Геннадий Прохоренко Директор Центрального рудоуправления НГМК Петр Шеметов Главный инженер карьера Мурунтау
Первоначальными проектами разработку месторождения Мурунтау предусматривалось вести двумя способами: открытым (до отметки -15 м при глубине карьера 575 м) и подземным (до отметки -395 м). Однако развитие погрузочно-транспортного комплекса показало возможность увеличить глубину открытой разработки до 700 800 м и более.
Проектирование и строительство карьера ведутся очередями (табл.1). В настоящее время месторождение вскрыто четырьмя траншеями внутреннего заложения, три из которых используются для движения технологического автотранспорта, а одна - для размещения конвейеров комплекса циклично-поточной технологии (ЦПТ). Высота уступов колеблется от 10 до 15 м. Среднее расстояние перевозки автосамосвалами составляет 3,5 км при высоте подъема 140 150 м. Фактическая глубина карьера превысила 400 м.
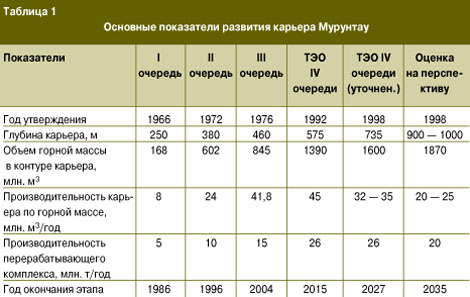 Производительность карьера по горной массе в 1990 1995 годах составляла 28 30 млн. м3/год, затем увеличилась и в 1997 2000 годах поддерживалась на уровне 36 38 млн. м3/год. Темпы понижения горных работ за последние 10 лет увеличились с 10,5 м/год до 20 м/год и в дальнейшем будут возрастать. При этом 70 % объемов горной массы извлекается с глубины более 200 м. На этой отметке ширина рабочих площадок и объем взрываемых блоков по сравнению с верхними горизонтами карьера уменьшились в 1,7 2,1 раза, что свидетельствует о существенном сокращении площади рабочей зоны в нижней части карьера.
Сложное строение месторождения обусловило разделение карьерного поля на природно-технологические зоны (рудную, рудно-породную и породную), где горно-геологические условия требуют различной организации буровзрывных, выемочно-погрузочных и транспортных работ с формированием комбинированных и разнородных грузопотоков, параметры которых носят случайный характер.
Таким образом, развитие экскаваторно-автомобильного комплекса карьера Мурунтау стимулируется постоянным ростом его глубины и происходит в условиях дефицита ресурса выработанного пространства на фоне увеличивающихся темпов понижения горных работ.
Первым выемочно-погрузочным оборудованием карьера Мурунтау были экскаваторы ЭКГ-4,6 (1967 1982 гг.), на смену которым пришли сначала экскаваторы ЭКГ-8И (с 1975 г.), а затем ЭКГ-12,5 (с 1986 г.), ЭКГ-10 (с 1992 г.), ЭКГ-15 (с 1993 г.), гидравлические экскаваторы с вместимостью ковша 17 18 м3 (с 1995 г.). Параллельно происходила замена автосамосвалов на более грузоподъемные модели, что в целом позволило обеспечить рост производительности труда на горных работах (табл.2).
В настоящее время выемочно-погрузочное оборудование представлено различными экскаваторами: тросовыми (ЭКГ-8И 8 шт., ЭКГ-12,5 5 шт., ЭКГ-15 2 шт.) и гидравлическими (САТ-5230 фирмы Саterpillar 2 шт., RН-170 фирмы О&К 2 шт. и ЕХ-3500 фирмы Нitachi 1 шт.). В процессе работы ими была достигнута производительность, приведенная в табл. 3.
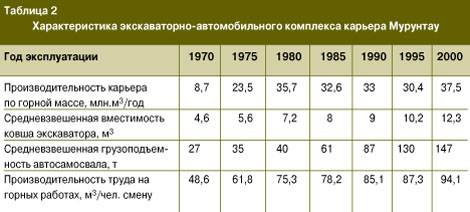
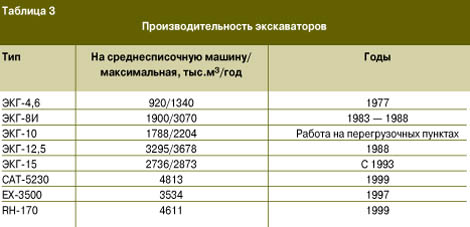
Технические характеристики и показатели работы экскаваторов в карьере Мурунтау показаны в табл. 4. Сравниваемые машины сопоставимы по своим геометрическим и энергосиловым параметрам. Главными же техническими особенностями гидравлических мехлопат по сравнению с электрическими следует считать автономность в работе и шарнирное сочленение рукояти ковша со стрелой. Первая особенность позволяет эффективно решать производственные задачи на карьерах с высокой изменчивостью потребительских свойств полезного ископаемого, вторая ограничивает высоту забоя высотой черпания экскаватора. Анализ показателей работы экскаваторов свидетельствует о том, что как плановый, так и фактический коэффициенты использования оборудованием календарного времени (КИО) относительно невысоки, в связи с чем их производительность ниже возможной. Такая ситуация объясняется тем, что комплектация экскаваторов автосамосвалами осуществляется с учетом текущих потребностей в руде заданного качества, поскольку управление ее содержанием начинается с экскаваторных забоев. Поэтому в зависимости от конкретной ситуации экскаваторы обеспечиваются автосамосвалами на 30 100 %.
Шарнирное сочленение рукояти ковша со стрелой уменьшает радиус черпания, поэтому гидравлические экскаваторы вынуждены ближе электрических подходить к откосу уступа, высота которого по условиям безопасности не должна превышать 10 12 м. В то же время безопасность работы таких экскаваторов на уступах высотой 15 м обеспечивается дроблением массива до размера среднего куска 0,1 0,15 м с управляемым обрушением верхней части забоя.
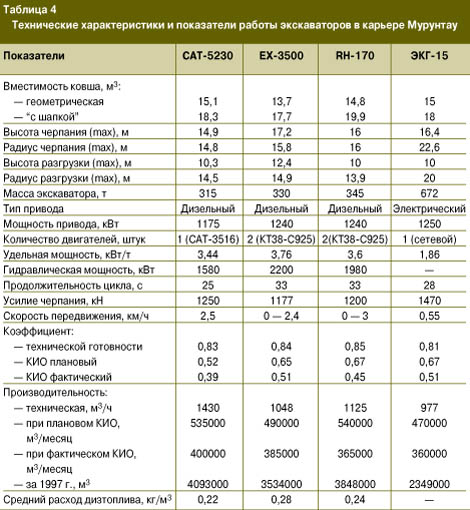 Значительные различия в расходе дизельного топлива обусловлены наличием у экскаватора СAT-5230 одного двигателя по сравнению с двумя у экскаваторов ЕХ-3500 и RH-170, а также наличием у последнего электронного впрыска топлива "CENTRY" и cистемы "TRI POWER", которая обеспечивает щадящий режим работы двигателей при наполнении ковша. Только по этой причине у экскаватора ЕХ-3500 годовой расход топлива на 150 т больше, чем у RH-170.
Анализ материальных и трудовых затрат показывает, что экскаватор ЕХ-3500 является наиболее, а САТ-5230 наименее дорогим и трудоемким в эксплуатации. Экскаватор RH-170 занимает по таким показателям промежуточное положение. Все это объясняется не только различием в стоимости запасных частей и количестве дизельных двигателей, но и взаимозаменяемостью (до 50 % по отдельным позициям) запасных частей у экскаватора САТ-5230 c другой горной и дорожно-строительной техникой фирмы Caterpillar.
Однако даже наименее дорогой и трудоемкий в эксплуатации гидравлический экскаватор с дизельным приводом имеет эксплуатационные затраты как минимум на 30 40 % выше, чем у тросовых экскаваторов с электрическим приводом. Тем не менее для гидравлических экскаваторов есть вполне определенная область применения, обусловленная их автономностью и более высокой маневренностью. Эти преимущества проявляются в наибольшей степени в глубоких карьерах при сокращении размеров рабочей зоны и концентрации горных пород на ограниченной площади.
Для уменьшения материальных затрат на эксплуатацию экскаваторов в карьере Мурунтау проведены следующие мероприятия: снижен ассортимент применяемых смазочных материалов; Навоийским машиностроительным заводом освоен выпуск быстроизнашивающихся сменных элементов ковшей (зубьев, режущих кромок, протекторов); увеличены срок службы и ремонтопригодность ковшей. Ходимость, например, зубьев всех фирм не превышает 150 часов работы в забое, а их потребность составляет более 300 штук в год на каждую машину. Поэтому освоение их производства собственными силами принесло значительный экономический эффект. За счет применения метода самофутеровки изнашиваемых поверхностей ходимость ковшей увеличена с 250 тыс. м3 до 1000 тыс. м3 , т. е. в 4 раза.
Характерными неисправностями для всех экскаваторов, правда, проявляющимися в разной степени, являются порыв шлангов высокого давления, трещины в гидробаках, выход из строя насосов, обрыв шпилек головок цилиндров двигателя. Причем порыв шлангов значительно увеличивается после наработки более 8000 моточасов. В частности, аварийная потеря масла у экскаваторов САТ-5230 в 2 3 раза выше, чем у экскаваторов других фирм.
Непременным условием безопасной работы гидравлических экскаваторов является их комплектация системой автоматического пожаротушения, поскольку своевременно заметить возгорание в моторном отсеке экипажу трудно, а потушить традиционными для горных машин первичными средствами вообще невозможно.
История развития карьера Мурунтау неразрывно связана с автосамосвалами Белорусского автомобильного завода, которые лишь с 1993 года начали заменяться машинами других фирм. Первыми были автосамосвалы КрАЗ-256 (1967 г.), на смену которым почти сразу же пришли БелАЗ-540 (с 1967 г.), а затем БелАЗ-548 (с 1972 г.), которых в 1978 году работало уже 410 штук. В 1979 1981 годах в карьере проходили испытания 4 автосамосвала БелАЗ-549 (грузоподъемность 75 т), по результатам которых было решено использовать их на горных работах. Уже в 1982 году количество таких машин достигло 35, а в 1985 году 161. Успешное освоение самосвалов указанной модели показало преимущества транспортных средств большой единичной мощности. Это послужило основой для принятия решения о замене автосамосвалов БелАЗ-549 на БелАЗ-7519 грузоподъемностью 110 т. Поступление этих машин продолжалось до 1991 года включительно (по 20 25 в год). Однако из-за их низкой надежности перевооружение транспортного технологического парка ожидаемого эффекта не принесло, поскольку БелАЗ-7519 эффективно трудился только первый год эксплуатации, а в последующее время требовал значительных материальных, трудовых и финансовых затрат на поддержание работоспособности.
Совещание, проведенное в 1991 году с представителями Белорусского автомобильного, Балаковского и Свердловского моторных заводов, Московского автомоторного института, пришло к выводу, что автосамосвал БелАЗ-7519 не пригоден для эксплуатации в условиях Мурунтау и требуется разработка новой модели для глубоких карьеров. Однако последующие события не позволили осуществить намеченное.
Единственным выходом из создавшегося положения явился переход на импортные машины. Первым шагом стало приобретение в 1992 году 15 автосамосвалов БелАЗ-75124 с двигателями КТА-50С фирмы Каmmins и начало испытаний в карьере автосамосвала CAT-785B (грузоподъемность 136 т) фирмы Caterpillar. Анализ двухлетней эксплуатации показал, что у самосвала БелАЗ-75124 только 3% отказов приходится на двигатель, а остальные на шасси и его системы. Поэтому было принято решение о полном переводе карьерного технологического транспорта на импортные автосамосвалы. В 1993 году запущены в работу первые 10 машин R-170 фирмы Yuklid (грузоподъемность 170 т) и начались испытания самосвала HD-1200 фирмы Komatsu (грузоподъемность 136 т). В 1994 году приобретены еще 10 машин R-170. Автосамосвалы CAT-785B приобретались в 1994 году (22 шт.), в 1995 году (21 шт.), 1996 году (6 шт.) и 1997 году (14 шт.). Показатели работы автосамосвалов БелАЗ-7519, CAT-785B и R-170 в сопоставимых условиях представлены в табл. 5.
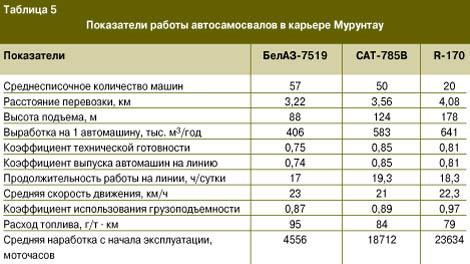 Первые месяцы эксплуатации импортных автосамосвалов показали, что их параметры не в полной мере соответствуют условиям карьера Мурунтау. В частности, фактическая вместимость кузова самосвала CAT-785B (78 м3) не обеспечивала использования его грузоподъемности в полной мере, поэтому в конце 1996 года началось наращивание бортов у кузовов этих машин. В настоящее время вместимость кузовов доведена до 88 91 м3, что позволило приблизить коэффициент использования грузоподъемности к единице.
Работа автосамосвалов в карьере Мурунтау характеризуется высокой температурой и запыленностью окружающего воздуха, что предъявляет повышенные требования к температурному режиму двигателя и очистке от пыли воздуха, поступающего в цилиндры.
Одной из первых проблем, с которой столкнулись специалисты, было кавитационное разрушение гильз цилиндров двигателей КТА-50 фирмы Кammins, установленных на автосамосвалах Yuklid, которое происходило при наработке 6000 8000 часов. Исследованиями установлено, что в этом случае причинами кавитации являются недостаточная концентрация антифриза в охлаждающей жидкости при относительно невысокой температуре его кипения и неравномерность работы цилиндров.
Влияние первой причины было устранено увеличением концентрации антифриза с 50 %, рекомендованных изготовителями, до 58 60 % с одновременным переходом на применение его разновидности с более высокой температурой кипения. От последствий избавились за счет внедрения плановых (через 1000 часов) углубленных испытаний двигателя и электропривода, направленных на своевременное устранение отклонений в работе отдельных цилиндров. Такое решение обусловлено тем, что углубленные испытания двигателя заводом-изготовителем рекомендуются только в случае заметного снижения более 10 20 % его мощности. Однако известно, что снижение мощности неисправных цилиндров компенсируется увеличенным расходом топлива и соответствующей перегрузкой исправных цилиндров, поэтому работа двигателя в таком режиме может продолжаться длительное время. Внедрение указанных мероприятий позволило исключить кавитационные разрушения цилиндров в течение всего конструктивно заложенного (18000 20000 часов) ресурса двигателя.
Предельный износ гильз и поломка поршневых колец автосамосвалов САТ-785В при наработке двигателя 5600 8000 часов в 5, 7 и 11 цилиндрах происходили значительно чаще, чем в других, что является признаком влияния системных факторов, к которым относятся пыль и сернистое топливо. При этом было установлено, что причинами попадания пыли оказались необоснованно частое обслуживание фильтров и разгерметизация соединений воздушного тракта. Изменение периодичности обслуживания фильтров и внедрение оригинальной методики испытания воздушного тракта на герметичность значительно уменьшили влияние пыли на срок работы двигателя. Снижение действия сернистого топлива достигнуто уменьшением допустимой разницы температуры цилиндров по отношению к техническим условиям.
В целом накопленный фактический материал позволяет сделать достаточно обоснованные выводы о достоинствах и недостатках автосамосвалов CAT-785B и R-170.
Поступление импортной техники потребовало адаптации существовавшей базы технического обслуживания и ремонта к новому оборудованию и специфичным требованиям фирм-поставщиков. Причем понадобилось освоить не только замену узлов и агрегатов, но и их ремонт в соответствующем подразделении карьера. Задача в основном была решена. Уже в 1996 году на автосамосвалах и другой импортной технике было заменено 24 и отремонтировано 16 двигателей, а также более 150 таких агрегатов, как бортовые редукторы, коробки передач, гидротрансформаторы, подвески и т.п., восстановлено 55 рам, 25 кузовов, 115 крупногабаритных шин.
Важный фактор повышения эффективности работы импортного оборудования взаимоотношение между фирмой-поставщиком и покупателем. Фирмы Caterpillar, Hitachi и О&К открыли в Зарафшане свои представительства, однако принцип их работы значительно отличается. Так, фирма Caterpillar в основу своей деятельности положила оперативное реагирование на все проблемы, связанные с эксплуатацией экскаваторов. Для этого в ее офисе есть два секретаря-переводчика и несколько консультантов, что значительно облегчает работу. Помимо этого раз в квартал приезжают высококвалифицированный инженер и менеджер фирмы по Центральноазиатскому региону для изучения ситуации на месте и оказания практической помощи. Представительства же Hitachi и О&К являются временными и достаточно качественно могут решать только технические вопросы.
Следует также отметить планомерную работу фирмы Caterpillar по улучшению конструкции оборудования (программа PIP), которая проводится на всех без исключения машинах. Наряду с этим Caterpillar выпускает журнал "Технические новости", позволяющий заказчикам самостоятельно совершенствовать машины.
Таким образом, при разработке месторождения Мурунтау открытым способом накоплен значительный опыт применения разнообразного погрузочно-транспортного оборудования, который может быть использован на других карьерах со сложными горно-геологическими и горнотехническими условиями ведения работ.
|