|
|
Журнал |
|
Архив |
|
Подписка |
|
Реклама |
|
САММИТ |
|
Книжная полка |
|
Контакты |
|
В начало |
|
|
|
| |
|
|
|
"МИРОВАЯ МЕТАЛЛУРГИЯ. ВЫЗОВЫ ГЛОБАЛИЗАЦИИ." |
2-Й МЕТАЛЛУРГИЧЕСКИЙ САММИТ В МОСКВЕ |
Владимир Дунаев Генеральный директор ЗАО «Управляющая компания «Магнезит Огнеупор Групп»
ОПЫТ УСПЕШНОЙ СТРАТЕГИИ НА ГЛОБАЛЬНЫХ РЫНКАХ
гнеупорная промышленность России состоит из нескольких групп производителей. Основной объем продукции выпускают 1012 крупных специализированных предприятий, включая лидеров отрасли комбинат «Магнезит», Боровичский комбинат огнеупоров и «Динур». Достаточно успешно действуют на рынке 68 специализированных предприятий среднего размера, а также группа малого бизнеса. Помимо этого, крупные собственные огнеупорные производства существуют на Магнитогорском, Нижнетагильском и Новолипецком металлургических комбинатах, на «Мечеле» и «Уральской стали».
Сегодня объем производства огнеупоров в России составляет менее половины от уровня, достигнутого к началу 90-х годов. Однако это не является показателем кризиса огнеупорной промышленности. Скорее следует говорить о прогрессе технологий в производстве как огнеупоров, так и стали. Так, снижение ее производства мартеновским способом неминуемо ведет к сокращению удельного расхода огнеупоров. Аналогичный эффект вызывает и повышение качества огнеупорной продукции. К примеру, если в начале 90-х годов стойкость футеровки конвертеров обычно не превышала 1000 плавок, то сегодня лучшие производители гарантируют стойкость на уровне 45 тыс. В частности, наша футеровка, установленная на конвертере ММК, выдерживает сейчас до 5 тыс. плавок.
Серьезно меняется структура потребления огнеупорной продукции в России. В первую очередь, это вызвано совершенствованием технологического процесса на металлургических предприятиях. В результате за последние 12 лет существенно изменился ассортимент выпускаемой огнеупорной продукции, что выразилось прежде всего в увеличении доли магнезиальных огнеупоров более высокого качества, в первую очередь, периклазоуглеродистых.
В ближайшие годы мы прогнозируем рост потребления в России неформованных огнеупоров. Доля этого вида продукции в общем объеме потребления ведущих стран мира составляет 5065 %. У нас же пока не превышает 15 %.
Обновление огнеупорной промышленности пойдет по двум основным направлениям реформирование организационной структуры и модернизация технологических процессов.
Организационные изменения, на наш взгляд, проявятся в консолидации предприятий-производителей. Только крупные огнеупорные конгломераты могут сконцентрировать средства на создании исследовательских центров, модернизации производственных процессов, развитии сырьевой базы. Кроме того, крупные корпорации имеют возможность проводить гибкую ценовую политику, не снижая при этом своих финансовых результатов.
По сути, консолидация производителей огнеупоров в России уже началась. На базе комбината «Магнезит» мы начали строить холдинг, центром управления которым на стадии формирования выступает управляющая компания «Магнезит Огнеупор Групп».
Одновременно с укрупнением огнеупорных предприятий будет происходить сокращение количества производителей среднего размера. Только за последний год практически остановили производство огнеупоров Латненский завод в Воронежской области, Домодедовский в Московской и Восточно-Сибирский завод в Иркутской области.
Представляется, что огнеупорные производства металлургических комбинатов будут со временем выделены по экономическим соображениям в самостоятельные бизнес-единицы.
Изменения на рынке вынуждают производителей огнеупоров России ускорить темпы модернизации собственного производства. Например, комбинат «Магнезит» в ближайшее время начнет строительство технологического комплекса, включающего мощности по кальцинированию сырого магнезита, брикетированию каустического магнезиального порошка, а также высокотемпературную шахтную печь для обжига брикета.
Крупные производители огнеупоров активно внедряют современное оборудование для производства периклазоуглеродистых огнеупоров. Ряд предприятий начали выпуск современных видов неформованных материалов, имеющих большие перспективы применения в металлургии. Например, «Динур»успешно работает в нише неформованных огнеупоров для доменного производства. Однако потребность в таких огнеупорах для различных агрегатов растет быстрее, чем их производство. Создание до конца 2004 года холдингом «Магнезит Огнеупор Групп» и немецкой фирмой «Интокаст» совместного предприятия отчасти решит эту проблему. «Интокаст» предоставит нам современное оборудование и технологии, аналогов которых в России сегодня нет. Кроме того, немецкий партнер выразил готовность организовать повышение квалификации специалистов СП, что соответствует нашей стратегии развития персонала. Все это позволяет рассматривать СП как приоритетный проект, имеющий стратегическое значение для развития не только нашей компании, но и всей огнеупорной отрасли России.
Отдельное направление в ее обновлении занимает развитие на предприятиях огнеупорной отрасли системы инжиниринга с предоставлением потребителям полного комплекса услуг в области комплектации тепловых агрегатов. В рамках этого направления холдинг «Магнезит Огнеупор Групп» недавно создал инжиниринговый центр, отвечающий за комплексное обслуживание тепловых агрегатов. Центр предлагает весь спектр огнеупоров, включая продукцию, не выпускаемую предприятиями холдинга. Такая продукция поставляется в рамках агентских договоров с ведущими фирмами Европы и Китая. В комплекте с огнеупорами инжиниринговый центр может предложить поставку оборудования для выполнения футеровочных работ, сервисное обслуживание тепловых агрегатов. Кроме того, центр поддерживает непрерывную связь со специалистами металлургических предприятий, в результате чего вырабатываются предложения по совершенствованию существующих и созданию новых продуктов.
Мы считаем, что для успешной модернизации огнеупорной отрасли России с учетом требований конечных потребителей необходимы целевые инвестиции по следующим основным направлениям.
1. Инвестиции в развитие производственных площадок. В первую очередь это касается глубокой модернизации технологических процессов, оставшихся в наследство от советской системы массового производства узкой номенклатуры продукции. Сегодня нам необходимо создавать более гибкие производственные линии, позволяющие оперативно реагировать на запросы потребителей, выпуская как небольшие, так и крупные партии продукции стабильно высокого качества.
2. Инвестиции в развитие системы дистрибуции. Здесь следует акцентировать внимание на расширении дистрибьюторской сети и повышении уровня сервиса, внедрении системы комплексного обслуживания тепловых агрегатов. Например, наш холдинг планирует завершить реорганизацию дистрибьюторской сети к концу 2004 года. К этому времени во всех значимых регионах потребления на территории СНГ и Восточной Европы будут созданы представительства сбытовой сети холдинга.
3. Инвестиции в развитие системы снабжения. Прежде всего необходимо решать вопросы, связанные с обеспечением российских производителей огнеупоров отечественным сырьем высокого качества. Эта задача, по нашему мнению, носит стратегический характер. Так, холдинг «Магнезит Огнеупор Групп» предполагает осуществить значительные инвестиции в разработку крупнейшего месторождения высококачественного магнезита в Красноярском крае.
4. Целенаправленные инвестиции в НИОКР. Сегодня они являются обязательным условием сохранения конкурентоспособности на огнеупорном рынке.
5. Модернизация производства, внедрение комплексного обслуживания тепловых агрегатов, технические и технологические новшества не принесут ожидаемых результатов без развития систем обучения, аттестации и мотивации персонала. Поэтому пятым важным направлением целевых вложений я бы назвал инвестиции в подготовку кадров.
Все инвестиции холдинга «Магнезит Огнеупор Групп» в настоящее время подчинены долгосрочной корпоративной стратегии развития. Это дает твердую уверенность в том, что мы сможем укрепить лидирующие позиции в огнеупорной отрасли России и сделать бизнес наших партнеров-металлургов еще более эффективным.
Юрий Мишин Директор по маркетингу управляющей компании «Промышленно-металлургический холдинг»
КИТАЙСКИЙ ФАКТОР РЫНКА МЕТАЛЛОРЕСУРСОВ
правляющая компания «Промышленно-металлургический холдинг» сравнительно новое образование, созданное примерно 1,5 года назад. Оно объединяет несколько предприятий, в первую очередь, в угольном бизнесе несколько шахт и разрез в Кузбассе, там же Березовская обогатительная фабрика, Кемеровский коксохимический завод «Кокс», а также производители чугуна компания «Тулачермет», ванадиевой продукции «Ванадий-Тула», молибдена, хрома, вольфрама и изделий из этих металлов «Полема» и ряд предприятий по производству металлоконструкций и чугунного литья.
«Тулачермет» является крупнейшим поставщиком чугуна на рынок, в том числе международный. По нашим оценкам, это примерно 20 % мирового рынка. Мы попытались оценить, как в мире меняется потребность в металлоресурсах для производства стали. Расчеты показывают, что переработка скрапа за последний год увеличилась на 3035 млн т, что в общем-то немало. Доля металлолома в общей потребности остается более-менее стабильной и составляет 3637 %. Эта тенденция прослеживается уже в течение достаточно длительного времени.
Здесь говорилось, что рост потребления лома привел к увеличению объема торговли на международном рынке примерно на 10 млн т. Ведущие поставщики начали обращаться в свои правительства с просьбой установить контроль над экспортом металлолома как важнейшего стратегического сырья. Я, честно говоря, надеялся услышать в выступлении руководителя МАИР информацию по поводу того, что же у нас происходит с ломом. К сожалению, ничего вразумительного об этом не сказано.
Те процессы, которые в последнее время происходят на мировом рынке, в значительной степени обусловлены ситуацией в Китае. Во-первых, он прекратил крупные поставки чугуна на международный рынок. Увеличил импорт металлолома до 910 млн т, металлизованного сырья до 1,61,8 млн т. Если все суммировать, Китай стал дополнительно выводить с международного рынка примерно 1315 млн т металлоресурсов в год по сравнению с тем, что было несколько лет назад.
В последние два года наблюдается цикличное развитие цен и объемов продаж, что, на наш взгляд, спровоцировано двумя факторами. С одной стороны, это совершенно объективный фактор роста потребности в готовой стальной продукции, а с другой, фактор чисто психологический, связанный со спекулятивными процессами. В конце 2002 года начале 2003 года произошел первый резкий скачок, когда буквально за 3 месяца цены на основные виды металлопродукции увеличились на 3040 %. Рост на сырьевые компоненты составил 5070 %. Затем в марте-апреле 2003 года цены несколько снизились, потом стабилизировались. В этом году ситуация повторилась с поразительной точностью, но на гораздо более высоком ценовом уровне. В Китае продолжала расти потребность в стальной продукции. И здесь, видимо, сыграли роль опасения китайских металлургов, что у них будет очень ощущаться дефицит сырья. В результате с декабря 2003 года до марта 2004 года опять-таки произошел резкий бросок цен, более серьезный, чем в прошлом году, когда цены на стальную продукцию увеличились на 6080 %, на лом и чугун на 100 % и более.
Сейчас опять-таки происходит реакция рынка, но отличие от ранее имевшей место заключается в том, что КНР стала усиливать меры государственного регулирования в основных отраслях промышленности. Можно также отметить, что на все эти резкие скачки оказывает влияние сама структура металлургического бизнеса в Китае и то, как осуществляются закупочные операции. При общем производстве в 220 млн т распределение было следующим: 40 млн т, 18 % выпускается на предприятиях с годовым производством меньше 1 млн т. Предприятия с объемом 12 млн т выпускают почти 30 млн т. Получается, что 70 млн т выпускается небольшими предприятиями, которые самостоятельно никогда на экспортные и импортные рынки не выходят, все закупают через трейдеров. При этом в Китае просто неисчислимое количество этих компаний-трейдеров, которые, если появляется спрос на рынке, начинают проявлять очень высокую активность, существенно приумножая фактическую потребность конечных потребителей. А когда ситуация становится определеннее, трейдеры начинают нервничать, избавляться от накопившегося, и это толкает ситуацию вниз.
Последнее, что хотел бы отметить. Сегодня создалась ситуация, когда Китай, являясь крупнейшим поставщиком кокса, начинает показывать нам те рычаги, которыми он в скором времени начнет оперировать на международных рынках. Сегодня установлены искусственные планки в ценах на кокс, которые находятся на уровне 420 долл./т фоб. 200 долл из них это стоимость лицензии, которую должен купить китайский поставщик. Думаю, именно так Китай будет действовать в будущем.
Ибрагим Едильбаев Вице-президент Евразийской промышленной ассоциации, Казахстан
НАДЕЖНЫЙ ПОСТАВЩИК ХРОМОВОГО СЫРЬЯ
орно-металлургические предприятия, входящие в Евразийскую промышленную ассоциацию (ЕПА), являются традиционными поставщиками железорудного и хромоворудного сырья, угля и электроэнергии для металлургического и энергетического комплексов Урала и Сибири. Соколовско-Сарбайское производственное объединение поставляет Магнитогорскому металлургическому комбинату большую часть своей продукции свыше 10 млн т в год. «Казхром» поставляет в Россию хромовую руду и ферросплавы, «Алюминий Казахстана» высококачественный глинозем в объеме 1400 тыс. т в год. Евроазиатская энергетическая корпорация (ЕЭК) поставляет уголь и электроэнергию. Все предприятия динамично развиваются, чтобы и в будущем оставаться надежными партнерами.
ТНК «Казхром» в составе Донского горно-обогатительного комбината, Аксуского и Актюбинского экспортирует свою продукцию в 15 стран мира. Компания постоянно наращивает объемы производства, расширяет номенклатуру выпускаемой продукции, постепенно завоевывая новые рынки. Стратегические цели ТНК «Казхром» укрепление лидирующих позиций в мировой ферросплавной промышленности, в первую очередь, хромовой. Компания активно участвует в организации высокотехнологичных производств с комплексной углубленной переработкой минерального сырья в рамках реализации Стратегии индустриально-инновационного развития Республики Казахстан на 20032015 годы.
В числе приоритетных инновационных проектов компании внедрение технологий получения металлизированных и хромитовых окатышей из неликвидного, мелкого рудного сырья, окускование мелких фракций марганцевых руд, раздельное складирование и вторичная переработка пылей и зол основных и вспомогательных производств, реконструкция и совершенствование основных производственных мощностей, получение ильменитовых, рутиловых и цирконовых концентратов, вторичная переработка шлаков и отходов производства с доизвлечением металла, получение рудных концентратов из хвостов обогатительных фабрик и техногенных рудных отходов, внедрение передовых технологий производства дешевой электрической энергии на газотурбинных электростанциях там, где генерирующие энергетические мощности ограничены. Реализация вышеуказанных проектов позволит обеспечить к 2008 году рост производства феррохрома в два раза, существенно увеличить производство кремниевых и марганцевых сплавов без строительства новых ферросплавных печей.
В ходе реализации проектов развития металлургического производства особое внимание уделяется укреплению сырьевой базы хромовой отрасли. Ежегодно выделяются достаточные инвестиционные средства на развитие шахт, обогатительного передела, на производство брикетов, окатышей и агломерата из неликвидных мелких руд и концентратов, а также на строительство природоохранных объектов. Все подразделения «Казхрома» имеют сертификаты соответствия систем управления качеством требованиям международного стандарта ИСО 9001:2000.
Основой оптимистического взгляда на будущее компании служит наличие крупных подтвержденных запасов высококачественных хромитовых руд в западном регионе республики, на базе которых действует Донской горно-обогатительный комбинат. По химическому составу руды являются высокосортными, металлургического класса. Содержание полезного компонента оксида хрома изменяется от 30 до 55 %, содержание вредных компонентов (кремнезем, фосфор, сера, кальций) незначительно. Детальная геологическая изученность месторождения обеспечивает высокую сходимость оценки запасов и показателей качества хромовых руд по данным разведки и эксплуатации. Прогнозные ресурсы по богатым хромовым рудам промышленных категорий составляют около 300 млн т, прогнозные ресурсы более бедных, но имеющих выходы на поверхность также оцениваются в сотни млн т.
До 95 % руд будут отрабатываться подземным способом, тогда как до 1995 года была преимущественно открытая добыча. За очень короткий срок удалось осуществить плавный переход на подземную добычу. В ближайшие 2530 лет действующая шахта «Молодежная» даст по 2 млн т в год. Развивается недавно введенная в эксплуатацию новая подземная шахта «10 лет независимости Казахстана», общая мощность которой рассчитана на 4 млн т руды. Первая очередь в 2 млн т уже работает и будет освоена в течение 23 лет. Для обеспечения перспективного развития ТНК «Казхром» заключил с Правительством в 2003 году контракт на проведение геологоразведочных работ на новой рудоносной площади на юго-западе Актюбинской области, где прогнозируется крупный рудный объект. С целью повышения степени извлечения металлов из руды и увеличения выпуска концентратов готовится полномасштабная реконструкция обогатительных фабрик с заменой устаревшего оборудования на современное.
Аркадий Вундер Директор Серовского завода ферросплавов по внешнеэкономическим связям
ОТЕЧЕСТВЕННЫЙ ФЕРРОХРОМ: СПОСОБНОСТЬ К КОНКУРЕНЦИИ
лагодарю организаторов саммита за возможность пообщаться на таком высоком уровне. Слушая доклады, я поймал себя на мысли, что мы друг друга повторяем. Проблемы-то у всех одинаковые что у сталеплавильщиков, что у ферросплавщиков, что у других. Рост цен на продукцию черной металлургии коснулся и нас, производителей феррохрома. По данным Metall Bulletin, цена на все виды феррохрома выросла практически в 2 раза. Мы достаточно хорошо знаем цикличность нашего рынка, на моей памяти это третий скачок. Дальше придется падать, вопрос: куда? Поэтому не только мы, но и зарубежные фирмы провели исследования: устойчиво ли производство?
В 2003 году Россия произвела всего 76 тыс. т высокоуглеродистого феррохрома из мировых 5 млн т. Несколько другое положение на рынке низкоуглеродистого хрома. Здесь Россия произвела 181 тыс. т из 500 тыс. т. Большинство исследователей сходятся в том, что в близком будущем Казахстан, Южная Африка и, по-видимому, Индия смогут обеспечить всех потребителей высокоуглеродистым феррохромом.
76 тыс. т российской продукции вроде бы немного, но качество нашего феррохрома хоть и хуже, чем казахского, все же лучше, чем юаровского. Когда рынок хороший, мы свою нишу находим. Что касается рынка низко- и среднеуглеродистого феррохрома, Россия всегда была главным игроком: 37 % среди основных конкурентов ЮАР, Казахстан, Германия и Китай, но КНР из экспортеров феррохрома стал импортером.
Что определяет спрос и предложение на рынке феррохрома? Это рост производства нержавеющих сталей около 5 % в год, в Китае до 10 %. А предложение феррохрома определяется прежде всего наличием и стоимостью руды, энергоресурсов, углеродистых восстановителей. Сегодня говорили уже, что с коксом проблемы. Его стоимость выросла для нас в 34 раза. И если мы когда-то мечтали, что низкофосфористый кокс будем покупать в Китае, сейчас такой проблемы нет.
Большая проблема соотношение курсов валют для внешних рынков. Даже Южная Африка в связи с тем, что национальная валюта стала достаточно крепкой, испытывают трудности. Цена электроэнергии там выросла в 1,51,7 раза. Еще одна проблема стоимость транспортировки, поскольку ферросплавные заводы расположены достаточно далеко от потребителя. У нас достаточно много проблем, связанных с качеством рабочих кадров.
Из чего складывается себестоимость нашей продукции? При производстве углеродистого феррохрома стоимость руды составляет 63 % общей стоимости, средне- и низкоуглеродистого 3436 %, электроэнергии, соответственно, 18 % и 79 %. кремнистого восстановителя 45 % и 36 %. Эти расчеты сделаны для Серовского завода, но в Челябинске структура такая же.
Качество российского феррохрома, в частности серовского, не уступает мировым стандартам, здесь особых проблем нет, за исключением того, что заводы до сих пор не аттестованы по ISO 9000. Но работа ведется. Еще важно отношение правительства к нашей подотрасли. Достаточно сказать, что мы завозим руду, которой в России нет, и платим при этом высокую ввозную пошлину. Год назад мы обратились в Минэкономразвития, нам сказали «да», мы подготовили пачку документов. Долго была тишина, потом пришел ответ в таком духе: дайте справку, что вам нужна справка.
По нашим экспертным оценкам, продукция Южной Африки и Казахстана примерно одинакова по конкурентному уровню, а Россия отстает. В чем преимущество наших конкурентов? У них относительно низкая стоимость шихтовых материалов, преимущественно руды, как и электроэнергии.
Мы пытаемся предпринимать свои действия. Создаем собственную хромоворудную базу. Пришли на Сарановскую шахту в Пермской области. Никто не думал, что она может давать 150 тыс. т руды в год. Именно благодаря этой руде выстояли в трудное время после развала СССР. С апреля Серовский завод ферросплавов владеет контрольным пакетом акций трех рудников в Турции и ведет аналогичную работу на Ямале, где также действует Челябинский комбинат. В принципе, мы приближаемся к решению рудной проблемы.
Ведутся переговоры о более-менее щадящих тарифах на электроэнергию. Завод полностью перешел на отгрузку продукции в контейнерах, за счет чего, в первую очередь, снижена стоимость транспортных расходов, во-вторых, поставки осуществляются в срок, в нужном количестве и туда, куда надо. Не секрет, что у российских производителей потери велики при транспортировке в открытых полувагонах.
Хромовые заводы России стали обращать внимание на шлаковые отвалы. У нас лежит 8 млн т шлака в отвале. Действует первая очередь шлакопереработки, ведем переговоры с инвесторами о начале строительства второй очереди. Занимаемся брикетированием мелких руд.
И последнее о совершенствовании организации производства. Сейчас организуется холдинг, в который будет входит Серовский завод ферросплавов, завод «Русский хром», Сарановская рудная шахта, ферросплавный завод в Германии Weisweiler и шахты в Турции. Все это позволяет нам с определенным оптимизмом смотреть в будущее.
Евгений Панков Холдинг ВМС
ВЫГОДНЫЕ РАСКИСЛИТЕЛИ
одольский завод вторичных металлов и сплавов, являющийся частью холдинга ВМС, входит в пятерку крупнейших производителей вторичного алюминия и отличается от других предприятий тем, что здесь уделяется большое внимание постоянному совершенствованию технологий, выбору такого оборудования, которое позволило бы занимать лидерские позиции. В 2000 году, когда были пущены первые небольшие плавильные печи, мощность завода составила 20 тыс. т вторичного алюминия в год, а к концу 2004 года мы планируем довести ее до 50 тыс. т, а при возможности и больше. Основной продукцией являются литейные алюминий-кремниевые сплавы, которые широко используются в автомобильной промышленности и в России, и за рубежом, а также раскислитель в виде мелкой чушки либо мелких форм. В конце 2004 года наше предприятие намерено приступить к выпуску алюминиевой катанки.
С 2001 года мы имеем сертификат ISO 9001 версия 2000 года, а с 2002 года наше предприятие зарегистрировано на Лондонской бирже металлов. Все больше внимания и на Западе, и у нас уделяется внепечной обработке стали. Более точное дозирование раскислителя позволяет более точно регулировать качество стали, при этом улучшаются условия труда. Мы сделали сравнительный анализ применения разных форм раскислителя. Традиционно в этом качестве используется чушка. Она имеет достаточно низкую степень усвоения, то есть меньше трети алюминия идет собственно на раскисление, а две трети сгорает, переходит в окись алюминия и уходит в шлак. А расход достигает в среднем 2 кг на тонну стали. Перед введением, чтобы улучшить поверхность контакта и степень усвоения, чушку приходится дробить, а это дополнительные трудозатраты.
Алюминий в виде мелких форм пуль, гранул, конусов, полусфер более эффективен, при этом расход меньше. А для введения совсем мелких форм необходимы достаточно сложные аппараты. Не так давно на рынке появились прессованные таблетки или брикеты из более дешевого сырья, то есть дробленые банки, стружка. Обладая малой плотностью, эти брикеты быстрее всплывают и дают еще меньшую степень усвоения алюминия.
В последнее время предприятиями черной металлургии все более широко используется катанка. Использовать ее для раскисления не только более технологично, но и гораздо выгоднее с финансовой точки зрения. При расходе чушки от 0,5 кг до 2,5 кг на тонну стали затраты на раскисление составляют от 0,8 до 4 долл. При использовании катанки расход может быть в 23 раза меньше. В среднем экономия может достичь 1 долл./т выпускаемой стали. Значит, на каждый 1 млн т стали наши коллеги из черной металлургии, используя катанку, могут дополнительно получать до 1 млн долл. прибыли.
|
| |
|
текущий номер

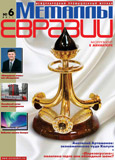
предыдущий номер

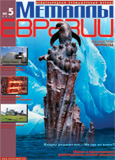
|
|