спроса на сырье и объемов инвестиций в воспроизводство рудных мощностей. После 1998 года спрос стал расти, что позволило поднять добычу, выйдя на предельные возможности предприятий. Дальнейший рост производства может быть обеспечен только за счет повышения объемов подготовки новых запасов к отработке. В определенной мере такую подготовку можно количественно выразить изменением объемов капитальных и подготовительных работ (КПР) в шахтах.
Анализ показывает, что снижение объемов КПР с 1990 года по 2002 год вызывает адекватное падение объемов добычи на подземных предприятиях (рис. 1). Ясно, что это может происходить лишь до тех пор, пока позволяют экономические условия, а они на самом низком уровне. Средняя рентабельность подземной добычи в ОАО «Рудпром» в 2002 году не превысила 2 %. Иначе говоря, при существующей технологии и организации ведения горных работ предприятия достигли предельных возможностей. Из анализа также следует, что изменения объемов КПР, в свою очередь, определяются в основном объемами инвестиций в воспроизводство мощностей предприятий (рис. 2). Технология добычи руды в рассматриваемый период не менялась, значит, основная часть инвестиций шла на КПР для поддержания производственных мощностей: снижались капиталовложения уменьшались объемы КПР, сужался очистной фронт в шахтах и соответственно падала добыча.
Этот анализ лишний раз подтвердил, что горное производство требует постоянного вложения денежных средств. При этом, в отличие от других производств, несвоевременное инвестирование может привести к необратимым последствиям, когда никакие деньги уже не смогут восстановить утраченную мощность предприятия.
К сожалению, подземная добыча железной руды не вызывает сегодня инвестиционного интереса, поскольку ее себестоимость, за редким исключением, в 24 раза выше, чем при добыче открытым способом. Так останется до тех пор, пока не будут повышены экологические платы и налоги на землепользование. Сегодняшний инвестор нацелен только на кредиты с окупаемостью не более 34 лет, что для шахт во многих случаях нереально. Сложность ситуации усугубляется тем, что основная часть предприятий в период реформ оказалась в стадии реконструкции, которая из-за недостатка средств затянулась до настоящего времени. Особенно ярко это проявилось на рудниках Западной Сибири. Кроме того, нынешняя налоговая политика в стране не способствует разработке месторождений в сложных горно-геологических условиях, что также является существенным тормозом в инвестировании воспроизводства мощностей подземных предприятий.
Их собственники сегодня озабочены реконструкцией металлургических производств, так как они дают конечную продукцию. Считается, что подъем сырьевой базы станет возможным после обновления этих предприятий, когда начнется возврат вложенных в них средств. Потому прибыль тех горных предприятий, где собственниками являются металлурги, также направляется на реконструкцию металлургических производств. А на подземных предприятиях основными инвестиционными источниками, за редким исключением, являются амортизационные отчисления, направляемые на строительство. В ближайшем будущем не приходится рассчитывать на существенные внешние вложения в подземную добычу железной руды.
При таком раскладе какой может быть перспектива, скажем, к 2010 году? В целом по подземным предприятиям ОАО «Рудпром», по самым оптимистичным прогнозам, можно ожидать в 2010 году по добыче сырой руды и производству концентрата выход на уровень 19941995 годов. В этом прогнозе предусмотрен ввод в эксплуатацию долго строящихся предприятий. Это касается, в частности, ОАО «Яковлевский рудник», где шахта строится с 1974 года, и ОАО «Краснокаменское рудоуправление», в котором шахта «Одиночная» сооружается с 1981 года. Оптимизм еще и в том, что некоторые предприятия смогут довольно длительное время существовать с предельно низкими объемами производства.
В условиях дефицита денежных средств на поддержание мощностей важно, как никогда, сконцентрировать усилия на сокращении производственных расходов, снижении себестоимости продукции, жесткой экономии на всех переделах. Основным направлением этой работы является технический прогресс, обеспечивающий снижение расходных коэффициентов на всех процессах производства, оптимизацию численности трудящихся, повышение качества продукции, улучшение показателей извлечения железа при добыче и переработке руды. Только такой подход позволит предприятию осуществлять внутренние инвестиции в воспроизводство своей мощности.
Это актуально еще и потому, что многие эксплуатационные показатели предприятий за последние 1012 лет заметно ухудшились. Так, годовая производительность одного работающего на добыче сырой руды снизилась в 2 раза, на производстве товарной руды в 1,5 раза, на проходке выработок в 1,2 раза. Удельный расход взрывчатых веществ (ВВ) на тонну добычи повысился в 1,2 раза, удельный показатель горно-подготовительных выработок вырос почти в 1,3 раза, выход товарного продукта из добытой руды снизился почти на 1,5 %, а засорение добытой руды на некоторых предприятиях достигло 4243 %.
А ведь известно: рост засорения на 1 % приводит к снижению себестоимости добычи руды также в среднем на 1 %.
Тем не менее повсеместного технического прогресса на предприятиях не наблюдается. В какой-то мере это объясняется отсутствием средств для начальных вложений в разработку и приобретение новых техники и технологии. Но только в какой-то мере, ведь опыт работы отдельных предприятий показывает, что даже в этих условиях прогресс не только возможен, но и приносит существенные результаты. Так, в ОАО «Комбинат «КМАруда» активно занимаются внедрением новых конструкций перфораторов, бурильных установок, бурстанков, ВМ, бурстали, разрабатывают технологию складирования хвостов обогащения в очистных выработках. Вместе с использованием организационных мер, технические новшества позволили улучшить показатели работы комбината. В 2002 году производительность труда на шахте выросла по сравнению с 1998 годом в 1,22 раза, на ДОФ в 1,16 раза. Удельный расход буровых коронок для скважин диаметром 105 мм снизился в 2,37 раза, для шпуров в 1,45 раза, расход бурстали в 3,94 раза, электроэнергии в целом по комбинату в 1,4 раза, теплоэнергии в 1,12 раза. Все это позволило «КМАруде» улучшить экономическое положение.
В акционерном обществе «Шерегешское рудоуправление» на ДОФ построен новый тракт для дообогащения хвостов старых отвалов, что позволяет получать дополнительный, более дешевый концентрат и повысить использование мощности фабрики. В ОАО «Богословское рудоуправление» занимаются наладкой системы предварительного нагрева с помощью пара подаваемого в шахту воздуха, что значительно сократит затраты на электроэнергию.
Все это лишний раз доказывает: в любых условиях можно и нужно использовать на предприятиях возможности технического прогресса. Для специалистов здесь обширное поле деятельности, которое практически остается нетронутым.
Есть смысл обозначить некоторые направления совершенствования технологии, повышающие экономическую эффективность разработки месторождений. Например, около 80 % железной руды на подземных предприятиях добывается системами этажного принудительного обрушения, которое осуществляется с использованием ВВ. Суммарная масса зарядов достигает 700 т. При массовых взрывах обрушается до 1 млн т руды, которая выпускается затем в течение нескольких месяцев. Такая технология применяется повсеместно. Но она имеет ряд недостатков, повышающих себестоимость добычи. Нужно много времени для подготовки блока к обрушению, что увеличивает затраты на поддержание нарезных выработок. При взрыве больших зарядов происходят значительные законтурные нарушения прилегающего к блоку массива и выработок в нем, что удорожает работы по подготовке следующего блока. При массовых взрывах происходят нарушения выработок днища блока, что требует значительного объема восстановительных работ с остановкой выпуска руды. При зарядке скважин все работы в блоке останавливаются почти на неделю, на нее отвлекается большое число рабочих. В связи со сравнительно длительным периодом выпуска руды из обрушенного блока происходит замораживание затраченных средств. При наличии в массиве влаги и глинистых включений идет переуплотнение обрушенной массы и намного осложняется ее выпуск из блока.
Словом, пора совершенствовать технологию. Сам собой напрашивается переход на послойное обрушение и выпуск руды из блока. Это потребует четкой организации и увязки всех работ в блоке, но исключит приведенные выше отрицательные факторы. Послойное обрушение может иметь разные модификации в зависимости от горно-геологических условий. Например, в Канаде, Австралии и Китае широко применяют технологию Vertiсal Retreat Mining (VRM). Суть ее в последовательной отбойке горизонтальных слоев руды секционным взрыванием вертикальных скважин большого диаметра до 160170 мм. Опыт работы участка самоходной техники в Богословском рудоуправлении показывает, что применение в одинаковых условиях систем принудительного этажного обрушения с массовой отбойкой руды, выпускаемой через днище блоков, и подэтажного обрушения с послойной отбойкой и торцевым выпуском позволяет во втором случае снизить трудоемкость технологических процессов в 1,47 раза, себестоимость в 1,26 раза, а производительность труда повысить в 1,57 раза. Так что гигантизм взрывов, отбойка большого количества руды должны по возможности уступить место планомерной, четко организованной технологии с порционной отбойкой серией мелких взрывов.
Далее: применение, например, эмульсионных ВВ для зарядки скважин в карьерах позволило в 23 раза сократить расходы на взрывных работах, повысить безопасность перевозки и заряжания таких материалов. Эта проблема на подземных предприятиях не менее актуальна, чем на открытых, и требует активной проработки.
Исследованиями, проведенными в свое время на железорудных шахтах в Кривбассе, установлено, что наибольшее влияние на производительность труда рабочего в целом по шахте оказывает не столько процесс отбойки и доставки руды, сколько ее перемещение от выемочных участков на поверхность. Если учесть, что транспортные схемы на железорудных шахтах остаются практически без изменения со времени появления локомотивной откатки (изменениям подверглась лишь грузоподъемность составов), то совершенствование технологии перемещения рудной массы также является существенным внутренним резервом предприятия.
При этом необходимо отметить, что еще в конце 80-х годов на рудниках Западной Сибири были отработаны основные элементы циклично-поточной технологии (ЦПТ) доставки руды в блоке и перемещения ее в шахте. Созданы и апробированы конвейер на скользящей ленте, телеуправление процессом выпуска и доставки руды в блоке, устройства, сопрягающие вибропитатель с конвейером и конвейер с рудоспуском. Институтом «ВостНИГРИ» разработана мобильная участковая дробилка, располагающаяся в рудоспуске. В свое время выполнялся проект на опытно-промышленный участок с ЦПТ для ОАО «Казский рудник», но с началом перестройки работы были остановлены.
Расчеты показывают, что внедрение циклично-поточной технологии в шахтах с объемом добычи 2 и более млн т сырой руды в год позволяет сократить эксплуатационные затраты на выпуске и транспорте руды в 2,53 раза. Это подтверждает и опыт применения ЦПТ за рубежом.
Для разработки подземных зарядных комплексов эмульсионных ВВ и ЦПТ перемещения руды в шахтах целесообразно объединение усилий нескольких предприятий хотя бы в рамках одного собственника с выработкой единой программы работ, что позволит снизить финансовую нагрузку на отдельное предприятие.
Перечисленные выше направления совершенствования технологии подземных работ на железорудных предприятиях не исчерпывают все многообразие направлений технического прогресса и приведены лишь в качестве примеров, указывающих на наличие у предприятий внутренних ресурсов, использование которых поможет им улучшить экономическое положение.
В качестве подтверждения этому можно привести опыт канадской компании INCO. В свое время в результате резкого падения цен на никель фирма была вынуждена искать пути снижения себестоимости добычи руды. Для этого INCO полностью модернизировала технологию добычи руды, ввела неординарные новшества и добилась существенного роста производительности труда и прибыли. За 5 лет модернизации производительность труда на рудниках увеличилась в среднем на 87 %. Такие результаты получены благодаря внедрению эффективных технологий отработки блоков VRM и VGR (Vertical Grater Retreat) и поточной технологии перемещения рудной массы с использованием погрузчиков непрерывного действия, самоходной участковой дробилки, системы конвейеров.
Подведем итоги. Инвестиционный климат в стране складывается не в пользу шахтной разработки. Подземные предприятия в подавляющем большинстве резко снизили объемы производства. Сегодня наметился процесс стабилизации производства на новом, зачастую более низком уровне, что позволяет предприятиям работать без внешних инвестиций на предельных возможностях. В перспективе при неизменной налоговой и инвестиционной политике рост объемов подземной добычи железной руды окажется незначительным, а существование многих предприятий будет зависеть от их способности максимально использовать внутренние резервы. Основную ставку необходимо сделать на реализацию мер технического прогресса, объединение усилий предприятий для совершенствования технологии разработки месторождений, что позволит изыскать денежные средства для начальных инвестиций в создание и приобретение новых техники и технологии. Опыт отечественных и зарубежных предприятий показывает, что такое совершенствование может существенно укрепить экономическое положение предприятий, обеспечить увеличение объемов финансирования воспроизводства производственных мощностей и рост конкурентоспособности предприятий.
|
|
|
|
|
текущий номер

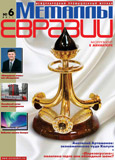
предыдущий номер

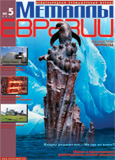
|
|