|
|
Журнал |
|
Архив |
|
Подписка |
|
Реклама |
|
САММИТ |
|
Книжная полка |
|
Контакты |
|
В начало |
|
|
|
| |
|
|
 |
№2' 2004 |
версия для печати
|
|
ЛИЧНОЕ ВИДЕНИЕ ПРОИЗВОДСТВА |
Ричард Баррет (Richard Barrett) пишет: «Среди главных направлений деловой активности группы Arvedi, которыми являются производство труб из углеродистых и нержавеющих сталей, а также нержавеющей полосы, именно производство горячекатаной полосы наряду с дальнейшей развитием технологии мини-металлургии на предприятии Acciaieria ISP di Cremona, флагмане группы в Италии, формирует видение будущего у главы компании Джованни Арведи (Giovanni Arvedi). |
Джованни Арведи (Giovanni Arvedi)
ИЧНОЕ ВИДЕНИЕ ПРОИЗВОДСТВА
В то время как ведущие европейские производители листа и полосы часто испытывают гордость за свои самые современные технологии, закупаемые с целью удовлетворения запросов по качеству и цене требовательных автомобилестроителей, непривычно встретить главу металлургической компании, который любит обсуждать в деталях технико-экономические преимущества своего передового завода. Джованни Арведи именно такое исключение из правил.
Finarvedi группа из пяти фирм, которую он возглавляет, была образована 40 лет назад как производитель труб, но с тех пор расширила свое производство с включением прецизионной нержавеющей полосы. В настоящее время на долю рулонной полосы приходится наибольшая часть объема производства.
Фирма Arvedi задумала создать Acciaieria ISP di Cremona в середине 70-х годов прошлого века. Предприятие считается первым мини-заводом по производству горячекатаных листа и полосы в Европе. Оно было построено фирмой Mannesmann Demag, ФРГ, всего в десяти минутах езды на автомобиле от сегодняшней главной конторы Finarvedi в центре Кремоны. Первый рулон был получен в феврале 1992 года.
Процесс ISP (непрерывное производство полосы) используется для выпуска горячекатаных рулонов с коротким циклом производства, и именно на прошлом и будущем этой технологии основывается стратегическое видение Арведи.
Компактный завод
Завод в Кремоне компактный, расстояние от сталеплавильного цеха до участка намотки рулонов всего 180 метров. Он выпускает полосу толщиной 112 мм, с упором на прокатку тонких типоразмеров. Ширина полос от 1000 до 1300 мм. Персонал всего завода, с учетом травильного агрегата и агрегата цинкования на той же площадке, составляет 500 человек, оборот в 2003 году превысил 350 млн евро.
На мини-заводе в Кремоне в качестве шихты используют в основном лом плюс небольшое количество чугуна или губчатого железа прямого восстановления. На 120-тонной печи завода время плавки менее одного часа, среднее количество плавок в сутки 25. После рафинирования в одном из двух 120-тонных агрегатов ковш-печь сталь поступает через установку непрерывной разливки тонких слябов непосредственно на трехклетьевой черновой стан. Скорость разливки 4,24,8 м/мин для низкоуглеродистых сталей, обычно поступающих в первую клеть чернового стана в виде сляба толщиной 50 мм, шириной 10001300 мм.
На выходе из чернового стана раскат проходит через индукционную печь в двухрулонную камеру печи Cremona, которая служит буфером между разливкой и чистовой прокаткой на пятиклетьевом стане с последующим струйным охлаждением и смоткой полосы на моталке под полом.
Объем производства горячекатаных рулонов в 2003 году составил 860 тыс. т, выше показателя 2002 года (840 тыс. т). Производство в 2004 году прогнозируется на уровне примерно 1 млн т, более половины которого будет приходиться на долю специальных марок сталей.
Максимальная производительность прокатного стана более 1,2 млн т/год. Есть планы модернизации МНЛЗ с увеличением толщины сляба с 50 до 55 мм и скорости разливки с 5 до 5,5 м/мин с ростом обшей производительности на 20 %. Модернизацию намечено провести в течение второго квартала с пуском в конце августа.
Помимо уже установившегося в настоящее время принципа замены производства рулонной полосы из толстых слябов на тонкие, главной задачей Acciaieria ISP di Cremona является производство высококачественной горячекатаной тонкой полосы в рулонах как заменителя некоторых типоразмеров, которые обычно требуют холодной прокатки.
Около 40 % объема производства Arvedi ISP полоса толщиной менее 1,6 мм. Качество отделки поверхности полосы считается высоким, регулирование толщины хорошим, при точном контроле плоскостности и профиля обеспечиваются те же допуски, что и на холоднокатаную металлопродукцию. Минимальный размер партии один рулон.
Специализация фирмы конструкционные стали, от горячекатаных высокопрочных марок до борсодержащих и предназначенных для термообработки (цементация и отпуск). Производятся стали общего конструкционного назначения и трубные, плюс стали с высокой деформируемостью для холодной формовки, вытяжки и гибки. Были также проведены успешные испытания по выпуску нержавеющих сталей серий 300 и 400 и магнитных сталей. Проводятся также опыты по производству двухфазных сталей с отправкой образцов конечным потребителям. Получены первые заказы на стали для автомобильных колес. Ведутся опыты по производству оцинкованной металлопродукции из двухфазных сталей.
Горячекатаные рулоны поставляют после прокатки или травления. Большая часть металлопродукции подвергается дальнейшей обработке на расположенных на той же площадке агрегатах травления и цинкования. В прошлом году в Кремоне было изготовлено 220 тыс. т оцинкованной стали при максимальной мощности 400 тыс. т/год.
Рулоны реализуют в основном в Италии для использования в строительстве и автомобильной промышленности. При сооружении агрегата цинкования планировалось сократить импорт и содействовать развитию европейского рынка оцинкованных рулонов, однако недавний существенный рост местных мощностей по производству оцинкованной металлопродукции ужесточил положение на этом рынке. Поэтому агрегат цинкования в Кремоне в начальный период работал пять дней в неделю, а сейчас на полную мощность, семь дней в неделю.
Для повышения качества оцинкованной металлопродукции фирма Arvedi поставила устройство для получения мини-блесток (кристаллов цинка на поверхности) и дрессировочный стан фирмы Danieli, а также правильно-растяжную машину. Клети дрессировочного стана (1000 МПа) для обработки высокопрочного стального листа были поставлены в прошлом декабре, и первый дрессированный рулон будет получен к концу апреля.
Путь вперед
Перед лицом конкуренции со стороны импорта, растущих цен на лом, транспортных и энергетических расходов и стагнации европейской черной металлургии Арведи полагает, что путь вперед это выпуск металлопродукции с добавленной стоимостью и применение новых технологий: «Единственный ответ заключается в инновациях и качестве продукции».
Он также подчеркивает доминирующий конкурентный фактор срок доставки: «Временной фактор становится все более стратегически важным. Единственным ответом на ситуацию, обуславливаемую рынком, является инновация технологии и продукции».
Он подчеркивает скорость работы совмещенного литейно-прокатного агрегата, его компактную планировку и низкие (по сравнению с обычными полосовыми станами горячей прокатки) капиталовложения: «Инновация продукции включает возможность производства всего марочного сортамента; точный и надежный контроль температурного режима и высокая гибкость агрегата позволяют производить даже многофазные стали, представляющие огромный интерес для автомобилестроения».
По его заявлению, главными преимуществами использования технологии ISP как раз и являются более высокая добавленная стоимость продукции и прибыль, достигаемая на единственном заводе, пониженные капитальные затраты на единицу продукции, широкий марочный сортамент и сверхтонкая горячекатаная полоса, производимая при конкурентоспособных издержках производства.
«Применяя совмещенную разливку и прокатку, мы создали патенты и новые машины, экспериментировали с высокоинновационными процессами, что дало выдающиеся результаты и позволило осуществить дальнейшие значимые разработки», сказал Арведи. «За десять лет мы получили положительные результаты с промышленной, технологической и экономической точки зрения, достигая средней валовой операционной прибыли на оборот 15,5 %».
На базе уже известных данных за 2002 год Арведи сделал сравнение затрат по переделу жидкой стали в горячекатаный рулон. Для совмещенной разливки и прокатки этот показатель составляет 38 евро/т по сравнению с 72 долл., 62 и 55 евро за тонну для завода с полным циклом производства в США, Германии и Франции соответственно, за исключением постоянных (общих и накладных) издержек. Постоянные издержки составляют 12 евро за тонну для совмещенного производства и 26 долл., 24 и 22 евро за тонну для полного цикла производства в других странах. По тем же базовым данным, передельные затраты на мини-заводах США были равны 53, постоянные 10 долл./т.
Следуя за мечтой
Мечта Арведи перевести технологический процесс, используемый в Кремоне, на следующую стадию непрерывной разливки-прокатки (ECR), что станет возможным при прохождении промежуточной полосы между двумя печами Cremona непосредственно в чистовую группу при той же скорости, с которой полоса выходит из комбинированного агрегата разливки-черновой прокатки, напрямую соединив разливку и прокатку. Непрерывный процесс позволит достичь производительности 2,5 млн т/год в единой линии разливки. «Теперь мы готовы к Arvedi ISP-ECR, говорит он, это эволюция, основанная на фактах, а не прыжок в темноту».
Он предвидит агрегат, в котором непрерывнолитой сляб толщиной 70 мм поступает в черновую клеть, выходит из нее в виде раската толщиной 10 мм, проходит напрямую через индукционную печь в чистовой стан перед смоткой (для малых толщин) на двухбарабанной карусельной моталке. Затем полосу разматывают для прохождения через холодильник со струйным охлаждением перед окончательной смоткой на паре моталок.
Скорость разливки нужно повысить до 8 м/мин. Скорость полосы толщиной 0,7 мм на выходе из последней клети чистового стана будет равна 12,5 м/с в настоящее время такая скорость используется для полосы толщиной 1 мм. Толщина готовой полосы составит 0,712 мм, ширина 9001600 мм. Планируется производство сталей для глубокой вытяжки и двухфазных сталей.
Будет обеспечено производство тонкой полосы из двухфазных сталей, сталей, пластичных при превращении и двойниковании, поскольку с бесконечной разливкой-прокаткой станет возможным точно управлять кривой охлаждения, учитывая стабильный скоростной режим, достигаемый в течение длительного промежутка времени.
Планировка, которую активно пропагандирует Арведи, предусматривает мини-завод ISP-ECR производительностью 2,5 млн т/год и, для завершения схемы, агрегат травления, стан холодной прокатки, агрегаты отжига, лужения, цинкования и маркировки на той же площадке. Он стремится содействовать разработке такого высокоинтегрированного проекта на территории Европы и говорит, что его финансирование европейского научно-исследовательского проекта могло бы стать возможным, если бы пару ведущих металлургических компаний, какую-либо машиностроительную фирму и пару крупных автомобилестроителей подтолкнули бы к участию в этом проекте.
«Наша технология нуждается в партнерстве со стороны машиностроителей», говорит Арведи.
Несмотря на прогресс в области прямой разливки полосы, достигнутый на других предприятиях, Арведи скептически настроен в отношении ее универсальности: «Превращение из жидкого состояния в твердое происходит слишком быстро». Он также сомневается в однородности качества полосы по ширине и мощности мини-заводов, построенных по этому принципу: «С промышленной точки зрения это не имеет никакого смысла».
Арведи уверен, что расширение его технологии ISP до ECR сработает успешно. Возможно, более критической для него проблемой является необходимость убедить черную металлургию, инвесторов и конечных потребителей в преимуществах его процесса, превышающих характеристики имеющихся технологий разливки тонких слябов и прямой разливки полосы. Поиск подходящего партнера продолжается.
Вставка 1:
ГРУППА ARVEDI
Общий объем производства группы Arvedi превышает 1,2 млн т/год. В группе работают более 1600 чел., консолидированный оборот около 650 млн евро. В среднем более 40 % общего оборота получают за счет экспорта.
АТА производит горячекатаные и электросварные (методом сопротивления) трубы наружным диаметром 15,8168,3 мм, толщиной стенки 112 мм. Годовой оборот около 175 млн евро; 470 работников. Ilta Inox выпускает сварные трубы из нержавеющих сталей наружным диаметром 6406,4 мм, толщиной стенки 0,56 мм. Оборот более 100 млн евро, более 300 работников. На агрегате ISP обеспечивается 2025 % потребности предприятий группы в полосе для производства труб.
Arinox единственный в стране производитель сверхтонкой холоднокатаной полосы из нержавеющих сталей прецизионного назначения (минимальная толщина 0,05 мм). Ширина 5650 мм. В компании 195 работников при обороте 55 млн евро.
В декабре прошлого года Арведи вновь получил группу в свое полное владение, выкупив 40 % акций Finarvedi, которыми владела Arcelor наследие от поддержки Usinor, полученной в стартовый период производства на агрегате ISP в начале 90-х годов прошлого века, когда группа испытывала финансовые затруднения.
Вставка 2:
ПОСЛЕДУЮЩИЙ ПЕРЕДЕЛ
Эксплуатация травильного агрегата компании Acciaieria ISP di Cremona началась в 1998 г. Агрегат полунепрерывный, оборудован установленным в линии дрессировочным станом, имеет производительность более 40 тыс.т/мес и обрабатывает рулоны с минимальной толщиной полосы 1 мм. Намечено увеличить среднюю скорость работы агрегата до 150 м/мин. Заказано оборудование для модернизации агрегата, которое начнет работать к концу этого года. Примерно половина объема производства подвергается травлению на месте, однако дополнительное травление заготовки, получаемой по толлингу, позволяет подвергать травлению в общей сложности 60 % горячекатаных рулонов.
В апреле прошлого года на площадке был введен в эксплуатацию агрегат горячего цинкования фирмы Danieli. Агрегат спроектирован специально для цинкования сверхтонких рулонов (0,70,8 мм), производимых агрегатом ISP, но на нем можно также при необходимости наносить покрытие на холоднокатаную полосу. На агрегате, оборудованном горизонтальными накопителями и печью, оцинковывают горячекатаную рулонную полосу со скоростью 8090 м/мин. Агрегат стоимостью 25 млн евро останавливают только на техобслуживание.
Рулоны катаной или травленой и дрессированной полосы превращают в полосу, лист или заготовки в принадлежащем группе Arvedi центре обслуживания в Милане. В центре полосу подвергают продольной и поперечной резке, резке на заготовки и лист, а также правке для конечного потребителя в автомобильном и строительном секторах и в производстве бытовой техники («белых товаров»). Оборот 30 млн евро, персонал 65 чел.
Таблица
Компании группы «Арведи»
Компания Металлопродукция Мощность (т/год)
Arvedi Tubi Acciaio (Кремона) Трубы из углеродистых сталей 300000
Ilta Inox (Робекко д’Олио, Трубы из коррозионностойких сталей 40000
Кремона и Sestri Levante, Генуя)
Arinox (Рива Тригозо, Генуя) Прецизионная нержавеющая полоса 13000
Acciaieria ISP di Cremona Лист и полоса из углеродистой стали 860000
(производство)
CSS (Милан) Лист и полоса из углеродистой стали 300000
(центр обслуживания)
|
|
|
|
|
текущий номер

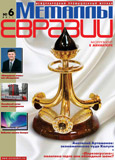
предыдущий номер

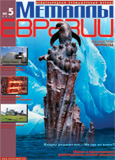
|
|