Василий Горпинченко Директор ГУП ЦНИИСК им. В.А. Кучеренко, доктор технических наук, профессор Павел Одесский Главный научный сотрудник, доктор технических наук, профессор
Стали с пределом текучести 200...800 Н/мм2 применяются при изготовлении сварных металлических конструкций, как массовых, так и уникальных стальных каркасов промышленных и гражданских зданий, резервуаров, башен, мачт, опор воздушных линий электропередачи и других сооружений. Их проектирование регламентируется строительными нормами СНиП II-23-81*, а изготовление ГОСТ 23118-99. Близкие по составу стали используются при изготовлении железнодорожных мостов, трубопроводов, конструкций различных кранов, строительных машин, кузовов больших грузовых автомобилей и т.д. Перечисленные конструкции изготавливают из проката тонко- и толстолистового, фасонного и сортового, из труб, холодногнутых профилей открытых и закрытых сечений и пр. Стоимость проката составляет до 40 % стоимости металлических конструкций. Стали, применяемые в строительных конструкциях, можно разделить на три группы: поставляемые предприятиями металлургической промышленности по действующим общегосударственным стандартам; нового поколения, производство которых осуществляется по техническим условиям или договорным нормативным документам; старинные, которые сохраняются в сооружениях при реконструкции, восстановлении или усилении. Кратко остановимся на последней группе. В настоящее время идет масштабная перестройка исторических центров крупных городов, при этом старинные стали часто сохраняются, например в Москве покрытие Киевского вокзала, Государственный Исторический музей, радиобашня Шухова. Эти материалы после восстановительных работ останутся в конструкциях на обозримую перспективу, так что их по праву следует назвать современными. Наиболее полное представление о сталях для металлических конструкций, выпускаемых по действующим стандартам, можно получить из ГОСТ 27772-88 "Прокат для строительных конструкций. Общие технические требования" (табл. 1). Основным классификационным признаком этих сталей является гарантированная величина предела текучести (в Н/мм2). Материал подразделяется на стали обычной прочности (sТ < 300 Н/мм2), повышенной (sТ = 300 385 Н/мм2) и высокой (sТ і 390 Н/мм2). Согласно европейским нормам, к сталям высокой прочности для металлических конструкций относят стали с (sТ і 355 Н/мм2. Основной особенностью химического состава отечественных сталей повышенной и высокой прочности является наличие ~ 1,5 % Mn при Mn : Si = 2, а также достаточно большое, по современным представлениям, содержание S и Р. Даже у сталей с sТ і 590 Н/мм2 содержание S и Р Ј 0,035 %, что недостаточно для обеспечения требуемого качества проката. За последние 10 лет в металлургии, а также в строительной индустрии произошел ряд экономических и технических изменений, что потребовало существенного развития сталей, поставляемых по действующим стандартам. Перечислим основные изменения, приведшие к созданию сталей нового поколения. 1. В результате интеграции отечественной металлургии в мировое хозяйство возникла необходимость в освоении методов контроля качества проката, принятых в зарубежных странах. Например, в России испытания на ударный изгиб традиционно проводятся на образцах Менаже с U - образным надрезом. В настоящее время в отечественной промышленности ускоренно осваиваются испытания образцов с V - образным надрезом, принятые в зарубежных стандартах. 2. В России ограничено производство марганцевых ферросплавов, потребности промышленности удовлетворяются менее, чем на 10 %. Отсюда возникла необходимость в создании низколегированных сталей с меньшим содержанием марганца, чем указано в таблице 1. При этом следует учитывать резко возросшую экономическую самостоятельность предприятий, заинтересованных в выпуске сталей, экономически выгодных в конкретных хозяйственных условиях комбинатов, например, с широким использованием природнолегированных чугунов.
3. В последние годы на металлургических предприятиях используются процессы, позволяющие улучшить качество проката. Широко освоены методы внепечной обработки стали, позволяющие уменьшить содержание в металле вредных примесей и газов, облагородить фазу неметаллических включений, улучшить однородность металла, сузить нормативный разброс содержания углерода и легирующих. Также широко освоено производство слябов методом непрерывного литья. При этом уходит в прошлое выпуск кипящих и даже полуспокойных сталей из-за невозможности достичь требуемого качества поверхности проката. Наконец, начали широко применяться процессы его упрочнения на станах, что объективно ведет к снижению содержания легирующих элементов в сталях с одновременным повышением качества продукции. В связи с этими переменами идет пересмотр действующих строительных норм и правил, регламентирующих проектирование и изготовление металлических конструкций. Коснемся основных подходов к нормированию проката из сталей нового поколения. В таблице 2 представлены гарантии по ударной вязкости проката для металлических конструкций, обеспеченные современным уровнем металлургической промышленности (знаменатель) в сравнении с гарантиями, регламентированными ГОСТ 27772-88 и другими аналогичными действующими стандартами (числитель) и нормированными в СНиП II-23-81*. По мере возрастания ответственности сооружения, сложности работы материала в конструкциях, прочности проката, а также снижения температуры эксплуатации увеличиваются и требования к ударной вязкости стали. Обычное содержание вредных примесей, в первую очередь серы, может снизить ряд важных свойств проката из низколегированных сталей с марганцем: возникают склонность к слоистому разрушению и низкая пластичность по толщине, ухудшаются свариваемость, технологичность и ударная вязкость при нормальной температуре. Природа этого явления связана с наличием в прокате марганцовистых сталей некоторых видов неметаллических включений, в первую очередь строчечных или ленточных сульфидов марганца, иногда строчечных оксидов. Для предотвращения подобных явлений существующую систему оценок рабочих свойств в стандартах и строительных нормах необходимо дополнить определением пластических свойств по толщине проката, так называемых Z-свойств. Такие свойства, согласно действующему ГОСТ 28870-90 и аналогичным зарубежным стандартам, определяются по относительному сужению ((z) образцов, вырезанных по толщине проката. Минимальная гарантированная величина yz і 15 % Согласно ГОСТ 28870-90, имеются также градации yz і 25 % и даже 35 %. Известно, что Z-свойства возрастают при повышении чистоты стали по вредным примесям, особенно по сере, и при глобулировании (сфероидизации неметаллических включений). Эти процессы реализуются при внепечной обработке жидкого металла, достаточно широко освоенной в настоящее время на отечественных металлургических предприятиях. Иными словами, гарантии по Z-свойствам современной промышленностью могут быть обеспечены во всей полноте.
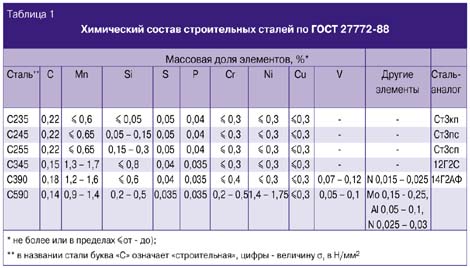 Рассмотрим наиболее вероятные пути развития строительных сталей с учетом хозяйственных реалий и необходимости соответствия новым техническим требованиям, включая положения современных зарубежных стандартов. О сталях обычной прочности с sT < 300 Н/мм2 типа Ст3, из которых изготавливается более 80 % строительных металлоконструкций, следует, во-первых, сказать, что объем производства не полностью раскисленных сталей сокращается и будет сокращаться из-за широкого освоения экономически эффективных методов производства непрерывнолитых слябов, при которых у изделий из кипящих и полуспокойных сталей не обеспечивается нужное качество поверхности. Согласно СНиП II-23-81*, малоуглеродистые стали с обычной хладостойкостью при температурах tэ < -40ОС можно использовать лишь в конструкциях группы 3 (колонны, стойки и т.п.) (табл. 2). В соответствии с европейскими нормами малоуглеродистые стали выпускаются с более высокими требованиями: КСV0, KCV20 (EN 10025) и даже KCV50 (сталь S275NL по EN 10113-2). Такие нормы обеспечиваются микролегированием с одновременным измельчением зерна. Стали с подобными свойствами производятся отечественной металлургией по ТУ, в частности АО "НОСТА", и включаются в строительные нормы и правила как материалы, предназначенные для конструкций, эксплуатируемых при tэ < -40ОС. В сталях повышенной прочности С345 предлагается полностью перейти на гарантии по КСV при различных температурах и исключить гарантии по КСА, поскольку они в данном случае всегда выполняются. В настоящее время для проката повышенной прочности используются стали, содержащие ~1,5 %Mn, прежде всего марок 09Г2С или 12Г2С. Усиление гарантий по ударной вязкости достигается при увеличении дисперсности микроструктуры нормализацией (или альтернативной обработкой) - КСV20, при термическом улучшении (или альтернативной обработке) - КСV40. Из-за дефицита марганца в России основное направление развития этих сталей - сокращение его содержания в химическом составе.
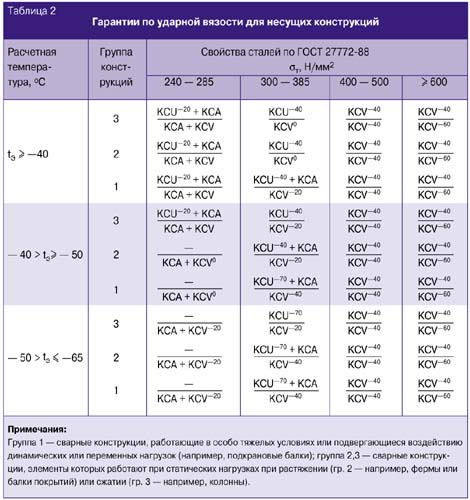 Разработан путь создания сталей повышенной прочности на базе малоуглеродистой стали Ст3сп с содержанием Mn Ј 0,65 %. Обеспечение повышенного уровня свойств в данном случае эффективно достигается путем микролегирования недорогими нитридами титана и алюминия при добавлении ~ 1 % Si, что в случае понижения температуры конца прокатки (ниже 900ОС) упрочняет сталь вследствие легирования твердого раствора кремнием и измельчения зерна. Последнее происходит в результате улучшения кинетики выделения дисперсной фазы в данных условиях прокатки. Для стали 18САТЮ толщиной до 20 мм включительно обеспечиваются следующие гарантированные свойства: sт і 350 Н/мм2; sв і 500 Н/мм2; d5 і 30 %; КСU-70 і 34 Дж/см2 и KCV-40 і 34 Дж/см2. В целом прокат полностью удовлетворяет наиболее жестким требованиям к сталям повышенной прочности. На ряде металлургических комбинатов повышенный и даже высокий уровень прочностных характеристик и ударной вязкости при отрицательной температуре достигается упрочнением малоуглеродистой стали Ст3 в потоке станов при охлаждении проката ламинарными, иногда турбулентными токами воды. В последние годы эта ресурсосберегающая технология находит все большее применение на заводах стран СНГ и Европы, в Японии и США. В подобном прокате с дисперсной феррито-перлитной структурой содержание вредных примесей не должно превышать, по крайней мере, S и P Ј 0,025 %. Приведенные сведения показывают, что в стандарты и строительные нормы наряду со сталями повышенной прочности с ~ 1,5 %Mn, дефицитность и стоимость которых со временем будет постоянно возрастать, следует ввести материалы с пониженным содержанием марганца. Тогда химический состав этих сталей в нормативной документации можно регламентировать с помощью углеродного эквивалента, разумеется, с одновременным ограничением максимального содержания углерода и вредных примесей. Еще более жесткие требования следует предъявлять к сталям высокой прочности (sт і 390 Н/мм2), особенно по ударной вязкости: КСV-40 для сталей С390 и КСV-60 для сталей со свойствами С590, причем независимо от температуры эксплуатации и группы конструкции. Это связано с тем, что в сталях высокой прочности условия обеспечения заданного сопротивления хрупким разрушениям сварного соединения оказываются более жесткими, чем отрицательное влияние низкой температуры эксплуатации и условий работы конструкции. При необеспеченности указанных выше норм хрупкие разрушения сварных конструкций из сталей высокой прочности наблюдались уже при их изготовлении и транспортировке, т.е. еще до ввода в эксплуатацию.
Поэтому при выборе стали для крупных инженерных сооружений в Москве были выдвинуты новые, более жесткие требования к прокату и свойствам промышленных партий с учетом реальных возможностей современной металлургии: сейчас KCV-40 і 35 Дж/см2 вместо KCV-40 і 20 Дж/см2 по ГОСТ 27772-88 (возможно увеличение ударной вязкости до уровня KCV-50 і 35 Дж/см2); СЭ Ј 0,46 % вместо СЭ Ј 0,49 % по тому же ГОСТу; обязательны гарантии по Z-свойствам в толщинах свыше 20 мм. Для получения полного комплекса свойств уменьшено содержание вредных примесей: вместо S Ј 0,035 % и Р Ј 0,03 % были приняты 0,015 % каждого элемента и при этом реализованы процессы облагораживания фазы неметаллических включений. Кроме того, стали высокой прочности начали выпускать с наименьшим содержанием газов (например, Н2 не более 2 см3 на 100 г металла) и улучшенной геометрией, а также термообработанными для получения дисперсной структуры. Подобные стали надежно работают в конструкциях при их изготовлении и эксплуатации. Для уникальных сооружений нами успешно применялась термически обработанная сталь типа 10ХСНД с уменьшенным содержанием легирующих и высокой чистотой металла. Примеры использования этих сталей: конструкции Большой спортивной арены стадиона в Лужниках, фермы старого Гостиного двора и конструкции надтрибунного покрытия футбольного стадиона "Локомотив". При этом прокат удовлетворял всем описанным выше требованиям. Высокое его качество способствовало изготовлению и возведению сооружений в сжатые сроки, поскольку отсутствовали специфические для сварных конструкций дефекты. Разумеется, при выполнении изложенных требований может также рассматриваться прокат из сталей с иными химическими составами. Подведем итоги. 1. Совершенствование процессов производства сталей, достигнутое в последние годы в отечественной металлургической промышленности, позволило обоснованно повысить требования к строительным сталям для массовых и уникальных металлических конструкций. На комбинатах выпускается прокат для стальных конструкций, соответствующий требованиям зарубежных, в частности европейских стандартов EN 10025, EN 10113 и т.д. Стали нового поколения массово применялись при возведении современных общественных зданий и сооружений. 2. Действующие в настоящее время стандарты, по которым металлурги поставляют листовую сталь отечественным потребителям, отражают представления о материалах, сложившиеся в 60 70-х годах ХХ века. Создание национальных стандартов на строительные стали, отражающие новые реальные возможности металлургической промышленности, позволит обеспечить выпуск сталей и изготовление конструкций, соответствующих современному мировому уровню.
|