Владимир Парамонов Государственный научный центр РФ "ЦНИИчермет им. И. П. Бардина"
Нанесение различных покрытий (металлических, полимерных, эмалевых) на поверхность стальных полуфабрикатов фактически переводит их в новый, весьма динамично развивающийся класс конструкционных материалов. Высокая коррозионная стойкость, прекрасная обрабатываемость и отличное сочетание механических характеристик, превосходные декоративные свойства обеспечивают этим изделиям широкое применение в различных сферах хозяйства (строительство, транспортное машиностроение, упаковка, товары длительного пользования и т.д.). Экономическая эффективность использования стальной продукции с покрытиями обуславливается существенным повышением надежности и сроков эксплуатации, а также ее относительно небольшой стоимостью по сравнению с прокатом из нержавеющей стали и цветных металлов. Если условно принять срок эффективного использования стального холоднокатаного листа за единицу, то для горячеоцинкованного листа этот показатель может составить не менее 1,3; для алюминированного листа 1,4; для листа с полимерным покрытием 2,4. Следует отметить также высокую рентабельность производства листа с покрытиями, которая составляет при выпуске белой жести около 45 %, а горячеоцинкованного листа 40 %, что обеспечивает быструю окупаемость инвестиционных затрат в производственное оборудование.
Россия пока отстает
В промышленно развитых странах доля стального листа с покрытиями составляет более половины всего холоднокатаного листового проката при четко выраженной тенденции дальнейшего роста этого показателя. Наиболее динамично (среднегодовой темп прироста 5,6 % за 1989 1996 гг.) растет производство оцинкованного металла. По данным аналитиков компании CRU International, в Северной Америке ежегодные темпы прироста оцинкованного листа в последние 15 лет составили около 6,6 %, в том числе полученного электролитическим способом более 14 %. В странах Западной Европы этот показатель составил в среднем около 5 и 3 % соответственно.
По оценкам журнала "Metal Bulletin", темпы производства оцинкованного листа в указанный период существенно опережали динамику выплавки стали. В ближайшие годы весьма вероятен дальнейший прирост мощностей по выпуску этой продукции в Северной Америке на 5 млн. т, в Европе не менее чем на 2 млн. т, в Азии на 8 млн. т. В значительной мере это объясняется ростом спроса со стороны автомобильных компаний.
Другим крупным потребителем продукции с покрытиями является строительный комплекс, где широко используются листовые полуфабрикаты с полимерным (в основном лакокрасочным) покрытием, наносимым на оцинкованный металл на специализированных агрегатах (Coil Coating). Так, в Германии в настоящее время выпускается около 1,3 млн. т, в Италии более 750 тыс. т, в Испании 630 тыс. т, в Великобритании более 400 тыс. т таких полуфабрикатов.
Существенные структурные сдвиги в последние годы наблюдались в производстве жести с покрытием оловом и хромом (TFS), которая является основным материалом для упаковки различных пищевых продуктов. В этой сфере основным направлением было снижение толщины жести до 0,17 0,19 мм и уменьшение слоя оловянного покрытия до 1,3 г/м. Это, безусловно, способствует повышению эффективности использования жести, так как снижение объема производства в весовых показателях сопровождается его существенным приростом по показателям площади.
Развитие производства металлопродукции с покрытиями в СССР существенно отставало от уровня ведущих промышленно развитых стран. Это отставание сохранилось и в России, где за годы реформ практически во всех отраслях экономики наблюдается спад производства и потребления всех видов металлопродукции с покрытиями (см. таблицу). В общем объеме производства проката доля этой продукции в России составляет в настоящее время около 3 % (для сравнения в США 23 %, в Германии около 19 %, в Японии 15 %).
Среди продукции с покрытиями в России в наибольшем объеме производится горячеоцинкованный лист, который выпускают АО "ММК", АО "НЛМК" и АО "Северсталь", небольшое количество электролитически оцинкованной и освинцованной стали производит АО "Лысьвенский металлургический завод".
В Казахстане осуществлен пуск и начато освоение нового высокопроизводительного агрегата горячего цинкования и нанесения покрытия цинкоалюминиевыми сплавами типа "гальвалюм" (55 % Al, 43 % Zn).
Большая часть оцинкованного листа используется в строительстве, в основном в виде профилированного настила для кровельных и стеновых панелей для промышленных и административных зданий, сельскохозяйственных строений, сборных складских помещений, а также в жилищном индивидуальном строительстве. Значительная часть оцинкованного металла экспортируется. Однако в связи с наметившимся ростом промышленного и жилищного строительства доля экспорта оцинкованной стали, очевидно, в ближайшие годы будет сокращаться, а внутреннее потребление оцинкованного листа расти.
Главный потребитель автопром
Одним из основных потребителей оцинкованной стали в развитых странах является автомобильная промышленность. В последнее время значительно возросли требования по коррозионной стойкости кузовов и других узлов автомобилей в связи с необходимостью увеличения сроков их эксплуатации. Крупнейшие металлургические и автомобилестроительные фирмы пошли на значительные капиталовложения для организации производства различных видов оцинкованной стали для кузовных и других деталей при существенном повышении качества металлопродукции, что позволяет автозаводам обеспечивать гарантированную длительность службы кузовов автомобилей в отношении косметической и сквозной коррозии. Сегодня, без преувеличения, качество и конкурентоспособность автомобиля напрямую зависят от применения оцинкованной стали для кузовных деталей.
Для России с ее суровыми климатическими условиями, с большим использованием солей и кислот в зимний период применение оцинкованной стали исключительно важно. Однако в настоящее время в автомобильной промышленности России оцинкованная сталь применяется сравнительно мало. На кузовных деталях российских машин косметическая коррозия, т. е. первые следы ржавчины, появляется уже в первые 1 2 года эксплуатации, а через 3 5 лет имеет место многочисленная сквозная коррозия. Только в последние 2 года на АвтоВАЗе начали использовать электролитически оцинкованную сталь с односторонним покрытием для автомобилей ВАЗ 2110, некоторое количество оцинкованного листа используется для моделей 2108 и 2109. Для этих целей в 1997 году было закуплено по импорту около 40 тыс. т электролитически оцинкованной стали. В 1998 году потребность ВАЗа составляет 45 тыс. т, в 2000 году около 100 тыс. т, а в 2003 году 150 тыс. т.
Потребность в оцинкованном стальном листе АО "ГАЗ" и АО "АЗЛК" на ближайшие годы оценивается как минимум в 100 тыс. т ежегодно.
Можно ожидать, что после реализации намеченных мероприятий по развитию автомобильной промышленности потребность в оцинкованном листе составит примерно 200 тыс. т в 2000 году и 250 тыс. т в 2005 году, хотя по нормам потребления оцинкованного листа на один автомобиль в Западной Европе и Америке (330 350 кг) для намеченного производства автомобилей в указанные годы потребность в этой продукции должна быть в два раза больше.
Как известно, основным материалом, применяемым для изготовления кузовных деталей автомобилей, является электролитически и горячеоцинкованная сталь с высокими пластическими свойствами. При этом в мировой практике доля электролитически оцинкованного металла с односторонним и двусторонним покрытием в автомобилестроении значительно превосходит долю горячеоцинкованного листа. Однако, учитывая меньшую стоимость горячеоцинкованного листа и возможность получения покрытия в виде железоцинкового сплава ("гальванил") с высокими пластическими свойствами за счет применения сверхнизкоуглеродистых сталей типа "IF", доля используемой горячеоцинкованной стали в ближайшем будущем значительно возрастет.
Все построенные и реконструированные в последние годы за рубежом агрегаты горячего цинкования специализированы на производстве горячеоцинкованного автолиста и имеют в своем составе специальную, чаще всего индукционную, печь для получения "гальванила" (содержание железа около 12 %).
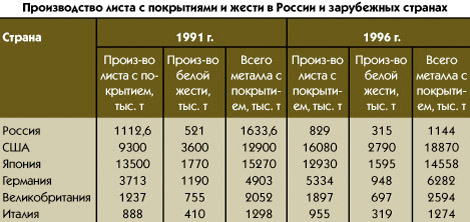 В настоящее время автомобильные заводы России оснащены в значительной мере устаревшим оборудованием и не могут использовать всю гамму оцинкованных сталей. Так, АвтоВАЗ для основных кузовных деталей может использовать только электролитически оцинкованную сталь с односторонним покрытием, а для других деталей автомобиля некоторое количество горячеоцинкованной стали. Другие автозаводы находятся не в лучшем положении и не смогут без дополнительного оснащения широко использовать оцинкованный лист. В то же время проблему широкого использования оцинкованного листа заводы вынуждены будут решать незамедлительно, так как дальнейшее производство автомобилей без противокоррозионной защиты не обеспечит необходимого сбыта внутри страны, а тем более, выход на мировой рынок.
В настоящее время очевидно, что развитие отечественной автопромышленности во многом связано с организацией производства электролитически оцинкованной стали всего необходимого сортамента и горячеоцинкованной стали с высокими пластическими свойствами.
Сегодня в России подобную металлопродукцию производит Лысьвенский завод, однако размерный ограниченный сортамент не позволяет использовать ее для кузовных деталей автомобилей.
Для организации производства электролитически оцинкованной стали, в объемах и сортаменте удовлетворяющей потребность автопромышленности, необходим ввод новых агрегатов. Ранее было намечено строительство двух агрегатов на Новолипецком и Магнитогорском металлургических комбинатах производительностью по 300 350 тыс. т в год. Однако, учитывая ограниченность средств, намечалось в первую очередь (до 2000 года) провести дооборудование агрегата полимерных покрытий АО "НЛМК" узлом электроцинкования и реконструировать агрегат Лысьвенского завода на ширину полосы до 1800 мм, что в значительной мере позволило бы снять дефицит в этом материале.
Главным лимитирующим фактором является недостаточно развитая машиностроительная база, и отсюда низкий уровень технологической части оборудования агрегата электролитического цинкования.
Следует отметить, что выпускаемое ранее отечественное оборудование для нанесения покрытий отличалось конструктивными ошибками и плохим качеством изготовления, что приводило к необходимости многочисленных переделок отдельных узлов оборудования, а сроки освоения непомерно затягивались. Особенно плохого качества было оборудование химической и электрохимической обработки, включая вспомогательное оборудование, сварочные машины, электрическое оборудование и автоматику.
В связи с этим наиболее целесообразным представляется проведение проектирования и изготовление в АО "Уралмаш" хвостовой и головной частей агрегатов с привлечением одной из специализированных зарубежных фирм для изготовления остальной технологической части агрегата. Для полного удовлетворения потребностей автопромышленности в листовом прокате с покрытиями для кузовов в обозримой перспективе целесообразно строительство двух агрегатов электролитического цинкования на АО "НЛМК" и АО "ММК", а также реконструкция агрегатов горячего цинкования на АО "Северсталь" и АО "ММК" с частичным переводом их на производство оцинкованного автомобильного листа.
Жесть и полимеры
Для России серьезные проблемы в производстве жести всего необходимого сортамента возникли после разрыва традиционных связей с Казахстаном и сокращения поставок жести с Карагандинского металлургического комбината (ИСПАТ-КАРМЕТ). Магнитогорский металлургический комбинат остался единственным в России производителем жести, причем его устаревшее оборудование не обеспечивает производства всех видов и сортамента жести, требуемого современным потребителем.
Цех жести АО "ММК" не выпускает наиболее дефицитные виды жести толщиной 0,18 0,20 мм, шириной более 820 мм, жесть двойной прокатки, тончайшую жесть 0,14 0,15 мм. Сокращено до минимума производство хромированной жести на Лысьвенском металлургическом заводе из-за высокой стоимости подката, поставляемого из Караганды.
Таким образом в России не производятся наиболее экономичные виды жести, потребность в которых удовлетворяется за счет импорта. В этой связи в ближайшей перспективе необходима реконструкция цеха жести АО "ММК" с целью обеспечения производства всего требуемого сортамента и увеличения общего производства жести.
Серьезной проблемой является отработка сквозной технологии производства жести от выплавки стали до электролитического лужения и отделки белой жести. На Магнитогорском металлургическом комбинате эта проблема возникла в связи с переходом на производство жести из конвертерной стали непрерывной разливки. Международными стандартами предусматривается строгое ограничение по составу стали, включая такие элементы, как алюминий, кремний и другие, что особенно важно при производстве жести с тонкими покрытиями первого класса и ниже. Такие покрытия становятся основными, поэтому и процесс электролитического лужения должен обеспечивать получение покрытия высокой коррозионной стойкости, главным образом за счет высокой плотности и равномерности оловянного слоя.
Этим требованиям отвечает новый процесс электролитического лужения из сульфаминового электролита, разработанный ГНЦ "ЦНИИчермет" совместно с АО "ММК" и "ИСПАТ-КАРМЕТ". Процесс является экологически чистым по сравнению с применяемым ранее, где использовалась фенолсульфоновая кислота, и обеспечивает высокую плотность и равномерность оловянного покрытия, отсутствие краевого эффекта и других дефектов покрытия, характерных для старого электролита. Новый процесс электролитического лужения внедрен на всех агрегатах АО "ММК" и "ИСПАТ-КАРМЕТ", к нему также проявляет интерес ряд зарубежных фирм.
Анализ потребления жести показывает, что в дальнейшем потребуется строительство нового цеха жести мощностью до 500 700 тыс. т в год с набором оборудования, обеспечивающим производство всех современных видов жести.
Производство стальной полосы с полимерными покрытиями (Coil Coating) было создано в бывшем СССР на ряде металлургических комбинатов, заводах строительной индустрии и др. Оборудование в основном было закуплено по импорту и представляло собой непрерывные линии для нанесения на стальную оцинкованную или алюминиевую полосу различных полимерных покрытий. Во многих случаях в комплект оборудования входили профилегибочные станы и другое оборудование для изготовления профилированного настила, стеновых и крышных панелей. Во всех линиях полимерных покрытий предусмотрена современная технология нанесения покрытий в виде лакокрасочных, органозольных, пластизольных и пленочных материалов. В России наиболее крупные агрегаты работают в АО "НЛМК", "Профнастил" (Челябинск), АО "Электрощит" (Самара), АО "Совиталпродмаш" (Волжск), АО "Лысьвенский металлургический завод" и др. Общая мощность всех линий составляет более 350 тыс. т/год. Однако в 1997 году было произведено всего около 25 тыс. т оцинкованной стали с полимерными покрытиями, что объясняется спадом в промышленном и гражданском строительстве, высокой ценой отечественных и зарубежных полимерных материалов и, как следствие, высокой стоимостью такого материала для отечественного потребителя.
Совершенно очевидно, что такой материал, как оцинкованная сталь с полимерными покрытиями, имеющая практически неограниченный срок безремонтной службы, нашедшая в мире самое широкое применение в строительстве, машиностроении, бытовой технике и др., не может быть не востребован отечественным потребителем. Уже сейчас потребность в этом материале начинает расти за счет использования его в виде профилированного настила в индустриальном строительстве при сооружении торговых комплексов, кафе, ресторанов, в индивидуальном строительстве в виде металлочерепицы для крыш и др.
Основа прогресса научные разработки
Государственный научный центр РФ "ЦНИИчермет им. И.П. Бардина" является одним из ведущих научных подразделений в области металлопродукции с покрытиями. Многие его разработки соответствуют самым высоким международным стандартам. Авторитет института в этой области способствует привлечению заказчиков и быстрому внедрению научных разработок в производство. Так, важная задача по разработке технологии и организации производства полосы с электролитическим покрытием сплавом свинец-олово для бензобаков автомобилей была в короткие сроки решена учеными ГНЦ "ЦНИИчермет" совместно со специалистами АО "Лысьвенский металлургический завод" и АО "АвтоВАЗ".
Для агрегатов электроцинкования разработана современная скоростная технология нанесения покрытия цинком, сплавами цинк-никель, цинк-железо, а также с возможностью дополнительной хром-хроматной обработки.
Особо следует остановиться на разрабатываемом совместно с фирмой "Маннесманн Демаг" процессе под условным названием "Вертикаль". Суть его заключается в использовании МГД затвора для удержания жидкого металлического расплава в процессе нанесения горячих покрытий (цинкования, алюминирования, алюмоцинкования гальвалюм) при вертикальном прохождении полосы через жидкий расплав. В этом процессе полоса проходит вертикально через ванну покрытия, при этом отсутствует всякое погружное оборудование, и стальная полоса имеет очень короткий контакт с расплавом металла покрытия. Такой процесс опробован на опытном агрегате с движущейся полосой шириной до 250 мм. В ближайшем будущем этот процесс будет опробован на одной из промышленных линий с последующим внедрением его на другие агрегаты, особенно для процессов алюмоцинкования (гальфан, гальвалюм) и алюминирования.
На стадии опытно-промышленного внедрения находится процесс получения так называемых оксидных покрытий стальной полосы. Процесс заключается в том, что при непрерывном отжиге тонкой стальной полосы в одной из промежуточных камер охлаждения производится регулируемое окисление поверхности, в результате которого образуется тонкая и прочносцепленная оксидная пленка необходимого состава. Такое покрытие, самостоятельное или в сочетании с лакокрасочным покрытием, может быть использовано в различных областях применения.
Серьезной задачей является коренное усовершенствование процессов нанесения покрытий металлическим хромом и хроматными пленками, которые в настоящее время осуществляются из электролитов и растворов на основе шестивалентного хрома и широко используются при производстве жести типа TFS. В лабораторных условиях нами разработан процесс по получению хромового покрытия на жести (TFS) из экологически чистых электролитов, основанный на использовании солей трехвалентного хрома, а также получение покрытий из сплавов железо-хром, имеющих высокую коррозионную стойкость, хорошую адгезию лакокрасочных материалов и способность к сварке.
Перспективным и оригинальным является процесс, также разработанный в лабораторных условиях, получения тонких железных полос из чистого железа электролитическим способом. Эта технология включает в себя три передела: электролиз, термообработку и холодную прокатку. Изменяя режимы этих переделов, можно изменять в довольно широком диапазоне физико-механические и магнитные свойства тонких железных полос. Производство таких полос можно организовать как в составе металлургического предприятия, так и на других заводах. Потребителем тонких полос из чистого железа является электронная и электротехническая промышленность.
Оригинальная технология нанесения лакокрасочных покрытий внедрена на Лысьвенском металлургическом заводе. Она заключается в электростатическом распылении лакокрасочного материала на движущуюся стальную полосу с последующей индукционной сушкой покрытия. В этом процессе отсутствуют традиционные печи для сравнительно длительного процесса полимеризации лака, а весь процесс термообработки занимает несколько секунд. По такой технологии на Лысьвенском металлургическом заводе производится лакирование жести типа TFS.
Эти и некоторые другие процессы могут лечь в основу новых технологий, реализуемых в XXI веке при производстве листового проката с покрытиями.
|