Конструкция электрических сталеплавильных печей продолжает совершенствоваться с точки зрения эффективности и управления. Недавние модели компаний иллюстрируют некоторые перспективные разработки.
Развитие конструкции современной дуговой электропечи приближается к тому, что изменения состава шихты и растущее использование углерода и топлива как частичного заменителя электроэнергии все больше увеличивают сложность, а следовательно, и повышают требования к управлению процессом плавки.
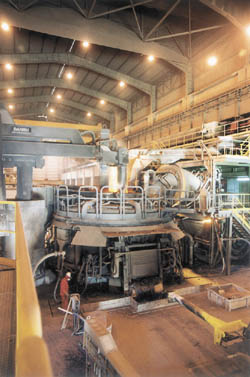 |
Завод SN Longos располагает системой управления, разработанной в соответствии с его техническими возможностями Предоставлено: Danieli |
Как сообщает итальянская фирма Danieli, новое плавильное производство на заводе сортового проката и стержней Siderurgica Nacional Productos Longos (город Сейксал, Португалия), которое было построено в мае и начало вводиться в эксплуатацию в августе, содержит последние достижения компании в ответ на подобные вызовы. Завод, по свидетельству фирмы, добивается хороших стабильных результатов.
Danieli поставила новую 120-тонную дуговую электропечь, новую ковшовую печь, новую установку по очистке газов и другое вспомогательное оборудование, олицетворяющее высокий технологический уровень. Например, дуговая электропечь снабжена системой Hireg регулировки электродов с встроенным анализатором и контролем за вспениванием шлака, модулями Danarc и анализом отходящих газов.
Обычно процесс в дуговой электропечи управлялся посредством статических профилей плавления с заданными параметрами и на основе данных, получаемых в ходе процесса. Но на самом деле процесс плавления очень динамичен и, учитывая этот факт, Danieli создала систему DanExpert EAF Suite. Эта система состоит из описываемых ниже модулей, каждый из которых может использоваться как отдельно, так и в качестве компонента интегрированной системы полного контроля за ходом процесса плавления.
Оптимизатор процесса. Он состоит из набора онлайн моделей для заданного развития процесса и динамичного управления плавкой в рамках конкретных задач по весу плавки на выпуске, продолжительности плавки от выпуска до выпуска, температуры плавки на выпуске и содержании углерода в плавке. Система основывается как на статическом, так и на динамическом равновесии по энергии и массе, обновляемых в соответствии с основными условиями процесса, которые регистрируются эксплуатационными приборами.
Модули контроля. Достигнутые заданные параметры плавки, затраченная энергия, минутный расход кислорода и скорость подачи материала контролируются по ходу процесса.
Анализатор процесса. Основывается на данных эксплуатационных приборов по нескольким нагревам. Дается оценка работы печи и оптимизируются ее параметры с тем, чтобы они соответствовали заданным характеристикам.
Цель всей системы состоит в том, чтобы обеспечить контроль над тремя основными переменными процесса:
динамический контроль дуги через стандартную цепь, основывающуюся на замере сопротивления;
динамический контроль за пенистым шлаком;
повышенный динамический контроль дуги на основе первых двух факторов.
Это становится возможным посредством оперативного получения и обработки информации о величине затрат, таких как электрический, химический и материальный балансы.
В результате, как заявляет Danieli, станет возможным определить две величины, которые более всего характерны для оптимальной работы печи: индекс стабильности дуги (ИСД) и индекс дугового покрытия (ИДП).
Ведя постоянный мониторинг и регулируя подобные параметры, можно будет обеспечить:
один из самых эффективных режимов плавки с точки зрения экономичности и потребления;
заданный вес плавки на выпуске, конкретно вес выпуска и зеркала расплавленного металла;
требуемую продолжительность плавки от выпуска до выпуска.
Рентабельность работы дуговой электропечи очень тесно связана с термической эффективностью используемых источников энергии. Полученный опыт используется затем для обеспечения полной оптимизации процесса с учетом всех заданных условий и имеющихся ограничений.
Плавильный завод SN Longos в Сейксале работает сейчас двенадцать часов в сутки в соответствии с программой компании по наращиванию производства. Постепенность наращивания производительности завода влияет на работу дуговой электропечи например, потребление кислорода в настоящее время удерживается на низком уровне (см. таблицу). На данном этапе ввода печи в эксплуатацию Danieli продолжает свое сотрудничество с SN Longos в вопросах оказания технологической помощи и обучения приемам эксплуатации для постоянного повышения производительности завода.

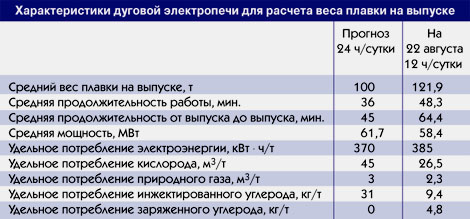
Переходя от кислородного конвертера к дуговой электропечи в Шаогуане
Как сообщают, несколько комбинатов рассматривают возможность вывода из эксплуатации одной или более доменных печей и перехода на производство стали в дуговой электропечи. Используя промышленный скрап в комбинации с 30 40 % жидкого металла, производители могут обеспечить такое же качество, которое давало производство в кислородном конвертере, считает итальянская компания Technint Technologies.
Непрерывная загрузка жидкого грунта и скрапа создает новые возможности для электросталеплавильных предприятий в плане сокращения расходов, повышения производительности и качества продукции. Примером служит завод по выпуску разнообразной продукции с объемом производства 2 млн. т в год, находящийся в Шаогуане, провинция Квандун (Китай).
Введенный в эксплуатацию в конце 2000 года, этот завод располагает 90-тонной дуговой электропечью, получающей скрап с помощью системы Consteel(r) компании Technint. Ее также можно загружать жидким чугуном при помощи 60-тонного ковша. Содержимого одного ковша обычно хватает на две плавки.
Чугун непрерывно подается по бортовой канаве с огнеупорной футеровкой во время плавки, для обеспечения надежной и безопасной работы скорость подачи регулируется автоматически.
Исходный наклон ковша производится вручную оператором дуговой электропечи, чтобы начать подачу жидкого металла в бортовую канаву. Чтобы обеспечить оптимальную скорость (быстрый наклон в первой фазе) и безопасность, оператору необходимо внимательно следить за начальной и самой сложной фазой заливки.
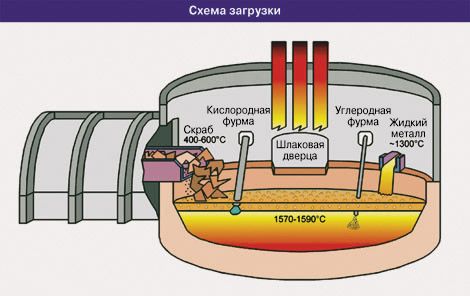
Точка загрузки жидкого металла находится на расстоянии от системы загрузки скрапа Consteel; это место расположено там же, где и кислородная фурма с водяным охлаждением (см. диаграмму). Кислородная фурма помогает увеличивать тепловую нагрузку и перемешивание в ванне жидкой стали на участке скрапа, повышая таким образом скорость плавления поступающего скрапа.
Этот тип конструкции делает возможным перерабатывать различные смеси: например, до 50 % жидкого металла поступает через систему Consteel, а остальные загрузочные материалы составляют твердые скрап, железо прямого восстановления (DRI), HBI или передельный чугун. Может использоваться и такой альтернативный вариант, когда твердый материал скрап, DRI, HBI или передельный чугун составляют все 100 %. Дуговая электропечь также приспособлена и для бадьевой загрузки.
С момента пуска дуговой электропечи завод в Шаогуане работает с полной нагрузкой, а поставленные цели были достигнуты уже через шесть месяцев, при среднем расходе электроэнергии 260 кВт . ч/т при использовании смеси с 30 % жидкого металла.
«Помимо отличных результатов в плане общего потребления электроэнергии, заявляет представитель Technint, стоит выделить низкое содержание азота в стали на выпуске, что позволяет получить высококачественный продукт. Сегодня завод работает стабильно, демонстрируя большой потенциал роста производства: 31 плавка в день уже считается китайским рекордом. В 90 с лишним процентах плавок с системой Consteel для загрузки используется жидкий металл.»
«По нынешней программе характеристики системы Consteel позволяют при использовании жидкого металла в дуговой электропечи избежать типичных связанных с этим проблем», указывает Techint.
Новая модель печи может работать со 100 %-ной загрузкой железа прямого восстановления
Несмотря на то, что продукты прямого восстановления известны уже давно, их использование в плавке всегда порождало проблемы для сталелитейщиков. Их доля в загрузках кислородного конвертера обычно ограничена 10 20 %. Применение железа прямого восстановления в индукционных электропечах в объеме более 70 % создает трудности из-за очень больших отходов шлака и высокого уровня потребления энергии. 100 %-ная загрузка продуктов прямого восстановления успешно практикуется в дуговых электропечах, но это означает высокие энергозатраты, что делает такой вариант экономически невыгодным.
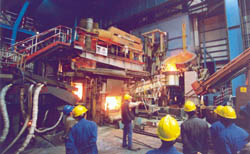 |
Участок выпуска и загрузки жидкого металла на заводе в Шаогуане Предоставлено: Techint |
Новая печная технология Contifur считается экономичной альтернативой, позволяющей использовать в загрузках до 100 % продукта прямого восстановления. Полное название технологии означает непрерывное литье в индукционных печах, а разработана она была компанией Electrotherm (Индия). Первая печь электрической мощностью в 4 МВт, работающая на технологии Contifur, была установлена на заводе Twenty First Century Wire Rods Ltd, в городе Силваса (Индия), и ее должны были ввести в эксплуатацию в прошлом месяце. Ее производственная мощность составляет 25 т, а выпуск равняется 10 т.
Индукционная печь с технологией Contifur канального типа имеет под и свод, шахту, панель управления питанием и индуктор.
Под печи представляет собой сборную конструкцию, футерованную огнеупорным кирпичом. Свод тоже стальной и футерован изоляционным материалом. Свод печи изолирует печную камеру, изоляция уменьшает просачивание воздуха и повышает эффективность. Шахта находится над сводом.
На поде постоянно находится ванна с жидким металлом. Жидкий металл нагревается индуктором, который находится внизу пода. Число блоков индуктора и подача электроэнергии определяются в зависимости от объема загрузки и желаемого объема производства. Каждый индуктор снабжен панелью управления питанием.
Смесь скрапа и железа прямого восстановления может быть любой пропорции. Она подается через шахту. Во время загрузки свод печи закрыт. Увеличение объема потребляемой энергии происходит одновременно с увеличением доли железа прямого восстановления в загрузке. При 100 %-ной загрузке железа прямого восстановления объем потребляемой энергии составляет 600 700 кВт . ч/т.
Скрап загружается из емкости для скрапа, а шнековый питатель может быть использован для загрузки продуктов прямого восстановления. Скрап предварительно подогревается в шахте горячими газами, а также от работающих на нефти горелок. Железо прямого восстановления добавляется без какого-либо предварительного подогрева, но в будущем это будет делаться с помощью дополнительного оборудования, которое находится сейчас в стадии разработки.
Кроме того, в печи можно эффективно перерабатывать ферросплавы, вторичную окалину, пыль и прочие отходы.
Специальная ненаклоняющаяся конструкция печи облегчает выпуск жидкого металла, не содержащего шлак. Постоянно действует зеркало металла, рассчитанное примерно на 10 15 т и выпуск около 10 т. Пробы берутся через специальный проем, через него же замеряют температуру.
В расчете на тонну жидкого металла добавляется примерно от 10 до 65 кг извести и от 5 до 25 кг доломита в зависимости от процентного содержания в загрузке железа прямого восстановления. Для удаления шлака есть шлаковый желоб. При температуре 1540 1555 оС металл выпускается в копильную печь, выполняющую роль миксера.
В копильной печи выравниваются температура, а также химический состав жидкой стали, после чего она готова к разливке. Во время загрузки или выпуска металла печь остается включенной.
Поскольку в печи с технологией Contifur поддерживается низкая рабочая температура с тем, чтобы повысить срок службы футеровки, рекомендуется постоянное использование копильной печи. В копильной печи сталь можно подогревать.
Любое остывание металла вызывает очень длительные и дорогостоящие остановки производства. Поэтому печи с технологией Contifur и копильные печи, оборудованные резервными панелями приборов для поддержания жидкого состояния стали.
Футеровку индуктора меняют каждые 1,5 2 месяца, весь процесс ее замены занимает примерно 16 18 часов. Футеровка пода нуждается в ремонте или замене каждые 6 8 месяцев, и на это уходит 3 4 дня.
Печь с технологией Contifur, как считается, обладает следующими преимуществами: низкие потребление электроэнергии и эксплуатационные расходы, увеличенный срок службы футеровки, предварительный нагрев скрапа, непрерывная работа, сравнительно простой слив шлака, загрузка до 100 % продуктов прямого восстановления, отсутствие потребностей в кислороде, непрерывное использование электроэнергии, отсутствие мерцания. Работа возможна даже при слабых электрических решетках или вспомогательных энергетических установках.
Электроэнергия: выгоды для завода ACB
Добавление второй нитки к установке непрерывного литья тонкостенных слябов на заводе компании Aceria Compacta de Bizkaia (ACB) в Бильбао (Испания) потребовало усовершенствования двух работающих на постоянном токе дуговых электропечей для обеспечения ежегодного производства 2 млн. т стали каждая дуговая электропечь обслуживает одну нитку. Работы по усовершенствованию выполнялись компанией SMS Demag без каких-либо изменений в существующих источниках электроснабжения.
После завершения работ на первой печи (№2) в конце 2000 года и проверки ее способности обслуживать однониточную установку непрерывного литья слябов была усовершенствована печь № 1, и к производству подключились вторая нитка, туннельная печь и сопутствующее прокатное оборудование.
В ACB выражали некоторую озабоченность по поводу работ в связи с предложением не повышать электроснабжение печи. Вместо этого успех работ по усовершенствованию был поставлен в зависимость от улучшения использования химической энергии, поднятия электрического КПД путем совершенствования связанных с пенистым шлаком операций и минимизации периодов отключений. Эта концепция применяется еще на одном объекте SMS Demag предприятии Nucor Berkeley в США.
В целом на проведение первой серии работ было отведено лишь 25 дней. В это время печь была остановлена. Выполненные за этот период работы включали:
удаление старой надстройки свода, поворотной системы, а также верхнего и нижнего кожухов печи, в том числе горелки и инжекторов;
модификацию платформы печи;
установку нового контейнера для хранения клапанов горелки и инжекторов;
установку трех инжекторов, питаемых из существующего бункера;
установку манипулятора кислородной фурмы для открытия окна выпуска;
установку пневматической системы дозагрузки бункера формовочной смеси для окна выпуска;
прокладку всех труб и проводов;
установку необходимых приборов и средств управления.
Печь была оборудована тремя системами инжекторов, расположенными с интервалами примерно в 120o. Каждая из них может работать и как горелка, и как инжектор кислорода при одновременном впрыскивании углерода или без него. Номинальный расход кислорода каждым модулем составляет 3200 м3/час, природного газа 700 м3/час и углерода 30 кг/мин.
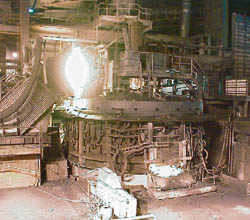 |
Усовершенствованная печь значительно повышает производительность и снижает потребление энергии Предоставлено: SMS Demag |
Производственные показатели до и после усовершенствования суммируются в таблице. Очень существенным моментом является то, что снижение на 95 кВт . ч потребления электроэнергии достигнуто не только за счет увеличения использования природного газа, углерода и кислорода, как считают в SMS Demag. Согласно расчетам, общая экономия электроэнергии должна составить примерно 85 кВт . ч. Дополнительная экономия 10 кВт . ч, как считается, стала результатом увеличения электрического КПД благодаря более эффективному вспениванию шлака и, возможно, более эффективному использованию кислорода и инжектируемого углерода.
Лучшее вспенивание шлака позволило сократить продолжительность плавки от выпуска до выпуска и обеспечить более низкое конечное содержание азота. Сейчас содержание азота на выпуске составляет максимум 0,006 %, что до модернизации дуговой электропечи было самым низким показателем.
Хотя еще одной выгодой от улучшения вспенивания шлака стало сокращение потребления электродов, показатели экономии не столь впечатляющие, как приводимые выше.
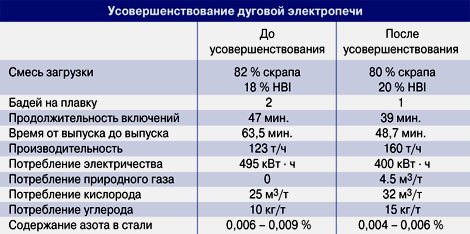
В целом более высокая производительность стала результатом следующих модификаций:
нижнего кожуха с повышенным объемом зеркала расплавленного металла и шлака, а также модифицированной системе закрытия окна выпуска;
увеличения диаметра и высоты верхнего кожуха, что позволяет обходится одной операцией бадьевой загрузки;
конструкции свода печи, позволяющей сократить продолжительность отключений и обеспечивающей быструю обменную систему;
манипулятора замера температуры и взятия проб, а также кислородной фурмы на окне выпуска для повышения безопасности персонала;
системы подачи кислорода и углерода через боковую стенку, улучшающую проведение операции с пенистым шлаком.
Одним из самых важных аспектов усовершенствования первой дуговой электропечи стало то, что оно позволило ACB продолжать работу, избегая сколько-нибудь существенного сокращения производства. После ее успешного завершения началась вторая фаза заводской модернизации в начале этого года были проделаны работы на второй дуговой электропечи.
Сдача в эксплуатацию второй нитки установки непрерывного литья слябов и сопутствующего заводского оборудования произойдет в апреле 2003 года.
|