|
|
Журнал |
|
Архив |
|
Подписка |
|
Реклама |
|
САММИТ |
|
Книжная полка |
|
Контакты |
|
В начало |
|
|
|
| |
|
|
 |
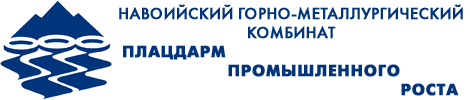 |
№4' 2003 |
версия для печати
|
|
КАРЬЕР МУРУНТАУ РАСТЕТ В ГЛУБИНУ |
|
Олег Мальгин
Заместитель главного инженера НГМК, доктор технических наук
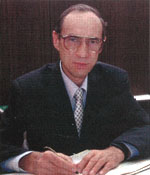 Олег Мальгин |
|
роблемы отработки глубоких карьеров имеют определенную специфику как в научно-методическом, так и в практическом плане. Об опыте НГМК в решении некоторых из этих проблем, связанных прежде всего с организацией транспортировки руды и породы, а также с подготовкой горной массы, и хотелось бы рассказать в этой статье.
Не снижая темпов и объемов
Технологии, применяемые на золоторудном месторождении Мурунтау, которое отрабатывается открытым способом, позволяют стабильно поддерживать экономически эффективное производство при постоянном увеличении глубины горных работ. Сейчас карьер развивается в границах третьей очереди с плавным переходом работ в четвертую очередь. Глубина карьера превысила 400 м. В дальнейшем планируется довести ее до 600 м. Одновременно продолжаются научные изыскания, которые уже показали принципиальную возможность вести открытую добычу руды на глубине до 900 м и даже до 1000 м.
Отработка рудных тел Мурунтау, как и других горных объектов НГМК, производится по селективно-площадной схеме добычи взрыванием рудных зон с сохранением структуры массива, экскаваторной выемкой различных сортов руд по видимым ориентирам, с зачисткой откосов забоя при входе и выходе из руды. Возможность значительно расширить минерально-сырьевую базу золотоизвлекательного комплекса открывается благодаря вовлечению в рентабельную переработку бедных, забалансовых руд и части минерализованной рудной массы. Ведется подготовка к эксплуатационному оконтуриванию балансовых запасов по более низким бортовым содержаниям золота в руде. В условиях Мурунтау, где отрабатываются рудные тела с высотой уступа 15 м и выше и применяются мощные экскаваторы с емкостью ковша от 12,5 м3 до 20 м3, это обеспечивает снижение потерь товарной руды с 5 % до 34 % и разубоживание с 1214 % до 910 %.
Вовлечение в отработку рудных тел с более низким бортовым содержанием золота позволяет поставить вопрос о переходе от селективной схемы транспорта руды к валовой выемке. Это увеличивает объем товарной руды и упрощает процесс ее выдачи на поверхность с применением конвейерных линий. Эффект достигается в следующем технологическом цикле, на стадии обогащения. В свое время на гидрометаллургическом заводе № 2 (ГМЗ-2) предполагалось в рамках четвертой очереди перерабатывать 26 млн т руды в год. Но благодаря успешно проведенной реконструкции завода планируется в 2003 году на тех же площадях переработать 27,5 млн т руды, а фактически ожидается более высокий результат 28 млн т. Увеличение валовой выемки позволяет полностью загрузить дополнительные мощности завода. Вот конечный смысл изменений и усовершенствований в технологиях горного производства.
В настоящее время специалисты комбината и Центрального рудоуправления НГМК при содействии ученых Узбекистана, России и Украины выполняют большой объем работ, направленный на увеличение устойчивости бортов карьера. Внедрение научных рекомендаций позволит принять к проектированию новые углы откосов, на 23o круче, чем планировалось раньше. Новая компьютерная технология построения финальной формы контуров карьеров при новых углах откосов позволит значительно сократить объемы горной массы и увеличить глубину отработки без дополнительного разноса бортов карьера.
Самосвалы и конвейеры
В динамическом развитии горных объектов особое значение имеет транспорт руды и породы. Выбор наиболее рациональных схем и эффективных видов транспорта предполагает учет смежных технологических операций, таких, как управление сырьевой базой, экскавация, подготовка горной массы буровзрывным способом, поддержание устойчивости бортов карьеров и др.
Развитие технологического транспорта в карьере Мурунтау неразрывно связано с изменением горнотехнических условий. За последние 30 лет среднее расстояние перевозки по карьеру увеличилось в 1,8 раза (до 5,7 км), в отвал в 3,1 раза (до 7,7 км), а средняя грузоподъемность автосамосвалов возросла в 5 раз. Опыт эксплуатации самосвалов «Катерпиллар» и «Юклид» грузоподъемностью соответственно 136 и 170 т показал несомненные преимущества транспортных средств большой единичной мощности: уменьшилась численность обслуживающего персонала, снизилась напряженность на дорогах, в пунктах погрузки и разгрузки и т.п., что способствовало безопасности транспортных работ. Однако эти изменения не могли компенсировать ухудшение работы автотранспорта, связанное с увеличением глубины карьера.
В этих условиях весьма значительную роль в обеспечении эффективной работы горно-транспортного оборудования и снижении себестоимости вскрыши играет комплекс циклично-поточной технологии. В его составе три дробильные установки, две линии конвейеров с шириной транспортерной ленты 2 м и два консольных отвалообразователя.
Циклично-поточная технология (ЦПТ) действует на карьере Мурунтау с 1984 года. В ее разработке и проектировании, в изготовлении и монтаже необходимого оборудования принимали участие научно-исследовательские организации и предприятия России, Украины и Узбекистана. Надо сказать, что в то время еще отсутствовал опыт применения ЦПТ для транспортировки скальных пород в столь больших объемах. Так что это решение было далеко не простым. Целесообразность внедрения новой схемы вызывала споры, да и последующее освоение комплекса шло достаточно трудно. Помог опыт эксплуатации роторных экскаваторов, конвейеров и отвалообразователей, накопленный специалистами Северного рудоуправления НГМК при разработке разнопрочных пород месторождения Учкудук. Практическую пользу принесли и научно-исследовательские работы по определению оптимальных углов откоса бортов карьера. По сути, это ответственные инженерные сооружения, и, проектируя их, необходимо обеспечить устойчивость бортов при минимальных объемах вскрышных работ.
Следует отметить большой вклад Навоийского машиностроительного завода. Коллектив НМЗ не только изготовил своими силами значительную часть узлов и конструкций, но и сумел исправить конструкторские недоработки, которые имелись в поставляемой технике, обеспечил вывод основного оборудования на проектные параметры.
Сегодня производительность комплекса ЦПТ достигла 2022 млн м3 горной массы в год. Таким образом, можно сказать, что эта технология в условиях карьера Мурунтау полностью себя оправдала.
Чем глубже, тем мобильнее
Концепция развития карьера Мурунтау и его транспортной схемы предусматривает дальнейшее применение ЦПТ. Однако в стесненных условиях глубокого карьера на нее воздействует целый ряд негативных факторов. С ростом глубины карьера увеличиваются углы откосов рабочего и нерабочего бортов, сокращается ресурс полезного рабочего пространства, производительность карьера по горной массе снижается. Между тем возможности поддержать стабильную работу существующего комплекса ЦПТ, увеличивая глубину его ввода в карьер, практически исчерпаны.
Наиболее эффективным техническим решением в этих условиях представляется переход от конвейеров традиционного исполнения к крутонаклонным конвейерам, способным осуществлять транспортировку горной массы под углом 40 и более градусов. Следует отметить, что в последнее время такие конвейеры привлекают внимание специалистов горнодобывающей промышленности. Проектные проработки, связанные с использованием крутонаклонных конвейеров, ведутся, в том числе в России на Ковдорском горно-обогатительном комбинате и в акционерном обществе «Карельский окатыш», в Монголии на предприятии «Эрдэнэт».
В настоящее время подготовлено ТЭО «Развитие комплекса ЦПТ карьера Мурунтау на основе внедрения опытно-промышленного мобильного дробильно-перегрузочного комплекса». Предполагается ликвидировать действующие конвейерные подъемники и дробильно-перегрузочные пункты, а вместо них построить модульные, в том числе с крутонаклонными конвейерами, которые будут применяться вместе с магистральными конвейерами, расположенными на борту карьера и задействованные в настоящее время для транспортировки породы во внешние отвалы. Для транспортировки руды на северо-восточном борту карьера создается самостоятельный конвейерный комплекс.
Для интенсификации поточных транспортных процессов разработана новая технологическая схема. Она заключается в следующем. Нижнюю часть наклонного конвейера формируют из автономных мобильных дробильно-перегрузочных комплексов, представляющих собой комбинацию передвижного дробильно-перегрузочного пункта с межуступным крутонаклонным перегружателем. Использование автономных комплексов в сочетании с существующим комплексом ЦПТ позволяет расширить область применения поточной технологии перемещения горной массы, значительно приблизив перегрузочные пункты к рабочей зоне карьера. Кроме того, такая технология дает возможность своевременно перемещать дробильно-перегрузочный пункт, следуя за развитием горных работ. Он может устанавливаться на рабочей площадке уступа при минимальных объемах горно-подготовительных работ, без строительства мощных подпорных стенок.
Межуступный перегружатель представляет собой двухленточный конвейер, установленный на самоходной тележке. Угол наклона конвейера до 40o, высота подъема горной массы до 30 м. В состав комплекса может входить межуступный перегружатель, имеющий две (верхнюю и нижнюю) самоходные тележки и перемещающий горную массу на высоту до 90 м. Предусматривается последовательная установка 23 перегружателей с последующей заменой при необходимости на секцию крутонаклонного конвейера.
В целом развитие циклично-поточной технологии в условиях глубокого карьера предусматривает внедрение в поточном звене мобильных дробильно-перегрузочных комплексов в сочетании с крутонаклонными конвейерами (до глубины 800850 м) и в цикличном звене высокоманевренных полноприводных автосамосвалов на стадии доработки карьера (глубина 9501000 м).
Взрыв под контролем компьютера
Требования, предъявляемые к современной горнодобывающей промышленности, хорошо известны. Они направлены на снижение ресурсоемкости горного производства и уровня его техногенной нагрузки на окружающую среду. Речь также идет о необходимости постоянного сокращения доли ручного труда, повышения безопасности работ и улучшении санитарно-гигиенических условий.
Эти требования учитываются и в практике использования взрывчатых веществ. Предприятия, отрабатывающие месторождения полезных ископаемых открытым способом, постоянно увеличивают объемы производства таких веществ на месте ведения взрывных работ. Предпочтение отдается безопасным и экологически чистым ВВ простейшего состава, преимущественно эмульсионного типа (ЭВВ). Новая рецептура, разработанная по принципу обратной эмульсии «вода в масле», придала ЭВВ ряд уникальных свойств. Их можно закладывать в скважинах с проточной водой, где ранее мог применяться только гранулотол. При этом эффективность взрыва за счет высокой плотности заряжания остается на прежнем уровне, а себестоимость снижается.
Именно эти тенденции были учтены в создании стационарного модульного комплекса по производству ЭВВ на карьере Мурунтау. Рассматривалось несколько вариантов. В итоге предпочтение было отдано проекту, технологиям и оборудованию компании Orica (Германия), которая предоставляет полный пакет нормативной и разрешительной документации. Эта компания хорошо известна на мировом рынке: ее заводы работают в 30 странах, выпуская различные виды гранулированных и эмульсионных ВВ, а также неэлектрические системы взрывания. Технология, предложенная нашему комбинату, полностью адаптирована к местному сырью, что имеет большое значение, учитывая сложившийся высокий уровень потребления ЭВВ в карьерах НГМК, при этом гарантируются безопасность и надежность в их изготовлении и применении. В составе завода построена линия по изготовлению эмульсионных патронированных ВВ. Предусмотрена возможность использования неэлектрических систем инициирования (индивидуальная задержка для каждой скважины) и др. Диаметры патронированной взрывчатки могут варьироваться от 36 до 90 мм, что позволяет оптимально использовать патроны ВВ в скважинах различного диаметра.
Смесительно-зарядные машины оборудованы автоматизированной системой управления, которая способна точно отмерять необходимое количество компонентов ЭВВ для каждой из скважин, что позволяет оптимизировать заряд по глубине. Компьютер, управляющий смесительно-зарядными машинами, может производить до 12 вариантов ЭВВ с разными физико-химическими и взрывчатыми показателями. Он дозирует компоненты согласно выбранному рецепту, обеспечивает их смешивание. На выходе из машины полученный состав соединяется с газогенерирующими добавками. Реакция сенсибилизации проходит непосредственно в скважине в течение 1520 минут, после чего смесь приобретает свойства эмульсионного ВВ.
Эксплуатация стационарного модульного комплекса на месте проведения взрывных работ позволила НГМК значительно усовершенствовать процесс подготовки горной массы и получить при этом высокий экономический эффект 10 млн долл. в год. По стоимости взрывчатые вещества собственного производства оказались более чем в 23 раза дешевле промышленных ЭВВ. Поскольку технология рассчитана на использование невзрывоопасных сырьевых компонентов, соблюдение мер предосторожности при их транспортировке и хранении не представляет особой сложности. Само производство также отличается высокой безопасностью и экологической чистотой. Взрывные работы полностью механизированы, тяжелый и сопряженный с риском физический труд исключен.
Подводя итог, необходимо сказать следующее. Комплексный подход к проблемам отработки сложноструктурных месторождений, к которым относится и золоторудное месторождение Мурунтау, позволяет успешно решить весь спектр задач, возникающих в ходе проектирования, строительства и отработки карьеров. В результате достигается основная цель: обеспечиваются устойчивые показатели по разработке вскрыши, добыче руды с заданным содержанием, что и позволяет поддерживать производство золота на уровне запланированных объемов.
Длительный опыт работы карьера Мурунтау убедительно показывает, что на основе новейших разработок и технологий, которые внедрены и планируются к внедрению, уже сегодня можно сформулировать требования к «карьерам будущего» глубоким, мощным, высокоэффективным.
|
|
|
|
|
текущий номер

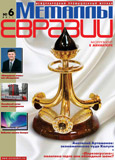
предыдущий номер

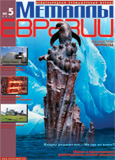
|
|