Владимир Столяров, Юрий Морозов, Леонид Эфрон Институт качественных сталей ГНЦ РФ "ЦНИИчермет им. И.П. Бардина"
Организация производства отечественного штрипса и газопроводных труб большого диаметра является задачей федерального уровня и определяет стратегическую безопасность страны. Подходы к решению этой проблемы базируются на следующих ключевых аспектах:
создание базы для производства трубной заготовки обуславливает необходимость совершенствования марочного сортамента сталей, гарантирующих необходимые свойства проката, что, в свою очередь, требует самого современного металлургического оборудования и систем контроля качества;
трубное производство должно быть ориентировано на выпуск продукции, конкурентоспособной по качеству и размерному сортаменту.
Ситуация на металлургических предприятиях России, как показывает анализ, предопределяет два варианта решения проблемы дооснащение существующих производственных мощностей и создание новых сталеплавильных и трубных комплексов. Эти варианты не являются альтернативными, они дополняют друг друга.
В качестве базового сортамента для строительства магистральных газопроводов Западная Сибирь Европа Газпромом приняты трубы диаметром 1420 мм, составляющие более 50 % всего объема труб, используемых для этих целей. Основные толщины 15,7 мм (III IV категории) и 18,7 мм (I II категории). Неосвоенным в России сортаментом остаются трубы диаметром 530 1020 мм с толщиной стенки до 36 мм.
Повышение прочности для основного размерного сортамента труб (1420 мм) может обеспечить только замена стали с прочностью К60 сталью с прочностью К65 (при рабочем давлении 75 атм.), так как в этом случае предельно допустимой становится толщина стенки трубы в 14,3 мм. Такая замена позволяет экономить до 7 % металла. Повышение прочности труб диаметром 1420 мм других категорий (I II, ВК) не так эффективно в связи с относительно ограниченным объемом их потребления.
Современные требования к газопроводным трубам включают показатели прочности, вязкости, хладостойкости и свариваемости. Критерии механических свойств возрастают с увеличением диаметра трубопровода и рабочего давления (табл. 1).
В будущем возможен рост потребности в более высокопрочных сталях, предназначенных для труб категорий прочности Х80 и Х100. При этом должны значительно расти показатели вязких свойств (табл. 2). Правда, требования к стали Х100 являются предварительными и могут быть скорректированы по результатам исследований и анализа рабочих условий эксплуатации высокопрочных арктических трубопроводов.
Одним из ключевых качественных показателей надежности трубопроводов считается показатель вида излома образцов DWТТ, являющийся критерием предотвращения протяженных хрупких разрушений. Кроме того, весьма важен уровень вязкости при температуре эксплуатации. Требуемая хладостойкость может быть получена только с применением оптимальной технологии термомеханической прокатки. Особенно большие сложности связаны с освоением производства сталей повышенной толщины и прочности и с требованиями, касающимися особых условий эксплуатации. Выдвигается и ряд других критериев, связанных с обеспечением надежности: сплошность по результатам ультразвукового контроля, по сегрегационной однородности, по стойкости к коррозионному растрескиванию под напряжением. При разработке сталей повышенной надежности необходим учет многих факторов, связанных со структурой, механизмами упрочнения, химическим составом и чистотой.
Повышение прочности обычной стали класса выше К60 связано с дальнейшим измельчением зерна (с 7 до 2 3 мкм), что достигается переходом от традиционной ферритно-перлитной микроструктуры к ферритно-бейнитной. Для получения хорошей вязкости бейнит должен быть низкоуглеродистым, что благоприятно и для свариваемости стали.
Ужесточение требований к однородности металла, сегрегационным явлениям в осевой зоне и по всей толщине листа, сплошности проката по результатам ультразвукового контроля диктует необходимость разработки нового поколения трубных сталей с пониженным содержанием элементов, вызывающих указанные нежелательные явления.
Особую значимость в комплексе характеристик надежности трубопроводов приобрело сопротивление сталей коррозионному растрескиванию под напряжением (КРН). Исследования металла категории К56 показали преимущества технологии контролируемой прокатки с ускоренным охлаждением как экономичного способа получения дисперсной микроструктуры со значительным сопротивлением КРН. Этот фактор необходимо учитывать при разработке сталей более высоких категорий прочности, предназначенных для эксплуатации на коррозионно-активных участках магистралей.
В целом разработка сталей для газопроводных труб в Институте качественных сталей ГНЦ "ЦНИИчермет им. И.П. Бардина" производится в рамках следующей концепции:
снижение содержания углерода;
повышение степени чистоты по вредным примесям;
рациональное микролегирование (при термомеханической прокатке наилучшим образом подходит ниобий);
применение термомеханической прокатки с ускоренным охлаждением для эффективного измельчения зерна и отказ от термической обработки.
В рамках этого же направления проводится замена устаревших нормализуемых сталей типа 17Г1С-У на современные, той же категории прочности с повышенной хладостойкостью, свариваемостью и сегрегационной однородностью, получаемые контролируемой прокаткой. Необходимость замены продиктована тем, что стали типа 17Г1С не удовлетворяют новым требованиям по низкотемпературной ударной вязкости, свариваемости, обладают высокой критической температурой хрупкого разрушения. В то же время на российских заводах существенно повысилось металлургическое качество металла (в частности, снижен уровень вредных примесей) и осваиваются прогрессивные технологии термомеханического упрочнения в процессе горячей деформации. Все это позволяет рекомендовать потребителям новые высоконадежные низкоуглеродистые свариваемые марки сталей с экономичным микролегированием. Институтом проводятся также работы по совершенствованию состава сталей категорий до Х70-Х80 и разработка сталей класса Х100.
Обобщая, можно сделать вывод: трубные стали улучшаются одновременным повышением прочности и вязкости, в первую очередь за счет непрерывного измельчения зерна.
Теперь об уровне технологии и оборудования действующих сталеплавильных предприятий России.
На стане 2000 ОАО "Северсталь" возможно производство сталей для прямошовных труб диаметром 530 мм категории прочности до К60 с толщиной стенки до 12 мм. При производстве листа для спиральношовных термообрабатываемых труб (особенно повышенных толщин до 15,7 мм) необходимо скорректировать технологию контролируемой прокатки для подготовки структуры под последующую термообработку и выбрать марку стали для повышения прокаливаемости.
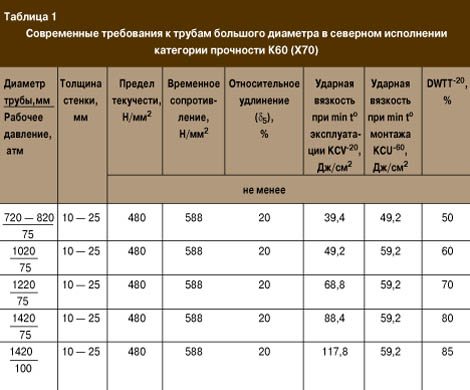 На стане 2800 принципиально возможно при определенных условиях производить прокат для труб диаметром 720 и 820 мм с толщиной стенки до 12 мм категорий прочности К52 К60. При этом необходимо использовать технологическую схему контролируемой прокатки с завершением деформации при температурах до 780 оС и модифицировать состав стали. В этом случае термическая обработка не требуется. Реконструкция стана 2800, предусмотренная руководством ОАО "Северсталь" (усиление чистовой клети и оснащение установкой ускоренного охлаждения), позволит существенно расширить возможности в производстве качественного проката для труб.
Реконструкция стана 5000 (листоотделка, ультразвуковой контроль, установка ускоренного охлаждения и др.) и проведение цикла научно-исследовательских работ позволят создать и освоить технологию производства трубного проката категорий прочности до Х80 для изготовления труб диаметром 1020 и 1420 мм с толщиной стенки до 36 мм.
В активной стадии реконструкции находится ОАО "НОСТА" предприятие, поставляющее листовой штрипс на ведущие трубные заводы России. Здесь осваиваются современные технологии обеспечения металлургического качества сталей, модернизируется оборудование. Совместно с ЦНИИчерметом разработаны и внедрены технологии, позволяющие получать листовой прокат, удовлетворяющий современным требованиям, внепечная обработка для получения стали с пониженным содержанием серы и контролируемая прокатка на стане 2800 с температурой окончания деформации 780 оС. Освоено производство стали марок 12Г2СБ (К56), 10Г2СФБ (К60) для магистральных газонефтепроводов в северном исполнении диаметром 530 1220 мм с толщиной стенки 8 25 мм. Разработаны новые низкоуглеродистые природнолегированные стали марок 09ГНФБ-ПЛ (К56) и 08Г1НФБ-ПЛ (К60).
После завершения в 2001 году реконструкции, включающей монтаж второй установки печь-ковш и слябовой МНЛЗ в электросталеплавильном цехе, новой чистовой клети стана 2800, установки ускоренного охлаждения, правильной машины и ультразвукового контроля, ОАО "НОСТА" получит возможность производить высококачественный прокат для труб диаметром до 1420 мм (в двухшовном варианте) категории прочности до К65 (Х80) с толщиной стенки до 20 мм.
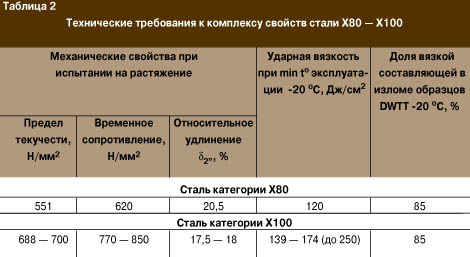 К освоению качественных марок стали для прямошовных и спиральношовных труб подключилось ОАО "Магнитогорский металлургический комбинат". Совершенствование марочного сортамента, отработка технологии выплавки, глубокой десульфурации на установке печь-ковш, усовершенствование технологии непрерывной разливки и контролируемой прокатки на стане 2000 позволит производить штрипс с повышенными перспективными требованиями для труб ОАО "Производственное объединение "Волжский трубный завод".
В России в настоящее время имеются мощности по производству труб диаметром 530 1420 мм, способные в значительной степени обеспечить потребность при строительстве и обновлении газопроводов и полностью нефтепроводных транспортных систем.
ОАО "Челябинский трубопрокатный завод" (ЧТПЗ), обладая возможностью изготавливать трубы диаметром до 1220 мм с использованием прессовой формовки, осваивает уникальный процесс локальной термомеханической обработки шва (ЛТМО), позволяющий не только повысить уровень механических свойств сварного соединения, но и существенно улучшить геометрические характеристики трубы. Организация производства принципиально новых труб с поставкой штрипса с ОАО "НОСТА" представляется в настоящее время близкой перспективой. Планируемая реконструкция, предусматривающая производство двухшовных труб диаметром 1420 мм с последующей ЛТМО, существенно расширит номенклатуру и технологический потенциал предприятия. Введение в 2000 году участка трехслойного полимерного покрытия повысило конкурентоспособность челябинских труб. Используя качественный штрипс ОАО "НОСТА", на ЧТПЗ могут производить газопроводные трубы, соответствующие современным требованиям рынка.
Значительный прогресс достигнут в последние годы в ОАО "ПО "Волжский трубный завод": пущен участок полимерного покрытия, освоены технологии производства труб из рулонной стали повышенной толщины, с положительным результатом проведена серия испытаний труб у потребителей. При небольших капиталовложениях возможна организация массового производства труб диаметром 1420 мм, длиной до 18 м, с толщиной стенки 15,7 18,7 мм из сталей классов прочности К60, К65.
При участии ЦНИИчермета отработана технология производства листового проката из стали марки 10Г2ФБ в толщинах 15,7 18,7 мм повышенной сплошности, прочности и плоскостности, без дефектов, вызывающих боковые поры при сварке. На стане 2520 изготовлены промышленные партии спиральношовных труб диаметром 1420 мм. Результаты испытаний свидетельствуют о том, что эти волжские трубы по своим эксплуатационным характеристикам соответствуют требованиям, предъявляемым к газопроводным трубам класса прочности К60 на рабочее давление до 75 атм. в северном исполнении с минимальной температурой строительства до -60 оС и температурой эксплуатации до -15 оС.
Большим потенциалом трубного производства обладает ОАО "Выксунский металлургический завод", имеющее монопольную возможность изготавливать трубы диаметром до 1020 мм с толщиной стенки до 32 мм. С пуском участка покрытий продукция предприятия способна в большей степени удовлетворить требования потребителей, причем реконструкция стана горячей прокатки 5000 ОАО "Северсталь" рассчитана на обеспечение ВМЗ штрипсом современного качества и требуемой толщины.
Таким образом, при необходимом дооснащении оборудованием и обеспечении качественным штрипсом российские трубные заводы могут выпускать продукцию на уровне современных требований.
Институтом качественных сталей обобщен передовой технологический опыт и составлен перечень мероприятий, необходимых для организации производства газопроводных труб нового поколения. В предложениях содержится информация для выполнения проектных работ по компоновке, составу и параметрам технологического оборудования для сталеплавильного и прокатного переделов. Разработано технологическое задание на проектирование комплекса по производству широкоформатного высокопрочного толстолистового проката и труб большого диаметра (1020 1420 мм) длиной 18 м с полимерным антикоррозионным покрытием для магистральных газопроводов. Задание подготовлено с учетом отечественного и зарубежного опыта и содержит основные требования к технологии и оборудованию комплекса с толстолистовым станом 5000 и трубосварочным станом 1420. Учтены перспективные критерии качества. Необходимость высокой конструкционной и эксплуатационной надежности газопроводов при давлении 10 МПа и более в суровых климатических условиях диктует жесткие требования по уровню вредных примесей и газов в металле. Металлургическая часть комплекса должна обеспечивать производство сталей заданного состава с ограничением содержания серы до 0,001 0,002 %, фосфора менее 0,015 %, азота менее 0,007 %, водорода менее 4 ppm в кристаллизаторе и менее 2 ppm при обработке на вакууматоре, кислорода до 0,003 0,004 %.
Для прокатки на толстолистовом стане 5000 должны использоваться непрерывнолитые слябы, а разливка осуществляться на современной установке, обеспечивающей минимальную структурную и сегрегационную неоднородность и загрязненность неметаллическими включениями, высокое качество поверхности.
На стане 5000 основным технологическим процессом станет термомеханическая обработка с использованием различных режимов охлаждения готовых листов, включая ускоренное. Применение комплексной технологии в сочетании с рациональным химическим составом и высокой чистотой металла позволит получать штрипс категорий прочности до Х100, в том числе с высокой хладостойкостью и стойкостью в среде агрессивного газа.
Для реализации такой технологии при прокатке листов шириной до 4600 мм клети стана 5000 должны быть рассчитаны на усилие прокатки 10 12 тыс. т и обеспечивать высокую точность размеров по толщине, ширине и плоскостности раската. Отделочное оборудование предусматривает возможность использования термических средств (в потоке и вне его) и жесткий контроль за качеством готовой продукции, включая 100 %-ный ультразвуковой контроль по всей площади листов. Высокое их качество по сплошности обеспечивается получением низкого содержания водорода и других неметаллических включений, а также применением комплекса специальных технологических операций.
Для производства толстостенных одношовных сварных труб рекомендован метод формовки труб UO-образного прессования. Ориентировочная производительность трубного цеха 1 млн. т в год.
Подведем итоги. Действующие производственные мощности при условии их дооснащения и реконструкции позволяют изготавливать значительную часть трубной продукции применяемого сортамента. Однако с учетом роста требований к качеству и служебным свойствам труб и новых проектов транспортировки нефти и газа необходимо создать в России современный металлургический комплекс по производству газопроводных труб нового поколения.
|