Василий Поляков
Генеральный директор ОАО «Черметинформация»
По предварительным данным секретариата Международного института черной металлургии, мировое потребление готовой стальной продукции в 1997 году достигло рекордного уровня 680 млн. т, или на 19 млн. т больше предыдущего рекорда 661 млн. т, который был установлен в 1989 году. Этот прирост достигнут, несмотря на снижение потребления стали в бывших социалистических странах Восточной и Центральной Европы.
Данные, характеризующие изменение видимого потребления готовой стальной продукции, приведены в табл.1.
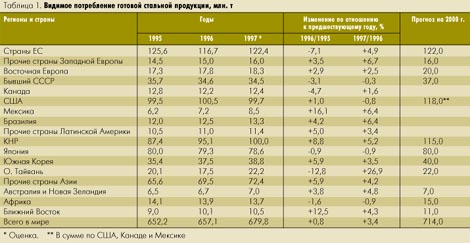 Мировое производство стали непрерывно увеличивается (табл.2). Так, если в 1970 году было выплавлено 595,4 млн. т, то первая половина 90-х годов характеризуется уже величиной 730 750 млн. т/год.
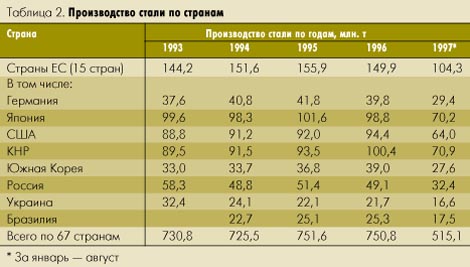
По прогнозам, мировое производство стали в 2000 году составит около 785 млн. т при производственных мощностях 1015 млн. т.
Увеличение производства стали в развитых странах будет сопровождаться дальнейшими структурными перестройками, модернизацией и реконструкцией предприятий и оборудования с целью повышения качества металлопродукции и создания новых ее видов, отвечающих требованиям потребителей и превосходящих конкурирующие материалы.
Развивающиеся страны создают свою черную металлургию, практически полностью основываясь на опыте развитых стран и с их помощью.
Таким образом развитие черной металлургии в мире идет в основном по единому сценарию.
Общим для всех стран (причем для развивающихся даже в большей степени) при вводе нового агрегата, цеха, завода, реконструкции и модернизации оборудования стало соблюдение правила 3Е (Energy + Ecology + Economy энергия + экология + экономия), т.е. выбор наименее энергоемкой, экологически чистой и экономически эффективной технологии и соответствующего конструктивного решения.
Проводимый в течение ряда лет институтом «Черметинформация» анализ на основе зарубежных источников показывает, что во всем мире, начиная с индустриально развитых стран и кончая такими «экзотическими», как, например, Зимбабве, Тринидад и Тобаго, Уганда и др., идут непрерывное строительство металлургических заводов, новых агрегатов, модернизация существующего оборудования и вывод устаревшего. Иллюстрирующие это положение данные приведены в табл.3. Соотношение между промышленно развитыми и остальными странами составляет соответственно 30 и 70 %.
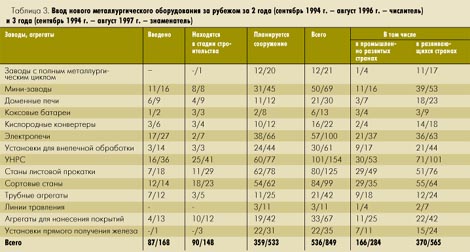 Это соотношение косвенно подтверждает тот факт, что металлургическая промышленность все более широко распространяется по всему миру. Ее начинают развивать у себя страны, до недавних пор не имевшие даже самых примитивных металлургических объектов. В 1960 году только 18 % стали производилось за пределами Европы, СССР и Северной Америки. К 1995 году эта доля увеличилась до 48 %, а в 2000 году, как ожидается, она достигнет 60 % (табл.4).
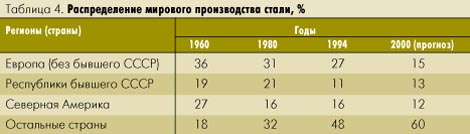
Сталеплавильное производство не сконцентрировано в каком-либо одном регионе. На долю лидирующих металлургических фирм приходится только 35 % мирового объема производства стали, а самая крупная фирма производит всего 4 %.
Интересно отметить, что в развивающихся странах (табл.5) строится либо оборудование для переработки металлургического сырья, запасами которого располагает страна, либо оборудование (чаще всего в составе мини-завода) для производства металлургической продукции (чаще всего сорта), необходимой для внутреннего рынка.
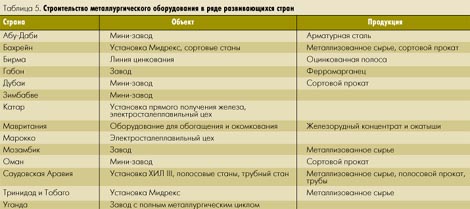 Инвестиции в технологические линии отделки проката на металлургических заводах развивающихся стран и поставка туда полупродукта могут оказаться весьма привлекательной сферой для промышленно развитых стран.
В настоящее время возможно строительство в любой стране металлургического завода любого типа. При этом трудозатраты не играют особой роли при определении местоположения завода. Гораздо большее значение имеют доступность сырья, стоимость энергии и наличие транспортных средств.
Кратко рассмотрим главные тенденции в развитии основных производств черной металлургии, которые будут определять технический уровень этой отрасли промышленности в будущем.
Добыча и обогащение руды
Для железорудной промышленности за рубежом характерна тенденция увеличения добычи руд с низким содержанием железа при росте требований к качеству товарной руды.
В первой половине 90-х годов произошло значительное увеличение мировой добычи железных руд, и в 1995 году она достигла 1 млрд.т. Имеющиеся прогнозы позволяют предполагать, что объем добычи может увеличиться в 2000 году до 1,1 млрд.т и в 2005 году до 1,24 млрд.т.
Добыча руд открытым способом составляет 85 90 %.
Практически во всех странах, осуществляющих добычу железной руды, продолжают совершенствоваться технологические процессы и повышается производительность оборудования, улучшаются эргономические и экологические характеристики.
В области буровзрывных работ применяют все более мощные и безопасные взрывчатые вещества, разрабатываются новые системы инициирования зарядов с использованием новых электронных детонаторов с расширенным диапазоном изменения времени их срабатывания, системы неэлектрического взрывания, детонаторы, не содержащие первичных инициирующих взрывчатых веществ.
На железорудных карьерах за рубежом сохраняется тенденция замены основного оборудования на более крупное. Наиболее перспективны создание и внедрение автосамосвалов с электродвигателями переменного тока. В подземных рудниках дальнейшее развитие получит применение малогабаритного самоходного оборудования с увеличенной вместимостью ковша, дизельные двигатели будут заменяться электрическими.
Модернизация агломерационного производства за рубежом в основном направлена на совершенствование способов подготовки шихты к спеканию, загрузки шихты на аглоленту, улучшение качества шихтовых материалов, автоматизацию процессов, использование отходов, снижение энергопотребления и количества выбросов.
Производство железорудных окатышей постоянно увеличивается в связи с ростом спроса на них, повышением качества этого вида сырья для доменного передела, снижением производственных затрат.
Особенностями работы зарубежных окомковательных фабрик остаются жесткий контроль за качеством железорудных окатышей в соответствии с требованиями потребителей, планомерное повышение свойств окатышей, обеспечивающих их эффективное использование в доменной печи, экономию энергоресурсов и топлива, конкурентоспособность по сравнению с другими железосодержащими материалами.
Внедрение новых технологий в доменном переделе выдвигает новые требования к качеству железорудных материалов. Так, распространение технологии вдувания пылеугольного топлива в доменную печь заставило специалистов ужесточить требования к прочностным характеристикам окатышей, характеризующим их поведение при низкотемпературном восстановлении.
Производство кокса
В период 2000 2005 годов общая потребность в коксе в мире составит 350 360 млн. т в год. Исходя из прогрессирующего старения коксовых батарей и неизбежной остановки тех из них, которые уже не отвечают жестким природоохранным нормативам, прогнозируется снижение мощностей по производству кокса примерно наполовину к 2010 году. Поэтому, если существенно не снизится спрос на кокс, то неминуем его дефицит. В отдельных регионах этот дефицит может появиться уже в ближайшем будущем.
Среди технических решений, направленных на преодоление дефицита кокса, особо выделяют снижение расхода кокса в доменном производстве и удлинение срока службы коксовых батарей. Широкое распространение в Японии, странах Западной Европы и США получила замена кокса пылеугольным топливом. Расход вдуваемого пылеугольного топлива на многих доменных печах достигает 200 кг/т, удельный расход кокса снижается при этом до 240 270 кг/т (средний удельный расход кокса без вдувания составляет 470 кг/т чугуна).
Важное значение для уменьшения дефицита кокса имеет практика продления продуктивного срока службы коксовых батарей до 35 лет; фактически некоторые батареи эффективно работают 40 и более лет. В Японии продление продуктивного срока службы коксовых батарей до 40 лет принято в качестве генерального направления развития коксохимического производства на ближайшую перспективу. Для выполнения этой программы разработаны различные системы обследования и диагностирования состояния кладки коксовых печей с целью своевременного обнаружения дефектов и устранения их путем текущих восстановительных ремонтов. Широкое распространение получили методы профилактического ремонта кладки печей факельным, а также плазменным торкретированием с использованием робота-манипулятора. В Германии, США, Австралии и других странах получил применение метод ремонта кладки керамической сваркой.
Основными направлениями развития коксохимического производства на ближайшую перспективу останутся: повышение единичной мощности оборудования путем увеличения размеров коксовых печей, что обусловливает снижение капитальных затрат; увеличение доли неспекающихся и слабоспекающихся углей в шихте для коксования (в Японии более 20 %) в результате освоения эффективных процессов подготовки углей к коксованию (частичное брикетирование, трамбование, сушка и предварительный подогрев); снижение энергозатрат на производство кокса в результате внедрения автоматизированных систем управления тепловым режимом коксования, применения сухого тушения кокса и освоения других энергосберегающих технологий; повышение уровня автоматизации и управления (имеется опыт работы коксовой батареи полностью в автоматическом режиме с дистанционным управлением) и улучшение условий труда персонала; снижение пылегазовых выбросов в результате оснащения коксовых батарей современным пылеулавливающим и газоочистным оборудованием (основная, не решенная до конца проблема).
В настоящее время проводятся активные исследования в сфере производства кокса. В Германии отрабатывается новая концепция процесса коксования с использованием супермощных модулей для коксования реакторов Джамбоу, обеспечивающих повышение производительности и улучшение рабочих условий. Объем камеры коксования в реакторе Джамбоу составляет 250 м3, что примерно в 7 раз больше, чем у современных коксовых печей (30 40 м3). В США отрабатывается процесс коксования угля в коксовых печах без улавливания химических продуктов коксования. Промышленная эксплуатация таких печей в США и Австралии доказала их высокую надежность. В этих печах газ и смола, образующиеся в процессе коксования угля, полностью сжигаются; печи работают под постоянным разрежением, что обусловливает экологическую чистоту процесса. В Японии наряду с интенсивными работами по внедоменному получению чугуна на базе жидкофазного восстановления руды без использования кокса продолжаются разработки процесса производства формованного кокса в качестве технологии будущего.
Огнеупоры
Эффективная работа основной части металлургического оборудования невозможна без качественных высокостойких и не загрязняющих металл огнеупоров.
Развитие мировой огнеупорной промышленности в последние годы определяется разработками в области огнеупорных бетонов, пластичных масс и периклазоуглеродистых огнеупорных изделий, а также распространением таких новых технологических процессов, как формование с охлаждением и направленное окисление металла.
Низкоцементные, сверхнизкоцементные и бесцементные огнеупорные бетоны с низким содержанием алюминаткальциевого цемента заменяют обычные бетоны, пластичные и набивные массы, а также торкрет-смеси в тех случаях, когда предъявляются требования высокой огнеупорности, улучшенной коррозионной стойкости и повышенной устойчивости к абразивному износу.
Создаются самотекучие (перекачиваемые) бетоны, способные заполнять сложные формы без какого-либо дополнительного воздействия (например, вибрации), из которых изготовляют крышки сталеразливочных ковшей, арматурный слой футеровки промежуточных ковшей и фасонные литые изделия.
Использование пневматического нанесения является наиболее прогрессивным методом укладки пластичных масс. По сравнению с широко распространенным методом набивки оно обеспечивает получение качественной футеровки при значительной экономии времени и средств.
Периклазоуглеродистые огнеупоры первоначально были предназначены для футеровки водоохлаждаемых электродуговых печей. Кроме того, их использовали в кислородных конвертерах с комбинированной продувкой. В течение многих лет эти изделия постоянно совершенствовали и начали широко применять в шлаковых поясах сталеразливочных ковшей, а также в футеровке вакууматоров.
Процесс формования фасонных огнеупорных изделий с охлаждением обеспечивает производство высокоглиноземистых огнеупоров с точными размерами без механической обработки, имеющих поры небольших размеров, например, детали скользящих затворов сталеразливочных ковшей.
Еще один технологический процесс, осваиваемый в промышленном масштабе, направленное окисление металла используют для получения композитов с керамической матрицей, например из периклаза и нитрида алюминия (применение разливочное оборудование, фурмы доменных печей и т.д.).
Доменный передел
Основными направлениями развития в технике и технологии доменного производства являются: строительство современных доменных печей большой мощности взамен морально и физически устаревших печей малого объема; капитальный ремонт и реконструкция доменных печей с увеличением их объема; модернизация оборудования, совершенствование систем охлаждения и футеровки для продления кампании до 15 лет и более; оснащение доменных печей бесконусными загрузочными устройствами с целью улучшения газодинамики процесса, особенно при широком использовании вдувания пылеугольного топлива в горн доменных печей, а также производства высококачественного чугуна.
Большое значение придается средствам измерения, контроля, диагностики и системам автоматизированного управления технологией ведения доменного процесса, внедрению экспертных систем и искусственного интеллекта.
На строящихся и реконструируемых доменных печах совершенствуется конструкция футеровки и систем охлаждения, применяются новые виды огнеупоров для продления кампании доменной печи. На ряде доменных печей выплавка чугуна за кампанию достигла 48 млн. т и более (например, доменная печь № 3 в Касиме фирмы «Сумитомо метл индастриз», Япония).
В странах с развитой черной металлургией происходит дальнейшее оснащение доменных печей бесконусными загрузочными устройствами лоткового типа конструкции фирмы «Поль Вюрт». Наибольшим числом таких устройств оснащены доменные печи Японии, Германии и КНР. Установка бесконусных загрузочных устройств и конусных аппаратов с подвижными плитами колошника значительно расширяет возможности регулирования шихтовых материалов в печи, что обеспечивает повышение использования восстановительной способности газов, снижение расхода кокса и высокую удельную производительность доменных печей.
Вдувание пылеугольного топлива в доменные печи, позволяющее снизить удельный расход кокса на 25 30 %, способствует снижению себестоимости чугуна, повышению производительности, расширению энергетической базы доменного производства. В настоящее время более ста доменных печей в мире работают с вдуванием угля, из них только в Японии 26 из 31 действующей доменной печи. Проводится работа по совершенствованию конструкции установок для подготовки угля к вдуванию. В последнее время большое значение придается отработке технологии и организации производства в доменных печах низкокремнистого чугуна.
Выплавка стали
Основными способами производства стали за рубежом уже в течение длительного периода являются кислородно-конвертерный и электросталеплавильный. В настоящее время в конвертерах выплавляется более двух третей всей стали, производимой за рубежом, в том числе в Японии 67 %, США 61 %, Германии 76 %, в России 48 %. Конвертерный способ наиболее стабильный и стандартизованный метод выплавки стали, большинство операций в котором автоматизировано. Это не означает, однако, отсутствия задач, которые требуют своего решения. В настоящее время этот способ выплавки стали развивается в следующих направлениях:
продолжается замена верхней продувки на комбинированную, обеспечивающую более глубокое рафинирование стали, снижение окисленности металла и шлака, повышение выхода годного (с комбинированной продувкой в Японии, например, работают 85 % конвертеров);
на основе внедрения внедоменной десиликонизации и дефосфорации чугуна разрабатываются и внедряются различные варианты малошлаковой технологии, обеспечивающей повышение производительности и выхода годного и открывающей перспективы прямого легирования стали марганцевой рудой или концентратом;
совершенствуются системы контроля и управления конвертерным процессом, обеспечивающие точность попадания в заданные пределы по химическому составу и температуре, сокращение длительности продувки и, следовательно, повышение производительности;
продолжаются разработки новых огнеупорных материалов и методов футеровки конвертеров, сопровождающиеся повышением стойкости футеровки, механизацией труда, повышением технико-экономических показателей производства.
Расширяется применение дуговых печей для выплавки стали, связанное в основном с интенсивным строительством мини-заводов за рубежом. Считают, что этот способ в ближайшем будущем будет существовать параллельно с конвертерным, который сохранится на заводах полного цикла. Доля электростали в мировом производстве составляет около 30 %: в США 39 %, Японии 33 %, в России 13 %.
Развитие этого способа производства стали идет в направлении сокращения простоев (длительности отключения печи на время выпуска, торкретирования футеровки, завалки шихты и т.д.); сокращения общего потребления энергии, зависящего от температуры и состава шихты, температуры выпуска и т.д., а также увеличения подачи энергии, которое сокращает активное время работы печи и, следовательно, тепловые потери. Большой интерес проявляется к разработке новых способов подогрева лома и регулирования загрязнения окружающей среды.
Значительно повысить эффективность работы электропечей позволяют процессы с оставлением части жидкого металла в печи, вспенивание шлака и перемешивание ванны.
Дальнейшего изучения требует вопрос эффективности работы и преимуществ электропечей постоянного тока. Считают, что в ближайшей перспективе будет продолжаться строительство печей как переменного, так и постоянного тока с некоторым перевесом в пользу последних.
На фоне постоянно растущих требований к качеству продукции черной металлургии все фирмы продолжают совершенствовать процессы внепечного рафинирования, вводя в эксплуатацию новое оборудование и улучшая характеристики действующего. Происходит дальнейшее расширение применения агрегатов типа ковш-печь; проводятся усовершенствования конструкции вакууматоров, расширяются их функции (не только дегазация, но и окисление углерода, регулирование температуры путем добавки алюминия).
Распределение функций сталеплавильного агрегата между печью и устройством внепечного рафинирования позволяет сократить продолжительность плавки и, тем самым, повысить производительность электропечи и достичь максимальной чистоты стали.
Примером эффективности агрегата ковш-печь является модернизация электросталеплавильного цеха на заводе немецкой фирмы «Гамбургер штальверке», где три печи по 85 т заменили одной модернизированной и агрегатом ковш-печь с устройствами для быстрой коррекции химического состава и легирования стали. Печь дает в сутки 24 25 плавок массой около 115 т.
Разливка стали в основном осуществляется непрерывным способом, доля которого в мире превышает 70 %: в США 90 %, Японии 96 %, в России 37 %.
Литье и прокатка
Одним из важных направлений разработок в сталеплавильном производстве стало промышленное внедрение непрерывного литья тонких слябов. Частичное исключение горячей прокатки (прокатки в черновой группе) за счет непрерывного литья тонкого сляба (толщиной 40 60 мм) освоила в промышленных условиях фирма «Ньюкор», США. Производство горячекатаных полос стало возможным при относительно малых капиталовложениях, поэтому идет активное внедрение такой технологии на мини-заводах с электрометаллургическим производством по схеме дуговая печь УНРС стан горячей прокатки.
Ведутся активные работы в направлении непрерывного литья заготовки с размерами, близкими к конечным. Эта технология предполагает непрерывное литье в условиях, еще более приближенных к получению готового продукта, чем это имеет место на тонкослябовой УНРС, и еще большее упрощение процесса прокатки. Уже действуют промышленные УНРС для литья балочных и полых заготовок, а машины для литья тонкой листовой заготовки находятся в стадии разработки во многих странах мира. Этот способ предполагает литье в двухвалковый кристаллизатор и получение непосредственно литой полосы толщиной 1 5 мм. Производительность в расчете на один ручей может составить 500 тыс.т в год. Поэтому считают, что данный способ получит развитие при производстве коррозионностойких сталей, сплавов с низкой технологичностью при обработке давлением, а также при разливке малых партий металла.
По прогнозам, к 2000 году мощности по разливке тонких слябов резко увеличатся, доля этих процессов составит от 10 до 20 %.
Наиболее перспективным для улучшения эксплуатационных показателей обычных УНРС для отливки толстых слябов является увеличение массовой скорости разливки, в частности, путем повышения линейной скорости.
Большие возможности при производстве высоколегированных специальных сталей, слитки из которых нельзя подвергать выпрямлению, открывает горизонтальная непрерывная разливка.
Очевидным фактором развития листопрокатного производства является его непрерывное усовершенствование. В обозримом будущем главной технологической схемой станет производство с использованием разнообразных методов непрерывного литья, а основной тенденцией увеличение доли непрерывных процессов благодаря созданию таких комплексов, как литье горячая прокатка травление холодная прокатка термообработка и других, объединяющих ряд смежных технологических процессов, вплоть до создания единого технологического агрегата по производству полос.
В области производства горячекатаной полосы продолжают развиваться технологии прямой прокатки и горячего посада, разрабатываются конструкции экранирующих установок для снижения тепловых потерь. Применение прямой прокатки позволяет снизить трудозатраты в 2 3 раза в расчете на 1 т стали.
На основе принципа литья тонких слябов были разработаны различные конструкции литейно-прокатных агрегатов. Более чем шестилетний опыт применения таких агрегатов (фирма «Ньюкор», США) показал, что эта технология является в настоящее время наиболее экономичным процессом производства горячекатаной полосы.
Разработан и совершенствуется процесс бесслиткового литья полосы с ленточным кристаллизатором с последующей горячей прокаткой применительно к коррозионностойким и углеродистым сталям.
В листопрокатном производстве ярко выраженной тенденцией развития является модернизация действующих агрегатов, которая характеризуется низкими капитальными вложениями и быстрой окупаемостью затрат. Производительность агрегатов возрастает за счет автоматизации процессов на входном участке станов, сокращения продолжительности вспомогательных операций, например, за счет использования быстродействующих устройств для смены валков, принципа бесконечной прокатки, совмещения процессов травления, прокатки и термической обработки в едином технологическом агрегате, широкой автоматизации процессов с использованием ЭВМ. Улучшение качественных показателей достигается в результате перечисленных выше мероприятий, а также использования гидравлических нажимных устройств, установки новых систем автоматического регулирования толщины, профиля и формы полос, совершенствования систем смазки и охлаждения валков.
Перспективным в области производства холоднокатаных полос является совмещение операций травления, холодной прокатки, непрерывного отжига, дрессировки и инспекции в единую технологическую линию непрерывного действия. Разрабатываются новые конструкции клетей для повышения точности профиля и улучшения формы полосы.
Получившие широкое распространение и предназначенные для выпуска массовой продукции линии непрерывной термообработки постоянно совершенствуются по количеству и качеству выполняемых производственных функций. Эффективность их использования возрастает при объединении линий термообработки и бесконечной холодной прокатки полос. Перспективным является совмещение агрегатов в одну технологическую линию.
Наиболее эффективным и экономически целесообразным способом борьбы с коррозией черных металлов являются защитные покрытия металлические и неметаллические. По прогнозам, к концу века доля листов с покрытиями возрастет до 60 80 %. Производство их будет расширяться за счет коренной модернизации действующих линий с изменением ряда технологических процессов и конструкций узлов и агрегатов, а также строительства новых линий. Перспективным является новый технологический процесс электролужения жести с использованием экологически чистого электролита, обеспечивающего высокое качество покрытия и увеличение производительности при исключении применения фенолсодержащих продуктов или фторидов.
Развитие производства сортового проката происходит в направлении перехода на непрерывнолитую заготовку, сокращения выпуска крупного сорта, расширения производства экономичной арматурной стали класса A500C, улучшения качества и точности размеров катанки.
В трубопрокатном производстве разработаны и совершенствуются способы прошивки заготовок из коррозионностойких и высоколегированных сталей при больших углах подачи, раскатки на стане-элонгаторе с уменьшением разностенности, повышением точности геометрических размеров. Среди новых технологических разработок следует назвать прокатку на планетарно-косовалковом стане (PSW) и редуцирование на стане-элонгаторе поперечно-винтовой прокатки.
В области роликовой формовки электросварных труб развитие продолжается в направлении увеличения диаметра труб и расширения сортамента по толщине стенки (толсто- и тонкостенные трубы), а также производства труб более высоких категорий качества.
Научные исследования
Учет таких «негативных» для развития черной металлургии факторов, как стагнация спроса на сталь, наличие избытка мощностей, низкий уровень рентабельности предприятий-производителей (часто ниже уровня, необходимого для обеспечения их жизнеспособности), позволяет сделать вывод, что в целом производство стали в мире приближается (или уже приблизилось) к предельному уровню, и возможен спад ее производства в следующем десятилетии или в течение двух последующих десятилетий в связи с усилением конкуренции между сталью и такими материалами, как алюминий, пластмассы и композиционные материалы.
В то же время научные исследования и разработки в черной металлургии проводятся в невиданном ранее масштабе.
В большинстве случаев при определении уровня зрелости черной металлургии до сих пор анализировался только общий объем производства стали. При этом недостаточно учитывались интересы потребителя. Если рассматривать эффективность применения стали в динамике, то получается, что в 1994 году произведенная сталь была использована более эффективно, чем в 1984 году, хотя общий объем производства был одинаковым. Причины этого заключаются в следующем:
повышение выхода годной продукции (тонкого листа, толстого листа, сортового проката и др.) из того же количества стали;
уменьшение расхода стали для изготовления продукции из нее;
увеличение срока службы изделий благодаря растущему использованию коррозионно- и износостойких сталей.
Таким образом, если определять состояние черной металлургии по уровню полезности стали, то можно заключить, что в черной металлургии происходит качественный рост: сортамент продукции расширяется, появляется много новых видов продукции, которые выпускаются небольшими партиями, фирмам приходится все время совершенствовать свою продукцию, чтобы она больше соответствовала условиям потребления.
Скорость совершенствования технологии производства в основном зависит от инвестиционного цикла. В связи с высокой капиталоемкостью черной металлургии этот цикл является относительно продолжительным, и скорость совершенствования технологии получается относительно низкой. Однако с течением времени процесс совершенствования технологии ускоряется.
Очевидно, что сокращение издержек производства останется основным направлением деятельности в области научных исследований и разработок. При их проведении основное внимание по-прежнему будут уделять вопросам снижения расхода энергии, капиталовложений, трудоемкости и основным факторам, влияющим на выход годной продукции.
Благодаря разработкам менее дорогого оборудования можно будет создать такую ситуацию, при которой металлургические заводы будут способны заменять оборудование через более короткие интервалы времени и быстрее приспосабливаться к новым технологическим требованиям.
В перспективе черная металлургия станет по существу промышленностью с высокой технологией, причем управление бизнесом будет неотделимо от управления технологическим процессом и от управления научными исследованиями и разработками.
Традиционно считалось, что научные исследования и разработки обеспечивают преимущество одной фирмы над другими. В настоящее время металлургические фирмы начали сотрудничать в области научных исследований и разработок не только между собой, но также с заказчиками продукции и поставщиками оборудования. Таким образом, разделение расходов на научные исследования и ответственности за риск обеспечит более быстрое внедрение результатов научных исследований и разработок.
Большое внимание уделяется управлению людскими ресурсами в связи с распространением мини-заводов, которые начали стимулировать уменьшение численности обслуживающего персонала и сокращение издержек производства. Это может быть достигнуто, например, с помощью особых структур управления, многофункциональных рабочих групп и их участия в прибылях (в зависимости от стажа работы и прочих заслуг перед фирмой). В попытке достичь «безболезненного» сокращения штатов на 3 % в год французская фирма «Юзинор-Сасилор» разработала «графики гибкого уменьшения занятости». Около 10 % персонала будет работать 60 % полного рабочего времени. Такой способ, подкрепленный соответствующими программами обучения, должен помочь формированию высокоинтеллектуального персонала, необходимого для достижения целей фирмы.
|