|
|
Журнал |
|
Архив |
|
Подписка |
|
Реклама |
|
САММИТ |
|
Книжная полка |
|
Контакты |
|
В начало |
|
|
|
| |
|
|
 |
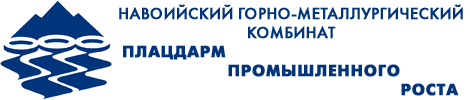 |
№4' 2003 |
версия для печати
|
|
ПО СТУПЕНЯМ НОВЫХ ТЕХНОЛОГИЙ |
|
Александр Рогачев
Главный инженер производственного объединения «Навоийский машиностроительный завод»
 Александр Рогачев |
|
а всех ступенях развития НМЗ и когда он только создавался, работая на уровне ремонтно-механического цеха, и когда стал машиностроительным объединением мы постоянно решали задачи, связанные с освоением новых технологий. Новых, прежде всего, для нас. Так повелось с первого директора НГМК З.П. Зарапетяна, который считал, что ремонтные подразделения (в то время они еще не были машиностроительными) должны собственными силами максимально обеспечивать потребности горнорудного производства. Дело было даже не в экономике. Сроки вот что определяло все действия, методы и средства. Ставились государственной важности задачи, их надо было выполнять.
Конечно, любой заказ комбината можно было разместить на других предприятиях страны. Но тогда неизбежно последовали бы согласования, переписка, выбор схемы транспортировки, ожидание наладчиков и авторского надзора. А это все потеря времени. Никакое производственное задание не было бы выполнено за те несколько дней или месяцев, в течение которых оно выполнялось здесь. Наш завод и производил, и ремонтировал, и занимался монтажом, ни на одном этапе не выпуская процесс из-под контроля. Каждое такое задание представляло целый комплекс вопросов организационных, технических, кадровых. Но в основу будущих решений всегда закладывалась инженерная идея. Само содержание и характер этой работы каждый раз требовали новых подходов.
Поход в другие отрасли
В номенклатуре завода есть продукция, которая не имеет прямого отношения к основной деятельности Навоийского горно-металлургического комбината и заимствована из других отраслей. Примером может служить шахтное оборудование. В свое время с участием специалистов по строительству угольных шахт и метростроевцев в кратчайшие сроки был организован выпуск проходческих щитов больших диаметров и арочной крепи, освоены их монтаж и обслуживание. С тех пор структура деятельности нашего генерального заказчика существенно изменилась. Подземные горные работы на урановых месторождениях давно прекращены. Эти изделия так бы и остались музейным экспонатом в истории завода. Но некоторое время назад арочная крепь вновь была востребована она понадобилась для разведочной шахты Мурунтау. И хотя мы более 10 лет не занимались этой продукцией, тем не менее за полгода сумели восстановить технологию, укомплектовали, должным образом оснастили оборудование и приступили к выполнению заказа.
Быть самостоятельным, независимым от внешних влияний таков основной принцип деятельности НГМК, обеспечивающий стабильность и устойчивое развитие комбината. В русле этой установки мы и взялись за конструирование собственного станка. Специалисты, которые занимаются станкостроением, хорошо представляют сложность этой задачи. Ее выполнение требует не только подготовленной производственной и конструкторской базы, но и предполагает наличие школы, системы обучения людей. Возможно, мы были несколько самоуверенными, не осознавали до конца, какие трудности ждут впереди. Но этот путь был пройден в сравнительно небольшой отрезок времени: через несколько лет завод начал выпуск токарного станка. Этот станок получился добротным и надежным. Он работает и у нас в инструментальном цехе, где требуется высокая точность, и в других подразделениях НГМК, которые охотно его приобретают для своих нужд. Мы имеем информацию, что наша продукция хорошо себя зарекомендовала также у сторонних потребителей в России, на Украине, в Казахстане.
И вот какая интересная особенность. Оказалось, что, ступив однажды на эту стезю, мы уже не можем притормозить остановка равносильна утрате завоеванных позиций. Стали возникать новые идеи. Мы изучали потребности в подразделениях комбината, в различных отраслях экономики Узбекистана, в других регионах. Начали заниматься сначала проектированием, а затем и производством заточных станков, настольно-сверлильных. По-настоящему высокого уровня эта работа достигла, когда мы освоили фрезерный станок НФ-630, который удачно сочетает в себе возможность выполнения нестандартных операций с простотой схемы и относительно невысокой ценой.
Постижение материала
Поскольку основной задачей завода было и остается поддержание высокой эффективности горно-перерабатывающего комплекса НГМК, то отсюда следует и одно из важнейших для нас направлений: увеличение сроков ходимости футеровок размольных мельниц на золотоизвлекательных фабриках. Мы занимаемся этой проблемой уже несколько десятков лет, и чтобы обозначить результаты, приведу цифры. Ходимость, то есть средняя наработка футеровок, возросла с 2500 до 4100 часов. Даже если бы удалось повысить показатель всего на 1020 %, то и такой результат следовало бы считать большим успехом. Это увеличение на целый месяц межремонтного срока работы мельничного блока и соответственно снижение расхода футеровки, экономия труда многих людей. Кроме того, повышается стабильность технологического процесса. Этот показатель трудно измерить в конкретных величинах, но тем не менее он объективен. Пуски и остановки, нарушающие установившийся режим работы мельницы, всегда приводят к потерям электроэнергии, сырья, качества.
Проблемой ходимости занимаются и другие службы комбината Центральное конструкторское бюро НГМК, специалисты золотоизвлекательных фабрик. Они принимают решения, в основном касающиеся конструкции футеровок. Представители НМЗ, конечно, тоже принимают участие в этих решениях, оценивая их с точки зрения возможностей литейного производства. Но главное, чем заняты наши специалисты, они ведут скрупулезную, каждодневную работу, связанную с анализом статистики и выявлением слабых мест футеровки, с внесением необходимых корректив в ход технологического процесса. Поскольку здесь нет заведомо выигрышных инженерных решений, каждое изменение характеристик должно подвергаться новому статистическому анализу. Все это длится не день и не месяц. Цикл работы футеровки превышает 4000 часов, то есть полгода. Именно через такой промежуток времени мы можем увидеть результат наших усилий положительный или отрицательный.
Одно из перспективных направлений, которое мы избрали и реализуем вместе со специалистами из Санкт-Петербурга, это микроскопические добавки в отливки из марганцовистой стали. Микролегирование позволяет повысить износостойкость футеровок, а значит, увеличить их ходимость. В конце 2002 года фирма, обладающая этой технологией, проводила с нашим участием опытные работы на горно-обогатительных комбинатах Северо-Западного региона России. Эксперимент показал возможность увеличения ресурса деталей, по самым скромным подсчетам, на 3040 %, а в отдельных случаях и до 100 %.
Большие надежды мы связываем с использованием в литейном производстве технологии холоднотвердеющих смесей. В свое время у нас уже был опыт их применения, к сожалению, отрицательный. Компонентами тогда служили фенолформальдегидные смолы и ортофосфорная кислота, поэтому условия труда в цехе оставляли желать лучшего. К тому же нередко возникали трудности с поставками. Мы никак не могли выйти на оптимальный режим работы и в итоге этот процесс забросили, отдав предпочтение стандартной технологии с приготовлением стержней и основных форм из земли, с использованием жидкого стекла в качестве связующего вещества.
Но жизнь заставила вернуться к нерешенной проблеме. Главная цель улучшение качества поверхности литых деталей. Это не просто эстетическая категория. Изделия работают в условиях или ударных нагрузок (с рудой, с шарами), или истирания, как скажем, зубья ковшей экскаваторов. Очень часто даже незначительные поверхностные дефекты небольшая раковина, не идеально ровный профиль становятся источником последующего разрушения отливок.
Мы проанализировали ситуацию, поработали с документацией, пообщались со специалистами и пришли к выводу: иной перспективы улучшения качества литейных форм, кроме как с помощью быстротвердеющих смесей, у нас нет. Сотрудничая с московской фирмой «Полион-П», мы приобрели небольшое количество нового связующего и в присутствии его разработчиков провели опытно-промышленные испытания. Перед этим постарались освежить в памяти прошлый опыт. Представление о работе с холоднотвердеющими смесями имелось, нашлись и люди, которые пробовали эту технологию много лет назад. Мы смогли организовать их поездки по предприятиям Российской Федерации, чтобы они посмотрели весь процесс на практике. И когда представители фирмы-поставщика приступили к испытаниям в литейном цехе НМЗ, они были немало удивлены. Оказалось, что ничего не надо показывать, только подправлять. Испробованы были все доступные варианты, проверены и запредельные режимы. Результаты получились превосходные, особенно по тем 56 позициям, ради которых мы и затевали это дело. Подготовлен контракт на промышленную поставку этого вещества. Надеемся, что и эта технология станет для НМЗ традиционной.
Гарантия надежности
Необходимо подчеркнуть: при всем стремлении к самостоятельности в техническом обслуживании основного производства наше предприятие отнюдь не пренебрегало преимуществами, которое дает кооперация. Другой вопрос, что ими далеко не всегда и не в полном объеме удавалось воспользоваться.
В начале 90-х годов возникли серьезные затруднения с организацией ремонта автомобильной техники. Прежняя централизованная система, действовавшая в масштабе большой страны, развалилась. Сервисное обслуживание на уровне западных фирм могло появиться разве что в неопределенном будущем. Тогда руководство комбината приняло решение идти двумя путями.
Прежде всего речь шла об использовании собственных резервов. На заводе имелись достаточные свободные площади, а также небольшой авторемонтный цех. Правда, он наполовину свернул свою деятельность, поскольку установилась другая тенденция передавать эти работы на специализированные предприятия. Но оборудование и часть специалистов-ремонтников еще остались. Силами этих людей, используя прошлый опыт, мы начали наращивать объемы капитального ремонта дизельных двигателей и постепенно довели до 20 единиц в месяц. Это показатель на данный момент, в основном он соответствует потребности НГМК.
Параллельно велась серьезная работа на перспективу. В сотрудничестве с ташкентским институтом НИПИпромтехнологии, с субпроектировщиками «Гипроавтомаш» и СКБ «НАТИ» было подготовлено ТЭО комплексного развития ремонтного производства. Уверен: если не в этом году, то наверняка в следующем году мы будем иметь профессиональную проектную базу для того, чтобы развивать ремонт не только дизелей, но и карбюраторных двигателей, а также основных узлов автомобиля коробок, мостов и т.д.
Перед нами стоит более сложная задача, чем ординарная сборка-разборка с переточкой каких-то деталей на ремонтный размер. Нет, речь идет о максимально возможном восстановлении техники с целью использования всего мыслимого и немыслимого ее ресурса. В ходе любых ремонтных работ мы обязательно ставим вопрос: а какую деталь сможем изготовить сами сегодня, завтра, послезавтра, какое для этого нужно оборудование, какие технологии.
Конкретный пример. Чтобы восстанавливать коленчатые валы дизельных двигателей, мы осваиваем два метода. Во-первых, с Институтом сварки им. Патона работаем над системой специальной наплавки валов. Во-вторых, готовимся использовать так называемое «осталивание» с помощью гальванического процесса. Это опять-таки продлевает ресурс дорогостоящих деталей.
В ремонтных целях беремся и за производство запасных частей к импортной технике. Тут уже необходимо исследовать химический состав металла, механические свойства детали. Заводская лаборатория, которая занимается таким анализом, располагает измерительным оборудованием европейского класса, а имеющееся на заводе металлообрабатывающее оборудование, в том числе и собственного производства, обеспечивает выполнение сложных операций с высокой точностью. Все это и позволяет с успехом решать подобные задачи.
Выполняя столь ответственные работы, производитель, конечно же, должен гарантировать безопасную и надежную эксплуатацию своей продукции. Все службы контроля ПО «НМЗ» аккредитованы в системе сертификации Республики Узбекистан на техническую компетенцию. Этим вопросом мы занимаемся с 1996 года, и были одними из первых, кто подал соответствующую заявку.
Центральная заводская лаборатория имеет в своем составе несколько специализированных служб, и они наделены правом проводить государственные испытания непосредственно на площадке НМЗ. Скажем, канатно-испытательная станция проводит испытание канатов для шахтных установок с выдачей сертификатов, а также механические испытания сварных образцов на предмет аттестации сварщика и на подтверждение марок сталей. Она же занимается испытанием пружин, их механических свойств. Лаборатория неразрушающего контроля осуществляет контроль металла на наличие скрытых дефектов, замер толщин стенок сосудов ультразвуковым, рентгеновским, капиллярным и другими неразрушающими методами. Металлография проводит исследования структуры металла, замеры твердости и микротвердости. В задачах спектральной лаборатории экспресс-анализ химического состава металлов.
Люди решают все
Прежде чем обратиться к проблеме людей не хотелось бы употреблять менее человечное слово «кадры», следует вновь напомнить факты истории Навоийского комбината. Общеизвестно, что сюда, в пустыню, ехали со всей страны. Но это были не просто добровольцы-романтики, а лучшие представители профессий, отобранные специальными комиссиями. Причем таким способом отбирались не только инженеры-специалисты, но и рабочие различных специальностей, в том числе модельщики, формовщики, сталевары, монтажники, станочники... Эта система комплектования создала комбинату такой запас прочности, что до сих пор и наш завод, и все другие подразделения НГМК опираются на достаточно сильные коллективы, способные справляться с задачами любой сложности.
Между тем время идет. Сегодня ведущим специалистам и руководителям производств, цехов ПО «НМЗ» уже, как говорится, «вокруг пятидесяти». Сил хватает, и опыта не занимать. Но пора задуматься: а кто придет на смену? Когда выясняется, что тот или иной специалист у нас в буквальном смысле незаменимый, это, может быть, и хорошо для оценки человека, но создает определенную угрозу для производства. Такого быть не должно. Мы обязаны заранее видеть кандидатов на ключевые должности главного технолога, главного металлурга, главного сварщика, начальника цеха, начальника участка, мастера.
Общая ситуация поменялась не в нашу пользу. Массовый приток людей в начале 90-х годов прекратился, и, наоборот, начался отток. И тогда вместе с главными специалистами и кадровыми службами мы сосредоточили основное внимание не на вопросе приема на работу, а на системе отбора и профессиональной подготовки нужных нам людей, начиная со школьной скамьи.
В качестве примера могу привести такой. НГМК держит на своем балансе несколько учебных заведений, в том числе колледж и Навоийский горный институт. Учащимся колледжа, которые выполняют учебную программу на «отлично», наш завод платит именные стипендии, и этих же ребят мы в первую очередь приглашаем к работе на нашем предприятии. Представители НМЗ участвуют в учебном процессе, в работе экзаменационных комиссий. На заводе организована кафедра горного института: для этой цели предоставлены помещения, наглядные пособия, наши ведущие специалисты проводят практические занятия.
Республиканская система высшего образования стала более гибкой. Появилась возможность готовить небольшими группами, по 45 человек, специалистов в тех областях, которые нам нужны в первую очередь. Для них мы сами составляем учебную программу. Отбором кандидатов на такие курсы занимаются кадровые службы и специалисты НГМК и НМЗ.
В Узбекистане пока нет учебной базы для подготовки специалистов определенного профиля. Прежде всего это касается литейщиков, но также нужны и специалисты кузнечно-штамповочного производства, и термисты. Мы уже направляем своих студентов в Московский институт стали и сплавов для прохождения курса по теме «Литье черных металлов» и в этом году ждем на работу первых выпускников. Подобное сотрудничество собираемся начать с Уральским политехническим институтом. Интересно будет сравнить, какая школа лучше московская или уральская.
Мы очень надеемся, что все эти меры позволят нам с наименьшими потерями пройти смену поколений, подготовить специалистов, которые продолжат славную историю нашего предприятия.
|
|
|
|
|
текущий номер

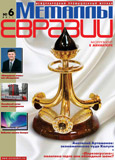
предыдущий номер

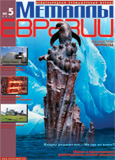
|
|