|
|
Журнал |
|
Архив |
|
Подписка |
|
Реклама |
|
САММИТ |
|
Книжная полка |
|
Контакты |
|
В начало |
|
|
|
| |
|
|
 |
№1' 2004 |
версия для печати
|
|
СИСТЕМНАЯ КООПЕРАЦИЯ |
НОВЫЕ ТЕХНОЛОГИИ УКРЕПЛЯЮТ РОЛЬ СТАЛИ В АВТОМОБИЛЕСТРОЕНИИ |
Юрий Адно
ИМЭМО РАН
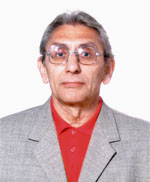 Юрий Адно |
|
огда около ста лет назад из ворот предприятия в Детройте выехал автомобиль марки «Форд-Т», это событие ознаменовало не только рождение одной из наиболее передовых отраслей промышленности ХХ века, но и явилось началом производства самого массового продукта современной цивилизации. Сегодняшний автомобиль динамично совершенствуется, отражая изменения общественных потребностей и развитие научно-технического прогресса. Обострение конкуренции в условиях растущей диверсификации и индивидуализации потребительского спроса, колоссальные масштабы производства и сбыта все это побуждает ведущие корпорации к постоянному обновлению моделей, совершенствованию конструкций, повышению безопасности, комфорта, экономичности автомобиля.
Очевидно, что выбор материалов и технологий их обработки относится к факторам, в значительной степени определяющим уровень конструктивных, эксплуатационных и потребительских параметров современной машины. Среди конструкционных материалов в автомобилестроении ведущее место принадлежит стали: в большинстве развитых стран эта отрасль, как правило, является главным потребителем стали во всем машиностроительном комплексе. В США, например, в 19701995 годах доля автомобильной промышленности в потреблении стальных полуфабрикатов выросла с 37 % до 43 %.
Однако в нынешних условиях сталь вынуждена уступать свои позиции основным конкурентам алюминию и пластмассам, использование которых в современном автомобиле, по многочисленным оценкам, непрерывно увеличивается (рис. 1). Этот рост можно рассматривать, в первую очередь, как развитие тенденции снижения металлоемкости и уменьшения массы в качестве одной из важнейших функциональных характеристик современной техники вообще и транспортных средств в особенности. Уменьшение массы, как правило, сопровождается ростом единичной мощности или грузоподъемности машины, что существенно повышает экономическую эффективность ее эксплуатации. Весьма важную роль при этом играет также фактор экономии топлива в связи с колебаниями цен на нефть и нефтепродукты, а также с возможностью резкого снижения экологически вредных атмосферных выбросов.
Что могла противопоставить черная металлургия столь весомым аргументам главных конкурентов, кроме своих традиционных преимуществ сравнительно низкой стоимости, доступности, высокой прочности, способности к утилизации?
Ответом на этот вопрос, по-видимому, можно считать своеобразный стратегический альянс ведущих сталепроизводящих компаний, которыми еще в 1994 году по инициативе Американского института черной металлургии (AISI) был создан международный консорциум для разработки нового облегченного стального кузова для легковых автомобилей. Очевидно, кузов избрали как наиболее объемную, металлоемкую часть автомобиля. Целью проекта ULSAB (Ultra Light Steel Auto Body), в котором были представлены интересы 35 компаний черной металлургии из 18 стран, стало снижение массы не менее чем на 25 % как минимум при равноценной экономичности, повышении жесткости конструкции и сохранении ее безопасности. Кроме того, новый кузов должен был иметь улучшенные конструктивные характеристики и легко вписываться в современное крупносерийное производство.
В проекте ULSAB участвовали специалисты металлургии и металловедения, автопромышленности, сборочно-монтажных работ. Иными словами, проект явился первой попыткой коллективного решения межотраслевой комплексной проблемы совместными усилиями производителей и потребителей металлопродукции. Опытно-конструкторские работы проводились на базе автомобильной фирмы Porche AG. В качестве объекта внедрения был выбран четырехдверный лимузин класса выше среднего на базе известных моделей компаний BMW, Ford, Mazda. Общий объем финансирования первого этапа работ составил 22 млн долл.
Осуществление проекта ULSAB развивалось по основным взаимосвязанным направлениям:
совершенствование применяемых и разработка новых сталей;
оптимизация технологии и элементов конструкции автомобиля.
Традиционный подход при выборе материалов кузова базируется на использовании современных высокопрочных сталей, позволяющих снижать толщину листа для конструктивных элементов. Эти стали, как правило, обладают также значительной энергоемкостью, что оказывает положительный эффект на противоударные характеристики, повышая безопасность пассажиров. Более 90 % оцинкованного стального листа толщиной 0,62 мм имеют предел текучести в диапазоне 210800 МПа. Основная проблема состояла в том, чтобы из этого многообразия выбрать те марки, которые оптимально сочетают высокую прочность с пластичностью, позволяющей получать необходимую толщину и конфигурацию конструктивных элементов методами формовки, глубокой вытяжки и сварки.
Этим требованиям отвечают, прежде всего, стали с упрочненной поверхностью, микролегированные, холоднокатаные двухфазные и так называемые TRIР-стали (transformation induced plasticity пластичность в результате превращения). Исследования компании Thyssen Krupp показали, что, изменяя содержание легирующих элементов (например, хрома и марганца), температурный режим прокатки, смотки в рулон и отжига с последующим горячим оцинкованием, можно варьировать структуру и свойства стали в довольно широких пределах. В частности, при этом достигается повышенная пластичность и технологическая деформируемость при стабильной прочности.
В современном автостроении исключительно важную роль играет обработка поверхности металлических деталей, большинство которых подвержено значительным поверхностным нагрузкам, в том числе коррозии, истиранию, механическим перегрузкам при циклических колебаниях. Поэтому в проекте ULSAB, кроме высокопрочных сталей, широко использовался принцип изготовления деталей из сравнительно дешевого материала (например, углеродистой стали) с необходимой обработкой или отделкой всей поверхности или наиболее нагруженного участка с помощью поверхностной закалки или нанесения коррозионно-стойкого покрытия. В настоящее время удельный вес деталей автомобиля с различными видами покрытий и упрочняющей поверхностной обработкой (оцинкование, никелирование, хромирование, алюмо-цинкование, азотирование и др.) превышает в среднем 80 %.
Интересное решение было найдено для изготовления гнезда запасного колеса и передней стенки кузова в виде стального сэндвич-листа, что позволило снизить массу этих деталей вдвое. Сэндвич-лист представляет собой два тонких стальных листа, склеенных полипропиленовой пленкой.
Технологическая часть проекта включала набор деформационных и сварочных технологий (рис. 2). Здесь применялись как традиционные методы пластической деформации, например, глубокая вытяжка, на долю которой приходится около 45 % всех операций по изготовлению кузова, так и новые, специально разработанные технологические приемы и агрегаты. Так, для изготовления бокового каркаса крыши корпуса сложной формы была успешно использована холодная деформация стальных тонкостенных труб высоким внутренним давлением в специальных штампах, что обеспечило высокую точность и чистоту поверхности. Сама крыша была изготовлена с помощью гидромеханической деформации высокопрочного (предел текучести 210 МПа) стального листа толщиной 0,7 мм.
Среди технологических разработок проекта ULSAB наиболее интересной является создание комплексной технологии изготовления тонких стальных листовых элементов с использованием лазерной сварки, получивших название tailored blanks. Это заготовки, сваренные при помощи лазерной сварки из предварительно раскроенных листов различной толщины и сталей разных марок, изготовленных по различной технологии. Например, можно получить плоскую заготовку, состоящую из мягкой горячеоцинкованной стали толщиной 1,5 мм, сваренную с холоднокатаным листом повышенной прочности толщиной 1 мм и горячекатаным листом толщиной 0,8 мм. Размер заготовки определяется габаритами конечной детали и возможностями формовочного агрегата, на котором будет штамповаться эта деталь. В современной практике, например, используется заготовка размерами 2 х 3,5 м.
В результате изготовления составного листа из элементов разной толщины появляется возможность регулирования технологических свойств листа и потребительских параметров детали автомобиля. В настоящее время крупносерийное производство сварных заготовок tailored blanks применяется для изготовления практически любых деталей кузова (рис. 3). При раскрое листов перед сваркой могут быть использованы заготовки любой формы, в том числе фасонные.
Лазерная сварка встык требует очень точной и чистой обрезки кромок листов, поэтому особое внимание уделяется конструкции и настройке обрезных прессов. За последнее десятилетие применение технологии tailored blanks и лазерной сварки на европейских автозаводах возросло в десятки раз, вытесняя традиционную роликовую электросварку (рис. 4).
Главными преимуществами заготовок tailored blanks является, прежде всего, снижение массы, сокращение затрат, стабилизация и повышение эксплуатационных характеристик конструкции, например, за счет жесткости. Разработанный в соответствии с проектом ULSAB, облегченный кузов на 50 % состоит из заготовок tailored blanks.
Реализация проекта позволила снизить массу кузова легкового автомобиля на 25 % по сравнению со стандартным образцом, причем без ущерба для механических и эксплуатационных характеристик. Эксплуатационные испытания и компьютерное моделирование аварийных ситуаций показали, что достигнутое увеличение жесткости на 80 % повышает защищенность пассажиров при ударных нагрузках. Кроме того, ультралегкий кузов при крупносерийном производстве оказывается дешевле не менее чем на 5 %. При этом для более полного использования новаторского потенциала применяемых материалов и технологий разработчики проекта предложили решение цельной конструктивной задачи, обеспечивающей комплексный подход к конструкции кузова в целом. Это позволило в процессе работы сократить почти на 20 % количество деталей кузова по сравнению со стандартным образцом. Благодаря этому уменьшается инструментальный парк и соответственно снижаются производственные затраты.
Первые итоги выполнения проекта ULSAB были подведены во время Женевского автосалона 1998 года и вызвали большой интерес всех автомобильных компаний. Практически сразу же было принято решение о создании проекта ULSAB-2 на базе малолитражных автомобилей. Заметно активизировались работы по созданию новых марок стали, режимов деформации и термообработки, исследований в области совершенствования технологии tailored blanks, в частности освоения лазерной сварки нелинейных швов, создания новых комбинированных конструкционных материалов типа сэндвич (сталь-пеноалюминий), рециклинга использованных кузовов ULSAB и т.д.
Успех проекта ULSAB способствовал также началу разработки в последние годы еще двух проектов ULSAC (Ultra Light Steel Auto Closures) и ULSAS (Ultra Light Steel Auto Suspension), относящихся, соответственно, к оптимизации внешних элементов кузова капота, крышки багажника, дверей и к технологии изготовления компонентов подвески колес. Интегрированным результатом всех этих разработок явилась опубликованная в 2002 году концепция «прогрессивного» автомобиля ULSAB-AVC, отвечающего новым, более жестким стандартам безопасности, экологии и экономичности. Реализация этой концепции предполагается на основе дальнейшего развития металловедческих и технологических инноваций, успешно апробированных в предыдущих модификациях проекта ULSAB.
По мнению большинства экспертов, в целом сталь сохраняет сегодня и, по крайней мере, не утратит в перспективе свои достаточно прочные позиции в одном из наиболее рыночных секторов промышленности. Залогом этого является переход черной металлургии от роли простого, традиционного поставщика конструкционных материалов к системному сотрудничеству с потребителями. При этом развитие индивидуализации спроса требует расширения поставок комплексных конструкций из сталей, ориентированных на эксплуатацию в конкретных условиях, с использованием облегченных элементов, максимально приближенных по свойствам и размерам к требованиям потребителя.
|
|
|
|
|
текущий номер

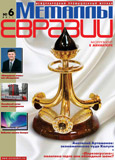
предыдущий номер

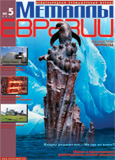
|
|