Дмитрий Еланский Московский государственный институт стали и сплавов(Технологический университет)
Если первую половину прошедшего столетия можно назвать временем мартеновских печей, вторую кислородных конвертеров, то наступивший век, по мнению большинства экспертов, будет характерен расцветом электродуговой плавки (рис. 1). Высокая производительность, компактность, экономичность, технологическая гибкость, сопряженность с машинами непрерывного литья и агрегатами внепечной обработки, возможность выплавки сталей и сплавов любого химического состава с низким содержанием вредных примесей все это обеспечивает дуговым сталеплавильным печам (ДСП) роль фаворита.
Уже сегодня удельный вес электростали и доля непрерывного литья заготовок являются важнейшими показателями эффективности сталеплавильного передела той или иной страны (табл. 1). Кроме того, ДСП являются технологической основой мини-заводов одного из динамичных направлений развития мировой черной металлургии, которая сохранит высокие темпы роста в обозримом будущем.
Электроплавка, сравнительно молодой технологический процесс, оказалась восприимчивой к нововведениям, позволившим за короткий период существенно повысить основные технико-экономические показатели и обеспечить опережающие темпы роста выплавки электростали (рис. 2, табл. 2).
Произошедшие в последние 10 лет изменения в технике и технологии плавки в ДСП способствовали снижению удельных расходов электроэнергии, электродов и огнеупоров и росту производительности печей. Эффективность работы ДСП резко возрастает с применением установки ковш печь. При этом дуговая печь используется только для плавления лома, дефосфорации и обезуглероживания металла, а все операции по десульфурации, раскислению, легированию и доводке по температуре выполняются вне ДСП. При использовании современной печи высокой мощности, оснащенной оборудованием для интенсивного применения кислорода, природного газа и углеродсодержащих порошкообразных материалов, в связке с агрегатами внепечной обработки удается стабилизировать на достаточно высоком уровне технико-экономические показатели практически для всего выплавляемого сортамента (за исключением нержавеющих и быстрорежущих высоколегированных сталей).
Современная ДСП, параметры которой представлены в табл. 2, обеспечивает цикл от выпуска до выпуска в пределах 45 мин, расход электроэнергии в 350 кВт*ч/т жидкой стали и расход электродов на уровне 1,5 кг/т при суммарном использовании кислорода 35 45 м3/т, газа - 4 - 8 м3/т и углерода (кокс/уголь) в завалку (5 15) плюс инжектированный (3 10) кг/т. Современная технология плавки стали в ДСП должна быть приспособлена к использованию большого количества первичного железа в виде восстановленных окатышей или брикетов (DRI/BRI), жидкого или твердого чугуна. По некоторым оценкам, к 2010 году в шихте электропечей может быть использовано не менее 50 млн. т металлизованного сырья и до 9 млн. т жидкого чугуна. Качество лома, в частности содержание в нем вредных примесей, является одной из главных проблем электроплавки, обеспечения чистоты металла.
Основные усилия разработчиков новых агрегатов направлены на снижение таких важных статей условно-переменных затрат, как расход электроэнергии, электродов и огнеупоров. Усовершенствование техники, как правило, ведет к росту капитальных вложений и в ряде случаев может повышать эксплуатационные расходы из-за усложнения ремонта и на запасные части. Поэтому экономическую эффективность предлагаемых технических решений, очевидно, следует оценивать исходя из того, что надежность оборудования обратно пропорциональна его сложности.
Современные печи, как правило, способны работать под током до 45 50 мин. Именно этот показатель и является основным в рекламе и гарантиях поставщика, наряду с такими коэффициентами, как расход электроэнергии и электродов. Однако для достижения необходимой годовой производительности печи и низких издержек производства решающее значение имеют надежность и ремонтопригодность оборудования ДСП, развитость инфраструктуры цеха (электросетей, газового и кислородного хозяйства, вспомогательного оборудования, потоков сырья, материалов и продукции), обученность и мотивированность персонала, его способность обеспечить стабильность технологических операций.
Основные пути развития техники и технологии плавки в дуговых сталеплавильных печах условно можно разделить на два вида:
применение ДСП новых конструкций (двухванные, агрегаты с подогревом лома, печи с непрерывной подачей лома, шахтные печи и др.);
модернизация действующих ДСП традиционной конструкции путем использования оптимизированных современных технологий и оборудования.
Печи постоянного тока. Выбор питающего тока является одним из основных параметров ДСП.
Основные преимущества дуговых печей постоянного тока (ДППТ) сокращение расхода электродов, электроэнергии, огнеупоров, меньший уровень шума и колебаний электросети. Главным фактором, обеспечивающим экономическую привлекательность ДППТ, считается меньший расход электродов. Однако с ростом объема печи и увеличением в связи с этим диаметра электродов это преимущество частично утрачивается из-за опережающего роста их стоимости.
К недостаткам работы на постоянном токе следует отнести усложнение электротехнического оборудования. ДППТ большой вместимости оснащаются 2 4 преобразователями тока, что приводит к повышению капитальных затрат, расходов на обслуживание и к снижению надежности оборудования. Большинство публикаций о работе подовых электродов говорит как минимум о необходимости большого внимания к надежности и о том, что их обслуживание выделяется отдельной строкой в списке затрат на выплавку стали в ДППТ.
Двухкорпусные печи. Развитие электроплавки идет не только по пути использования новых идей, но и совершенствования ДСП традиционной конструкции. Последнее связано с оптимальным применением как известных, так и новых видов оборудования и технологических приемов для вспенивания шлака, комплексного использования кислорода и инжекции углеродсодержащих материалов, привлечения неэлектрических источников энергии (газокислородных горелок, дожигания отходящих газов) и др. На ряде металлургических заводов Люксембурга и Франции для увеличения времени использования трансформатора были применены двухкорпусные печи. Когда в одном корпусе проводятся додувка, выпуск, заправка, завалка (заливка чугуна), в другом работают дуги. Однако в рабочем цикле печи режим ожидания каждого корпуса составлял длительный период, что заметно снижало тепловую эффективность ДСП. По расчетам некоторых специалистов, использование указанных двухкорпусных агрегатов не приносит явных преимуществ с точки зрения условно-постоянных затрат на выплавку стали, более того, вызывает увеличение капитальных вложений и усложняет конструкцию печной установки.
Подогрев лома отходящими из печи газами и шахтные печи. Эта идея вызывает значительный интерес вследствие существенной экономии технологической электроэнергии. В промышленной практике используются печные агрегаты, совмещенные с подогревателями лома, в частности шахтные печи. Подогрев лома в обычных бадьях в специальных камерах экономически мало оправдан из-за значительного износа емкостей. При использовании специальной бадьи 45 % тепла отходящего газа идет на нагрев лома и бадьи, 37 % на нагрев воды охлаждаемых элементов, 18 % теряется с газом.
Исследование, проведенное японскими металлургами, показало, что физическое тепло, накапливаемое ломом, растет прямо пропорционально температуре его подогрева. Однако с ростом температуры лома увеличивается его окисление, а следовательно, расход энергии, затрачиваемой на последующее восстановление железа. Наиболее подходящим с точки зрения суммарной экономии энергозатрат является нагрев лома до 400 500 оС, что ниже, чем типичный (около 550 оС) нагрев в шахтных печах.
Существенным фактором, который необходимо учитывать при подогреве лома, является выделение диоксинов и фуранов. Это происходит при наличии в ломе пластика, масел, красок. Нежелательный процесс развивается в интервале температур 300 1000 оС. Проблема, кстати, весьма актуальна для России, где пока отсутствуют нормы выбросов диоксинов в воздух печными установками.
Подогрев лома в шахте одновременно означает улучшение условий образования диоксинов и фуранов. Для их разрушения применяют повторный нагрев газа в камере дожигания с помощью дополнительных газокислородных горелок достаточно большой мощности, что требует дополнительно около 94 кВт . ч/т. Использование адсорбентов для очистки газа от диоксинов, фуранов и иных соединений является, видимо, достаточно эффективным приемом, но порождает проблему затрат на адсорбент и последующее его захоронение или утилизацию.
В современной практике используются различные конструктивные варианты шахтных подогревателей, в которых предусмотрена подача лома с его одновременным подогревом. При этом для подавления синтеза диоксинов и фуранов необходима достаточно высокая температура газа.
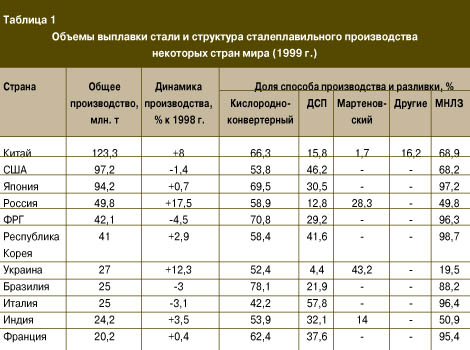
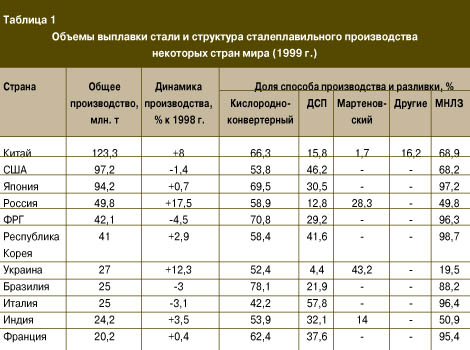 Печи с непрерывным процессом плавления. Идея непрерывного процесса плавления и постоянной работы дуг на жидкой ванне нашла свое воплощение в электропечах типа Consteel с боковой подачей лома конвейером и печи типа Contiarc с высоким двойным корпусом и верхней загрузкой лома. Практика использования таких печей на ряде зарубежных заводов показала, что по сравнению с ДСП традиционной конструкции эксплуатация агрегата Consteel требует затрат на фрагментирование лома, на термическое разложение диоксинов и фуранов в газе, отходящем из конвейерного туннеля, на обслуживание и ремонт конвейера. Особенно много вопросов вызывает надежность последнего. Но, видимо, в определенных условиях для сталеплавильщиков может быть привлекательной возможность работать на малой мощности, с большой долей стружки в завалке, практически постоянно на жидкой ванне и, следовательно, без сильного пылевыделения и с малыми уровнями фликера и шума.
Печь типа Contiarc обеспечивает большую экономию электроэнергии. Однако необходимость использовать лом мелких фракций приводит к росту затрат на выплавку стали. Кроме того, печь системы Contiarc менее приспособлена для рафинирования металла, чем ДСП традиционной конструкции или агрегат системы Consteel, и в наибольшей степени нацелена только на расплавление лома. Для более точной оценки всех преимуществ и недостатков эксплуатации печей Contiarc надо дождаться появления данных о работе второй такой установки, ввод которой в строй планировался в 2000 году.
К сожалению, многие современные технические и технологические решения, связанные с выплавкой стали в ДСП, до настоящего времени не нашли своего воплощения на российских заводах. Очевидно, что в процессе структурной перестройки металлургического производства необходимо использовать возможности эффективной замены электропечами морально устаревших мартенов.
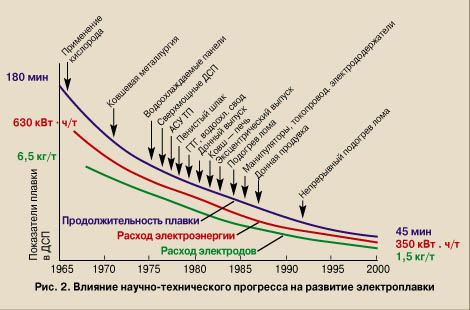 Несомненным приоритетом при выборе основного и дополнительного оборудования ДСП должна быть комплексная оптимизация работы печи, достигаемая возможно более простыми способами при высокой надежности техники и быстрой окупаемости вложений за счет снижения удельно-переменных затрат на выплавку стали и повышения производительности оборудования.
В российских условиях выбор новых, нетрадиционных конструкций печей можно рекомендовать только предприятиям, уже обладающим опытом электросталеплавильного производства. Думается, в условиях ограниченных инвестиций основное внимание при покупке дорогостоящего оборудования ДСП должно быть направлено на подбор проверенной и хорошо зарекомендовавшей себя техники, максимально простой и надежной в эксплуатации. Можно также предположить, что внедрение современных технических устройств, например, инжекционного оборудования для подачи кислорода и углеродсодержащих материалов или дожигания СО, на дуговых сталеплавильных печах заводов России даст значительный технико-экономический эффект. Имеет смысл рекомендовать применение на российских ДСП комплексов современного оборудования, например, наборов "инжектор углерода горелка-фурма инжектор кислорода для дожигания" с последующей совместной оптимизацией электрического режима и параметров использования кислорода и углеродсодержащего порошка.
При выборе конструкции печей и технологических решений, по-видимому, следует прежде всего исходить из оценки комплексного технико-экономического и экологического эффекта и ориентироваться на лучший зарубежный опыт. Заинтересованность российских металлургических предприятий в использовании ДСП должна быть поддержана национальным капиталом и правительством страны, ибо высокие экономические преимущества электроплавки бесспорны.
|