Леонид Казанбаев Технический директор ОАО «Челябинский цинковый завод»
Как и на любом старом предприятии, в цехах завода можно встретить сегодня оборудование и даже целые переделы разного технического уровня и состояния. В 1935 году первоначальная производственная мощность предприятия была рассчитана на выпуск 20 тыс. т цинка. За время существования завода его основные цеха и переделы неоднократно подвергались частичной модернизации, и к началу 90-х годов производственная мощность возросла до 130 тыс. т, то есть фактически на тех же площадях выпуск основной продукции удалось увеличить в 6,5 раза. По-видимому, на этом завершился первый этап реконструкции предприятия.
К началу 90-х годов завод подошел с весьма старыми основными фондами (степень износа около 80 %). Несмотря на это, до начала перестройки завод 65 кварталов подряд по результатам работы завоевывал переходящее Красное Знамя Министерства цветной металлургии Союза. Однако практически все ресурсы модернизации были исчерпаны. Стало очевидным, что дальнейшее развитие предприятия при том же подходе не имеет перспективы, так как реконструкция устаревших мощностей не могла обеспечить прирост экономической эффективности и соблюдение жестких экологических нормативов. Современное оборудование просто не вписывалось в старые корпуса.
Уже в середине 80-х годов встал вопрос о новом этапе модернизации предприятия. При этом в результате длительного и детального анализа был выбран обоснованный вариант создания высокоавтоматизированного производства, отвечающего самым передовым технико-экономическим критериям, в результате чего Челябинский завод стал бы одним из самых современных и эффективных предприятий по выпуску цинка в мире.
В 1986 году в результате тендера за основу был выбран проект итальянской инжиниринговой компании «Снампроджетти», который должен был стать базовым в проведении второго этапа реконструкции ЧЦЗ. В качестве главного новшества проект предусматривал переход на работу с суперкатодами площадью 3,4 м2 (в настоящее время 1,2 м2) в новом зале электролиза при значительном усовершенствовании сопряженных переделов и всей инфраструктуры для достижения годовой мощности предприятия в 200 тыс. т цинка при существенном повышении качества продукции. При этом сохраняется технологическая основа гидрометаллургический способ производства, что полностью отвечает требованиям безотходной технологии. Специфика этого способа замкнутый цикл с высоким уровнем извлечения цинка (97,1 %) из исходного концентрата. Сохраняется и основная продуктовая специализация завода: кроме цинка, производятся сплавы на его основе, металлический кадмий и индий, а также серная кислота, клинкер сырье для медной промышленности, свинцовый кек, отгружаемый на заводы по выпуску свинца, технический цинковый купорос.
К сожалению, реализация проекта «Снампроджетти» была приостановлена в начале 90-х годов в связи с ликвидацией централизованного финансирования после распада СССР, хотя компания к тому времени поставила все необходимое оборудование.
Работа возобновилась в 1997 году, и после нескольких авторитетных экспертиз мы убедились, что основные положения проекта «Снампроджетти» не утратили своей технической новизны. На завершающем этапе генеральным менеджером выступала финская компания «Оутокумпу». Эти работы выполнялись не только по первоначальному проекту, но и в соответствии с локальными инвестиционными программами. Было приобретено дополнительное оборудование, полностью обновлена электроника, подготовлены специалисты. Инвестиционные затраты на реализацию этого этапа реконструкции составили 68,5 млн. долл.
В нынешнем году, который станет, по-видимому, историческим для ЧЦЗ, несмотря на неблагоприятную конъюнктуру мирового рынка, на заводе заканчивается второй этап реконструкции. Главным его звеном является завершающий этап строительства одного из самых совершенных в мире автоматизированных комплексов электролиза цинка (АКЭЦ) мощностью 200 тыс. т металла марки Special High Grade (SHG).
9 октября 2002 года на заводе произошло поистине знаменательное событие, которое его ветераны ждали долгие годы. Была подана электроэнергия на первую серию электролизных ванн нового комплекса и получен первый катодный цинк высокой чистоты.
Некоторые блоки нового комплекса были пущены в эксплуатацию еще в 2001 году: отделение очистки растворов, установки охлаждения электролита и вывода гипсовых осадков, кадмиевое отделение, участок производства анодов, компрессорная станция. На остальных объектах нового комплекса ведутся пусконаладочные работы, которые к концу 2002 года должны завершить ввод его в промышленную эксплуатацию. Наиболее важными являются отделения переплавки катодного цинка и производства сплавов на его основе, получения цинкового порошка и переработки дроссов.
Важнейшим моментом программы реконструкции является сбалансированная модернизация всех основных переделов производственного цикла. Так, в обжиговом цехе произведена полная замена трех обжиговых печей и двух электрофильтров, в выщелачивательном цехе реконструкция шести сгустителей и строительство установки переработки цинксодержащих отходов, в вельц-цехе замена трех вельц-печей вместе со вспомогательным оборудованием, в гидрометаллургическом цехе реконструкция установки экстракции индия. Характерно, что в результате этих мероприятий уровень износа оборудования снизился до 30,9 %.
Что даст пуск нового электролизного комплекса? Прежде всего, он позволит резко сократить уровень производственных затрат. Так, удельный расход электроэнергии сократится на 50 кВт . ч/т цинка, при этом годовая экономия электроэнергии оценивается в 7,5 млн. кВт . ч. На 600 700 тыс. м3 в год сократится расход промышленной воды. За счет увеличения срока службы анодов и катодов будет сокращен расход свинца, алюминия и серебра. Расход цинковой пыли, применяемой при очистке растворов, снизится на 20 30 %. При этом появится возможность производить тонкодисперсный цинковый порошок на продажу.
Автоматизация резко улучшит условия труда, полностью ликвидирует тяжелые ручные операции, позволит сократить численность обслуживающего персонала цеха с 400 до 250 280 человек. По расчетам, после пуска комплекса на полную мощность производительность труда должна возрасти в 1,6 раза.
Существенно меняется качество основной продукции завода. ЧЦЗ становится единственным в России предприятием, способным выпускать цинк чистотой 99,995 % марки SHG, отвечающей самым высоким требованиям мирового рынка. Цинк такой марки будет зарегистрирован на Лондонской бирже металлов (ЛБМ), что существенно расширяет возможности повышения валютных поступлений. Челябинский завод после ввода соответствующего плавильного оборудования сможет выпускать сплавы на основе цинка ЦАМ (цинк-алюминий-медь), спрос на которые довольно велик около 10 15 тыс. т ежегодно.
Разумеется, и после пуска АКЭЦ реконструкция нашего предприятия будет продолжена. Во-первых, необходимо подтянуть до требуемого технического уровня сопряженные переделы и заводскую инфраструктуру для того, чтобы обеспечить в перспективе выход АКЭЦ на проектную мощность 200 тыс. т. Согласно программе третьего этапа реконструкции, который рассчитан на ближайшие пять лет, предстоит провести комплекс работ с выходом на уровень выпуска 180 тыс. т цинка за счет получения 160 тыс. т из сульфидных концентратов и 20 тыс. т из вторичных материалов. Уже в первой половине 2003 года предполагается сдать в эксплуатацию заново построенную пятую систему сернокислотного цеха. Среди других важных объектов программы модернизации строительство пятой вельц-печи и расширение гидрометаллургического цеха, а также установка удаления ртути из обжиговых газов. Общие затраты на проведение этого этапа реконструкции оцениваются в 57 млн. долл.
В процессе выполнения этого этапа мы планируем исследовать различные виды цинкового сырья с целью снижения стоимости его переработки, а также оценить потенциальную структуру рыночного спроса на различные виды продукции.
Ответы на эти вопросы должны логично подготовить следующий, завершающий этап реконструкции, в котором выход на максимальную проектную мощность 200 тыс. т цинка в год достигался бы при минимальных эксплуатационных затратах, высокой конкурентоспособности и доходности продукции и полном соответствии самым жестким экологическим критериям. Мы предполагаем, что для этого потребуется модернизация и увеличение мощности обжиговых печей и сернокислотных установок, повышение мощности выщелачивательного и гидрометаллургического цехов, а также строительство шестой вельц-печи. Предварительные расчеты показывают, что после завершения этого этапа Челябинский цинковый завод по своему техническому уровню будет соответствовать лучшим мировым стандартам. Подобный уровень должен обеспечить самые низкие эксплуатационные затраты, что существенно повысит конкурентоспособность нашей продукции на рынке.
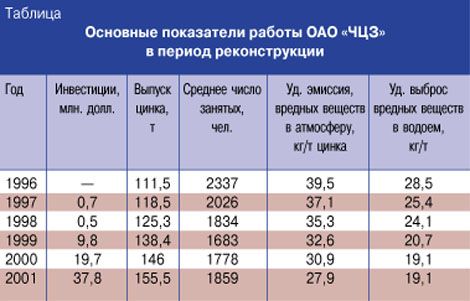
Разумеется, реализация этой стратегии во многом будет определяться наличием инвестиционных ресурсов, которые предполагается получить как из собственной прибыли, так и за счет заемных средств. Оптимизм наших прогнозов обусловлен, прежде всего, успешной работой завода, высокой востребованностью нашей продукции на рынке, наличием управляющей команды единомышленников и дальновидной политикой собственника предприятия компании «Евромин».
|