Олег Стеклов Профессор Университета нефти и газа им. Губкина, президент Российского научно-технического сварочного общества
Медленное развитие внутреннего рынка металлопродукции, как правило, имеет одно объяснение кризисное состояние основных металлопотребляющих отраслей. Но ситуация в отдельных секторах этого рынка выглядит не столь однозначной. Наиболее сложные проблемы возникают в связи с производством труб для нефтегазового комплекса. Казалось бы, есть все необходимые предпосылки для динамичного наращивания оборота между двумя отраслями. С одной стороны крупные платежеспособные заказчики в лице Газпрома и ведущих нефтяных компаний, громадная потребность в трубной продукции в связи с реализацией масштабных проектов и назревшей реконструкцией действующих транспортных систем. С другой стороны наличие свободных мощностей на предприятиях трубной промышленности, которые загружены едва на треть. Между тем интересы поставщиков и потребителей остаются несбалансированными.
Учитывая важность данной проблемы для металлургического комплекса и для экономики страны в целом, редакция журнала "Металлы Евразии" ввела новую постоянную рубрику "Нефть газ трубы". Сегодня публикуется очередной блок материалов.
Только на промысловых нефтепроводах России каждый год официально регистрируется около 30 тыс. протечек, т. е. по 50 70 ежедневно. Уйти от таких предкатастрофных явлений практически невозможно. Дело в том, что вопросу безопасной эксплуатации этого, самого быстрого, удобного и в то же время проблемного во многих отношениях, вида транспорта нефти и газа долгое время не придавалось должного значения. И сегодня специалисты далеко не всегда могут дать четкие рекомендации, что и как нужно делать для безаварийной работы систем.
Анализ статистики отказов выявил, что в нефтяной промышленности в первые несколько лет эксплуатации трубопроводов проявляются большей частью дефекты строительства, затем определенный период труба работает нормально, а через 14-16 лет начинаются отказы из-за старения конструкции. Статистика аварий на газопроводах, широкое строительство которых началось позднее, разумеется, имеет отличия, но закономерность, в принципе, такая же. Опираясь на эти данные, можно определенным образом сгруппировать факторы, влияющие на надежность трубопроводного транспорта углеводородов.
Первый фактор металлургический: качество выпускаемых труб.
Второй строительный: технология монтажа трубопровода, особенно все, что связано со сварочными работами в полевых условиях.
Третий, чрезвычайно важный, обеспечение надежной защиты трубы от влияния коррозионных процессов на стадии изготовления или в ходе эксплуатации.
Четвертый мониторинг, т. е. постоянный контроль за состоянием трубы на протяжении всего жизненного цикла, начиная с прокатного стана и до окончания срока эксплуатации.
Пятый сертификация системы качества в трубопроводном строительстве, которая должна предусматривать сертификацию конструкций, материалов, технологии изготовления и строительства, оборудования, защиты, контроля, аттестации персонала.
Более чем за семьдесят лет строительства отечественных магистральных трубопроводов материалы, которые здесь использовались, прошли определенную трансформацию (см. таблицу).
В 30 40-е годы, когда нефтепродукты еще не являлись основным бюджетообразующим фактором, объемы поставок измерялись в цистернах, а сам транспорт был в основном местным к терминалам и нефтеналивным узлам, технология не требовала высокого прочностного показателя металлов труб. Поэтому в первом поколении труб (довоенном, военном) использовались стали типа 20, пластичные, с малой прочностью.
По мере перехода на транспортировку углеводородов напрямую, исключающую дополнительную дорогостоящую перевалку, по мере того, как осваивались новые, отдаленные районы добычи, понадобилось увеличить диаметры трубопроводов, давление и, соответственно, повысить надежность материала для изготовления труб. Сталь начали упрочнять, и, казалось, оптимальное решение проблемы было найдено. Но вскоре специалисты столкнулись с тем, что с повышением прочностных характеристик металла сама конструкция становится более чувствительной к различного рода поверхностным воздействиям.
Была проанализирована склонность нефтегазопроводов к разрушению в зависимости от срока их эксплуатации и материалов, из которых их строили. Выяснилось, что на трубопроводах из более пластичных материалов трещины появляются через 25 и более лет, а на новых, высокопрочных, порой, уже через 4 года. Дело в том, что первоначально повышение прочности ведет к росту стойкости всей конструкции, однако на определенном этапе начинается резкий спад надежности системы. Причем это касается не только трубопроводов. По существу в каждой отрасли, где существуют оценочные показатели надежности систем и конструкций, есть свой прочностной предел, зависящий от того, как работает данная конструкция.
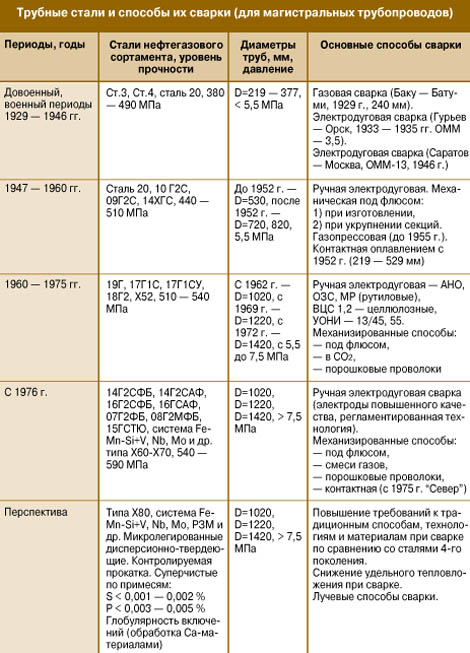 В свое время на судостроительных предприятиях для подводного флота был обозначен предел примерно в 800 мегапаскалей. Для трубопроводного транспорта этот предел не должен превышать 600 700 мегапаскалей. В ином случае выигрыш может оказаться мнимым. Этому есть три причины. Первая чем прочнее материал, тем выше его чувствительность к концетраторам напряжений. Вторая чем прочнее материал, тем сильнее он реагирует на технологические воздействия: удары, формоизменения и особенно сварку, поскольку этот процесс резко изменяет свойства материала в обрабатываемой зоне. А третья причина высокопрочный материал резче реагирует на воздействие разрушающих факторов природной среды: коррозионных, температурных и т.д.
Какие могут быть принципиальные решения? Можно вернуться к более пластичным материалам, но, учитывая современные диаметры трубопроводов и уровень давления, готовые конструкции окажутся столь металлоемкими, что стоимость их, сложность монтажа становятся совершенно неподъемными.
Есть другой путь внедрение технологий, которые позволяют создавать качественно новые материалы.
Процессы контролируемой прокатки, микролегирования, позволяюцие включать в стали карбонитридное упрочнение и измельченные структуры, широко применяются в современном трубном производстве. Материалы в результате такой обработки приобретают улучшенное качество по двум показателям прочности и пластичности. К тому же они и свариваются качественно, поскольку содержат очень мало углерода. Применение подобных технологий позволяет использовать не только фактор прочности, но и способность трубы с такой структурой успешно сопротивляться отказам. Вместе с тем существующие методы контролируемой прокатки требуют корректировки с целью получения структуры металла, способной противостоять коррозионному растрескиванию.
Магистральные трубы цельносварные, и от того, насколько качественно проведена эта операция на заводе, зависит будущее самого трубопровода. Нельзя сказать, что отечественные технологии серьезно отстают от зарубежных. И Челябинский трубопрокатный, и Волжский трубный заводы сегодня используют вполне современные методы. Но на этапе перехода к новым высокопрочным материалам нужно думать о способах сварки, основанных на иных физических решениях, с учетом требований самого изделия. Например, когда в авиации появилась необходимость сварки высокопрочного алюминиевого листа, был разработан и способ плазменной импульсной сварки, которая позволяла не допускать коробления конструкции. Сама конструкция диктовала выбор способа. В нашем случае это тоже справедливо. Исследования показали, что для трубного производства наиболее актуальными являются плазменная и лазерная сварка. Такие разработки нами ведутся. Подготовлен и передан в Газпром бизнес-план, который, в принципе, одобрен.
На строительстве трубопроводов основным остается ручной способ сварки. И как всегда при использовании ручного труда, реальное качество здесь зависит от множества трудноучитываемых факторов: от влажности воздуха до психологического состояния самого работника. Поэтому и на монтажных работах нужно кардинально менять технологии.
В мире на долю ручной сварки приходится около 30 % сварочных работ, в России значительно больше. Так, в строительстве (а монтаж трубопроводов по классификации относится именно к этой отрасли) объем ручных сварочных работ превышает две трети. Передовые страны активно переходят на полуавтоматическую, механизированную сварку, в смесях газов (углекислый газ с аргоном, углекислый газ с азотом и аргоном), сварку с подачей порошковой проволоки, плавящейся проволокой со смесью газов. Такие сочетания позволяют гибко комбинировать формирование корня шва, заполнение при разном пространственном положении.
Есть, конечно, причины, вынуждающие российских монтажников и сварщиков отдавать предпочтение ручному труду. Например, природные. В ходе полевых работ возникает масса задач, которые приходится решать с ходу, и автоматика здесь не всегда бывает безупречной.
Итак, сделали качественную трубу, доставили ее на место, уложили... Начинается эксплуатация.
Если говорить о промысловом транспорте нефти, там проблем особенно много. Сегодня на тонну топлива добывается 9 т воды. Причем воды, насыщенной солями, превращающими ее в крайне агрессивный агент. Необходимо заботиться о внутренней защите трубы. Сегодня предлагается целый ряд решений, но наиболее приемлемое, на наш взгляд, использование неорганических, эмалевых покрытий, стеклование. Особые свойства эмалей сводят к минимуму трение при перекачке углеводородов, позволяя в полтора раза уменьшить давление для того, чтобы перекачать те же объемы продукта. Понижается и оседание вредных веществ на стенках. Оставалась проблема соединений, т. е. защиты швов, но и она решена технологию уже разработали.
Для магистральных трубопроводов, где углеводороды чище, важнее защита от внешних повреждений. Качество защитных покрытий зависит в первую очередь от условий, в которых ведут обработку изделий. У нас в стране традиционно эту операцию делали на трассе, используя наиболее простые и дешевые технологии. Сначала применяли жидкие битумные покрытия, позже пленочные, которые рассчитаны всего на 10 15 лет. Теперь они в массовом порядке начали выходить из строя.
В промышленно развитых странах иная практика. Магистральные трубопроводы на трассах не изолируют, трубы обрабатывают заранее на заводе-изготовителе. В России пока только Волжский завод начал выпускать трубы с двух- и трехслойным покрытием.
Самый назревший вопрос эксплуатации трубопроводного транспорта проведение планово-предупредительного ремонта. Отставание в выполнении необходимых работ накапливалось многие годы, и сегодня мы не в состоянии произвести ремонт в полном объеме. Стоимость ремонта 1 км трубопровода составляет сотни тысяч долларов.
Сейчас важно вести диагностику состояния трубопроводов всех видов и назначений. Выявлять потенциально опасные участки трассы можно геофизическими способами. Есть возможность внутритрубной диагностики. Для этого созданы специальные снаряды. Нефтяники свои трубопроводы практически проверили. В газовой отрасли проверке подверглась всего треть трубопроводов. Этому препятствуют, во-первых, просчеты, допущенные на стадии проектирования строительства тогда мало задумывались о контролепригодности магистралей, поэтому из-за барьеров (станции перекачки и другие объекты) большая часть газопроводов в стране не подлежит внутренней проверке и диагностике. Вторая причина отсутствие необходимого оборудования и технологическая неразработанность программ контроля.
В этих условиях эксплуатационный мониторинг можно вести поступенчато. Сначала с использованием аэрокосмических систем, которые что уже доказано экспериментально в состоянии отслеживать малейшие изменения на трассах нефтегазопроводов. Затем проводить выборочный местный анализ металла, его состояния и на основе обобщенных результатов принимать необходимые решения.
Несколько лет назад мы выступали с инициативой создания единой комплексной программы осуществления контроля за объектами повышенной опасности. В частности, касалась она и трубопроводного транспорта углеводородов. На наш взгляд, эта программа должна объединить разработчиков и металлургов, трубопрокатчиков и строителей и курироваться государственными органами например, Министерством по чрезвычайным ситуациям (МЧС). Работать в рамках этой программы должны все крупнейшие фирмы по добыче и транспортировке нефти и газа, поскольку ситуация на трубопроводах, в прямом смысле, взрывоопасная.
|