Иван Лещенко Государственное научно-производственное предприятие "Аэрогеология"
Согласно комплексной оценке Горного бюро США, хромовые руды по своему стратегическому значению занимают десятое место среди 36 важнейших видов минерального сырья. Для России, Китая и почти всех промышленно развитых стран, кроме ЮАР и Финляндии, проблема обеспечения металлургии хромовыми рудами весьма актуальна из-за крайней ограниченности, а чаще полного отсутствия их запасов в недрах. Тот факт, что хром является обязательным и практически незаменимым компонентом нержавеющей стали и многих спецсплавов, применяемых в аэрокосмической промышленности и других отраслях, определяющих научно-технический прогресс, придает сырьевой проблеме особую остроту.
На долю металлургии приходится более 80 % мирового потребления хромовых руд. Оставшаяся их часть расходуется на выпуск хромистых химикалий около 10 %, хромомагнезитовых и других хромсодержащих огнеупоров и хромобетона 4 5 %, а также хромитового литейного песка 3 4 %.
История промышленного применения хрома насчитывает более двух веков. В 1766 году на Урале, в районе Екатеринбурга был найден новый минерал красивого красного цвета "сибирский красный свинец", впоследствии определенный как хромат свинца (PbCrO4) и получивший название крокоит. Измельченный крокоит в небольших объемах использовался в Европе и России в качестве стойкой на свету оранжево-желтой краски. В 1797 году французский химик Воклен, а годом позже немецкий ученый Клапрот выделили из "сибирского красного свинца" неизвестный ранее металл, получивший название хром от греческого слова "краска" из-за яркой и разнообразной расцветки своих многочисленных соединений.
Известно около 40 минералов, содержащих хром. Однако единственным природным промышленным источником получения металлического хрома, его многочисленных сплавов, соединений, а также огнеупоров и литейного песка являются месторождения минералов группы хромшпинелидов, получивших общее название хромиты. Начало применения хромовых руд в металлургической промышленности с выпуском феррохрома и легированных хромом сталей относится к концу XIX века.
Применение хрома в металлургии основано на его жаропрочности, твердости и устойчивости к коррозии, причем все эти качества придаются и хромовым сплавам. Товарные хромовые руды металлургических сортов почти полностью перерабатываются в различные сорта феррохрома (содержащего 52 70 % хрома, 30 40 % железа и 0,1 8 % углерода) и лишь 2 3 % руд расходуется на изготовление хромсодержащих лигатур. Основная часть феррохрома около 90 % используется в сталелитейной промышленности, в том числе до 75 % для выплавки нержавеющей стали.
Хромистые и хромоникелевые нержавеющие стали (содержащие в среднем 18 % Cr и 8 % Ni) применяются главным образом в машиностроении, в качестве конструкционного материала для арматуры крекинг-установок, для выпуска строительной арматуры (уголков, труб и др.), кровельных материалов, аппаратуры химических и пищевых предприятий, различных инструментов (включая хирургические), торгового оборудования, предметов быта, для архитектурных и скульптурных сооружений. Хром является обязательным компонентом жаропрочных, кислотоупорных, быстрорежущих, рессорных, шарикоподшипниковых и других качественных сталей, а также некоторых сортов литейного чугуна.
Объемы выплавки нержавеющей стали определяют спрос как на товарную хромовую руду, так и на феррохром. В долгосрочной перспективе общий рост выпуска этой продукции особых сомнений не вызывает. Основанием для подобного вывода служит устойчивая тенденция роста выплавки нержавеющей стали (при кратковременных спадах) в среднем более чем на 5 % в год за 1950 1998 годы. Нет оснований сомневаться и в дальнейшем расширении потребления хромовых спецсплавов, учитывая стабильный рост продукции авиационной и ракетно-космической промышлености. Таким образом, вполне определенно существует необходимость дальнейшего развития и освоения минерально-сырьевой базы производства хромсодержащей продукции.
Подтвержденные запасы хромовых руд разведаны более чем на 300 месторождениях 27 стран и на 1 января 1999 года составляли 4,5 млрд. т. Для минерально-сырьевой базы хромоворудной промышленности характерна высокая степень концентрации: в двух странах ЮАР и Казахстане сосредоточено почти 90 % мировых подтвержденных запасов хромитов. Крупными их запасами располагают также Зимбабве, Индия, Финляндия, Филиппины и Турция, а суммарная доля остальных 20 стран составляет всего 2,6 % (рис. 1), в том числе России 0,08 %.
Месторождения хромитов ЮАР находятся в пределах крупнейшего в мире расслоенного блюдцеобразного интрузивного массива Бушвельд общей площадью 67 тыс. км2, протянувшегося на 480 км в широтном и на 250 км в меридиональном направлении. Слои основных и ультраосновных пород наклонены к его центру под углами 10 12о. Все эксплуатируемые месторождения располагаются по периферии интрузива. В Северо-Западной провинции, в районе городов Рюстенбург и Бритс, находится Западный хромитовый пояс длиной 160 км, а в провинциях Мпумаланга и Северная, в районе городов Стилпурт и Лейденбург, Восточный пояс длиной 112 км. Хромитоносные горизонты тяготеют к нижней части расслоенного массива, где выявлено до шести промышленных пластов. Выдержанные по мощности рудные пласты прослеживаются по падению и простиранию на десятки километров. Мощности их колеблются от 1 до 1,8 м.
Качество трансваальских руд низкое; в значительной мере это относится к их агрегатному состоянию: доля кусковой руды, наиболее предпочтительной для плавки на феррохром, в суммарной добыче (и запасах) хромитов составляет только 25 30 %, тогда как рыхлые тонкозернистые, пылевидные разности (friable, fine), препятствующие газовыделению и нормальному ходу плавки, более 70 %. Среднее содержание Cr2O3 в целом по Бушвельдскому комплексу составляет 37 %. Выделяемая грохочением кусковая руда содержит 39 % Cr2O3, а оставшиеся мелкие фракции, содержащие в среднем 36 % Cr2O3, обогащаются в 45 %-ный концентрат. Качество концентрата, получаемого пока в небольших объемах из отходов переработки платиноносных хромитов пласта UG2, несколько ниже 42 %. Среднее содержание Cr2O3 в товарной хромовой руде горно-обогатительных комбинатов ЮАР с учетом реального соотношения кусковой руды и концентрата оценивается также в 42 %.
Низкое соотношение Cr2O3/FeO не позволяет получать ферросплавы с содержанием хрома более 52 55 %, а в сплаве, получаемом из отходов обогащения платиновых руд пласта UG2, оно не превышает 48 %. Низкое содержание хрома, однако, не препятствует успешному использованию южноафриканского (и финского) так называемого чардж-хрома (низкохромистого феррохрома) в производстве нержавеющей стали. Международная организация по стандартизации давно планирует понизить уровень минимальной концентрации хрома в высокоуглеродистом феррохроме до 45 55 %.
Казахстан располагает крупнейшими запасами хромитов (второе место в мире после ЮАР), среднее содержание Cr2O3 в которых (50,2 %) намного выше, чем в рудах практически всех других стран. Казахстанским рудам свойственно также низкое содержание железа и вредных примесей фосфора и серы, и они могут использоваться во всех сферах применения без каких-либо ограничений. Запасы хромовых руд Казахстана и вся их добыча сосредоточены на северо-западе страны, в Актюбинской области, в пределах Кемпирсайского ультрабазитового массива. Эти месторождения отрабатываются Донским ГОКом. Определенным недостатком является приуроченность большей части (более 90 %) оставшихся запасов хромитов к глубоким горизонтам массива и связанная с этим необходимость отработки их подземным способом. Резервом добычи хромитов на отдаленную перспективу может стать расположенный на юге Актюбинской области Даульско-Кокпектинский погребенный массив, являющийся непосредственным южным продолжением Кемпирсайского и сходный с ним по структурным и петрографическим характеристикам.
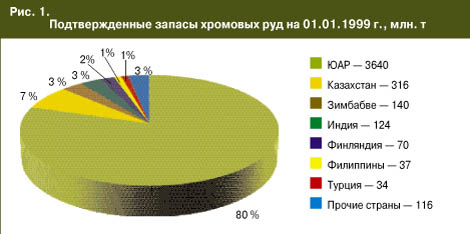
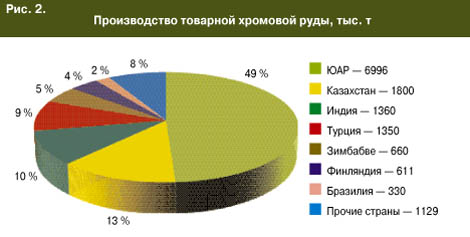
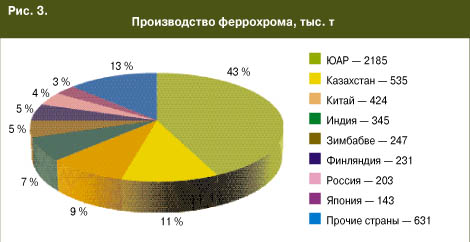
На другие страны приходится менее 12 13 % подтвержденных мировых запасов хромитов, и по значению в производстве хромсодержащей продукции они уступают месторождениям ЮАР и Казахстана.
Обеспеченность добычи хромовых руд их подтвержденными запасами, рассчитанная по уровню производства 1998 года с учетом потерь при обогащении и соотношения Cr2O3 в сырой и товарной руде, как во всем мире, так и в странах, располагающих крупнейшими месторождениями хромитов, в ЮАР, Казахстане, Зимбабве, а также на Филиппинах превышает 100 лет. Обеспеченность Финляндии составляет более 55 лет, Индии 53, Мадагаскара 42, Бразилии 34, Албании 30, Ирана 24, Турции 17 лет.
В мировом производстве товарной хромовой руды ведущую роль также играют ЮАР и Казахстан. Территориальная структура производства в целом аналогична структуре минерально-сырьевой базы, но степень его концентрации несколько ниже: на две ведущие страны приходится почти 2/3 производства (рис.2). Крупномасштабную добычу хромитов ведут также Индия, Турция, Зимбабве, Финляндия и Бразилия, суммарная доля которых в мировом производстве товарных хромитов в 1998 году составила 30 %, а доля остальных 17 стран 8 %, в том числе России 0,9 %.
За 1990 1998 годы мировое производство товарной хромовой руды увеличилось на 8 % (с 13,2 до 14,2 млн. т), в том числе примерно в полтора раза в ЮАР, Индии и Турции. В Казахстане, где запасы руды для открытой добычи практически отработаны и осуществляется переход на сложный и дорогостоящий шахтный способ, их производство в 90-е годы сократилось вдвое, а доля страны в мировом производстве упала с 28 % до 13 %. Сократилась также доля мелких стран продуцентов товарной хромовой руды с 14 % до 8 %.
Динамика производства феррохрома, на выпуск которого расходуется около 80 % товарной хромовой руды, практически повторяет динамику производства руды. Еще большее сходство отмечается между динамикой производства феррохрома и динамикой выпуска нержавеющей стали, где расходуется 3/4 всего феррохрома.
География производства феррохрома шире, чем его сырьевой базы, а степень концентрации ниже. В число крупных производителей феррохрома входят Китай, Россия, япония, Норвегия и Швеция, не имеющие сколько-нибудь значительных запасов хромитов, но располагающие мощностями и достаточными энергоресурсами для их переработки. Ведущие позиции здесь занимает ЮАР, которой значительно уступают Казахстан, Китай, Индия и другие страны (рис.3).
За 1990 1998 годы мировой выпуск феррохрома увеличился почти на треть (с 3,76 до 4,94 млн. т). Максимальные темпы роста (в среднем на 10 % в год) были достигнуты в ЮАР. Эта страна прочно занимает в отрасли ведущие позиции. Постоянное внедрение в производственную практику достижений научно-технического прогресса (главным образом, в сфере подготовки руд к плавке), а также дешевая электроэнергия, доля которой в себестоимости феррохрома составляет 22 25 %, что намного ниже, чем в других странах, частичное использование в качестве сырья практически по бросовым ценам отходов производства платины и платиноидов, дешевые восстановители и флюсы, низкие транспортные расходы обусловливают высокую конкурентоспособность южноафриканской хромсодержащей продукции на мировом рынке. Совместные предприятия с участием производителей нержавеющей стали в Китае, японии, других странах Юго-Восточной Азии обеспечивают южноафриканским компаниям дополнительное финансирование и устойчивый рынок продукции.
Казахстан также успешно развивал в 1990 1998 годах выпуск феррохрома и по темпам его роста уступал только ЮАР и Индии. Модернизировав два своих ферросплавных завода, Казахстан сумел за этот период увеличить выпуск феррохрома на 80 %.
Суммарное производство феррохрома в странах, располагающих мощной рудной базой, за 1990 1998 годы выросло на 78 % (с 2,12 до 3,78 млн. т). Здесь нашло отражение стремление компаний производителей товарной хромовой руды создавать собственные металлургические мощности, чтобы поставлять на рынок не рудное сырье, а феррохром полупродукт с большей добавленной стоимостью. В остальных странах, включая Китай, Россию, японию, Норвегию, Швецию, Германию, США, Италию и др., производство феррохрома сократилось на 31 % (с 1,63 до 1,12 млн т). Завод ферросплавов американской компании Macalloy Corp. в г.Чарльстон (шт. Южная Каролина) в 1998 году вообще был закрыт, в основном по природоохранным соображениям. Еще ранее, в 80-е годы, прекратился выпуск феррохрома в Великобритании и Франции.
Особенностью организации производства хромсодержащей продукции является тенденция к вертикальной интеграции в рамках одной компании мощностей по выпуску товарной руды, феррохрома, а также нержавеющей стали. Кроме возможности получать продукцию с большей добавленной стоимостью, подобная организация производства обеспечивает стабильное снабжение сырьем, позволяет сокращать управленческие, транспортные, а иногда и энергетические затраты. Например, в Финляндии на технологически объединенных предприятиях компании Outokumpu феррохром поступает на сталеплавильный завод в расплавленном состоянии; в непосредственной близости находятся и два карьера компании, отрабатывающие месторождение Кеми и снабжающие ферросплавный завод товарным хромовым сырьем.
Пока вертикальная интеграция затрагивает главным образом два начальных либо два конечных звена в цикле производства хромсодержащих продуктов, включающем получение сырья (товарной руды), полупродукта (феррохрома) и конечного продукта (нержавеющей стали). Масштабы производства всей триады хромсодержащих продуктов в пределах одной страны или в рамках одной компании еще незначительны. Так, на шесть стран ЮАР, Индию, Россию, Китай, Финляндию, Бразилию, выпускающих все виды хромсодержащей продукции, приходится 86 % мировых подтвержденных запасов хромитов, 67 % мирового производства товарной руды и 71 % феррохрома, но лишь 14 % нержавеющей стали (1998 г.). При этом только в Финляндии вертикальная интеграция существует в полном объеме и в наиболее прогрессивной форме в рамках одной компании Outokumpu и по существу одного горно-металлургического комбината.
Территориальная структура производства хромистой нержавеющей стали в минимальной степени зависит от минерально-сырьевой базы: 86 % производства в 1998 году было сосредоточено в странах, не имеющих запасов хромитов (или, как в США, не выпускающих товарную хромовую руду) и использующих только импортное сырье. В 1998 году мировой выпуск нержавеющей стали по сравнению с предыдущим годом сократился примерно на 1 2 % и составил около 16 млн. т (рис. 4), но уже в следующем году вырос до 16,7 млн. т.
Наращивание мощностей ферросплавных заводов при весьма низком уровне цен на их продукцию, особенно в 1998 и первой половине 1999 года, объясняется намерением наиболее мощных компаний, в основном действующих в ЮАР, захватить как можно большую часть мирового рынка, а также их уверенностью в хороших перспективах этого рынка.
На XIV международной конференции по ферросплавам в Монте-Карло в ноябре 1998 года прогнозировалось увеличение мирового производства нержавеющей стали к 2000 году до 17,5 млн. т, а к 2010 году до 28 млн. т, т. е. в среднем на 5,1 % в год за 1990 2000 годы и 4,8 % в год за 2000 2010 годы. В материалах XV конференции в Майами в ноябре 1999 года рост мирового производства нержавеющей стали в 2000 году прогнозировался на уровне 7,3 %. Предполагается, что в долгосрочной перспективе ее выпуск будет расти на 4 % в год. Только за три года с 1998 по 2001 год, судя по уже реализуемым проектам, намечается построить 19 предприятий с суммарной мощностью более 3 млн. т нержавеющей стали в год. Прогнозируется и соответствующий рост мирового выпуска феррохрома до 7 млн. т в 2010 году, 75 % которого составит доля ЮАР.
В долгосрочной перспективе высокие темпы роста потребления и производства нержавеющей стали особых сомнений не вызывают, учитывая непрерывно растущий спрос на нее в ключевых отраслях машиностроения, в автомобильной и электротехнической промышленности, в вагоностроении, строительстве, выпуске товаров народного потребления и т.п. Однако обусловленное этим благоприятным прогнозом расширение мощностей по производству и нержавеющей стали, и феррохрома осуществляется еще более высокими темпами, что неизбежно ведет к перепроизводству этих продуктов и снижению цен на них. Отсюда возникает известная цикличность: рост произодства перепроизводство снижение цен спад производства повышение цен и новое повторение цикла. Последний пик мирового производства практически всех видов хромсодержащих продуктов и цен на них отмечен в 1995 1996 годах. Есть все основания ожидать подобный пик производства и в 2000 году, причем на более высоком абсолютном уровне. Что же касается цен на товарную хромовую руду и феррохром, они наверняка будут ниже уровня пятилетней давности.
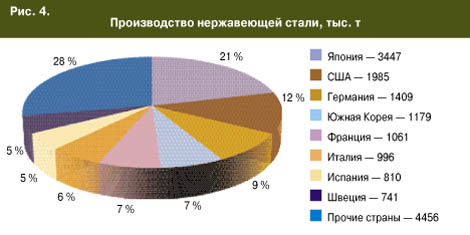 Потенциальные возможности для увеличения потребления нержавеющей стали в перспективе связываются и с общим усилением борьбы с коррозией. Благоприятными в этом плане представляются перспективы потребления металлического хрома (и его химических соединений) для получения коррозионностойких, а также декоративных покрытий.
В неметаллургическом секторе прогнозируется рост спроса на хромистые химикалии (1 2 % в год), в первую очередь в деревообрабатывающей промышленности. Наоборот, хромсодержащие краски по экологическим соображениям вытесняются органическими заменителями. Потребление диоксида хрома для выпуска магнитных лент аудио- и видеокасет может сократиться по мере расширения использования лазерных дисков. Доля огнеупорной промышленности в мировом потреблении товарной хромовой руды постепенно сокращается, в первую очередь в США и японии. В основном это связано с негативным влиянием на здоровье работников металлургических, а также цементных и стекольных производств. Кроме того, сталелитейная промышленность в последние годы предпочитает использовать более долговечные огнеупорные материалы. В японии, Южной Корее и других дальневосточных странах удельное потребление хромитовых огнеупоров сократилось с 15 20 кг на 1 т стали в 1970 1980 годы до 10 12 кг в 1998 году. В США выпуск хромомагнезитовых футеровочных кирпичей за 1988 1995 годы снизился со 104 до 36 тыс. т. Потребление хромитового литейного песка в перспективе останется стабильным.
Какое-либо значимое расширение использования заменителей хрома в перспективе не просматривается, их влияние на конъюнктуру рынка хромсодержащих продуктов весьма ограничено. Кроме хромитов не существует каких-либо других промышленных руд для производства всех видов хромсодержащей продукции. Для производства нержавеющей стали и спецсплавов нихромов, стеллитов, нимоник и т.п. какие-либо заменители хрома также полностью отсутствуют.
При выплавке нержавеющей стали единственным массовым заменителем феррохрома является ее лом. Разумеется, заменителем может служить и металлический хром, но из-за намного более высоких цен на него (по сравнению с ценами на феррохром) подобная замена происходит в крайне редких случаях. Доля лома в общем потреблении хромсодержащих материалов в черной металлургии США в 1998 1999 годах составляла 20 21 %, в том числе для производства нержавеющей стали около 30 %.
Заменители хрома как легирующего металла для рядовой стали, а также заменители его химических соединений и хромовых огнеупоров обычно имеют более высокую стоимость по сравнению с заменяемыми хромсодержащими продуктами и менее высокие эксплуатационные свойства. По данным Национальной академии наук США, замена хромсодержащих продуктов на аналогичные материалы без хрома позволяет сэкономить в огнеупорной промышленности до 90 % хромитов, в производстве низко- и высоколегированных сталей около 60 % хрома и при выпуске химических соединений 15 % хрома. При этом потребуется от 5 до 10 лет для разработки соответствующих технологий и адаптации экономики к более высокой стоимости заменителей. Повышенное внимание в США к проблеме заменителей связано, в частности, с жесткими природоохранными требованиями.
При благоприятном долгосрочном прогнозе развития мирового хромового комплекса отдельные его предприятия в ближайшем будущем могут столкнуться с рядом проблем. Неизбежным представляется резкое обострение конкуренции между продуцентами на рынках сбыта хромовой продукции. Скорее всего, развитие производства феррохрома на предприятиях ЮАР и Казахстана, обеспечивающих минимальные производственные издержки, компенсирует выбытие неэффективных мощностей в других странах. Другими словами, произойдет санация в масштабах всей отрасли, что в целом будет иметь положительный эффект для потребителей подешевевшей конечной продукции.
|