Георгий Шалаев Директор по маркетингу и продажам ОАО "Уралмаш"
Очередное заседание Межведомственной рельсовой комиссии прошло на Нижнетагильском металлургическом комбинате. Представительное собрание железнодорожников и металлургов России, Украины и Белоруссии в очередной раз обсуждало вопросы стойкости и качества рельсов, планы металлургов и железнодорожников, технические, экономические, ценовые и другие насущные проблемы. Некоторые их аспекты изложены в журнале "Металлы Евразии" металлургами (А. Дерябин, Л. Смирнов, "Деньги на рельсы!" 2000, № 3) и железнодорожниками (В. Семенов, "Качество для новых скоростей", 2000, № 5). Попытаемся изложить мнение третьей заинтересованной стороны машиностроителей ОАО "Уралмаш", которым далеко не безразличны вопросы повышения качества, увеличения объемов производства рельсов и пути развития их производства в России.
Поставщиками этой продукции являются Нижнетагильский и Кузнецкий металлургические комбинаты, имеющие возможность выпускать 1,3 1,4 млн. т объемно-закаленных рельсов в год. По оценке же заместителя министра путей сообщения В. Семенова, для удовлетворения годовой потребности железных дорог требуется не более 750 тыс. т. Однако не ясно, учтены ли при этом перспективы увеличения перевозок в связи с прогнозируемым экономическим ростом и планы создания трансконтинентальных коридоров между Европой и странами Азиатско-Тихоокеанского региона, а также между Скандинавией и Ближним Востоком (путь "Север Юг"). Между тем именно долгосрочные перспективы развития железных дорог во многом определяют объемы выпуска рельсов и, следовательно, стратегию развития производственных мощностей в металлургии и машиностроении.
Основные усилия металлургов в последние годы были направлены на улучшение качества выплавляемых сталей и заготовок для прокатки рельсов. Это благотворно повлияло на внутреннюю структуру, чистоту, механические свойства металла. Например, сегодня уровень чистоты по оксидным включениям и ударная вязкость образцов превышают мировой уровень. По мнению ученых-металлургов А. Дерябина и Л. Смирнова, этот этап работы "успешно реализован". Однако последние исследования на полигоне МПС в Щербинке, как пишет В. Семенов, выявили отставание отечественных рельсов по стойкости от лучших импортных аналогов почти в 2 раза. В чем же дело?
По нашему мнению, причина низкой стойкости рельсов российского производства в существенном отставании прокатного рельсового передела НТМК и КМК от уровня иностранных фирм, многие из которых за последние 10 15 лет уделили большое внимание именно его реконструкции. Под прокатным переделом мы понимаем существующее рельсобалочное производство (РБЦ), начиная с нагрева заготовок, прокатки и заканчивая отгрузкой термообработанных рельсов.
Технологии и оборудование рельсобалочных цехов России не претерпели принципиальных изменений с момента создания этих производств на НТМК и КМК, т. е. за последние 50 лет. Так, деформация в двухвалковых калибрах с непрямым обжатием головки рельса применяется по сей день. В то же время на многих зарубежных станах давно используются универсальные клети, основным достоинством которых является прямое обжатие головки рельса, кроме того, внедрены современные системы автоматического управления процессом прокатки, что позволяет добиваться лучших показателей по геометрии изделий.
Существенным достижением было внедрение в 60 70-е годы оборудования для объемной закалки рельсов, что позволило резко повысить их качество. Однако эта технология к настоящему времени устарела. Все более широкое применение за рубежом находят новые способы закалки, которые обеспечивают дифференцированное охлаждение различных элементов рельса и достижение в каждом из них требуемых эксплуатационных свойств. Оборудование же термоотделений на предприятиях России имеет запредельный износ и практически не обновлялось 20 35 лет.
Существенным недостатком является отсутствие в потоке РБЦ развитых систем автоматического контроля качества с паспортизацией каждого выпускаемого рельса. По данным ВНИИ железнодорожного транспорта, лучшие иностранные рельсы на полигоне в Щербинке пропустили 1000 млн. т брутто. В то же время у отечественных рельсов наметился рост их выхода из эксплуатации на ранней стадии при пропуске 50 200 млн. т брутто (при норме 500 600 млн. т). Внедрение автоматического контроля даст возможность выбраковывать на комбинате те рельсы, низкое качество которых и определяет стойкость всей партии. Наличие таких систем позволит также следить за состоянием оборудования и соблюдением технологии производства, вовремя выявлять и устранять отступления от нее и недопустимый износ рабочего инструмента.
Если проанализировать в целом последние немногочисленные приобретения рельсобалочных цехов, то, кроме строительства и недавнего пуска печи нагрева заготовок на НТМК, все остальное очень похоже на латание дыр (см. таблицу).
Стойкость рельсов обеспечивается на всех этапах технологии рельсобалочных цехов. Здесь прокатывается профиль, обеспечивается точность исполнения основных конструктивных параметров рельса, формируется прямолинейность его средней части и концов, появляются нежелательные риски и дефекты, изменяется структура стали за счет изотермической выдержки и закалки, вносятся остаточные напряжения, проверяется качество полностью готовых изделий, в том числе на наличие внутренних и поверхностных дефектов. Таким образом, оборудование и технологии прокатного передела не только определяют работоспособную конечную форму поверхности рельса, но и изменяют его внутренние параметры.
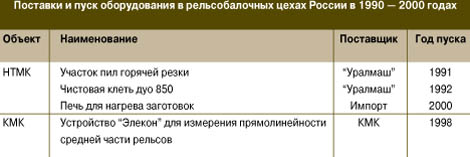 Влияние всего перечисленного на стойкость рельсов в пути представляется определяющим. Так, точность профиля и его прямолинейность способны существенно увеличить или уменьшить динамические нагрузки на рельс (особенно при скоростном движении), что напрямую влияет на развитие усталостных дефектов. Задиры и риски на рельсе являются концентраторами напряжений или, в лучшем случае, местами пониженной прямолинейности после зачистки дефектов. Точность и чистота обработки болтовых отверстий способны изменить процент выхода рельсов по концевым дефектам и т.п.
Таким образом, без коренной реконструкции отечественных рельсобалочных цехов невозможно добиться выполнения современных требований и обеспечить выпуск рельсов высшей категории качества в соответствии с новым стандартом России, который планируется ввести в действие с 1 июля 2001 года. Поэтому мы поддерживаем точку зрения МПС о необходимости разработки комплексной и поэтапной программы реконструкции отечественных рельсовых производств.
Отметим, что направления реконструкции НТМК отражены в разработанном под руководством ГНЦ РФ "Уральский институт металлов" комплексном технологическом задании. В нем предусмотрено внедрение новейших технологий на всех основных участках РБЦ: прокатка термообработка отделка контроль качества. Для реализации этих технологий ОАО "Уралмаш", имеющее богатый опыт проектирования и изготовления рельсопрокатного оборудования, готово осуществить комплексную поставку различных высокоавтоматизированных машин нового поколения: установок для гидросбива окалины; универсальных клетей, конструкция которых учитывает все особенности современной технологии прокатки; рельсоправильных комплексов, включающих горизонтальную и вертикальную роликовые правильные машины; гидравлических прессов двустороннего действия для правки концов рельсов и др.
Необходима конкретная программа действий, на первое место в которой следует поставить поэтапное перевооружение прокатного передела. При определении очередности обновления РБЦ основными факторами следует считать сохранение непрерывного производства и постепенное повышение качества и стойкости рельсов на каждом этапе реконструкции.
По нашему мнению, в сложившейся ситуации начинать целесообразно с реконструкции хвостовых частей существующих термоотделений и участков отделки, поставив основными задачами всемерное повышение прямолинейности рельсов по всей длине, увеличение доли такой продукции в общем объеме производства, организацию сортировки на разные категории качества с максимальным исключением рельсов, которые потребуют ранней замены на железной дороге. Поэтому в хвостовых частях существующих термоотделений в первую очередь следует создать линии полного автоматического контроля качества, приобрести и запустить станки по обработке торцев, закупить гидравлические прессы и установить новые рельсоправильные роликовые машины.
Работа по созданию опытного закалочного устройства с широкими возможностями должна вестись параллельно и иметь статус второй важности, ведь еще идут дискуссии, как выбирать способ закалки рельсов. Комбинатам потребуется много времени на создание опытного устройства, проведение научно-исследовательских работ, отработку технологии, выполнение испытаний опытных партий рельсов (в том числе на кольце в Щербинке), на разработку, изготовление, монтаж и доводку надежного промышленного оборудования с развитыми системами автоматизации. Поэтому, по нашей оценке, объемная закалка сохранится в промышленных объемах еще 7 10 лет.
Уверены, что деньги на российские рельсы будут найдены при настойчивости заинтересованных сторон и государственном подходе к решению проблемы. Причем роль Министерства путей сообщения как монополиста, диктующего цены, в проведении реконструкции очень велика. МПС может и должно экономически заинтересовать производителей не только в повышении качества рельсов, но и в сохранении самого рельсового производства. Так, не секрет, что НТМК серьезно нацелен на возведение стана 5000, обеспечивающего выпуск более рентабельной продукции. Реализация такого громадного проекта может отодвинуть реконструкцию рельсового производства на неопределенный срок. В таком случае за короткий срок произойдет сокращение, а то и полное исчезновение отечественного рельсового производства под давлением иностранных конкурентов.
Вопрос стоит достаточно серьезно: либо России удастся сделать рельсовое производство конкурентоспособным на мировом рынке, либо оно сожмется, как шагреневая кожа. Будущее этой отечественной продукции зависит от настойчивых и целенаправленных совместных усилий металлургов, железнодорожников, машиностроителей при поддержке Правительства РФ. Рельсовая проблема, затрагивая безопасность России, имеет государственное значение и нуждается в целевой федеральной комплексной программе, о чем пишут и авторы статей в журнале "Металлы Евразии". "Уралмаш" готов всемерно поддержать металлургов и железнодорожников и обеспечить высококачественным отечественным оборудованием рельсобалочные цехи НТМК и КМК.
|