Леонид Смирнов Генеральный директор ГНЦ РФ "Уральский институт металлов", член-корреспондент РАН Юрий Сорокин Исполнительный директор программ "Переработка техногенных образований Свердловской области", кандидат технических наук Яков Школьник Заведующий лабораторией, доктор технических наук
В черной металлургии при выплавке чугуна, стали и ферросплавов неизбежно образуется большое количество технологических отходов. Из них 80 % приходится на шлаки, которые образуются из пустой породы, флюсов, золы, а также продуктов окисления металла и примесей. Суммарное содержание оксидов кальция, железа и кремния в шлаках достигает 75 % .
Годовой выход шлаков на предприятиях черной металлургии России в 1991 году составил 31,7 млн. т. К 2000 году из-за снижения производства металла он уменьшился, по оценочным данным, примерно до 24,7 млн. т. Кроме того, в отвалах уже находится около 350 млн. т шлаков, занимающих свыше 600 га.
Металлургические шлаки по своим физико-механическим свойствам не только не уступают, но в ряде случаев превосходят качество заменяемых ими природных материалов. Это предопределяет широкие перспективы использования отходов в народном хозяйстве. Так, в течение многих лет доменные шлаки широко применяются для изготовления шлакопортландцемента, объем производства которого в 1990 году составил около 30 млн. т.
Одним из перспективных направлений комплексной переработки шлаков является организация производства литых изделий, шлакоситаллов и других стеклокристаллических материалов на их основе. Закристаллизованные шлаки обладают высокой износо-, термо- и кислотостойкостью. Шлакокаменное литье по своим прочностным свойствам соответствует бетону марки 600 700, может выдерживать температуру до 900 оС. Литые изделия, кроме бетона, заменяют металл и огнеупорные материалы, что увеличивает срок службы оборудования и сооружений в 2 6 раз. Уральским институтом металлов совместно с другими организациями проведены крупные исследования по отработке технологии производства тюбингов и других изделий, используемых при строительстве метро.
В ряде регионов страны ощущается острый дефицит в дорожно-строительных материалах. Зарубежный, а также отечественный опыт свидетельствует, что шлаки (особенно сталеплавильные) эффективны для применения во всех слоях дорожных "одежд", причем в дорогах различной сложности, в том числе и аэродромных.
Высокие прочностные и износостойкие качества шлаков предопределили возможность использования их для производства абразивов, которые применяются для струйной обработки поверхности металла и по качеству превосходят зарубежные при значительно меньшей стоимости.
Наиболее ценной составляющей шлаков является металл, среднее содержание которого оценивается в 10 12 % их объема. Из доменных и сталеплавильных шлаков ежегодно извлекается 1,5 2 млн. т металла. Расчеты показывают, что в отвалах предприятий черной металлургии содержится около 42 млн. т металлического железа. К примеру, если извлечь весь металл из шлаков, его хватит для обеспечения вторичным сырьем сталеплавильного производства такого мощного предприятия, как "Северсталь", на 20 лет!
В настоящее время, учитывая современные требования к охране окружающей среды, стоит задача создания специального оборудования для переработки шлаков и отлаживания технологических процессов, исключающих выбросы вредных веществ.
В последнее десятилетие, несмотря на общий спад производства черных металлов в России, уровень переработки шлаков по отношению к текущему годовому выходу возрос с 98,7 % до 118,2 % (табл. 1). Введены дополнительные соответствующие мощности на Нижнетагильском, Новолипецком, Магнитогорском комбинатах, "Северстали", Северском трубном и других предприятиях. Приведенные данные свидетельствуют, что если к ликвидации отвалов доменных шлаков приступили более масштабно, то объем сталеплавильных и ферросплавных продолжает увеличиваться.
Наиболее распространенной продукцией из доменных отходов является гранулированный шлак, доля которого в общем объеме материалов переработки составляет 65 %. Грануляция позволяет эффективно сочетать задачи шлакоуборки с получением ценного строительного материала.
На новых доменных печах № 6 в ОАО "Новолипецкий металлургический комбинат" и № 5 в ОАО "Северсталь" внедрена припечная грануляция шлака. Однако и этот способ уборки имеет недостатки, главные из которых потребность значительных площадей непосредственно у печи, невозможность производства других, кроме гранулированного шлака, видов продукции, высокая энергоемкость процесса и большие эксплуатационные затраты.
В большинстве действующих доменных цехов вообще нет возможности перерабатывать шлак непосредственно у печей. Традиционно он вывозится в стальных нефутерованных ковшах емкостью 11 18 м3. Это требует большого парка шлаковозов, установок для удаления и переработки ковшовых остатков после каждого слива шлака, значительных затрат на замену шлаковых чаш (их срок службы около года) и ремонт ковшей. Такой вид уборки повышает себестоимость чугуна, а в ряде случаев даже сдерживает его производство. Причем попавший в шлак чугун удается извлечь лишь частично.
Уральский институт металлов совместно с рядом предприятий разрабатывает принципиально новую технологию уборки доменного шлака с помощью шлаковозов-миксеров повышенной емкости. Этому предшествовали исследования для определения возможности транспортировки в закрытом нефутерованном ковше емкостью 16 м3 без удаления ковшовых остатков после каждого слива. При конструировании шлаковозов в качестве исходных требований приняты условия работы в существующих доменных цехах. Новый шлаковоз, имея значительно увеличенную емкость ковша, должен вписываться в существующие железнодорожные габариты и при постановке у доменных печей отвечать всем требованиям техники безопасности. Ковш рассчитан на накопление осаждающегося из шлакового расплава металла и периодический его слив. Проектирование и изготовление первых таких машин осуществлено в Днепропетровске. Применение шлаковозов-миксеров обеспечит:
уменьшение парка шлаковозов в 3 4 раза и работу без удаления ковшовых остатков после каждого слива;
повышение на 25 30 % степени переработки шлака в жидком виде, что увеличит ресурсы для производства гранулированного шлака, пемзы, литых изделий и другой эффективной продукции;
практически полное извлечение и использование расплавленного чугуна, содержащегося в шлаке.
В основе процессов грануляции лежит переохлаждение расплавов до стеклообразного состояния, так как доменные шлаки с подобной структурой обладают потенциальными вяжущими свойствами. В связи с этим гранулированные шлаки широко используются в цементной промышленности в качестве активной минеральной добавки.
Как правило, для переохлаждения шлакового расплава до стеклообразного состояния используется вода. Поэтому такие процессы производства имеют существенные недостатки:
большой расход воды;
высокая (до 20 %) влажность продукции;
наличие в парогазовых выбросах токсичных сернистых соединений, концентрация которых в десятки раз превышает предельно допустимые нормы.
В связи с этим за последние годы большое внимание в институте уделяется разработке процессов переохлаждения расплавленных шлаков, исключающих контакт расплава с водой, которая используется лишь на второй стадии при грануляции. Это достигнуто в принципиально новом способе двухстадийной схемы охлаждения. На первой стадии шлаковый расплав на 300 400 оС охлаждается на металлической поверхности, а затем в воде. В настоящее время разработаны различные варианты агрегатов для этого способа, защищенные авторскими свидетельствами и патентами Российской Федерации. Промышленное опробование технологии проведено на Металлургическом заводе им. А.К.Серова.
Для шлаковых расплавов, отличающихся большой заметалленностью или по химическому составу склонных к силикатному распаду, принцип двухстадийного охлаждения реализован в агрегатах барабанного типа с шаровой насадкой. Первая стадия охлаждения осуществляется в перемещающемся межшаровом пространстве. Это обеспечивает остеклованность шлака и стабилизацию его структуры. На Синарском трубном заводе внедрена технология охлаждения ваграночного шлака в перемещающемся межцепном пространстве.
Оценка технологии производства гранулированного шлака по двухстадийной схеме охлаждения расплава показала, что выбросы сернистых газов в несколько раз ниже по сравнению с обычной технологией. При этом новый материал имеет ту же степень остеклованности, более низкую влажность, водоудерживающую способность и более высокую насыпную массу.
Еще одним важным направлением переработки шлаковых расплавов является производство пористых заполнителей для бетонов. Наиболее эффективным оказался заполнитель сфероидальной или близкой к ней формы с остеклованной поверхностью шлакопемзовый гравий, по своим физико-механическим свойствам имеющий преимущества перед обычной шлаковой пемзой.
Содержание стеклофазы в шлаковой пемзе оказывает большое влияние на теплопроводность шлакопемзобетона. Гидравлическая активность поверхностного слоя заполнителя, его стеклообразная структура обеспечивают более высокую прочность сцепления с цементным тестом, в результате чего повышается прочность бетона. Производство такого заполнителя осуществлено по разработанной Уральским институтом металлов и внедренной в ОАО "НЛМК" технологии, предусматривающей поризацию расплава на вибрирующей поверхности и дробление поризованной массы быстровращающимся барабаном.
Сталеплавильные шлаки в настоящее время перерабатываются в твердом виде тоже по двухстадийной технологии. Первая стадия термодробление, подготовительный этап для дальнейшего механического дробления или самостоятельный для производства нефракционированного шлакового щебня. Суть технологии в охлаждении шлака водой при температуре выше порога дробимости. За счет температурных градиентов возникает напряженное состояние шлаковых монолитов и их самодробление.
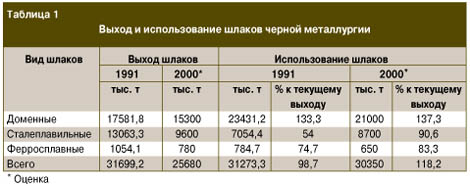 При первичной переработке шлака извлекается крупный стальной скрап, который большей частью свободен от включений и примесей и часто не нуждается в дополнительной очистке. Его зашлакованность обычно не превышает 5 7 %, а масса нередко достигает 2 3 т и больше. Весь крупный скрап перед возвращением в плавку разрезается на габаритные куски в зависимости от вида металлургического производства. Более мелкий скрап, средней массой 200 250 кг, имеет зашлакованность 10 40 %. Очистка производится с помощью падающего груза. Как показали исследования, проведенные на НТМК и ММК, при первичной переработке шлаков с использованием крановых электромагнитов может быть извлечено 60 65 % металла. Однако мелкие куски скрапа чаще всего извлекаются с помощью магнитных сепараторов.
В отечественной практике сложились три варианта вторичной переработки шлаков в зависимости от вида получаемой продукции. По первому на установках производится только фракционированный щебень. Извлекаемый металл возвращается в металлургический передел. Годовая производительность установок колеблется от 140 тыс. т (Таганрогский металлургический завод) до 3 млн. т (НТМК). Практически все установки работают с использованием отечественного оборудования. На "Северстали" дробильно-сортировочная установка построена по финской технологии с применением импортного оборудования, на НТМК эксплуатируется комплекс, смонтированный немецкой фирмой. Оба комплекса существенно дороже, чем отечественные установки, которые при хорошо организованной сепарации и выборке металла перед дроблением вполне надежны.
Ко второму варианту переработки шлака относятся установки по получению шлаковых удобрений мелиорантов (завод "Амурсталь").
Опыт показывает, что экономически целесообразно сочетать дробление с помолом (третий вариант), причем на помол отправлять только фракции 5 или 10 мм, неизбежно образующиеся при дроблении и сортировке. По такой схеме работает цех переработки шлаков сталеплавильного производства НЛМК. На установке производится фракционированный щебень для доменных печей и дорожного строительства, а также шлакоизвестковая мука для сельского хозяйства.
В табл. 2 приведены данные о выпуске продукции из сталеплавильных шлаков в последнее десятилетие. Больше половины составляет щебень для дорожного строительства. Почти 30 % продукции, получаемой из шлаков, возвращается в металлургическое производство. Доля мелиорантов около 1 %. Вероятно, такое соотношение сохранится в ближайшей перспективе.
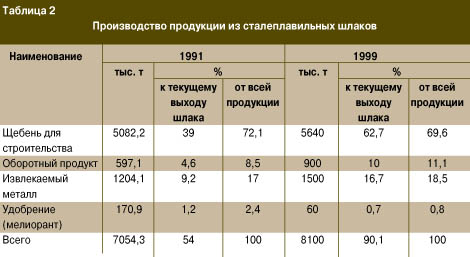 В последние годы Уральским институтом металлов разработана и внедрена на "Азовстали" и Алапаевском металлургическом заводе технология производства шлаковых абразивов для струйной обработки металла. Хотя их выпуск на предприятиях составляет всего 5 10 тыс. т в год, эта продукция в силу высокой стоимости существенно повышает экономичность переработки шлака. В дальнейшем получение абразивов целесообразно предусматривать как побочное производство при переработке сталеплавильных шлаков. Потребность в абразивах испытывают все регионы страны, но эти материалы ввозятся из-за рубежа по высоким ценам, причем по качеству импортные зачастую уступают отечественным.
Необходимо отметить, что существующее оборудование, как правило, недостаточно приспособлено для переработки твердых шлаков и потребляет немало энергии. Кроме того, процесс сопряжен со значительным выделением пыли, что требует специальных аспирационных агрегатов. Но эти недостатки устранимы при переработке шлаков в расплавленном состоянии, при котором, например, энергетические потребности почти на порядок ниже.
Разработаны способы грануляции сталеплавильных шлаков с применением газовых энергоносителей. Технология отлажена на "Северстали" (конвертерные шлаки), Сулинском металлургическом заводе (мартеновские) и ОЭМК (распадающиеся электросталеплавильные шлаки).
Гранулированный шлак обладает повышенной активностью, имеет влажность менее 1 %, поэтому может использоваться без предварительной сушки в цементной промышленности, а также в качестве добавок в аглошихту. Исследования, проведенные Уральским институтом металлов совместно с Воронежским инженерно-строительным институтом и строительной лабораторией в г. Губкине, показали, что гранулированные сталеплавильные шлаки после помола пригодны как вяжущие в автодорожном строительстве и при закладках горных выработок. Испытания сулинских гранулированных мартеновских шлаков, выполненные нашим институтом совместно с Северокавказским НИИ сельского строительства, показали, что после помола граншлака образуется вяжущее марки 150 200, а при активизации небольшим количеством щелочи активность повышается до марки 800. Бетоны на базе этих вяжущих отличаются повышенной кислото- и коррозионностойкостью.
На основе этих опытов создана технология и подготовлены предпроектные проработки по воздушной грануляции конвертерных шлаков с утилизацией тепла, что наиболее рационально решает проблему комплексного использования расплавов. Утилизированное тепло пойдет для прогрева шихты конвертеров. Результаты исследований заложены в технологическое задание по переработке конвертерных шлаков КМК, по которому Сибгипромезом подготовлен проект отделения воздушной грануляции расплава.
Среди технических решений, разрабатываемых и применяемых для охлаждения и дальнейшей переработки жидких шлаков, перспективными, на наш взгляд, являются технологические процессы, позволяющие охлаждать шлаковый расплав на металлической поверхности. С целью увеличения скорости охлаждения и придания продукту переработки необходимых форм и размеров были проведены исследования в условиях слива шлака на металлические тела различной конфигурации. В этом случае расплав проникает в пустоты между телами, используя большую площадь охлаждения, при этом получается щебень с заданными параметрами.
На основе этого принципа разработан агрегат в виде заключенного в кожух барабана с горизонтальной осью вращения и обечайкой, набранной из колосников. Установка испытана на доменных, сталеплавильных и ферросплавных шлаках ряда предприятий. Агрегат может принимать шлаковые расплавы в широком интервале химических составов и температур.
Годовой выход ферросплавных шлаков существенно ниже, чем доменных и сталеплавильных, однако в силу своих свойств они представляют особый интерес для переработки. Так, потери металла со шлаками низкоуглеродистого феррохрома достигают 15 % за плавку, а со шлаками ферросиликокальция 6 10 %. Большая часть ферросплавов обладает низкими магнитными свойствами, поэтому способы магнитной сепарации для них неприемлемы. Для извлечения ферросплавов из отвальных шлаков хорошие результаты дали способы обогащения на пневматических сепараторах типа СП6 и СП12, а также рентгенорадиометрические. В частности, обогащение шлаков высокоуглеродистого феррохрома на пневмосепараторах позволило увеличить извлечение металла до 75 % против 40 %, обеспечиваемых магнитной сепарацией.
Ферросплавные шлаки частично используются в самой металлургии. Так, на Ключевском заводе ферросплавов шлак от текущего производства металлического хрома, а частично и отвальный используются для выплавки углеродистого феррохрома, а шлаки ферротитана реализуются как легирующие добавки, а также применяются при производстве высокоглиноземистого клинкера.
Самораспадающиеся шлаки низкоуглеродистого феррохрома имеют повышенное содержание оксидов кальция и магния и годны как химические мелиоранты в сельском хозяйстве, а также как добавка для самотвердеющих формовочных смесей в литейном производстве. Шлаки высокоуглеродистого феррохрома обладают высокой температуростойкостью, поэтому используются в огнеупорной промышленности.
Таким образом, металлургические шлаки, представляющие определенную ценность для хозяйственной деятельности, сосредоточенные в промышленных зонах с избытком рабочей силы, на относительно небольших площадях со всеми необходимыми коммуникациями, не требующие дорогостоящих вскрышных работ, следует рассматривать как дешевую сырьевую базу для ряда отраслей. Большие запасы сырья, разнообразие способов и энергонасыщенность шлакопереработки вынуждают относиться к ней как к самостоятельной подотрасли. Главной задачей следует считать 100 %-ную переработку шлаков текущего производства и максимальную отвальных, а также создание технологий, гарантирующих защиту окружающей среды, наибольшее извлечение металла, получение оборотного продукта, граншлака, щебня и других материалов и изделий.
|