Евгений Зубицкий
Генеральный директор УК «Промышленно-металлургический холдинг»
Промышленно-металлургический холдинг вертикально интегрированная структура, объединяющая полтора десятка предприятий от добычи коксующегося угля до чугунного литья. Предприятия группы расположены в центральной полосе России и в Сибири. Это ОАО «Тулачермет» крупнейший в Европе экспортер чугуна, ОАО «Ванадий» крупнейший в России и один из самых крупных в мире производителей ванадиевой продукции, два угледобывающих предприятия на Кузбассе, ОАО «Кокс» коксохимзавод с тремя действующими батареями, Березовская обогатительная фабрика мощностью около 300 тыс. т угольного концентрата в месяц, ЗАО «Инертник» фабрика по производству инертной пыли, доломитовый карьер в Турдее, обеспечивающий стабильность поставок сырья для агломерации, завод котельно-вспомогательного оборудования в Советске (Тульская область), который используется в качестве ремонтного завода, карьерный участок Коксовый, две шахты, Сукремльский чугунолитейный завод, Рождественский карьер в Тульской области. Промышленно-металлургический холдинг является управляющей компанией. Все предприятия группы успешно развиваются. На них трудится около 15 тыс. человек.
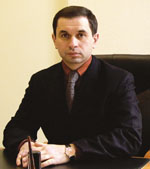 Евгений Зубицкий |
|
собенностью формирования холдинга можно считать приобретение проблемных предприятий угольной и металлургической отраслей. Мы брали предприятия, близкие к банкротству, и выступали, по сути, в роли антикризисных управляющих. Сначала это был кемеровский «Кокс» и другие сибирские предприятия, потом «Тулачермет» и предприятия соответствующего региона. Постепенно выстраивалась технологическая цепочка: уголь концентрат кокс чугун, что и дает сегодня определенную сырьевую независимость.
Несмотря на географическую разницу, проблемы оказались одни и те же чрезвычайно изношенные основные фонды, в модернизацию и реконструкцию которых средства не вкладывались с социалистических времен, раздутый штат, отсутствие вменяемой маркетинговой политики, фирмы-посредники, съедающие прибыль, неправильный бухгалтерский учет, устаревшие технологии, а главное отсутствие единой стратегии развития, прогнозирования на несколько лет вперед.
Наиболее показателен пример ОАО «Тулачермет» (ранее Новотульский металлургический завод), самого крупного предприятия холдинга. Завод основан в 1931 году, а в 1935 году, когда была задута первая доменная печь, пущен в эксплуатацию. С середины 50-х годов предприятие стало испытательной площадкой отработки новых технологий в металлургии. Создание машины непрерывного литья заготовок, разработка высокоэффективных упрочненных строительных сталей, синтетических литейных чугунов и другие инновации отмечены высшими наградами Родины Ленинской и Государственной премиями, переходящим Красным знаменем. В октябре 1959 года на базе завода был создан филиал ЦНИИчермет им. Бардина, а в 1973 году создано Научно-производственное объединение «Тулачермет». К тому времени предприятие имело в своем составе три доменных печи, одна из которых была на тот момент крупнейшей в СССР. Еще в 1952 году пущен в эксплуатацию цех по производству железных порошков, с 1961 года на предприятии началось промышленное производство хрома, а с 1974 года феррованадия.
В 90-е годы после поспешного акционирования уникальный научно-производственный комплекс «Тулачермет» фактически был разрушен. В течение десятилетия завод потерял наиболее рентабельные производства цеха по переработке хрома и феррованадия и превратился в группу формально независимых предприятий. Полная децентрализация привела к тому, что при сохранении единой инженерной инфраструктуры какая-либо координация в финансовой, маркетинговой и производственной политике и контроль над цехами отсутствовали как таковые. Неудачные попытки диверсификации бизнеса с ориентацией на выпуск товаров народного потребления привели к полному развалу технического комплекса. Отток капитала в производство кроссовок, пылесосов и телевизоров низкого качества проводился за счет вложений в основное производство. В результате к концу 2000 года предприятие фактически подошло банкротом. 1 млрд 300 тыс. рублей убытка, производство, едва превышавшее 1,5 млн т чугуна в год, скудная налогооблагаемая база и низкая заработная плата (на уровне 3 тыс. рублей) со всей очевидностью свидетельствовали о том, что завод находится на грани остановки и полного прекращения деятельности.
В таком вот плачевном состоянии предприятие, некогда считавшееся жемчужиной советской металлургии, досталось промышленной группе «Кокс», чья команда на тот момент уже обладала обширным опытом вывода промышленных предприятий из кризиса.
Надо отметить, что помимо решения проблем, накопившихся в «Тулачермете», кемеровчане не забывали и о развитии собственного производства. В мае 2001 года была введена в эксплуатацию новая коксовая батарея. Ее строительство стало крупнейшим инвестиционным проектом, реализованным в ОАО «Кокс» в его новейшей истории. Стоимость строительства составила почти 0,5 млрд рублей. Батарею построили за два года, если считать подготовительный период, а на собственно кладку и монтаж ушло 10 месяцев. За последние годы в ОАО «Кокс» выполнен ряд крупных работ, повысивших эффективность производства и экологическую безопасность сложных технологических процессов. По оценкам зарубежных специалистов, завод «Кокс» на сегодняшний день является одним из лучших и по технологии, и по экологии, и по уровню эксплуатации и надежности основных агрегатов, степени автоматизированного и компьютерного оснащения, контроля за производственными процессами.
Параллельно шло укрепление собственной сырьевой базы. Выведена из банкротства обогатительная фабрика в г. Березовский, на карьерном участке «Коксовый» в г. Киселевске ведется добыча коксующегося угля открытым способом. Строится шахта «Романовская» в Березовском с проектной производительностью в 1 млн т коксующегося угля в год, начаты работы на шахте «Владимирская».
Аналогичная схема возрождения производства была применена и в Туле, где результаты тоже не заставили себя ждать. Улучшение производственных показателей и значительная работа по снижению расходных коэффициентов позволили вывести предприятие на уровень безубыточности, а затем получить в 2001 году прибыль от реализации товарной продукции в 389 млн рублей. В 2002 году прибыль удвоилась, а в 2003 году, по самым осторожным прогнозам, она составит почти 1,5 млрд рублей.
Удовлетворительные финансовые показатели позволили рассчитаться с накопленными в предыдущие годы долгами, погасив более чем миллиардный непокрытый убыток и вдвое снизив кредиторскую задолженность. При этом «Тулачермет» за 2,5 года хозяйствования в новых условиях превратилась в одного из крупнейших налогоплательщиков Тулы и области. За тот же период увеличение заработной платы составило 200 %, существенно опередив рост инфляции в стране. Сейчас зарплата в ОАО «Тулачермет» одна из самых высоких в регионе и отрасли.
В 2002 году на «Тулачермете» удалось поставить сразу несколько рекордов месячной выплавки чугуна, отремонтировать градирни и первую доменную печь, сделать прекрасную подъездную дорогу, приобрести несколько десятков квартир для очередников, построить и ввести в эксплуатацию новый котел высокого давления.
Все это время особое внимание уделяется вопросам ремонтов и модернизации оборудования. Утвержденная Программа технического развития, рассчитанная на срок от 3 до 5 лет, должна привести к тому, что область получит предприятие, соответствующее европейским экологическим стандартам в металлургии. Освоение следующего передела дело ближайшего будущего, но серьезная проработка этого направления идет уже сегодня.
При проведении модернизации наибольшее внимание уделяется экологической составляющей. Значительные финансовые вложения и серьезный комплекс мероприятий позволили значительно снизить техногенное воздействие на окружающую среду. Так, резко уменьшился валовой выброс вредных веществ в атмосферу, сократился объем сточных вод в реку Упа, снизилось образование промышленных отходов. На предприятии уже решены вопросы переработки и утилизации доменного шлака, открыто новое производство цех металлургических брикетов и бетонов, реализующий идею рециклинга металлургических отходов.
Самый заметный показатель объемы основного производства. Если в 2000 году среднемесячный выпуск чугуна, доля которого 95 % в общем объеме производства, составлял 160180 тыс. т, то сейчас и 250 тыс. т не предел. Значительный рост производства, достигнутый в ОАО «Тулачермет», обусловил его попадание в первую сотню самого престижного отечественного рейтинга крупнейших предприятий страны «Эксперт 200». А по оценке экспертов центра AK&M, оно входит в число ста предприятий, имеющих наибольший вес в российской экономике.
Мы ожидаем, что в сравнении с 2002 годом основные производственные показатели по итогам 2003 года не изменятся, составив примерно 2,5 млн т чугуна, и это при том, что в течение 3 месяцев печь с наибольшей производительностью стояла на капитальном ремонте первого разряда. С 2004 года будет серьезный подъем производства до 33,2 млн т в год.
Исходя из того, что ОАО «Тулачермет» является крупнейшим в мире производителем и поставщиком товарного чушкового чугуна, главной задачей для предприятия является увеличение производства чугуна до 300 тыс. т в месяц при надежной стабильной работе основных металлургических агрегатов.
Первым шагом в этом направлении стал уникальный ремонт комплекса ДП-3, начатый в июле и завершившийся в октябре 2003 года. Последний капитальный ремонт доменной печи № 3 проводился в 1980 году и не в полном объеме. Днище печи, первый пояс кожуха с холодильными плитами нижней лещади и футеровкой находились в эксплуатации с 1962 года.
Уникальность проведенного в 2003 году ремонта обусловлена, прежде всего, техническими решениями, заложенными в проект и определяющими новую печь как один из самых современных доменных агрегатов в Европе. При этом подготовленные ранее технические решения, предполагавшие традиционный ремонт, были пересмотрены специалистами предприятия.
Новый проект позволил решить целый ряд задач увеличение производства чугуна в печи до 1,6 млн т в год, повышение производительности труда и надежности работы оборудования, рост прибыли и повышение социальной защищенности трудящихся, улучшение условий труда персонала и экологической обстановки в Туле. Главным проектировщиком был выбран московский «Гипромез».
Впервые за всю историю предприятия вместе с доменной печью ремонтировалось и модернизировалось 30 других объектов. Суммарные капитальные вложения составили более 1 млрд рублей.
В числе инновационных технических решений, примененных в ходе реконструкции ДП-3 и позволивших поднять производительность труда, увеличение объема свободно стоящей безмараторной печи до 2200 м3 за счет использования бетонной футеровки шахты. Установка 24 вместо 20 воздушных фурм повысила интенсивность процесса доменной плавки.
До ремонта в системе охлаждения печи использовалась вода, циркулирующая в открытом оборотном цикле с охлаждением в башенных градирнях. Такая схема приводила к образованию железо-карбонатных отложений на внутренних стенках труб змеевиков холодильных плит, и, как следствие, к уменьшению теплоотвода с преждевременным прогаром холодильника. Новая система охлаждения печи химочищенной водой с использованием холодильных плит усовершенствованной конструкции из высокопрочного чугуна с шаровидным графитом в экстремально напряженных зонах печи, как и использование микропористых углеродистых блоков андалузитовых изделий для футеровки горна, даст возможность значительно увеличить межремонтный период. Все это продлит кампанию печи до 1012 лет против шести на печах традиционной конструкции.
Существовавшая конструкция площадки для обслуживания фурменных приборов была не замкнута по окружности и имела разрыв в районе чугунных леток, что не позволяло персоналу осуществлять постоянный контроль за работой фурменных приборов и усложняло работы по замене фурм. Установленная кольцевая площадка сделала удобным обслуживание приборов фурменной зоны и позволяет использовать малогабаритную напольную машину для замены элементов фурменного прибора.
Требования безопасной эксплуатации на новой печи обеспечивает АСУ ТП системы разгара горна, лещади, системы подготовки и анализа проб колошникового и радиального газов.
Важным элементом капитального ремонта доменной печи № 3 стала модернизация литейного двора. Реконструированный литейный двор имеет рабочую горизонтальную площадку. Конструкционные особенности таковы, что верх полностью укрытых главных и транспортных желобов чугуна и шлака расположен на одном уровне с верхним уровнем пола литейного двора, что обеспечивает движение вспомогательных механизмов по площадке и практически полностью исключает выброс пыли.
Применение главных чугунных желобов типа Pooling с использованием качественных жаростойких бетонов увеличивает срок службы футеровки желобов на 220 тыс. т разливаемого чугуна с возможностью проводить ремонт в рамках планово-предупредительных ремонтов с шестинедельными циклами. Кроме того, применение бетонов в 5 раз уменьшит количество отходов от отработанных масс.
На литейном дворе установлен современный комплекс гидравлических машин для вскрытия и закрытия чугунных леток, гидроманипулятор для съема укрытий главных чугунных желобов. В целом модернизация литейного двора позволила значительно улучшить условия труда персонала, обслуживающего доменную печь № 3, и ликвидировать выбросы пыли при выпуске чугуна.
Проведен капитальный ремонт системы аспирации, системы подачи сырья и топлива ДП-3 на шихтоподаче. Физически и морально устаревшие очистные аппараты заменены на современные установки типа КМП, что в 5 раз уменьшает выбросы пыли в атмосферу.
Для обеспечения объектов ДП-3 построена центральная приточная станция, сооружение которой было заморожено на 12 лет еще в 90-е годы. Сейчас ЦПС успешно обеспечивает нормальные условия труда и воздушный баланс за счет снабжения очищенным и подогретым воздухом рабочих мест на литейном дворе, шихтоподаче, на пультах управления доменной печи, а также воздушный баланс систем аспирации шихтоподачи и литейного двора.
Одной из главных специфических особенностей проведенного ремонта стали короткие сроки. Работы по реконструкции третьей доменной печи ОАО «Тулачермет» проведены всего за 90 суток. Ни перед одним из российских предприятий, проводивших капремонты в течение последних пяти лет, не стояла задача уложиться в столь жесткий временной лимит, поскольку все они имели избыточные производственные мощности. На капремонте ДП-3 были задействованы 34 подрядные организации из России, Украины, Белоруссии и Казахстана. Около 3 тыс. человек работало на объектах круглосуточно по 12-часовому графику, что позволило свести к минимуму потери рабочего времени. В общей же сложности выполнением заказов для капремонта ДП-3 было занято более 7 тыс. специалистов из России, Словакии, Германии, Украины и Белоруссии. Не менее широка и география поставок оборудования и металлоконструкций.
Осуществленная реконструкция третьей доменной печи один из очередных этапов пятилетней Программы развития ОАО «Тулачермет» на 20032008 годы. Он включает в себя несколько основных направлений, в числе которых развитие производства чугуна, строительство новой аглофабрики, ряд экологических проектов и многое другое. Общие затраты на внедрение мероприятий составляют 147,2 млн долл. В итоге город и область получили динамично развивающееся, экономически устойчивое и экологически безопасное производство, в эффективной работе которого заинтересованы в конечном итоге все жители.
Таким образом, у ОАО «Тулачермет» появилась реальная возможность не просто восстановить промышленный потенциал, но и вернуть себе славу флагмана отечественной металлургии.
|