|
|
Журнал |
|
Архив |
|
Подписка |
|
Реклама |
|
САММИТ |
|
Книжная полка |
|
Контакты |
|
В начало |
|
|
|
| |
|
|
 |
№3' 2003 |
версия для печати
|
|
ПЕРВЫЕ КОНВЕРТЕРЫ !РОССИИ |
КИСЛОРОДНО-КОНВЕРТЕРНОМУ ЦЕХУ НТМК 40 ЛЕТ |
Михаил Аршанский
Директор по инвестициям ОАО «НТМК», кандидат технических наук
2003 году исполняется 40 лет со дня пуска в эксплуатацию конвертерного цеха на Нижнетагильском металлургическом комбинате. Его строительство стало важным событием не только для коллектива НТМК, но и для всей отечественной металлургии. С этого в отрасли началось ускоренное внедрение в промышленных масштабах кислородно-конвертерного способа производства стали с установкой конвертеров садкой 130 370 т.
К тому времени строительство конвертерных цехов стало ведущей тенденцией в мировой металлургии, что объясняется, прежде всего, большей эффективностью такого способа производства стали. В частности, в тогдашних условиях строительство конвертерного цеха обходилось едва ли не на треть дешевле аналогичного по мощности мартеновского, поскольку один конвертер заменял по производительности пять мартеновских печей. Кислородно-конвертерный способ обеспечивал не только наращивание мощностей по выплавке стали в более короткие сроки, но и позволял достигать этого с меньшими затратами сил и средств, снижая себестоимость металла, улучшая его качество, повышая эффективность труда.
Другим важнейшим фактором, повлиявшим на выбор путей дальнейшего развития выплавки стали на НТМК, стала ситуация с обеспечением комбината железорудным сырьем, сложившаяся к началу 60-х годов. Дело в том, что запасы месторождений Тагило-Кушвинского района, которые с момента открытия гор Высокая и Благодать в первой половине XVIII века обеспечивали богатыми рудами нижнетагильские и другие металлургические заводы Урала, постепенно отрабатывались. Руду в Тагил приходилось возить из других регионов, а местные горняки перешли от открытой добычи к строительству шахт. При этом в производство шло сырье с содержанием железа 25 30 %.
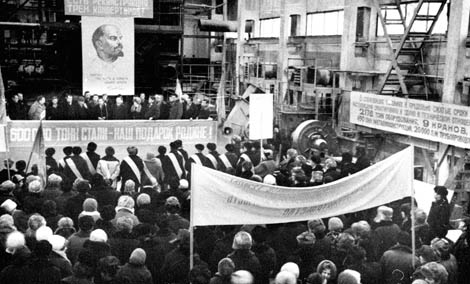 | Митинг в конвертерном цехе 1978 г. (Фото из архива) |
В таких условиях перспективы развития НТМК могли быть обеспечены только использованием титаномагнетитовых руд Качканарского месторождения, расположенного в 140 км от Нижнего Тагила. Оно было известно давно, но освоение сдерживалось из-за низкого содержания железа до 17 %. Кроме того, эти руды содержали ванадий, ценный легирующий элемент, дающий возможность получать стали, способные при эксплуатации выдерживать низкие температуры, что чрезвычайно важно в условиях России. Однако надежной технологии переработки таких руд долгое время не было.
К концу 50-х годов обе эти задачи удалось успешно решить. Исследования показали, что качканарская руда хорошо поддается обогащению, при этом содержание железа увеличивается до 63 65 %. С другой стороны, многолетние опыты, в которых принимали участие и тагильчане, по выплавке стали из руд, содержащих ванадий, привели к разработке революционной по тем временам технологии передела ванадиевого чугуна дуплекс-процессом. В результате было принято решение о строительстве на НТМК кислородно-конвертерного цеха со 130-тонными конвертерами. Комбинат получил надежную сырьевую базу и перспективу дальнейшего развития, а страна, кроме увеличения выплавки стали, источник ценного легирующего металла ванадия. Так тагильские металлурги стали пионерами в освоении кислородно-конвертерного способа производства стали в стране.
Государственное задание на строительство комплекса, выданное в конце 1961 года, предусматривало возведение трех конвертеров, миксерного отделения, шихтового и шлакового дворов, цеха разделения воздуха, градирни и т.д. всего 47 зданий и сооружений, занимающих площадь 50 га. Столь огромный объем работ в основном был выполнен за полтора года. Уже 5 июля 1963 года «Известия» писали о том, что «после тщательного горячего опробования нижнетагильский конвертер, построенный в исключительно сжатые сроки, выдал первую плавку». Акт о приемке цеха в эксплуатацию был подписан в октябре того же года.
Следует отметить, что внедрение кислородно-конвертерного производства стали из ванадийсодержащего сырья встретило сопротивление ряда ученых и возглавляемых ими институтов. Более оправданной они считали технологию дуплекс-процесса, применявшуюся на Чусовском металлургическом заводе. Там на первом этапе использовался конвертер с донным воздушным дутьем, а на втором мартеновская печь. Технология, предложенная для НТМК учеными Уральского института металлов, предполагала в первом конвертере с верхней кислородной продувкой получать ванадиевый шлак и углеродистый полупродукт, а во втором конвертере получать из полупродукта сталь. Особые возражения вызывала продувка полупродукта на сталь во втором конвертере, так как, по мнению оппонентов, «полупродукт, в отличие от чугуна, непригоден для конвертерного передела».
Настойчивая работа ученых и производственников по доводке примененной на НТМК технологии доказала ее эффективность. Она и поныне остается наиболее эффективной в мировой практике. Огромный вклад в ее совершенствование внесли ученые Уральского научно-исследовательского института черных металлов А.И. Пастухов, Л.А. Смирнов, О.М. Чарушников и Центрального научно-исследовательского института черных металлов С.Г. Афанасьев, М.М. Шумов, Т.В. Андреев, П.И. Югов, а также работники комбината Ю.В. Торшилов, В.Г. Удовенко, В.М. Баранов, М.И. Аршанский, М.А. Третьяков, В.Г. Карагодский, В.Г. Арнаутов и др.
Одновременно с технологией совершенствовалось оборудование цеха. Так, в 1964 году здесь впервые в СССР была разработана и внедрена трехсопловая кислородная фурма. Кроме того, вслед за металлургами Липецка тагильские сталеплавильщики в числе первых в российской металлургии стали применять шиберные затворы в стальковшах вместо стопоров, монолитную футеровку ковшей и т.д.
Ценный опыт, накопленный металлургами НТМК в освоении оборудования и технологии кислородно-конвертерного цеха, был учтен при его дальнейшей реконструкции, а также при строительстве подобных цехов на других предприятиях отрасли.
За четыре десятилетия своего существования кислородно-конвертерный комплекс НТМК неоднократно подвергался реконструкции. Например, в конце 60-х годов был установлен 3-й конвертер, 2 миксера, заменены дымососы, которые при этом были вынесены в отдельно стоящее здание. В конце 70-х построили 4-й конвертер на 160 т и три первых заменили на новые такой же мощности.
После реконструкции цех был способен производить 3 млн т стали в год. Однако в общем объеме выпускаемой на комбинате стали в конце 80-х годов он занимал не более 40 %. Большая часть металла по-прежнему выплавлялась в мартенах. В мировой металлургии к этому времени кислородно-конвертерная технология производства стали вместе с электрометаллургией практически полностью вытеснили мартены. При этом до 90 % стали разливается на машинах непрерывной разливки (МНЛЗ). Это обстоятельство ставило комбинат в крайне неблагоприятные условия на мировом рынке, где предстояло стать самостоятельным игроком. Единственным выходом явилась глубокая реконструкция сталеплавильного передела, которая непрерывно продолжалась на протяжении 90-х годов.
В 1990 1995 годах были заменены все четыре конвертера, отработавшие двойной нормативный срок. Поставили новые котлы-охладители, позволившие увеличить интенсивность продувки плавки кислородом до 400 м3 в минуту. Реконструировали газоочистки и заменили дымососы на более производительные.
Одновременно в 1993 2000 годах совместно с австрийской фирмой Voest-Alpine Industrieanlagebau и Уралмашем велось строительство отделения непрерывной разливки в составе трех машин непрерывного литья заготовок.
Сегодня, благодаря дружной и слаженной работе, а также за счет серьезных усилий по выполнению планов технического переоснащения производства конверторщики НТМК дают основной объем производимой на комбинате стали.
В настоящее время управляющей компанией «ЕвразХолдинг» на НТМК реализуется программа развития предприятия на 2003 2008 годы, которая предусматривает снижение доли энерго- и материалозатратных технологий, вывод из эксплуатации устаревших агрегатов, повышение конкурентоспособности продукции комбината как на внутреннем, так и на внешнем рынках. Применительно к производству стали это означает модернизацию конвертерного отделения, строительство установки десульфурации и МНЛЗ № 4.
В течение четырех лет предстоит провести реконструкцию всех действующих конвертеров с заменой котлов-охладителей, систем газоочистки, трактов подачи сырья и шлакоуборки. Кроме того, будут внедрены самые современные средства контроля химического состава плавки и ее температуры в процессе продувки, а также системы отсечки шлака. Автоматическая система управления конвертерной плавкой даст возможность оптимизировать расход кислорода, добиться более высоких технико-экономических показателей.
Важным событием в жизни конвертерного цеха должен стать ввод в строй МНЛЗ № 4. Согласно договору, заключенному с австрийской фирмой Voest-Alpine Industrieanlagebau, машина должна быть сооружена «под ключ». Срок строительства составляет 22 месяца. Проектная мощность МНЛЗ № 4 1,5 млн т слябов в год. Ввод этой машины в строй действующих позволит комбинату полностью отказаться от разливки стали в слитки, а также укрепить свое положение на мировом рынке.
Особо следует сказать о дальнейшем развитии на комбинате вторичной металлургии, во внедрении которой НТМК опережает многих коллег по отрасли. В конвертерном цехе уже действуют две установки доводки стали печь-ковш и вакууматор типа RH для дегазации стали, прежде всего, используемой для производства транспортного проката (рельсы, колеса, бандажи). Программа модернизации предполагает строительство еще одной установки печь-ковш и вакууматора. Кроме того, в настоящее время совместно с германской фирмой Krupp-Polisius ведется строительство установки десульфурации полупродукта с целью сокращения затрат на производство высококачественной стали с пониженным содержанием серы. С завершением этого строительства в июле 2003 года НТМК будет иметь полный набор агрегатов внепечной металлургии.
Ключевой вопрос любой программы развития инвестиции. Управляющая компания «ЕвразХолдинг» решает этот вопрос, используя самые разные варианты привлечения средств. Так, в 2002 году НТМК получил инвестиционный облигационный заем на сумму в 1 млрд рублей.
Для МНЛЗ № 4 сформирован пакет финансирования за счет иностранных кредитов, что является серьезным достижением инвестиционной политики «ЕвразХолдинга» и НТМК.
Еще один интересный вариант найден в финансировании строительства производства реагентов для установки десульфурации. Для ее эффективной и бесперебойной работы необходимо иметь стабильную и отлаженную схему поставки расходных материалов гранулированного магния, флюодизированной извести и специальных фурм.
На сегодняшний день в России только одно предприятие выпускает гранулированный магний, а производство других расходных материалов отсутствует. Поэтому принято решение организовать собственное производство извести и фурм. А для этого следует учредить совместное предприятие, участниками которого будут ОАО «НТМК» и фирма Almamet (Айнринг, Германия), располагающая необходимыми технологиями и оборудованием.
Предполагается создание двух производств: участка по подготовке десульфурирующих реагентов на базе цеха НТМК по обжигу извести в г. Кушве и участка по изготовлению специальных фурм на огнеупорном производстве комбината. При этом Almamet предоставляет ноу-хау и оборудование, а НТМК оплачивает строительно-монтажные работы. Незначительное расстояние между Нижним Тагилом и Кушвой, связанных между собой автомобильным и железнодорожным сообщением, позволяет минимизировать затраты на производство реагентов, организовать новые рабочие места в Кушве.
Такое разнообразие форм инвестирования (кредиты, облигационные займы, совместное предприятие) убедительное свидетельство высокого рейтинга доверия к НТМК со стороны инвесторов как в России, так и на Западе. С другой стороны это гарантия успешного выполнения намеченных программ модернизации и развития производства, в том числе в сталеплавильном переделе.
Выполнение программы модернизации конвертерного цеха даст возможность довести объем выплавляемой стали до 5 млн т в год, заменить физически и морально устаревшее оборудование, вывести из эксплуатации оставшиеся печи мартеновского цеха и блюминг, уменьшить расход металла при получении проката за счет полного перехода на непрерывную разливку стали, существенно повысить ее качество, снизить выбросы вредных веществ в атмосферу.
Особо хотелось бы подчеркнуть, что предполагаемое закрытие устаревших производств не приведет к обострению социальной напряженности. Во-первых, комбинат будет стимулировать выход на пенсию тех, кто свое отработал и заслужил право на отдых. Во-вторых, предусмотрена переподготовка освобождаемых работников.
Таким образом, уже в ближайшем будущем сталеплавильное производство НТМК будет отвечать современным требованиям как с точки зрения технической, так и технологической.
В планах управляющей компании «EвразХолдинг» сделать Нижнетагильский металлургический комбинат современным предприятием, оптимально сбалансированным по всем переделам, выпускающим конкурентоспособную продукцию, успешно решающим социальные проблемы своих работников. Выполнение программы модернизации и развития сталеплавильного производства это важный шаг к намеченной цели, новый этап в развитии первого в стране кислородно-конвертерного комплекса.
|
|
|
|
|
текущий номер

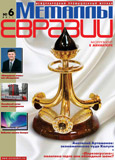
предыдущий номер

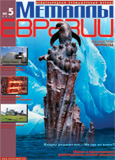
|
|