|
|
Журнал |
|
Архив |
|
Подписка |
|
Реклама |
|
САММИТ |
|
Книжная полка |
|
Контакты |
|
В начало |
|
|
|
| |
|
|
 |
№6' 2003 |
версия для печати
|
|
БОЛЬШЕ ПРОДУКЦИИ, МЕНЬШЕ ЗАТРАТ |
О РЕСУРСОСБЕРЕГАЮЩЕЙ ПОЛИТИКЕ НА БОГОСЛОВСКОМ АЛЮМИНИЕВОМ ЗАВОДЕ |
Евгений Липухин
Заместитель генерального директора Богословского алюминиевого завода филиала ОАО «СУАЛ»
роизводство алюминия один из самых энергоемких процессов. Вопросы эффективного использования топливно-энергетических и материальных ресурсов в развитии предприятия всегда стояли на первом плане. Сегодняшний день ставит в этом вопросе еще более жесткие требования.
Постоянное повышение цен на энергоносители, приближающие их к уровню мировых, приводит к росту как доли энергетических затрат во всех отраслях региональной экономики, так и абсолютной величины этих затрат. Указанной тенденции необходимо противопоставить и последовательно осуществлять энергосберегающую политику, обеспечивающую систематическое снижение энергоемкости производства, являющейся одним из основных показателей, определяющих себестоимость продукции. Данные о структуре себестоимости основных ее видов на Богословском алюминиевом заводе приведены в таблицах 1 и 2.
Как видно из таблиц, основными при производстве алюминия и глинозема являются сырьевые и энергетические затраты. Именно поэтому актуальной задачей современного этапа развития завода является разработка ресурсо- и энергосберегающих технологий, направленных на экономию сырья и тепловых ресурсов и получение дополнительной прибыли.
План технического развития БАЗ-СУАЛ включает в себя мероприятия по реконструкции и модернизации действующего оборудования, совершенствованию технологических процессов, капитальному строительству, улучшению экологического состояния окружающей среды.
Для решения задач энергосбережения разработана комплексная система. Основным направлением действий в глиноземном производстве является снижение расхода тепловой энергии в основных потребляющих тепло переделах: на выпарке и автоклавном выщелачивании.
Работы по снижению расхода пара на выпарке ведутся по двум направлениям:
по снижению удельного расхода пара на 1 т выпаренной воды, что зависит от кратности использования пара с ТЭЦ и конструкции используемого оборудования;
по снижению количества упариваемой воды на 1 т глинозема, что зависит от технологических показателей каждого передела глиноземного цеха.
Мероприятия, внедряемые на автоклавном выщелачивании боксита, направлены на снижение расхода пара и повышение химического извлечения глинозема из боксита.
Внедрение комбинированной схемы нагрева сырой пульпы позволило повысить ее температуру после подогревателей на 810 оС и тем самым сократить удельный расход пара на 1215 %.
Внедрение автоматизированной системы управления технологическими процессами (АСУТП) на участках выщелачивания привело к стабилизации температурного режима в автоклавных батареях. В результате удалось увеличить химическое извлечение Al2O3 из боксита на 0,5 %, что привело к снижению его удельного расхода (рис. 1).
На участках выпарки проводится перевод выпарных батарей на 4-кратное использование пара, а также реконструкция выпарных аппаратов на аппараты с «вынесенной зоной кипения». Как видно из графиков (рис. 2, 3), несмотря на все проводимые мероприятия, произошло незначительное увеличение расходных коэффициентов по электрической и тепловой энергии. Это обусловлено дополнительными затратами, связанными с реализацией мероприятий по «укрупнению» глинозема. Благодаря этим мерам удалось снизить содержание фракции 45 мкм в глиноземе на 11,8 % по сравнению с 1997 годом (рис. 4).
Реконструкция печей кальцинации с заменой холодильников вращения на холодильники кипящего слоя привела к следующим результатам:
к снижению удельного расхода газа на 11,1 % (рис. 5);
к снижению расхода охлаждающей воды на 65 %;
к сокращению расхода сжатого воздуха на переделе кальцинации на 35,7 % (рис. 6).
Реализация мероприятий технического развития в глиноземном цехе позволила увеличить производство глинозема по сравнению с 1997 годом на 16,3 %, а потребление энергетических ресурсов лишь на 8 % (рис. 7). При этом снижен удельный расход тепловой энергии на 7,9 %, а удельный расход электрической энергии на 3,7 %.
Для сбережения топливно-энергетических ресурсов в электролизном производстве с учетом опыта отечественных и зарубежных заводов были внесены коренные изменения в сам процесс электролиза, в первую очередь, в технологические параметры, такие, как состав и уровень электролита, уровень металла и сила тока. Проведена большая работа по улучшению технологической дисциплины и повышению квалификации ИТР и рабочих.
Внедрены новые системы автоматизации процесса АСУ ТП «Электра-160» и АСУ «Ток серии» с системой измерения тока по принципу Холла. Действующие сегодня системы автоматизации позволяют решать целый ряд технологических задач, основными из которых являются:
четкое выдерживание заданного напряжения на каждом электролизере;
раннее обнаружение отклонений от заданных технологических параметров и возможность принятия мер по их своевременному предотвращению.
Одним из основных параметров, влияющих на производительность серии, является величина тока серии и его стабильность. Наличие системы стабилизации тока позволяет исключить скачки силы тока во время анодных эффектов.
Снижению расходных коэффициентов в электролизном производстве, таких, как удельный расход глинозема, расходы электроэнергии, фторида алюминия, криолита, способствует получение «укрупненного» глинозема. Также при получении алюминия из «укрупненного» глинозема увеличивается выход по току.
За счет всех выполненных мероприятий в 2002 году по сравнению с 1997 годом в электролизном цехе удалось снизить удельные расходы:
глинозема с 1945 до 1930,4 кг/т, или на 0,76 % (рис. 8);
анодной массы с 560,8 до 480,5 кг/т, или на 16,7 % (рис. 9);
технологической электроэнергии с 15364,9 до 14848,5 кВт . ч/т, или на 3,5 % (рис. 10);
исключить из статей расхода чистый криолит и перейти на вторичный смешанный криолит (ВСК) и тем самым снизить себестоимость алюминия-сырца.
В электролизном цехе производство алюминия было увеличено по сравнению с 1997 годом на 22,9 %, а потребление энергетических ресурсов на 18,6 % (рис.11).
Комплекс мероприятий, реализованных на Богословском алюминиевом заводе, позволил добиться таких расходных коэффициентов, которые являются одними из лучших в отрасли.
Перспективным планом развития завода предусмотрена реконструкция корпусов электролиза и перевод их на электролизеры с обожженными анодами силой тока 300 кА. Это позволит сократить затраты на производство алюминия и значительно снизить выбросы вредных веществ в атмосферу.
Для дальнейшей модернизации глиноземного производства, предусматривающей увеличение химического извлечения глинозема из боксита и снижения энергозатрат, на заводе планируются следующие меры.
1. Реконструкция сгустителей и промывателей красного шлама из многоярусных в одноярусные с целью снижения расхода топливно-энергетических ресурсов (ТЭР) на 1015 % и снижения потерь щелочи с жидкой фазой отвального шлама на 34 %.
2. Реконструкция выпарных батарей с переводом на 5-кратное использование острого пара. Это позволит снизить его удельный расход на 10 %.
3. Проведение коренной реконструкции узла выщелачивания бокситов с переходом на высокотемпературное выщелачивание (260280 оС) с многократным самоиспарением автоклавной пульпы. Внедрение высокотемпературного выщелачивания обеспечивает увеличение химического извлечения Al2O3 из боксита и снижение удельного расхода боксита, а также создает условия для производства глинозема «песочного» типа. Внедрение многократного испарения автоклавной пульпы позволит значительно снизить энергозатраты на выщелачивание боксита.
4. Замена трубчатых вращающихся печей в цехе кальцинации на циклонно-вихревые. При этом снижение расхода топлива на переделе кальцинации составит около 50 %, истираемость глинозема снизится на 36 %, а содержание альфа-глинозема примерно на 30 %, что, в свою очередь, приведет к экономии сырья в электролизном производстве.
Все проводимые и планируемые мероприятия на Богословском алюминиевом заводе направлены на улучшение качества, снижение себестоимости продукции, снижение выбросов в атмосферу, улучшение экологической обстановки в регионе.
|
|
|
|
|
текущий номер

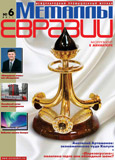
предыдущий номер

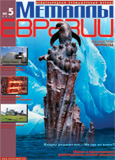
|
|