Александр Беломестнов
Начальник технического отдела
Георгий Белогорцев
Начальник отдела новых видов продукции
Объединенная металлургическая компания
Трубная промышленность России является одним из главных секторов металлургического производства и располагает крупнейшими в мире мощностями по производству труб различного сортамента. Несмотря на сложности последнего десятилетия, трубные заводы России в целом сохранили свой потенциал, стабилизировали производство, установили и укрепили прочные партнерские взаимоотношения со своими главными потребителями - предприятиями нефтегазового комплекса, развитие которого определяет динамику и перспективы общеэкономического роста российского хозяйства. Расширение географии добычи топливных ресурсов, в том числе освоение новых месторождений в труднодоступных регионах страны с суровыми природно-климатическими условиями, необходимость строительства новых трубопроводов с более высокими рабочими давлениями (до 8,4-15 МПа), рост требований к эксплуатационной надежности и экологической безопасности, - весь этот комплекс факторов определяет круг основных проблем трубного производства России.
Очевидно, что одним из важнейших направлений развития трубного сектора страны является совершенствование качества серийно выпускаемых труб и освоение производства новых видов продукции. Как показывает мировой опыт, в условиях рынка эти задачи решаются путем создания системы управленческих рычагов, методов и отношений, увязывающих в единое целое основные хозяйственные функции по разработке, производству и сбыту продукции и услуг. Такой системный подход наиболее эффективно реализуется компанией, сумевшей создать благоприятные условия для инвестиционной деятельности, обеспечить развитие материально-технической кооперации и сотрудничества с другими предприятиями и потребителями, сформировать современный уровень организации и управления производством и соответствующее развитие рыночной инфраструктуры. Требуемое качество нефтегазовых труб формируется при выборе оптимальных параметров всех стадий производственного цикла, включая подбор химического состава стали, технологию выплавки и разливки, прокатки листа и, наконец, процесс его формовки, сварку труб, их термообработку и нанесение антикоррозионного покрытия, неразрушающий контроль.
Именно такие принципы положены в основу деятельности Объединенной металлургической компании, в состав которой входят Выксунский металлургический и Челябинский трубопрокатный заводы, обеспечивающие около 40 % российского производства труб. При этом заводы компании выпускают около 80 % труб большого диаметра для строительства магистральных нефтегазопроводов, около 30 % нефтепроводных труб, 25 % водогазопроводных труб, 30 % обсадных труб. Некоторые виды продукции, например бесшовные горячедеформированные трубы диаметром 426-558 мм с толщиной стенки свыше 32 мм, холоднодеформированные трубы диаметром более 120 мм, сварные прямошовные трубы диаметром до 1020 мм с толщиной стенки 32 мм, в том числе для эксплуатации при температурах до минус 60 оС производятся в России только заводами ОМК.
В соответствии с выбранной стратегией развития Объединенная металлургическая компания активно развивает производственную кооперацию с ОАО "Северсталь", крупнейшим российским металлургическим комбинатом, который является главным поставщиком металлопроката для производства электросварных труб. Успешным примером такой кооперации является создание в июне нынешнего года совместного предприятия в рамках проекта "Альянс 1420" по выпуску магистральных прямошовных труб диаметром 508-1420 мм с толщиной стенки до 40 мм класса прочности Х80 и длиной до 24 м. Менеджеры компаний проводят единую инвестиционную и техническую политику, что позволило, в частности, освоить промышленное производство новых видов металлопродукции с повышенными потребительскими характеристиками (Подробнее о проекте "Альянс-1420" см. "Металлы Евразии" № 5, 2001 г.).
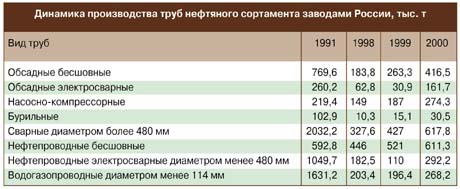
Производство труб повышенной прочности для добычи и транспортировки углеводородного сырья из районов с суровыми природно-климатическими условиями требует постоянной работы в направлении создания новых марок стали с оптимальным химическим составом, разработки технологии получения труб с высокой хладостойкостью и устойчивостью к воздействию агрессивных сред (например, сероводорода). Вместе с тем, заводы компании многое делают для совершенствования оборудования и технологии сварки, формовки, термообработки, нанесения покрытий, контроля и испытаний. Эта работа проводится в постоянном контакте с крупнейшими потребителями труб ОАО "Газпром", АК "Транснефть", НК "ЮКОС" и другими.
Для разработки новых марок стали в составе ЗАО "ОМК" создана рабочая комплексная группа, которая включает специалистов-металловедов, технологов, представителей компаний нефтегазового комплекса.
Высокое качество трубной продукции ОАО ОМК подтверждено международными сертификатами. Система контроля качества ВМЗ и ЧТПЗ сертифицирована на соответствие требованиям стандарта АРI Spec Q1. Эти предприятия получили лицензии, позволяющие использовать официальную монограмму Американского нефтяного института на магистральных газонефтепроводных трубах, изготовленных в соответствии со стандартами АPI 5L, и обсадных трубах по API 5СТ. Кроме того, сертификаты регистрации подтверждают соответствие действующей на ВМЗ и ЧТПЗ системы качества требованиям стандарта ISO 9001:94 при проектировании и производстве нефтегазопроводных, магистральных и обсадных труб, муфт, стальных слитков и железнодорожных колес.
Выксунский металлургический завод является одним из ведущих в России производителей стальных электросварных труб диаметром от 15 до 1020 мм различного назначения. В 2000 году ВМЗ поставил предприятиям нефтегазового комплекса более 11 тыс. т труб, из которых около 75 % составили трубы диаметром 530-1020 мм, в том числе до 50 % импортозамещающие трубы из стали марки 10Г2ФБЮА класса прочности К60 (Х70) на рабочее давление до 100 атм. В настоящее время партнерство ВМЗ с ОАО "Газпром" базируется на соглашении о сотрудничестве, заключенным на период до 2003 года. Это соглашение предусматривает освоение производства электросварных труб с наружным и внутренним антикоррозионным покрытием, выпуск труб большого диаметра с толщиной стенки до 32 мм на рабочее давление до 24 МПа, труб в хладостойком исполнении с температурой эксплуатации до минус 60 oС, коррозионностойких труб, а также обсадных с новыми резьбовыми соединениями повышенной герметичности. Для выполнения этих программ намечен и реализуется ряд соответствующих инвестиционных проектов. Так, в конце 2000 года на заводе был введен в эксплуатацию участок по нанесению наружного двух- и трехслойного антикоррозионного покрытия для труб диаметром 102-1220 мм с годовой производительностью около 200 тыс. т. В настоящее время прорабатывается вопрос по организации линии нанесения на трубы диаметром 159-1220 мм внутреннего антикоррозионного (для нефтепродуктов) и гладкостного (для газопроводов) покрытий на основе жидких или порошковых термореактивных композиций.
В 2001 году ОМК выполнила ряд заказов на производство труб для нефтедобывающих компаний. Например, партия в объеме более 28 тыс. т труб диаметром 630 мм с толщиной стенки 9 мм, рассчитанных на эксплуатацию до минус 60 С, из стали марки 10Г2ФБЮ с трехслойным покрытием была изготовлена для компании ЮКОС с участием ВМЗ (выпуск труб), ВМЗ и ЧТПЗ (нанесение покрытия). Кроме того, Выксунский металлургический завод изготовил и отправил первую партию (8,5 тыс. т) хладостойких труб размером 720х8-11 мм из стали класса прочности К54 на строительство газопровода Пелятка - Мессояха по заказу компании "Таймыргаз". Ранее подобные трубы закупались в Японии. Наконец, в текущем году ВМЗ будет выполнен заказ фирмы "Нова", осуществляющей строительство газопровода от Юрхаровского месторождения в Ямало-Ненецком автономном округе, на поставку партии в объеме 11 тыс. т труб диаметром 820 мм с трехслойным антикоррозионным покрытием.
Выксунский металлургический завод единственный среди отечественных предприятий, который может выпускать толстостенные трубы большого диаметра. В 2000 году здесь были изготовлены опытные партии труб из высокопрочных сталей АБ-11 и 10ГНБ класса прочности К60 диаметром 1020 мм с толщиной стенки 26 и 32,4 мм. Сталь была разработана ЦНИИ КМ "Прометей", а лист изготовлен на заводе "Ижорасталь". Испытания в АО "ВНИИСТ" показали, что трубы имеют трехкратный запас по давлению, вызывающему потерю устойчивости контура трубы, и полностью отвечают требованиям к трубам для строительства морского газопровода с максимальной глубиной укладки 320 м. На основании результатов испытаний трубы данного класса рекомендованы для использования при прокладке газопроводов Штокмановского газоконденсатного месторождения.
Другим уникальным видом продукции Выксунского металлургического завода являются сварные обсадные трубы диаметром 146-245 мм со стенкой 6,5 - 10,7 мм класса прочности Дс с трапецевидной резьбой "Батресс". По заказам потребителей в прошлом году было освоено производство труб этого вида с трапецевидной резьбой ОТТМ. Высокая точность электросварных обсадных труб по толщине стенки и овальности обеспечивает повышение эксплуатационных свойств и позволяет снизить металлоемкость колонны почти на 9 % по сравнению с бесшовными трубами.
Челябинский трубопрокатный завод и Газпром в конце 2000 года подписали соглашение о сотрудничестве для реализации совместных программ по освоению нефтегазовых месторождений, а также в сфере строительства новых и капитального ремонта действующих магистральных газопроводов. В рамках этого сотрудничества ЧТПЗ освоил выпуск газонефтепроводных труб в хладостойком исполнении из 7 марок стали, в том числе классов прочности К52 и К60. Особый интерес представляет сталь марки 09ГСФ (класс прочности К52), микролегированная ванадием, ниобием и титаном. Физико-механические свойства стали обеспечивают изготовленным из нее трубам высокую стойкость газонефтепроводов, как с обычными, так и с агрессивными средами практически в любых климатических зонах. Трубы из стали 08Г1НФБ (класс прочности К60), легированной ниобием, ванадием и титаном, имеют высокие характеристики ударной вязкости при температуре эксплуатации трубопровода.
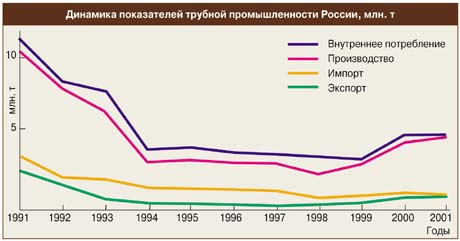
Повышению конкурентоспособности продукции ОАО "ЧТПЗ" способствует пуск в середине 2000 года отделения наружного трехслойного покрытия для труб диаметром 508-1220 мм. К настоящему времени опробовано несколько систем покрытий с использованием материалов ряда зарубежных фирм. По заказу АК "Транснефть" изготовлено и отгружено более 18 тыс. т труб с полиэтиленовым трехслойным покрытием усиленного и весьма усиленного типа на базе французских материалов. Кроме того, учитывая потребность в трубах с внутренним покрытием , заводом совместно с голландской фирмой "Selmers" рассматривается вопрос об организации отделения внутреннего покрытия труб диаметром 508-1220 мм. При этом наряду с тонкостенным гладкостным покрытием толщиной 50-80 мкм планируется и внедрение антикоррозионного двухкомпонентного эпоксидного покрытия толщиной 300-400 мкм. Пуск отделения позволит значительно повысить качественные характеристики труб и выполнить любые требования заказчиков.
Важнейшим направлением на заводе является повышение качества сварного шва труб. Прежде всего следует отметить освоение промышленных автоматизированных установок дуговой сварки с АСУТП под слоем флюса для труб диаметром 1020-1220 мм. В предыдущие годы была внедрена система управления сваркой внутренних швов для труб диаметром 1220 мм с использованием микропроцессорной техники. Аналогичные работы были выполнены и для сварки наружных швов. Главной целью создания АСУ трехдуговой сваркой швов является выбор и поддержание с достаточной точностью электрических и технологических режимов сварки, что позволяет впервые в мировой практике обеспечить заданные параметры геометрии сварного шва (ширина, усиление, глубина провара) по всей длине независимо от квалификации сварщика. В конечном итоге это позволяет резко повысить качество и надежность сварного соединения.
Завод планирует в ближайшее время провести опытно-промышленные испытания процесса лазерной сварки труб. Эта работа, в которой участвуют ЗАО "Лазерные комплексы", ОАО "ВНИИСТ" и ОАО "ВНИИГАЗ", направлена на максимальное сокращение зоны термического влияния сварного шва, что позволит повысить пластичность металла шва. Кроме того, использование лазерной сварки снизит до минимальных размеров усиление валика шва, что будет способствовать повышению его надежности.
И наконец, на ЧТПЗ проводится работа по организации производства принципиально новой "бесшовной" трубы с локальной термомеханической обработкой сварного соединения. Локальная термомеханическая обработка (ЛТМО) сварного шва заключается в нагреве зоны шва шириной 80-100 мм до температуры 1000-1050 оС, раскатке усиления шва до уровня основного металла в специальной клети и последующей закалке и отпуске указанной зоны. Проведенные заводом эксперименты показали, что в результате ЛТМО обеспечивается мелкозернистая структура металла сварного шва на уровне основного металла, выравниваются механические свойства по периметру трубы, существенно повышается ударная вязкость шва и зоны термовлияния, а также полностью исключается усиление шва как концентратора напряжений. Кроме того, значительно повышается надежность наружного покрытия за счет отсутствия усиления шва. Указанные преимущества были достигнуты на трубах из сталей классов прочности К52 и К60 и подтверждены в процессе полигонных испытаний.
На основании полученных результатов заводом разработано и согласовано с ОАО "Челябгипромез" техническое задание на проектирование отделения по промышленному производству труб диаметром 1020-1220 мм с ЛТМО сварных швов производительностью до 130 тыс. т в год. Монтаж и пуск отделения намечено осуществить уже в будущем году.
На заводе продолжается реконструкция трубопрокатного цеха №1, которая позволит освоить производство тонкостенных горячедеформированных труб диаметром до 600 мм. Здесь будет установлено современное отделочное оборудование, в том числе для выпуска обсадных труб диаметром до 508 мм с любыми типами резьб.
Стратегия развития Объединенной металлургической компании, в основе которой постоянный анализ рыночной конъюнктуры и активное взаимодействие с заказчиками и партнерами, продуманная инвестиционная политика, направленная на совершенствование качества и снижение производственных затрат, позволяют полностью обеспечивать потребности нефтегазового комплекса в качественной трубной продукции.
|