|
|
Журнал |
|
Архив |
|
Подписка |
|
Реклама |
|
САММИТ |
|
Книжная полка |
|
Контакты |
|
В начало |
|
|
|
| |
|
|
 |
№3' 2003 |
версия для печати
|
|
МЕНЕДЖМЕНТ POSCO ВНЕДРЯЕТ НОВЫЕ ИДЕИ ЭНЕРГОСБЕРЕЖЕНИЯ |
|
Компания Posco разработала множество способов экономии энергии. Ким Сен (Siwan Kim) и Пак Хён (Hyeon Park) рассказывают об основных технологиях, которые использует эта компания производитель стали из Южной Кореи.
жнокорейская компания Pohang Iron & Steel Co (Posco) была основана в 1968 году. Производством горячего проката она занялась в 1973 году во время первого нефтяного кризиса. В прошлом году принадлежащие компании заводы Похан и Кангуян произвели в целом 28 млн т стальной продукции, 77 % которой поступило на внутренний рынок, а остальное было экспортировано в Японию, Китай и другие страны.
В 70-х и 80-х годах правительство Южной Кореи начало проводить политику, направленную на экономическое развитие и ускорение промышленного роста страны. Однако, в условиях обострения проблемы защиты окружающей среды и роста рыночной конкуренции в 90-х годах, правительство изменило акцент, начав поддерживать отрасли промышленности с низкой энергоемкостью производства и использованием экологически чистой энергии.
В настоящее время проблемы климатических изменений касаются производителей стали во всем мире уже в силу того, что в ближайшем будущем может начать действовать Киотский Протокол. На фоне таких глобальных тенденций Posco отдает себе отчет в важности эффективного использования энергии, как основы успешного менеджмента и стремится разработать бизнес-план стабильного развития.
С самого начала сталелитейные заводы компании задумывались как предприятия, которые будут максимально эффективны в использовании энергии и транспортировке сырья, полуфабрикатов и готовой продукции, а также побочных продуктов и отходов. Согласно плану завод Кангуян, вступивший в строй в 1987 году, должен был сократить потери энергии при транспортировке продукции посредством «стратегической» концентрации всех агломерационных фабрик и коксовых цехов, доменных печей, сталеплавильного и прокатного переделов на одной площадке осушенном участке залива Кангуян.
В результате Posco применила для горячей промежуточной и чистовой прокатки оборудование, обеспечивающее повышение эффективности использования энергии. Компания также внедрила различное энергосберегающее оборудование, включая турбины для повышения давления газа в доменных печах (TRT), оборудование для регенерации тепла отходов агломерационных фабрик, котлы-регенераторы тепла для установок конвертерного газа Linz-Donawitz, а также оборудование для регенерации отработанного тепла охлаждающей воды при повторном нагреве печных подовых труб. Компания также создала установки PCI, которые позволяют осуществлять вдувание пылеугольного топлива непосредственно в доменные печи без какой-либо предварительной обработки.
Краткая история
За последние 30 лет Posco удалось сократить свое удельное потребление энергии на 25 % благодаря разнообразным мерам по ее экономии. В 70-х годах компания сосредоточивала свои усилия на уменьшении удельного потребления энергии, а после второго нефтяного кризиса (1979 г.) она предприняла целенаправленные усилия по снижению энергозатрат. С 90-х годов Posco проводит стратегию управления расходованием энергии с учетом проблем климатических изменений.
После второго нефтяного кризиса Posco сократила применение топлива с углеводородной основой, полностью заменив использовавшуюся в доменных печах тяжелую нефть на кокс. Она также повысила степень регенерации побочных газов и начала переходить от обычных процессов разливки стали на процесс непрерывного литья. В 1986 и 1988 годах Posco оборудовала установки сухого тушения кокса (УСТК) в коксовых цехах № 2 и № 3 на своем заводе Похан с целью регенерации тепла коксования.
В дополнение к этим изменениям компания реализовала энергосберегающие технологии, применив прямую подачу заготовок после МНЛЗ непосредственно в нагревательную печь вместо того, чтобы охлаждать их. Отработанное тепло, полученное при охлаждении горячего агломерата примерно с 800оС, также утилизировалось для производства пара или горячей воды.
С ужесточением требований по защите окружающей среды в 90-х годах, использование природных ресурсов, особенно в черной металлургии и сталелитейной промышленности, стало актуальнейшим вопросом. В результате компания форсировала установку дополнительного оборудования по регенерации энергии и построила теплоэлектростанции.
Posco стала первой корейской компанией, которая в декабре 1998 года добровольно заключила с правительством страны соглашение об экономии энергии. Такие «добровольные соглашения» обычно заключаются между какой-либо компанией и правительством с целью достижения конкретной цели в экономии энергии, добровольно устанавливаемой этой компанией с тем, чтобы повысить национальную индустриальную конкурентоспособность.
По этому соглашению Posco начала осуществлять программу, направленную на экономию энергии в размере 788 000 тонн нефтяного эквивалента (т.н.э. теплотворная способность одной тонны нефти, 1 т.н.э. равна 107 килокалориям) в период с 1999 года по 2003 год включительно. Это составляет 5,9 % от общего объема энергии, которую компания потребила в 1997 году. Posco досрочно превысила поставленную цель, сэкономив 796 000 т.н.э. энергии в 1999 2001 годах, или 6 % от объема энергии, потребленной в 1997 году.
Каким образом компания достигает своей цели? Она разрабатывает пятилетний, среднесрочный и долгосрочный планы экономии энергии, ежегодно проводя анализ получаемых результатов и действующих планов.
На каждом заводе отделы контроля над процессом отбирают потенциальные проекты экономии энергии для достижения целей компании. После изучения всех отобранных планов комитет по окружающей среде и энергетике утверждает окончательные варианты.
Группа собственных экспертов на регулярной основе оценивает все выполненные проекты, и полученные результаты сообщаются в комитет по окружающей среде и энергетике. В конечном итоге эти результаты находят свое отражение в решениях, принимаемых старшим менеджментом.
В целях улучшения планирования, использования результатов и оценки эффективности проектов Posco завершила в ноябре 2001 года разработку системы управления использованием энергии в соответствии с программой модернизации, которая проходит на всех объектах компании. Согласно этой системе отделы ныне могут непосредственно регистрировать проекты экономии энергии и оперативно анализировать их результаты.
Основные проекты 2002 года
В первой половине 2002 года завод Похан выполнил в целом 126 энергосберегающих проектов. В целом они позволили сберечь 50 700 т.н.э. энергии и сократить затраты на энергию на 14,3 млрд вон (12,1 млн долларов), тогда как завод Кангуян выполнил 197 проектов, сэкономив 44 500 т.н.э. энергии и снизив расходы на энергию на 11,9 млрд вон. Некоторые из этих проектов описаны ниже.
Так, во многом благодаря установкам сухого тушения кокса (УСТК) в коксовом цехе №3 завода Похан, куда Posco вложила 49,4 млрд вон (41,9 млн долларов), компания добилась ежегодной эономии 24 700 т.н.э. энергии. Она также обеспечила выработку 6,8 МВт электричества и 55 тонн пара в час: тепло с инертными газами регенерируется из кокса при температуре 1000оС и утилизируется в котлах высокого давления.
Помимо этого, УСТК в коксовом цехе №2 завода Кангуян позволяют ежегодно сберегать 41 000 т.н.э. энергии. Более того, эти установки разработаны таким образом, что дают возможность регенерировать электричество и пар селективно в зависимости от наличия или нехватки электричества и пара на заводе.
Газ, производимый в коксовых батареях, обязательно сжигается, если в процессе последующего рафинирования обнаруживаются какие-либо отклонения. Печной клапан на заводе был усовершенствован таким образом, что горючие газы, которые обычно поступали в клапан и постоянно сжигались, теперь сжигаются лишь в тех случаях, когда это необходимо. Это позволяет экономить 1 900 т.н.э. энергии в год.
Цехам № 1 и № 2 по производству стали завода Похан, а также цеху № 2 на заводе Кангуян удалось ежегодно экономить соответственно 550 т.н.э. и 516 т.н.э. энергии за счет усовершенствования конструкции горелок, которые использовались для сушки футеровки резервного заливочного ковша, в регенерирующие печные горелки с высокой тепловой эффективностью.
Блюминг завода Похан позволяет экономить 970 т.н.э. энергии путем увеличения доли теплой прокатки (WCR), при которой используются горячие блюмы, поставляемые от машин непрерывного литья через промежуточную нагревательную печь и прокатный стан. Цехи горячей прокатки № 1, № 2 и № 3 на заводе Кангуян сейчас сберегают 2 500 т.н.э. также за счет увеличения доли горячей прокатки.
Станы горячей прокатки №1 и №3 на заводе Кангуян также сэкономили еще 1 500 т.н.э. энергии в результате установки энергосберегающих систем регулируемого напряжения и регулируемой частоты (VVVF) в моторах выходного рольганга, где происходит охлаждение слябов обрызгиванием водой.
В результате совместных усилий группы специалистов, примерно 20 900 т.н.э. энергии было сэкономлено на доменной печи завода Кангуян за счет повышения тепловой эффективности нагревательных печей, отходящие газы которых имеют температуру более 1100оС. Группа остановила свой выбор на автоматической регенеративной компенсационной системе, которая повышает стойкость огнеупорного материала, используемого в нагревательных печах, и позволяет реально контролировать состояние регенерации при впуске горячего воздуха и вводе требуемого количества горючего газа в нагревательные печи.
В дополнение ко всем этим мероприятиям компания ввела в 2002 году систему объективного и последовательного управления расходованием энергии, которая позволяет давать оценку поставленным целям и достигнутым результатам, а также распределять обязанности между отделами. Принятие модели, называемой «системой квотирования потребления энергии» для каждого цеха, также помогает компании укрепить понимание работниками необходимости экономить энергию.
Основываясь на показателях 1997 года, Posco поставила цель сократить свое энергопотребление на 3,7 % в 2003 2007 годах. Для достижения этой цели компания планирует выполнить свыше 600 проектов экономии энергии к 2007 году, таких, как установка котлов регенерации тепла для газа конвертера ЛД в цехе № 2 завода Похан и размещение УСТК в коксовых цехах № 3 и № 4 на заводе Кангуян.
Posco приняла также ряд других энергосберегающих схем. Например, компания поставляет местной районной системе теплоснабжения отработанное тепло со своих заводов. С ноября 2001 года компания использует пар с температурой 260оС и горячую воду с температурой 90оС со своей агломерационной фабрики на заводе Похан для обогрева домов, музеев, торговых центров, школ, учебных заведений и исследовательских центров в близлежащих районах. В этот проект было вложено в целом 28,5 млрд вон, что позволяет компании экономить 11 300 т.н.э. энергии и сократить выброс углекислого газа на 52 000 т в год.
В целях наилучшего использования идей своих сотрудников на новых рынках Posco всячески поощряет их инициативы. Компания Esco (Energy Service Company), созданная в ноябре 2001 года, экспериментальная группа, успешно выполнили проект по сбережению энергии на Posco-CFM Coated Steel Co, совместном предприятии в Даляне (Китай).
Так же оказался успешным проект эмульсионного топлива на полностью принадлежащем компании предприятии Changwon Specialty Steel Co в Южной Корее. По этому проекту топливо смешивается со специальными добавками и превращается в эмульсию. В результате повышается эффективность топлива и сокращается выброс загрязняющих агентов.
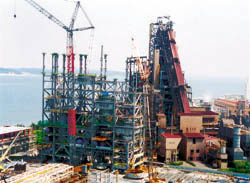
Находящийся в стадии строительства цех Finex на заводе Похан будет экономить энергию, производя чугун непосредственно из железной руды, угля и других материалов. Ему не потребуется агломерация руды или кокса
|
|
Компания Lemsco (Load & Energy Management Service Co), сервисное предприятие Posco, продемонстрировала свой высокий потенциал развития в энергетическом секторе после успешного осуществления проекта по минимизации расходов и повышению эффективности энергоснабжения, проанализировав схемы использования энергии потребителями.
Что касается парниковых газов, то использование УСТК, большее применение скрапа в производстве нержавеющей стали и замена тяжелой нефти чистым топливом дали Posco возможность уменьшить в 1990 2001 годах выбросы углекислого газа на 4,8%.
В самом производстве стали компания занимается разработкой малоотходного процесса Finex, который устранит необходимость применения отдельных стадий агломерации и коксования и сделает возможным прямое использование дешевой рудной мелочи.
Преимущества процесса Finex заключаются в уменьшении выбросов углекислого газа на 19 % по сравнению с существующими процессами, сокращении использования энергии посредством меньшего потребления угля на стадии восстановления железной руды и обеспечении большей доли утилизированных побочных газов. Кроме того, Finex уменьшит выброс окислов серы на 90 %, переводя содержащиеся в угле серные элементы в твердый шлак, который безвреден для окружающей среды.
Компания планирует завершить в апреле этого года строительство демонстрационного цеха Finex с ежегодным объемом производства 600 тыс. т.
Очевидно, что корпоративная деятельность неразрывно связана с использованием ресурсов и энергии. Постоянно стремясь экономить энергию и ресурсы и одновременно повысить свою корпоративную стоимость посредством большего использования регенерированной энергии, Posco вносит весомый вклад в создание современного малоотходного и энергоэкономного производства.
Авторы сотрудники комитета окружающей среды и энергетики компании Posco.
|
|
|
|
|
текущий номер

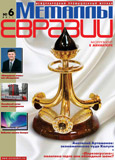
предыдущий номер

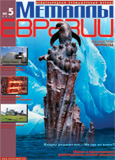
|
|