|
|
Журнал |
|
Архив |
|
Подписка |
|
Реклама |
|
САММИТ |
|
Книжная полка |
|
Контакты |
|
В начало |
|
|
|
| |
|
|
 |
№3' 2003 |
версия для печати
|
|
«УРАЛЭЛЕКТРОМЕДЬ»: ВРЕМЯ ВКЛЮЧАТЬ РЕЗЕРВЫ |
|
Александр Козицын
Директор ОАО «Уралэлектромедь»
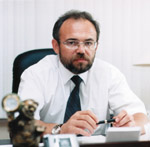
Александр Козицын
|
|
последние несколько лет мировой рынок меди характеризовался сначала стабильным уменьшением цен на катодную медь, а в дальнейшем квазистабильностью на весьма низком уровне. Это объясняется не только заметным снижением спроса на металл по сравнению с предложением, но также и появлением на рынке весомой доли так называемой «дешевой меди», получаемой из легко вскрываемых руд чилийских месторождений. В условиях нестабильности рынка на основную выпускаемую продукцию и, соответственно, цен на нее, ОАО «Уралэлектромедь» вынуждено в большей мере изыскивать и реализовывать резервы, которые могли бы снивелировать отрицательное воздействие мирового рынка металлов и невысокий уровень потребления меди в России.
Кроме прямого снижения затрат на выпускаемую продукцию, этого можно добиться повышением степени готовности выпускаемой продукции, а также диверсификацией товарной номенклатуры и ростом оборачиваемости используемых финансовых ресурсов.
Для снижения затрат на производство продукции предприятие, как правило, должно либо увеличивать объемы производства, либо снижать энерго- и материалоемкость продукции. Так, прирост объемов производства позволяет предприятию получить дополнительные ресурсы в виде относительной экономии на условно-постоянных расходах. Однако в 2001 2002 годах в «Уралэлектромеди» достигнуто максимальное использование основных мощностей по выпуску рафинированной меди, и дальнейшее его наращивание возможно только путем расширения производственных мощностей.
Основным направлением повышения эффективности производства является строительство нового цеха электролиза с расширением мощностей до 450 тыс. т катодной меди в год. Существующий цех построен в 1934 году и за последующее время претерпел многократные модернизации, наращивание производственных мощностей. К настоящему времени основные фонды цеха достаточно устарели морально и физически и не в полной мере соответствуют техническим требованиям. Ежегодно предприятие тратит более 1 млн долл. на проведение капитальных и текущих ремонтов корпуса цеха и технологического оборудования. Планировка существующего здания не позволяет проводить коренную модернизацию производства со снижением энергозатрат и созданием условий труда, соответствующих современным требованиям.
Эти обстоятельства явились основой для принятия решений о крупной реконструкции медеэлектролитного производства. Строительство нового цеха электролиза меди должно будет осуществляться с сохранением существующей производительности, качество и себестоимость выпускаемых после реконструкции медных катодов будет определяться совершенством используемых при этом технологии и оборудования.
Решение поставленной задачи было доверено фирме Outokumpu, с которой в настоящее время заключен контракт на разработку технической части проекта. Фирма занимает в мире передовые позиции по вопросам проектирования и изготовления оборудования для цветной металлургии, механизации и автоматизации производственных процессов.
Ввод проектируемого цеха в эксплуатацию предполагается осуществить в три этапа. На первом часть нового цеха электролиза меди предусматривается разместить на свободных площадях. Строительство второй очереди предполагается осуществить после введения в эксплуатацию первой и демонтажа помещений и оборудования ЦЭМ: новые производственные мощности будут частично размещены на их месте. После введения в эксплуатацию второй очереди начнется строительство третьей, которая доведет мощность нового цеха до 450 тыс. т меди в год.
Инвестиционные затраты на реализацию проекта, согласно подготовленному бизнес-плану, составляют 174,5 млн долл. в том числе стоимость технологического оборудования, поставляемого фирмой Outokumpu, оценивается в 86,2 млн долл. Срок окупаемости проекта около 4 лет.
На снижение себестоимости выпускаемой продукции направлена также планируемая работа по проектированию и строительству Сафьяновской обогатительной фабрики с мощностью по переработке 750 тыс. т товарной руды в год. В настоящее время добываемые на Сафьяновском медно-колчеданном месторождении сульфидные медные и медно-цинковые руды перерабатываются на обогатительной фабрике ОАО «Святогор», находящейся на расстоянии более 300 км. Значительные затраты по доставке товарной руды приводят к существенному увеличению себестоимости ее переработки и, в конечном итоге, себестоимости получения рафинированной меди.
Строительство и ввод в эксплуатацию обогатительной фабрики вблизи месторождения позволит не только заметно сократить объем перевозок и снизить затраты по перегрузочным операциям, но и улучшить показатели извлечения меди из руды. Проведенными опытно-промышленными испытаниями показано, что на оборудовании, закладываемом в проект, извлечение меди в концентрат увеличивается в среднем на 5,1 %.
Реализация данного проекта позволит снизить себестоимость получения меди из руды Сафьяновского месторождения в среднем на 365 долл./т. Прибыль оценивается в 7,8 млн долл. в год. Срок окупаемости проекта не превышает 4,5 лет.
Возможность увеличения отпускных цен и расширения рынков сбыта предоставляется повышением степени готовности выпускаемой продукции. Увеличение номенклатуры продукции с высокой долей добавленной стоимости обусловливает рост прибыли от реализации.
За истекшие четыре года на предприятии в этом отношении сделаны весомые шаги. В 1999 году было завершено строительство и запущено в эксплуатацию крупнейшее в России производство медной катанки из собственной катодной меди мощностью по проекту 235 тыс. т в год. В проект была заложена наиболее передовая в техническом плане технология Contirod с использованием оборудования немецкой фирмы Mannesmann Demag Sack. Успешное освоение производства, а также качество получаемой продукции позволили предприятию выйти на рынок сбыта медной катанки и непрерывно расширять свое присутствие на нем, доведя производство продукта в 2002 году до 130 тыс. т. В конце 2002 года в цехе катанки вновь случилось важное событие: введена в строй технологическая линия тонкого волочения с использованием технологии Niеhoff производительностью 12 тыс. т в год медной проволоки диаметром от 1,04 до 4,5 мм.
Очередным шагом в повышении степени готовности продукции является создание на предприятии крупномасштабного производства изделий из меди и других компонентов методами порошковой металлургии. Целесообразность создания данного производства диктуется нижеследующими соображениями. Наиболее существенным критерием, по которому выбранная технология более предпочтительна по сравнению с такими технологиями получения готовой продукции машиностроения, как штамповка, литье (с последующей мехобработкой), мехобработка из проката, является выход исходного сырья в готовую продукцию. Если обычные технологии дают коэффициент использования материала (КИМ) от 30 % до 70 %, то технология порошковой металлургии стабильно обеспечивает КИМ в 90 % на изделиях любой конфигурации. Более полное использование исходного материала позволяет технологии порошковой металлургии успешно конкурировать с другими технологиями по себестоимости продукции. Следовательно, производство изделий методом порошковой металлургии позволяет при соизмеримых ценах реализации получать большую прибыль по сравнению с теми же изделиями, но изготовленными по другой технологии. Предприятиями машиностроительного комплекса страны используется в год 70 90 тыс. т медного проката, выпускаемого заводами ОЦМ. Анализ структуры используемого проката показывает, что потенциальный рынок изделий, изготовление которых возможно методом порошковой металлургии, оценивается в объеме до 8 тыс. т. Кроме того, в таких отраслях машиностроения, как автопром и производство бытовой техники, имеется устойчивая потребность в бронзовых и бронзографитовых антифрикционных изделиях, получение которых возможно только методами порошковой металлургии.
Исходя в том числе и из этих соображений, принято решение о строительстве на существующих площадях предприятия цеха порошковой металлургии производительностью 2 тыс. т высокорентабельных изделий в год. Организуемое производство полностью обеспечивается собственным медным электролитическим порошком, ресурсами общезаводской системы энергоснабжения и других коммуникаций. Реализация проекта организации крупномасштабного производства порошковых изделий потребует 266,1 млн руб. капиталовложений и позволит окупить вложенные инвестиции немногим более чем за 5 лет.
Помимо резервов, которые при их реализации позволяют напрямую увеличивать объем производства, а значит, и прибыль, получать продукцию более завершенного цикла, а значит, с большей добавленной стоимостью, в ОАО «Уралэлектромедь» есть инвестиционные проекты, которые до недавнего времени считались затратными.
Производственная деятельность любого металлургического предприятия, а тем более предприятия медной подотрасли, по определению не может быть экологически абсолютно чистой. Однако снизить до минимума вредную нагрузку на окружающую среду одна из первостепенных задач производства, желающего оставаться эффективным. Особенно это важно на современном этапе развития общества, когда конечным продуктом становятся уже не только материальные, но и социально-значимые результаты, в том числе и благоприятная экологическая обстановка. А в условиях значительного повышения штрафных санкций со стороны государственных природоохранных органов за превышение предельно-допустимых выбросов вредных веществ в окружающую среду предприятию становится выгодно реализовывать проекты природоохранительного назначения.
Снижение выбросов в атмосферный воздух и сбросов вредных веществ в водоемы, помимо оздоровления окружающей среды, позволяет предприятию дополнительно извлекать ценные компоненты сырья, снижая тем самым себестоимость выпускаемой продукции. Поэтому все программы модернизации производства в ОАО «Уралэлектромедь» неразрывно связаны с осуществлением природоохранных мероприятий.
Для снижения вредного воздействия на атмосферный воздух выбросов медеплавильного цеха, одного из основных источников загрязнения на предприятии, была разработана и уже воплощается в жизнь программа очистки отходящих газов анодных печей. Установленное на газовых трактах двух печей газоочистное оборудование, включающее рукавные фильтры, привело к снижению запыленности отходящих газов на три порядка до 0,003 0,01 г/м3. На очереди внедрение аналогичных установок на двух других печах. Экологический эффект снижения запыленности в сочетании со значительным сокращением выбросов веществ высших классов опасности свинца и мышьяка сочетается с прибылью от реализации извлекаемых из пылей сотен тонн меди, сотен килограммов драгоценных металлов. Прибыль от реализации продукции, полученной при переработке ранее теряемых пылей от четырех печей медеплавильного цеха, превысит 13,4 млн рублей в год.
Задача снижения выбросов в атмосферу высокоопасных веществ свинца, теллура, оксидов мышьяка и селена, образующихся при переработке медеэлектролитных анодных шламов в химико-металлургическом цехе, оказалась более сложной. Попытка ее решить с использованием сухих методов очистки отходящих газов при проведении опытно-промышленных испытаний не привела к желаемым результатам из-за нестабильности режимов работы и возможности приемлемой очистки газов на рукавном фильтре только в очень узком диапазоне температур. Последующие после этого объемные исследования технологических процессов, обследование и расчеты аппаратурного оформления позволили прийти к однозначному ответу: только мокрыми методами очистки газов можно кардинально и надежно снизить содержание всех компонентов до уровня ПДВ и свести к минимуму их вредное воздействие на город и окружающую природу.
Решение, позволяющее снять эту проблему на десятилетия, конечно, потребует применения дорогого, но наиболее эффективного оборудования, зарекомендовавшего себя в мировой практике. Это скрубберы Вентури с регулируемой горловиной, электрофильтры с высокой плотностью поля, аппараты для быстрого и надежного охлаждения газов плавильных печей. Тем весомей будет результат, который через полтора года позволит предприятию уйти от миллионных штрафов сейчас и в будущем. Переработка же дополнительно уловленных пылей с переводом находящихся в них ценных компонентов в готовую продукцию позволит за 3,5 4 года окупить предстоящую реконструкцию.
Главная же составляющая результата благоприятные перемены в природной среде, негативное воздействие предприятия на которую в последние годы все более и более сокращается.
Подводя некоторые итоги, следует сказать, что на предприятии в той же мере, как и на других, практически всегда можно найти резервы повышения эффективности производства, выпуска продукции более завершенных переделов, экономически выгодных, экологически и социально направленных точек приложения сил и средств. Выделить из них главные на сегодняшний день, найти верный путь их реализации каждодневная задача руководителей предприятия и его коллектива.
|
|
|
|
|
текущий номер

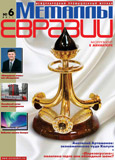
предыдущий номер

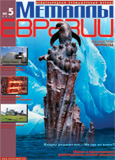
|
|