Валерий Паршин, Алексей Ларин ГНЦ РФ "ЦНИИчермет им. И.П. Бардина"
Процесс непрерывного литья заготовок, бесспорно, является одним из крупнейших технологических достижений, позволивших вплотную подойти к практической реализации важнейшей задачи получению металлопродукции за один рабочий цикл. Технология непрерывного литья, несмотря на ее сравнительную молодость (массовое промышленное освоение началось в 70-е годы), относится к разряду классических и в настоящее время составляет основу производства на переделе "сталь прокат". При этом непрерывное литье является универсальной технологией, которая стала необходимой для комбинатов полного цикла и прекрасно вписалась в технологические цепочки передельных мини-заводов.
Главные усовершенствования непрерывной разливки в последнее десятилетие были связаны с развитием производства заготовок, близких по размерам к готовой продукции, в том числе тонких слябов. В стремлении сократить производственный цикл логичной целью этих разработок явилось совмещение литья и прокатки. Так появились промышленные технологии CSP и ISP, способы прямого литья полосы CPR и DR.
Кроме принципиально новых разработок, в промышленной эксплуатации находится большое количество МНЛЗ первых поколений, многие из которых морально и физически устарели и нуждаются в серьезной модернизации с целью повышения производительности и улучшения качества продукта. Как показывает мировая практика, основные направления модернизации связаны в первую очередь с усовершенствованием конструкции главных блоков МНЛЗ: кристаллизатора (регулирование по ширине, система качания, оптимизированная геометрия полости для сляба и для сорта, подвижной стол и т.д.); системы охлаждения с широким интервалом регулирования расхода и давления воды и воздуха; промежуточных ковшей и погружных стаканов.
Исключительно важную роль играет комплексная автоматизация управления процессом разливки и качеством заготовки, в том числе система поддержания уровня металла в кристаллизаторе в сочетании с автоматическим пуском разливки и система прогнозирования прорыва, а также автоматическая подстройка ширины отливаемого слитка. Например, современный механизм качания Динафлекс имеет надежную компенсацию качающихся масс, автоматическое регулирование частоты и схемы качания. Функционирование динамической модели вторичного охлаждения Динакс основано на непрерывном слежении за тепловым состоянием непрерывного слитка с учетом свойств жидкой стали, температуры перегрева в ковше, фактической теплопередачи в кристаллизаторе, скорости разливки, температурного профиля поверхности сляба, толщины оболочки слитка. Промежуточный ковш современного типа обеспечивает снижение расхода огнеупоров, повышение стойкости, равномерность распределения температур и минимизацию турбулентности потоков металла.
Комплексное решение автоматизации процесса разливки предполагает, как правило, несколько уровней управления. Первый включает настройку и автоматическое регулирование последовательности операций, аварийную сигнализацию и слежение за потоком металла как в целом по МНЛЗ, так и по отдельным ручьям. Второй уровень хранит в памяти все технологические параметры настройки для всех марок стали и сечений, собирает всю технологическую информацию в реальном масштабе времени, хранит информацию по качеству литых заготовок, способен выдать при необходимости любую документацию по производству, качеству и т.д.
Названные технические новинки весьма существенно изменяют не только конструкцию, но и, что особенно важно, качественные показатели процесса, его экономичности. Это позволяет, по-видимому, говорить о создании нового поколения машин непрерывного литья заготовок. Такие принципы технической модернизации уже широко используются ведущими компаниями в странах с развитой черной металлургией.
В основном в аналогичных направлениях модернизация производства идет и на российских предприятиях. Так, Новолипецкий металлургический комбинат (100 % непрерывной разливки) направил крупные финансовые средства в модернизацию отделения непрерывной разливки стали в ККЦ-1 с заменой двух вертикальных МНЛЗ на одну современную вертикальную с изгибом. В новой машине реализованы опробованные ранее достижения фирмы "Фест Альпине", а именно:
вертикальный кристаллизатор с медными плитами высотой 900 мм и тремя роликами подвески, обеспечивающими минимальный износ рабочих поверхностей и уменьшение удельного расхода меди, чему также способствуют применение тонких стенок с фрезерованными каналами охлаждения и специальные износостойкие покрытия рабочих поверхностей. Вмонтированные в корпус кристаллизатора приводы обеспечивают изменение ширины отливаемой заготовки в процессе непрерывной разливки по заданной программе. Кроме того, вертикальный кристаллизатор наиболее прост в изготовлении и установке в МНЛЗ и обеспечивает наилучшие условия для удаления неметаллических включений и газовых "пузырей" в шлаковое покрытие;
многоопорные ролики поддерживающей системы диаметром 150 300 мм обеспечивают минимальные межроликовые расстояния, что исключает выпучивание оболочки слитка, а это одно из существенных условий получения бездефектной поверхности и макроструктуры слитка;
водовоздушная система вторичного охлаждения заготовки, способная работать в диапазоне от "мягкого" до очень "жесткого" режимов. Конструкция и контрольно-регулирующие устройства системы обеспечивают оптимальное вторичное охлаждение слябов всех типоразмеров из стали всех марок. Применение форсунок специальной конструкции позволяет получить монотонное снижение температуры поверхности слитка по заданной кривой с минимальным "термоциклированием". Благодаря этому исключается образование "сетчатых трещин";
многоуровневая автоматизация технологического процесса включает системы взвешивания металла в сталеразливочном и промежуточном ковшах, поддержания уровня в кристаллизаторе, изменения ширины отливаемого сляба, оптимизации параметров качания кристаллизатора и охлаждения заготовки, замены погружных стаканов и промежуточного ковша, раскроя на мерные длины и маркировки слябов. При анализе поступающей информации в масштабе реального времени на верхнем уровне создается динамическая модель разливки плавки с последующим прогнозом качества слябов и выдачей рекомендаций о необходимости дополнительного визуального или металлографического контроля;
эффективные системы смазки и охлаждения, диагностики и быстрой замены отдельных узлов и блоков обеспечивают высокую (около 1 млн. т) межремонтную стойкость оборудования.
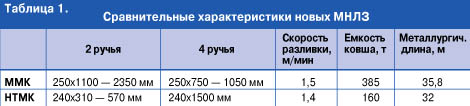

Одним из направлений расширения возможностей МНЛЗ могут быть комбинированные машины непрерывного литья, на которых отливают заготовки профилей в выгодных для производителей сочетаниях. К таковым относятся построенные в последнее время МНЛЗ в кислородно-конвертерных цехах Магнитогорского и Нижнетагильского металлургических комбинатов. Характеристика сечений отливаемых слитков, скорость разливки и другие параметры новых машин приведены в табл. 1. Каждый ручей имеет свой привод, что обеспечивает высокую работоспособность МНЛЗ.
Однако динамика развития непрерывного литья в России существенно отстает от мирового уровня. Это является одной из главных причин низких темпов структурной перестройки черной металлургии, в частности, реализации идеи широкого развития гибких модульных технологий (подробнее см. "Металлы Евразии", 1999, № 1) и создания на этой основе современной мини-металлургии.
Как свидетельствует мировая практика непрерывного литья, доля сортовых МНЛЗ обычно составляет 43 47 %, слябовых 23 30 %, блюмовых 26 30 %. Такая структура сложилась, главным образом, за счет опережающего развития мини-заводов, ориентированных на производство сортового проката, что отражает потребности современного рынка металлопродукции (табл. 2).
Низкая доля МНЛЗ в России подчеркивает серьезное отставание в развитии мини-заводов, которые являются наиболее динамично растущим сектором черной металлургии. В то же время в нашей стране сегодня действуют 15 металлургических предприятий с годовой производительностью от 80 до 200 тыс. т, имеющих устаревшую технологию во всех переделах. По нашему мнению, при определенных, не слишком высоких, затратах можно было бы эффективно развить мини-модульные сталеплавильные производства, используя существующие инженерные сооружения, коммуникации, квалифицированные кадры.
Стоит, наверное, напомнить, что наша страна в этом деле была пионером с середины 80-х годов на заводе "Электросталь" успешно эксплуатируется литейно-прокатный агрегат, совмещающий электропечь, непрерывную разливку, индуктор для выравнивания температуры заготовки и планетарный стан.
В настоящее время имеются разработки различных вариантов мини-заводов как для производства арматуры, мелкого сорта, проволоки, так и для тонкого листа. Иными словами, можно удовлетворить различные потребности рынка.
Учитывая огромную важность этого направления, в ходе реструктуризации российской металлургии, по-видимому, следует выделить несколько приоритетных инвестиционных проектов, готовых для практической реализации. Из многочисленных предложений можно, на наш взгляд, использовать разработки для ОЭМК, ОАО "Мечел", Верх-Исетского и Ашинского металлургических заводов, Миньярского метизного завода, ММЗ "Серп и молот". Для каждого из них возможны решения с минимальными затратами. Разумеется, предприятия должны быть готовы принять финансовое участие в этих проектах.
В феврале прошлого года Министерство науки и технологий РФ совместно с ГНЦ "ЦНИИчермет" и АХК "ВНИИметмаш" провело совещание по разработке и внедрению модульных технологий для производства продукции массового назначения с новым уровнем свойств на переделе "сталь прокат". Подчеркнуто, что основным направлением развития передела явится внедрение технологических схем на базе совмещенных процессов, трансформируемых в литейно-прокатные агрегаты. В качестве основных координирующих организаций по этой проблеме определены АХК "ВНИИметмаш" и ГНЦ "ЦНИИчермет".
Суть организации производства "сталь прокат" в модульном исполнении заключается в создании производственных комплексов по принципу единого агрегата с совмещением смежных технологических операций. По сравнению с традиционными технологическими схемами ожидается снижение удельных капитальных затрат и себестоимости металлопроката на 30 50 % в сопоставимых условиях.
Назовем основные предпосылки для реализации таких технологий.
1. Составляющие комплекс агрегаты, как правило, проверены многолетней практикой и эксплуатируются в промышленности в условиях традиционных схем.
2. Из производственного цикла исключаются промежуточное складирование, остывание, ремонт и последующий длительный нагрев заготовки перед прокаткой. Таким образом сокращается цикл производства и расход всех видов ресурсов.
3. Качество литой заготовки в 85 % объема соответствует требованиям прямой прокатки; исключается снижение ее среднемассовой температуры перед прокаткой ниже 950о С; при прокатке обеспечивается применение режимов высоких обжатий.
4. Достигается минимальная длительность цикла "сталь прокат", минимизируются затраты всех видов ресурсов за счет синхронизации почасовой производительности всех агрегатов модуля с допуском превышения не более 15 % у последующего передела.
5. Обеспечивается работа комплекса в режиме автоматического управления.
Основной упор в создании модульных комплексов можно сделать на отечественное машиностроение или существующие совместные предприятия и холдинги, что значительно дешевле, чем использовать импортное оборудование.
|