Николай Целиков Заместитель директора ВНИИМЕТМАШа
Создание промышленной технологии непрерывного литья тонких слябов существенно расширило продуктовые возможности мини-металлургии за счет рентабельного производства листового проката. Технические достижения в металлургической технологии способствовали оптимизации размеров мини-заводов. Сегодня, например, для эффективного производства стальной полосы экономически выгоден годовой объем выпуска не менее 1 млн. т. Уже появились предприятия этого типа с годовой мощностью 2 млн. т и более.
В мировой практике мини-заводы нередко рассматриваются как особая разновидность черной металлургии с вполне сформировавшейся технологической, организационной, сырьевой и продуктовой спецификой. Но в то же время нельзя не признать, что в обозримой перспективе они по-прежнему будут играть роль предприятий, дополняющих традиционное производство черных металлов в составе комбинатов с полным металлургическим циклом.
К сожалению, и в бывшем Союзе, и теперь в России идея создания мини-заводов встречала и встречает, мягко говоря, прохладное отношение. Считается, что эта идея подспудно направлена против наших металлургических гигантов. Сейчас дискуссия приняла еще более острый характер, так как впрямую касается выбора приоритетов развития отрасли на ближайшее будущее.
Безусловно, проблемы выбора технологических схем и размещения предприятий играют очень важную роль как факторы, определяющие основные направления инвестиционной политики в металлургическом комплексе. Однако, на наш взгляд, подобные дискуссии неплодотворны. Это все равно, что обсуждать, целесообразно ли выпускать автомобили "Газель", если производятся КамАЗы.
В России одним из научных центров, занятых разработкой концепции и практической схемы металлургических мини-заводов на базе производственного литейно-прокатного комплекса, является ВНИИМЕТМАШ. В этом комплексе оптимально скомпонованы процессы непрерывного литья и прокатки металла. На всех стадиях передела предполагается использование прогрессивных технологий и агрегатов. Как правило, такой комплекс включает в себя электродуговую печь, машину непрерывного литья и прокатный стан. Сортамент выпускаемого проката имеет специализированный характер, ориентирован в первую очередь на удовлетворение потребностей регионального рынка.
Разработано несколько технологических схем мини-заводов для производства сортового проката, катанки, помольных шаров, труб и листа в зависимости от производительности, сортамента, марочного состава выпускаемой продукции и других параметров, отвечающих различным требованиям заказчика. Эти наработки позволили нам подготовить конкретные предложения по созданию мини-заводов для регионов России, стран СНГ, стран Азии и Африки с учетом их специфики.
Для российской металлургии в нынешней экономической ситуации, по нашему мнению, наибольший интерес представляют разработки ВНИИМЕТМАШа, касающиеся, главным образом, мини-заводов для получения арматуры, мелкого сорта и проволоки с годовой производительностью ориентировочно от 50 до 200 300 тыс. т. Осуществление этих проектов не требует крупных затрат, они реальны для инвестирования, могут достаточно быстро окупаться и дают возможность получать конкурентоспособную продукцию.
Основополагающей в принципиальной схеме мини-завода является идея прямого совмещения литья и прокатки непрерывного процесса, начиная от разливки стали и кончая прокаткой готовой продукции, например, арматуры, проволоки, мелкого сорта. Такая схема дает возможность значительно сократить потери тепла, максимально использовать при прокатке первородное тепло расплавленного металла, полностью механизировать и автоматизировать процесс литья и прокатки, исключить склад литых заготовок, нагревательные печи, стабилизировать процесс прокатки и т.д. Работая над реализацией этой идеи, ВНИИМЕТМАШ пришел к принципиально новым решениям как в литейном, так и в прокатном оборудовании.
Литейно-прокатный агрегат прямого совмещения процессов непрерывной разливки и прокатки, предназначенный для получения катанки из труднодеформируемых сталей, более 10 лет эксплуатируется на заводе АО "Электросталь". Впервые в мире в промышленном масштабе осуществлена технология, при которой цикл от жидкого металла до готового проката замкнут в единую непрерывную линию. Агрегат состоит из МНЛЗ радиального типа, индуктора для выравнивания температуры по сечению слитка, планетарного стана с задающей клетью, тянущих роликов, обеспечивающих натяжение в выходящей заготовке, летучих ножниц для отрезки переднего конца, группы клетей продольной прокатки и моталок.
Основные трудности при совмещении процессов непрерывной разливки стали и прокатки возникают из-за несовпадения скорости литья, составляющей 3 3,5 м/мин, и скорости входа заготовки в прокатный стан 12 15 м/мин. Примерно так же соотносятся и производительности одноручьевой машины и прокатного стана. Преодолеть эти проблемы в данном агрегате удалось благодаря применению планетарного стана конструкции ВНИИМЕТМАШа, позволяющего вести обжатие заготовки в двух взаимно перпендикулярных плоскостях. Рабочие валки установлены в четырех кассетах, связанных между собой зубчатыми передачами. Двигаясь по орбитам, каждая пара валков обжимает заготовку то в одной, то в другой плоскости. Объем металла, попадающего в зону деформации, зависит от скорости разливки и скорости вращения кассет с рабочими валками. Благодаря высокой частоте обжатий в единицу времени и их всестороннему объемному воздействию величины обжатий достигают 97 %, что соответствует 33-кратной вытяжке даже при прокатке труднодеформируемых сплавов.
В условиях завода "Электросталь" труднодеформируемые сплавы обычно обрабатывались в несколько переделов, связанных с отжигом, зачисткой металла и другими операциями, на что уходило несколько недель. Теперь время выполнения заказа сократилось до нескольких часов.
Новым этапом в реализации идеи мини-завода является проект литейно-прокатного комплекса, разработанный для ПО "Усольмаш" и предназначенный для производства арматурного профиля № 12-28, круглого профиля диаметром 12 48 мм и эквивалентных им по площадям полос и шестигранников, уголкового профиля с размерами полок до 40 мм при общем объеме производства до 100 тыс. т в год. Предусмотрена также установка за черновой группой клетей стана для прокатки шаров диаметром от 80 до 100 мм.
Основой комплекса является непрерывный мелкосортный стан производительностью до 200 тыс. т в год, включающий черновую промежуточную и чистовую группу компактных клетей. За счет гибкого выбора технологических схем удалось решить главную проблему согласовать скорости непрерывной разливки и прокатки металла.
Удачная конструкция и компоновка стана позволяют рекомендовать его для реконструкции действующих прокатных цехов. В настоящее время на российских заводах эксплуатируются около 15 морально и физически устаревших, требующих замены мелкосортных станов со средним объемом годового производства от 85 до 200 тыс. т.
В работе по реализации идеи мини-заводов ВНИИМЕТМАШ старается использовать собственные разработки машин и агрегатов различных переделов. Так, для проекта литейно-прокатного комплекса производительностью 80 тыс. т по заказу ПО "Усольмаш" был использован опыт института по проектированию и внедрению МНЛЗ горизонтального типа. Применение такой машины позволяет компактно разместить комплекс в существующем здании без увеличения его высоты, обеспечить наилучшие возможности для разливки легированных и инструментальных сталей, уменьшить капитальные вложения.
Другая модификация литейно-прокатного комплекса базируется на использовании нового технологического процесса совмещения поперечной (винтовой) и продольной прокатки. Разработки и исследования, проведенные во ВНИИМЕТМАШе на опытно-промышленном агрегате, показали, что применение такого процесса в составе мелкосортного стана позволяет уменьшить металлоемкость оборудования, длину стана и занимаемую им площадь, улучшить температурный режим прокатки, обеспечить необходимое качество выпускаемой продукции, сократить энергоемкость процесса и приблизить их к показателям высокопроизводительных сортовых станов. При использовании на стане квадратных заготовок перед клетью винтовой прокатки дополнительно устанавливаются две формообразующие двухвалковые клети для придания заготовке круглого сечения.
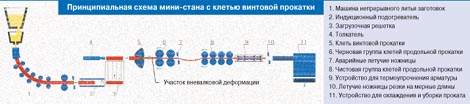 В одной трехвалковой клети винтовой прокатки может осуществляться обжатие заготовки с вытяжкой 6 8, что эквивалентно установке 6 8 клетей продольной прокатки. На участке прокатки осуществляется совмещение в одном технологическом процессе поперечной и продольной прокатки.
Участок продольной прокатки выполняется по наиболее простой схеме, т.е. с установкой только 6 10 горизонтальных рабочих клетей, расположением их с минимальным межклетьевым расстоянием, с осуществлением в них прокатки по системе "овал-круг", с кантовкой на 90о раскатов овального сечения и с незначительным натяжением. Такое решение обеспечивает минимальную металлоемкость стана и не требует большой высоты цеха. В составе участка продольной прокатки рекомендуется установить горизонтальные двухвалковые клети предварительно напряженной бесстанинной конструкции с несколькими калибрами на бочке валка, оснащенные индивидуальным приводом валков от электродвигателя постоянного тока.
Существуют и другие разработки нашего института в этой области. Однако возникает вопрос, насколько актуальны сейчас предложения по созданию новых металлургических производств, когда мощности большинства российских заводов используются менее чем на 50 %?
Большинство отечественных металлургических предприятий имеет высокие удельные расходы материалов и энергоносителей на тонну выпускаемой продукции в сравнении с мировыми показателями. В России по-прежнему мала доля стали, выплавляемой в конвертерах и электродуговых печах, подвергающейся внепечной обработке, разливаемой на МНЛЗ; большинство мелкосортных станов спроектировано более 40 50 лет назад и т.д. Негативные последствия оказывает также концентрация огромных объемов производства на крупных комбинатах с жесткой их специализацией и недостаточно развитым сортаментом выпускаемой продукции, что обуславливает необходимость дальних перевозок с соответствующим увеличением стоимости. Существуют серьезные экологические проблемы как следствие работы этих заводов. Поэтому мы считаем, что дальнейшее развитие металлургии в России должно идти по двум направлениям. Первое реконструкция и реструктуризация действующего производства на базе новых разработок в области совершенствования существующих машин и технологий. Второе строительство мини-заводов на базе принципиально новых технологий и машин.
Сейчас на территории России действует около 15 металлургических заводов, имеющих годовую производительность от 80 до 200 тыс. т, но эти предприятия не укладываются в современное понятие "мини-завод", так как имеют устаревшую технологию на всех переделах (мартеновское производство, разливка в изложницы, прокатка на станах устаревшей конструкции). Неудивительно, что произведенная здесь продукция оказывается неконкурентоспособной.
По нашему мнению, успех может быть достигнут путем строительства заводов небольшой или средней мощности с учетом новейших достижений науки и техники. Мы предлагаем обратиться к созданию мини-заводов или на базе существующих старых металлургических заводов небольшой мощности, или к строительству новых. Причем это может быть и площадка крупного машиностроительного предприятия, имеющего собственное литейно-заготовительное производство, а следовательно, готовые инженерные коммуникации и пригодные для дальнейшего использования здания. Кроме того, такие заводы, как правило, расположены в непосредственной близости к источникам металлолома и потребителям готовой продукции, им легче ориентировать сортамент на конкретного заказчика, значительно сокращая объем перевозок.
Как показывают проведенные нами расчеты и накопленный в мире опыт, при сооружении современного мини-завода на 1 т продукции требуется меньше производственных площадей в 2,5 раза, оборудования в 3 раза и мощностей электроэнергии в 1,5 раза. Удельные капитальные затраты на строительство комплекса производительностью 100 200 тыс. т мелкого сорта в год в зависимости от степени использования имеющихся зданий и сооружений в 2 5 раз меньше аналогичных показателей для металлургических комбинатов с полным циклом.
Надо также отметить, что при сравнении удельных показателей агрегатов большой и малой единичной мощности обычно исходят из предпосылки их стопроцентной загрузки. Однако в реальности при неполной загрузке агрегатов экономические показатели резко начинают падать, а при загрузке менее 60 % производство в большинстве случаев становится убыточным. В этом смысле агрегаты меньшей мощности более гибки, проще перестраиваются и более мобильно реагируют на изменение портфеля заказов. Окупаемость таких комплексов составляет 2,5 3,5 года.
По нашему мнению, удачно найденные технологические схемы российских мини-заводов позволят этим предприятиям сыграть заметную роль в структурной перестройке черной металлургии, будут способствовать росту эффективности производства и укреплению позиций отрасли на рынке металлопродукции.
|