Анатолий Дерябин Академик РИА, заместитель сопредседателя Межведомственной рельсовой комиссии
Леонид Смирнов Член-корреспондент РАН, генеральный директор ГНЦ РФ "Уральский институт металлов"
Россия давно признана мощной железнодорожной державой. В настоящее время протяженность железных дорог составляет 86 тыс. км, а на долю МПС приходится более 85 % грузооборота страны. Многие предприятия, в том числе металлургические как грузополучатели руды, окатышей, флюсов, угля, ферросплавов и как грузоотправители металлопродукции, кокса, шлаков и пр., практически не имеют альтернативы в выборе транспорта. Такое положение предопределило роль МПС как монополиста и в обеспечении перевозок, и в потреблении металлопродукции железнодорожного назначения рельсов, колес, бандажей, осей, подкладок, накладок и других элементов верхнего строения пути. Причем железнодорожное ведомство занимает довольно жесткую позицию в отношениях с заводами-изготовителями.
До начала 90-х годов потребности МПС в железнодорожных рельсах обеспечивали в основном три предприятия Нижнетагильский и Кузнецкий металлургические комбинаты и завод "Азовсталь", которые ежегодно производили по 700 тыс. т каждый. В последнее десятилетие в условиях экономического кризиса ситуация коренным образом изменилась. Из-за уменьшения грузооборота заказы МПС на рельсы резко сократились. Статистика свидетельствует: за последние 4 года НТМК и КМК, имея суммарную производственную мощность на 1300 1400 тыс. т термоупрочненных рельсов, выпускали их в 2 3 раза меньше (табл. 1). А МПС в это время "проедало" государственные резервы рельсов и диктовало очень низкие цены на рынке, которые порой оказывались ниже себестоимости. НТМК и КМК попали в крайне тяжелую ситуацию.
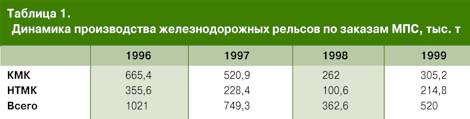 Определенное влияние на конъюнктуру оказали планы строительства высокоскоростной магистрали Санкт-Петербург Москва. МПС под предлогом того, что большие скорости требуют лучшего качества пути, начало приобретать рельсы за рубежом.
Проблема отношений двух отраслей не нова. Она постоянно обсуждается на ежегодных заседаниях Межведомственной рельсовой комиссии по улучшению качества железнодорожных рельсов и рельсовых скреплений, которая существует уже 118 лет. Металлурги и железнодорожники по-деловому решают проблемы отечественного производства, улучшения качества рельсов. Их надежность определяется условиями и качеством эксплуатации с учетом высокой грузонапряженности, сложного рельефа и наличия климатических зон, где зимние температуры опускаются ниже минус 40о С. Требования железнодорожников повысить качество рельсов до уровня лучших зарубежных аналогов побуждают металлургов принять необходимые меры.
По данным ВНИИЖТ, которые приводились на недавнем заседании Рельсовой комиссии, эксплуатационная стойкость французских, японских и австрийских рельсов, испытанных на экспериментальном кольце в Щербинке, почти вдвое выше, чем отечественных. А ведь в 60-е годы после внедрения на НТМК объемной закалки наша продукция превосходила по качеству многие зарубежные аналоги. Но затем технологические новшества, если не считать различные варианты раскисления стали комплексными сплавами, в производство не внедрялись. К середине 90-х годов уровень технологических операций по выплавке, внепечной обработке, разливке, термообработке, прокатке и отделке рельсов, контролю качества на НТМК и КМК заметно отстал от зарубежного.
В результате загрязненность рельсов неметаллическими включениями и газами оказалась в 1,5 4 раза выше, чем у импортных образцов. Выявились значительные отклонения по геометрическим характеристикам, в частности, по продольной прямолинейности и концевой кривизне, асимметрии и точности исполнения профиля. Если к этому добавить сравнительно малые объемы работ по шлифовке рельсов в пути, то можно понять и причины меньшего срока службы наших рельсов по сравнению с зарубежными. Правда, по уровню механических свойств они не уступают, а по отдельным характеристикам, например по ударной вязкости, даже превосходят импортные рельсы массового производства (табл. 2).
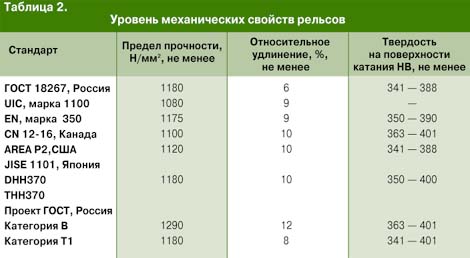 Проект нового национального стандарта, разработанный ГНЦ РФ "УИМ", ВНИИЖТ, НТМК и КМК, предусматривает существенное повышение требований к качеству рельсов текущего производства и выпуск рельсов, отвечающих уровню международных стандартов и нормам ведущих стран-производителей.
Критически оценивая сложившуюся ситуацию, НТМК еще в 1992 году разработал и начал реализовывать программу реконструкции и развития комбината по комплексному технологическому заданию, генеральным разработчиком которого был Уральский институт металлов. Первый этап, которым предусматривалось обновление сталеплавильного производства, успешно реализован. С 1997 года комбинат перешел на массовое производство рельсов из непрерывнолитых заготовок кислородно-конвертерной стали, которую перед разливкой подвергают эффективной внепечной обработке. Последняя включает операции рафинирования твердыми шлакообразующими смесями и продувку аргоном на установке печь ковш, а затем вакуумирование на установке циркуляционного типа. В результате содержание кислорода в рельсах удалось снизить в среднем до 20 ppm, в то время как в выпущенных из мартеновской стали было 80-90 ppm. Как следствие, резко уменьшилась загрязненность строчечными оксидными и сульфидными включениями. Сейчас рельсы НТМК по оксидным включениям близки к японским, несколько уступают им по загрязненности пластичными силикатами, но имеют меньший балл по недеформируемым силикатам.
Совершенствование технологии производства стали на НТМК позволило повысить и другие показатели металлургического качества рельсов:
уменьшилась степень их пораженности поверхностными дефектами сталеплавильного происхождения, в результате чего выход рельсов длиной 25 м возрос почти до 90 %, а рельсов 1 класса до 85,6 %;
уменьшилась пораженность дефектами макроструктуры;
уменьшилась флокеночувствительность за счет снижения содержания водорода в стали перед разливкой до 1,5 ppm;
повысилась ударная вязкость термоупрочненных рельсов в среднем на 0,3 кгс . бм/см2 и соответственно снизилась на 15 20 % отсортировка их по этому показателю во II сорт.
Оценивая нынешний технический уровень выплавки рельсовой стали, можно констатировать, что НТМК вышел на уровень мировых достижений.
Из многочисленных вариантов выплавки рельсовой стали, длительное время использовавшихся для производства рельсов I группы ГОСТ 24182, сейчас на НТМК применяют технологию, при которой для модифицирования используют кальций, а для микролегирования ванадий. Этот вариант оказался наиболее эффективным и с технологической, и с экономической точек зрения, так как обеспечивает наибольшее повышение эксплуатационной стойкости рельсов и позволяет использовать для микролегирования ванадий из промежуточных продуктов, в частности, природнолегированного ванадиевого чугуна и конвертерного ванадийсодержащего шлака, получаемых на самом комбинате при переработке железорудного сырья Качканарского месторождения. В последнее десятилетие НТМК производит рельсы только из ванадийсодержащей стали. Известно, что совместное присутствие ванадия и азота повышает ударную вязкость рельсов при отрицательных температурах, обеспечивая безопасность движения поездов в условиях, когда температура снижается до минус 40о С и ниже.
Тем не менее технический уровень прокатки, термической и механической обработки и контроля качества рельсов на Нижнетагильском комбинате пока заметно отстает от зарубежных достижений и не позволяет обеспечить геометрическую точность, в частности, по продольной и концевой кривизне, по исполнению профиля. Поэтому здесь продолжается реконструкция рельсового производства, согласованная с МПС. Для этого наш институт, который является ведущей организацией по повышению качества металлопродукции для железнодорожного транспорта, с участием ВНИИМТ, НИИтяжмаша, ВНИИЖТ, УГТУ-УПИ и других научных учреждений завершает разработку комплексного технологического задания. Реализация намеченной программы позволит поднять качество рельсов до уровня лучших зарубежных аналогов, что сделает тагильскую продукцию конкурентоспособной на мировом рынке.
На Кузнецком металлургическом комбинате, где длительное время не проводилась модернизация сталеплавильного производства, проблема повышения металлургического качества рельсов решалась в основном путем совершенствования технологии раскисления стали. Из-за финансовых трудностей комбинат постепенно снизил объем производства рельсов I группы из ванадийсодержащей стали и перешел в основном на производство рельсов Р65 СВ. Благодаря совершенствованию технологии выплавки стали качество рельсов повысилось. Рельсы категории СВ удачно соединили в себе преимущества I группы по характеру загрязненности оксидными включениями и II группы по повышенному уровню ударной вязкости.
На примере этой технологии была наглядно показана целесообразность и возможность использования алюминия для раскисления рельсовой стали, определены его оптимальные концентрации, при которых достигается высокий уровень ударной вязкости и отсутствуют включения глинозема, а неметаллические примеси представлены более благоприятными с эксплуатационной точки зрения алюминатами кальция. На этом основании в проекте нового национального стандарта на железнодорожные рельсы теперь допускается использование алюминия для раскисления стали. Предложены четкие требования по уровню загрязненности рельсов включениями, но не прописываются, как раньше, технические приемы его достижения.
При переходе от рельсов I группы к рельсам категории СВ содержание кислорода уменьшилось с 85 до 45 50 ppm. Однако достичь уровня 10 20 ppm кислорода, который обеспечил бы необходимое металлургическое качество рельсов без вакуумирования стали, подобным образом невозможно. Это наглядно подтвердил опыт НТМК, где обработка на установке печь ковш уменьшает содержание кислорода в рельсах из кислородно-конвертерной стали в среднем с 85 до 50 ppm, т. е. до уровня, достигнутого и на КМК.
Учитывая изношенность мартеновского цеха и необходимость эффективной внепечной обработки, перспективы получения высококачественной рельсовой стали на КМК следует связывать с ее выплавкой в электропечах. Для этого надо решить проблему отсечки шлака и эффективной внепечной обработки, обязательно включающей операцию вакуумирования. Лишь при этом условии КМК способен по металлургическому качеству рельсов выйти на мировой уровень.
В связи с предстоящей разработкой Чинейского месторождения ванадийсодержащих титаномагнетитов и поставками этого сырья на КМК здесь открываются перспективы выплавлять ванадийсодержащий чугун. Уральский институт металлов совместно с комбинатом предварительно опробовали выплавку в электропечи ванадийсодержащей рельсовой стали, в которой выше содержание азота, что позволяет с меньшими затратами получать рельсы низкотемпературной надежности. Это исключительно важно, поскольку КМК поставляет рельсы в основном в восточные районы России.
Если НТМК в последние годы сделал рывок по улучшению металлургического качества рельсов, то КМК опробовал и внедрил ряд рекомендаций, которые заметно улучшили геометрическое качество. На комбинате разработано оригинальное устройство "Элекон" для контроля продольной прямолинейности рельсов в технологическом потоке. В результате до 80 % термоупрочненных рельсов имеют теперь отклонения от прямолинейности по головке катания менее 0,3 мм на базе 1,5 м, что отвечает требованиям для скоростного смешанного движения.
Кузнецкий металлургический комбинат определил на ближайшие 3 года мероприятия по техническому перевооружению рельсового производства, отдав приоритет модернизации сталеплавильного передела. Таким образом, оба российских производителя рельсов имеют четкие программы действий. Условия для реконструкции сегодня более благоприятны. В январе МПС после длительных переговоров с металлургами подняло цены на рельсы практически вдвое, определив уровень доплаты за повышение качества. Да и заказ увеличило до 700 750 тыс. т в год. Но этого мало. Учитывая стратегическую значимость производства рельсов, было бы целесообразно включить эту продукцию в перечень государственных заказов, а для осуществления реконструкции рельсового производства на НТМК и КМК выделить льготные кредиты. Проблема заслуживает того, чтобы решать ее на государственном уровне.
|