Олег Стеклов Доктор технических наук, профессор Российский государственный университет нефти и газа им. И.М. Губкина
Один из существенных аспектов технической и экологической безопасности заключается в старении, коррозии потенциально опасных конструкций. Прежде всего несколько цифр. Общий действующий металлофонд Советского Союза составлял 1,6 млрд. т, в том числе 750 млн. т в промышленности, 400 млн. т на транспорте, 150 млн. т в сельском хозяйстве. При этом в России свыше 800 млн. т составляют несущие сварные конструкции. Еще одна немаловажная подробность: 40 50 % машин и сооружений работают в агрессивных средах, 30 % в слабоагрессивных, и только около 10 % не требуют активной антикоррозионной защиты.
В начале 90-х годов степень удовлетворенности страны основными средствами защиты была существенно ниже необходимой. В частности, потребность в лакокрасочных покрытиях и ингибиторах удовлетворялась приблизительно на треть, в защите готового металлопроката, например труб с покрытиями, менее чем на 20 %. Эти обстоятельства приводят к огромным потерям от коррозии: 22 23 % от всего проката, производимого за год, и примерно 12 % от национального дохода. Наибольшие потери от коррозии несут топливно-энергетический комплекс 20 %, сельское хозяйство 20 %, химия и нефтехимия 15 %.
В настоящее время проблема коррозии усугубляется резким старением, физическим и моральным износом основного металлофонда, совершенно недостаточной степенью возобновляемости и реновации (табл. 1). Большая часть сварных конструкций выработала плановый ресурс на 50 70 %. Значительная часть сооружений вступает в период интенсификации отказов. Исходя из экономической ситуации в России, начало XXI века будет отличаться приоритетом реновации металлофонда перед новым строительством как комплекса технологических, конструкторских и организационных мероприятий, направленных на увеличение ресурса реновируемого объекта или его составляющих, на использование по новому назначению либо вторичное использование конструкционного материала.
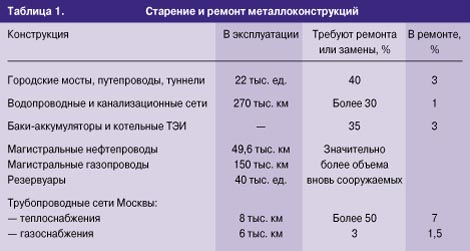 Нефтегазовые сооружения (трубопроводные, магистральные и промысловые системы, резервуары, морские нефтегазовые платформы, несущие конструкции нефтеперерабатывающих заводов и т.д.) представляют из себя сложные крупногабаритные сварные геотехнические системы, эксплуатируемые в условиях воздействия углеводородных продуктов и коррозионных сред. Их металлофонд близок к 1/5 от общего металлофонда. Большая часть сооружений выработала плановый ресурс на 60 70 %. 25 % газопроводов работают более 20 лет, 40 % 10 20 лет, а 5 % вообще превысили нормативный рубеж 33 года.
По магистральным нефтепроводам показатели тоже неутешительны: срок их эксплуатации составляет: свыше 30 лет 26 %, от 20 до 30 лет 30 %, от 10 до 20 лет 34 %, до 10 лет только 10 %. К 2000 году доля нефтепроводов с возрастом более 20 лет составит 73 %, а более 30 лет 40,6 %. Свой плановый ресурс уже выработало и более 50 % резервуарного парка (табл. 2, 3).
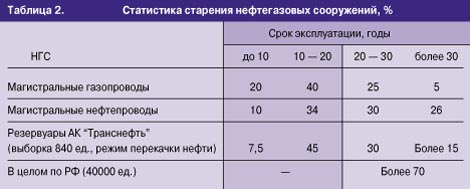
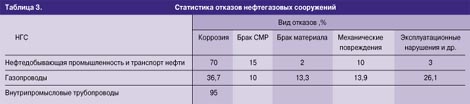 Анализ причин отказов нефтегазовых сооружений свидетельствует о превалирующем влиянии коррозионного фактора. В нефтедобывающей промышленности и транспорте нефти причины отказа (данные 1993 г.) выражены такой пропорцией: коррозионные повреждения 70 %, брак строительно-монтажных работ 15 %, заводской брак труб и оборудования 2 %, механические повреждения 10 %, нарушения правил технологии эксплуатации 3 %. Показатели на газопроводах в целом тоже не дают повода для оптимизма: коррозия наружной поверхности труб 36,7 %, дефекты труб и заводского оборудования 13,3 %, брак строительно-монтажных работ 10 %, механические повреждения труб 13,9 %, стихийные бедствия (оползни) 26,7 %. На внутрипромысловых трубопроводах нефти, воды, газа 95 % отказов вообще приходится на внутритрубную и наружную коррозию.
Диагностирование 59 резервуаров постройки 1975 1980 годов (объем резервуаров 20000 м3) для нефти и нефтепродуктов одной из ЛПДС показало, что понтоны и днище подвержены сквозной коррозии. Наиболее опасный вид нарушения герметичности коррозионное растрескивание стенок резервуаров происходит по монтажным сварным соединениям в зависимости от содержания в нефти воды, хлора, серы. Если их в совокупности менее 1 %, растрескивания не обнаружено. При большей концентрации интенсивность разрушения зависит от содержания и коррозионных примесей, и времени эксплуатации. Когда же их сумма превышала 3 %, коррозионное растрескивание имело место во всех резервуарах, эксплуатировавшихся более 15 лет.
Особую опасность представляет разрушение оборудования в условиях воздействия водородсодержащих и водородвыделяющих сред нефтегазового и нефтегазохимического комплексов.
Как и многие изделия и сооружения, жизненный цикл конструкции имеет четыре стадии: проектирование, изготовление, эксплуатация, реновация (реконструкция, ремонт). На эксплуатационной стадии изменение интенсивности отказов имеет три характерных периода:
приработка, или ранний период при уменьшающейся интенсивности отказов, когда выявляются недостатки строительства;
период нормальной работы при практически постоянной интенсивности отказов, преимущественно по причинам случайного характера;
третий, самый опасный период с возрастанием интенсивности отказов.
К настоящему времени большинство несущих конструкций вступило или вступает именно в третий период, а основными причинами отказов становятся коррозия и старение. Каков же вывод, или, точнее, выход? Решение проблем, связанных с коррозией и старением технических объектов повышенной опасности, представляет собой комплекс задач, включающих в себя:
установление причин, механизмов, закономерностей отказов конструкций;
создание системы мониторинга с учетом специфики отказов;
обоснованный выбор и оптимизацию конструкционных материалов, технологий, средств защиты;
нормативное, сертификационное, информационное обеспечение, в том числе для оценки ресурса длительно эксплуатирующихся объектов;
подготовку специалистов соответствующей квалификации;
материально-техническое обеспечение для решения этих задач.
В этой связи перед нефтегазовой отраслью, как и другими отраслями, чрезвычайно остро стоит проблема мониторинга и оценки прогнозируемого ресурса сооружений с целью определения плановых сроков эксплуатации, реконструкции, вывода из эксплуатации, необходимости проверки соответствия состояния этих сооружений законодательным требованиям и административным решениям.
Из общего комплекса факторов, влияющих на прочность конструкций (свойства материала напряженно-деформированное состояние эксплуатационные среды), остановимся на старении сталей нефтегазового сортамента и связи их коррозионного растрескивания под напряжением (КРН) с исходной прочностью. Коррозионно-активные среды, колебания температуры, рабочие нагрузки и напряжения с течением времени изменяют структуру и свойства эксплуатируемого металла. Анализ факторов, действующих на строительные конструкционные стали, позволяет выделить три основных процесса такого воздействия, приводящих к охрупчиванию и старению металла в широком смысле:
деформационное старение (особенно значимое для сварных соединений, испытывающих термодеформационное воздействие, и вызванное им повышенное напряженное состояние) связано с изменениями в распределении атомов внедрения в ферритной матрице и частичным распадом цементитной фазы в процессе технологических воздействий и при эксплуатации;
водородное старение (охрупчивание) связано с изменением напряженного состояния структуры матрицы и снижением ее трещиностойкости из-за ослабления границ зерен (рост доли межзеренного разрушения) при эксплуатации;
повторно-циклическое воздействие нагрузок и напряжений, которые посредством микропластических деформаций все более локализуют концентрацию напряжений, ускоряя эксплуатационное повреждение металла.
Все три процесса обуславливают повышение склонности стали к трещинообразованию и хрупкому разрушению по мере вызываемого им приближения температуры хрупкости стали к температуре эксплуатации трубопровода.
В условиях эксплуатации интегральные свойства материалов, эксплуатируемых при климатических температурах, в частности трубных сталей, изменяются незначительно. Столь же мало (при отсутствии пластических деформаций) меняется и уровень остаточных напряжений (менее 15 %). Однако параметры, характеризующие свойства локально охрупченных областей, в зависимости от длительности эксплуатации изменяются в значительных пределах.
Через изменения тонкой структуры и зернограничное охрупчивание старение сказывается в основном не на стандартных механических характеристиках, а на сопротивляемости хрупкому разрушению, особенно при водородном охрупчивании и это абсолютно необходимо учитывать при расчете прочности и оценке ресурса конструкции.
Основные виды коррозионного повреждения нефтегазопроводов это сплошная или общая коррозия (утончение стенки), локальная (язвы, свищи, ручейковая), коррозионное растрескивание под напряжением (в том числе сероводородное, сульфидное, водородно-индуцируемое и так называемая "стресс-коррозия"-КРН), обусловленное сопряженными по времени и месту механическими, коррозионными и сорбционными процессами.
С увеличением прочности применяемых материалов особенно резко возросла опасность именно коррозионного разрушения под напряжением. В последние годы КРН становится главным видом отказов магистральных газопроводов. Разрушение происходит преимущественно в зоне сварных соединений, по-видимому, по анодно-водородному механизму. В настоящее время следствием КРН является около 75 % отказов магистральных газопроводов по причине коррозии, а на газопроводах диаметром 1220 1420 мм за последние три года более половины общего числа отказов.
Отказы по причине КРН характерны для III и IV поколений трубопроводных сталей с контролируемой прокаткой, так как с повышением удельной прочности материала резко возрастает его чувствительность к концентраторам напряжений, технологическим воздействиям и активным средам.
Принципиальна зависимость сопротивляемости разрушению (иначе говоря, прочности) конструкций и критического коэффициента интенсивности напряжений при коррозионном растрескивании от прочности материала. Использование при сооружении газопроводов большого диаметра сталей повышенной прочности позволило увеличить давление перекачиваемого газа, что, в свою очередь, привело к значительному увеличению упругой энергии, запасенной в металле труб. Статистика свидетельствует о существовании явной корреляции между динамикой изменения прочности трубных сталей, увеличением запаса упругой энергии и временем до растрескивания магистральных газопроводов.
В связи с отмеченными обстоятельствами и огромной экологической опасностью при отказе нефтегазовых сооружений при проектировании, сооружении и эксплуатации оборудования из сталей IV и последующих поколений необходимы разработка и соблюдение научно обоснованных жесточайших требований к выбору материалов, технологии изготовления, особенно к сварке, комплексной защите (электрохимической, покрытиям, ингибированию), технической диагностике. Применительно к проблеме сероводородного растрескивания в результате целенаправленных исследований и опыта освоения Оренбургского газоконденсатного месторождения в основном решена проблема выбора конструкционных материалов.
На основе требований, предъявляемых к легированию и структуре металлов, разработан и освоен ряд марок отечественных сталей, стойких к сероводородному коррозионному растрескиванию: 20ЮЧ, 09Х12НАБЧ, 14Г2АФ, 10Г2Ф, 09ХГ2НАБЧ, 10С2Ф, 09Г2ФБ. Аналогичный подход необходим для решения проблемы КРН при выборе и совершенствовании материалов для современных магистральных газопроводов.
В свете изложенного требует взвешенного подхода применение новых конструкционных материалов с высокой удельной прочностью, которые ранее применялись преимущественно в оборонном комплексе. Полагаю, что для нефтегазового комплекса на основе анализа поведения сварных соединений в различных коррозионных средах весьма перспективно применение сплавов на основе титана и алюминия и неметаллических материалов.
Учитывая огромную проблему КРН современных газопроводов, можно привести несколько замечаний, которые либо недостаточно освещены в публикациях, либо не совпадают с имеющимися представлениями.
1. В условиях критического сочетания факторов системы М-Н-С все трубные стали проявляют склонность к стресс-коррозии. Вместе с тем у сталей разных групп наблюдаются принципиальные отличия в характере проявления такой склонности. Так, для низколегированных нормализованных сталей старшего поколения время наступления разрушения по причине КРН практически совпадает с началом периода ускоренной деградации свойств материала, обусловленного процессами в обобщенном смысле. В этом отношении аварии магистральных газопроводов из сталей этой группы не являются столь уж неожиданными. Для более новых и совершенных сталей четвертого поколения время до растрескивания во всех случаях не совпадает ни с периодом так называемой "приработки", ни с периодом "старения". И здесь каждое разрушение, вызванное КРН, должно рассматриваться как критическое событие. Наблюдаемое отличие в поведении рассматриваемых групп сталей отражает тот факт, что ответственными за процесс растрескивания в этих сталях, по-видимому, выступают разные механизмы.
2. Предрасположенность металла труб к растрескиванию обуславливается суммарным вкладом всех видов наследственности, приобретаемой на этапах изготовления прокатного листа, производства трубы, выполнения сборочно-сварочно-монтажных работ при сооружении трубопровода, а также изменений структуры и свойств металла, которые накапливаются в нем в процессе длительного воздействия нагрузок и коррозионных сред. В таком случае нет оснований выделять фактор металлургической наследственности в качестве основной причины подверженности металла растрескиванию. В развитии процесса стресс-коррозии (в особенности для сталей IV группы) помимо таких особенностей структуры, как чистота стали по неметаллическим включениям, их форма и размер, существенна роль факторов более высокого масштабного уровня и, в частности, роль тонкой структуры, формирующейся в металле трубопровода на всех этапах его жизненного цикла. Именно этот фактор способен объяснить большую склонность к стресс-коррозии сталей контролируемой прокатки, которые в сравнении с обычными сталями значительно превосходят последние, в том числе и по загрязненности неметаллическими включениями. В связи с этим необходимо проведение специальных исследований, направленных на оптимизацию структуры металла при контролируемой прокатке.
3. В дополнение к первым двум замечаниям необходимо высказать следующее: ни один из показателей служебных свойств, нормируемых существующими стандартами на сталь и на трубы, а именно: химсостав, структура, прочность, пластичность, сопротивляемость хрупким и вязким разрушениям и т.д., не дает возможности судить о степени стойкости металла труб к КРН. Этот вывод, с одной стороны, свидетельствует о том, что склонность сталей к растрескиванию закладывается уже на стадии проектирования (поскольку в стандартах не оговорены требования к коррозионной стойкости), а с другой показывает неспособность традиционных методов проверки качества трубной продукции выявлять те структурные механизмы, которые контролируют процесс КРН.
4. Известно, что газопроводы большого диаметра аккумулируют большое количество потенциальной энергии, резко повышающей опасность протяженных разрушений. В то же время в практике расследования причин стресс-коррозионных разрушений этому фактору сегодня не уделяется должного внимания. Считается, что в развитии коррозионно-механического разрушения определяющая роль принадлежит напряжениям, а величина упругой энергии деформации металла полностью зависит от них. Однако сопоставление приведенных данных свидетельствует, что эти понятия не всегда эквивалентны по своему влиянию. Установлено, что склонность к растрескиванию, а также время до разрушения практически во всех случаях коррелирует с уровня потенциальной энергии, запасенной в трубопроводе, в то время как с величиной напряжений такая корреляция просматривается не столь явно.
Характерно, что для магистральных трубопроводов, проложенных в коррозионно-опасных зонах, случаи аварий по причине КРН зафиксированы исключительно на трубопроводах большого диаметра (более 1020 мм) при том, что уровень рабочих напряжений в трубопроводах различных диаметров сопоставим.
Наиболее подверженными к растрескиванию оказались трубопроводы диаметром 1420 мм с толщиной стенки 15,7 и 16,5 мм, в которых потенциальная энергия деформации достигает максимального значения. Для сравнения: в трубопроводах диаметром 1220 х 12 мм (с большим сроком до аварии) запас потенциальной энергии более чем в 1,5 раза ниже, хотя расчетные напряжения в стенке трубы в последнем случае даже несколько выше. Обращает на себя внимание и тот факт, что в трубопроводах из одной и той же стали (Х70, ХТЗ) с увеличением толщины стенки от 15,7 до 16,5 мм аварийность снижается в 3 раза, а в трубопроводах с толщиной стенки 17,5 мм и выше случаев разрушений не отмечено вовсе.
Таким образом, при выяснении причин предрасположенности трубных сталей к стресс-коррозии необходимо в числе прочих факторов учитывать влияние запасенной в металле упругой энергии, определяемой давлением перекачиваемого газа и геометрическими параметрами трубопровода (его диаметром и толщиной стенки).
Общие выводы таковы:
1. Начало XXI века для России, несмотря на наличие ряда крупных строительных проектов, в силу экономической ситуации в стране период преимущественной реновации конструкций и сооружений повышенной опасности.
2. В связи с неоднозначной зависимостью сопротивляемости конструкции разрушению от свойств материала в условиях воздействия экологически- и коррозионно-опасных сред следует взвешенно и комплексно подходить к оптимизации прочностных характеристик материалов, технологии изготовления и защите конструкций.
|