|
|
Журнал |
|
Архив |
|
Подписка |
|
Реклама |
|
САММИТ |
|
Книжная полка |
|
Контакты |
|
В начало |
|
|
|
| |
|
|
 |
№4' 2004 |
версия для печати
|
|
ТРИ ВЕКТОРА МОДЕРНИЗАЦИИ |
|
Михаил Аршанский
Директор НТМК по перспективному развитию
еконструкция Нижнетагильского металлургического комбината вступает в решающую стадию. Сейчас на комбинате идет второй этап комплексной модернизации производства. В целом программа обновления, утвержденная советами директоров ОАО «НТМК» и управляющей компании «ЕвразХолдинг», рассчитана да 2009 года. Инвестиционные проекты комплексно развивают все металлургические и сопутствующие переделы предприятия. Программа направлена на то, чтобы превратить НТМК в одно из самых современных, рентабельных и успешно работающих металлургических подразделений холдинга.
В своей основе программа предусматривает реконструкцию существующих и в меньшей степени строительство новых производств. Модернизация охватывает доменный, сталеплавильный и прокатный переделы. Кроме того, существенно укрепляется энергетическая база: в скором времени НТМК сможет самостоятельно генерировать 60-70% потребляемой энергии. Обновление затронет и другие вспомогательные производства: железнодорожный транспорт, ремонтные цеха и ряд других.
Как известно, НТМК выпускает большое количество транспортного металла: железнодорожные рельсы, колеса, бандажи, заготовки для железнодорожных осей, профили для вагоностроения и так далее. Это - металл ответственного значения и к нему предъявляются особые требования. Исходя из этого, программа реконструкции предусматривает существенное повышение качества стали.
Все инвестиционные проекты нацелены на достижение серьезного экономического эффекта: они обеспечены финансированием и должны окупиться в сравнительно ограниченные сроки, после чего начнут приносить прибыль.
Во второй половине 2004 года на НТМК должны вступить в строй сразу несколько крупных объектов. В доменном цехе состоится пуск печи №6, в кислородно-конвертерном вводится в строй МНЛЗ №4 в комплексе с установкой «печь-ковш», в колесо-бандажном цехе намечен пуск новой прессо-прокатной лини, а также лини механической обработки и комплекса чистового контроля качества железнодорожных колес.
Из шести доменных печей на комбинате сегодня работают пять. Программа предусматривает реконструкцию трех доменных печей. В перспективе они будут выпускать такой же объем чугуна, сколько сейчас дает весь доменный цех. Печи будут унифицированы и начнут работать по единой технологии, с однотипным оборудованием, одинаковыми параметрами, что не только улучшит работу доменного производства организационно и технологически, но также повысит ремонтопригодность оборудования. В проектах реконструкции печей заложены современные технологические и конструкционные решения, такие, как использование засыпных аппаратов лоткового типа, закрытые литейные дворы и закрытые желоба. Интеллектуальные системы управления позволят в автоматическом режиме выбирать наиболее экономичные режимы работы и оптимизировать издержки. В частности, это даст нам возможность резко снизить потребление кокса: ожидаемая экономия - до 20 кг на тонну чугуна. Благодаря надежной аспирации домен улучшится состояние воздушной среды на предприятии и в городе.
В августе будет задута доменная печь №6 одна из самых больших в Европе. Она построена фактически заново на месте домны, закрытой в 1996 году, и спроектирована по расчетам специалистов-доменщиков комбината, которые имеют уникальный опыт выплавки ванадийсодержащих чугунов из сырья Качканарского ГОКа. Такого опыта в России нет ни у кого. Оптимальный профиль печи и ряд других технических мер позволят успешно плавить в ванадийсодержащий чугун, другие тугоплавкие чугуны, которые содержат, например, титан. Кауперы конструкции российского специалиста Калугина смогут работать без ремонта до 25 лет. Причем, вместо четырех здесь построено три воздухонагревателя, что также удешевит эксплуатацию, не снижая надежности агрегатов. Примерно столько же около 20 лет должна будет работать без капитальных ремонтов и сама домна. Оборудование для нее поставляли как российские, так и западные компании: Gosha ?, Paul Wurth, Voest-Alpine. Проектная мощность шестой домны 1 730 тыс т чугуна в год. Этого достаточно, чтобы без осложнения для производственного цикла поставить на ремонт пятую доменную печь для проведения аналогичной реконструкции.
Программа обновления сталеплавильного производства предусматривает реконструкцию и увеличение производительности конвертерного цеха. Если сегодня проектная мощность ККЦ ограничена 3,5 млн т стали в год, то после модернизации его производительность вырастет до 5 млн т стали, которая вся будет разливаться непрерывным способом. Разливка в изложницы будет прекращена. Цех оснащается современными системами очистки конвертерных газов, а также рядом технических устройств (установка десульфурации, вакууматор, «печь-ковш»), которые позволят сократить время продувки и при этом получить высококачественный металл. Увеличение объема выпуска конвертерной стали и полный переход к непрерывной разливке будет сопровождаться ликвидацией устаревших производств, таких, как пять оставшихся мартеновских печей и блюминг.
В конце июня в ККЦ вступила в эксплуатацию третья установка «печь-ковш», c пуском которой НТМК приобретает наиболее современную в российской металлургии систему подготовки металла к разливке, так называемую вторичную металлургию. В составе ее три агрегата «печь-ковш», вакууматор, установка десульфурации. Таким набором современных агрегатов пока не располагает ни один металлургический комбинат в России и СНГ.
Ко дню металлурга, на пять месяцев раньше намеченного срока, заработает машина непрерывного литья заготовок, поставленная фирмой Voest-Alpine. Напомню, что этот объект рассматривается, как первая очередь будущего трубного комплекса. Одноручьевая МНЛЗ №4 будет выпускать 1,5 млн т слябов в год. Она во многом уникальна: это - машина криволинейного типа с прямолинейным кристаллизатором, секционированной опорной роликовой системой, непрерывным изгибанием, правкой заготовки и возможностью сдвоенной разливки. Технические характеристики МНЛЗ №4 и сопутствующих ей агрегатов обеспечивают получение высококачественного трубного металла.
Это - первый проект на комбинате, который реализован «под ключ» иностранной фирмой и на средства зарубежных инвесторов. За счет предоставленного кредита в сумме 86 млн евро закуплена и установлена сама МНЛЗ, приобретен агрегат «печь-ковш», а часть средств вложена в развитие необходимой инфраструктуры энергетику, ремонтное хозяйство, транспорт. За два неполных года был построен целый комплекс, который позволит комбинату в кратчайшие сроки выйти на заданные объемы производства слябов и завершить переход к непрерывной разливке.
В прокатном производстве полностью обновляется колесо-бандажный цех. В июне здесь была пущена установка контроля качества колес, включающая в себя линию ультразвукового и инструментального контроля. Установка была специально разработана и создана для колесопрокатного производства НТМК немецким институтом Фраунгоферовского общества прикладных исследований. Она позволяет проверять цельнокатанные колеса по 13-ти каналам контроля согласно требованиям ОАО «Российские железные дороги», международным стандартам, а также национальным стандартам и спецификациям таких стран, как США, Германия, Франция. Установка ультразвукового контроля включена в систему информационного сопровождения колес. Детальная информация о параметрах настройки и результатах контроля также сохраняется во внутреннем протоколе системы на весь период службы колеса. Отмечу, что все работы по сооружению новой линии велись в сотрудничестве со специалистами ОАО «РЖД». Линия УЗК способна контролировать 300 тыс. шт. колес в год. Вторая линия чистового контроля для НТМК уже готова, но будет поставлена на комбинат несколько позже.
На 31 октября в колесо-бандажном цехе намечен пуск новой прессо-прокатной линий. Помимо повышения качества, эта линия позволит увеличить объем выпуска железнодорожных колес с сегодняшних 450 тыс. шт. в год до 630 тыс.
Колесопрокатный цех НТМК первый из построенных в СССР. Ему уже более пятидесяти лет, так что реконструкция давно назрела. Стоит подчеркнуть, что цех продолжает выпускать продукцию: все работы выполняются без остановки производства колес. Благодаря тому, что в ККЦ начал работать комплекс вторичной металлургии, в колесном цехе появилась возможность закрыть большой участок, где проводилась противофлокенная обработка колес, и на его месте начать практически новое строительство.
Новую прессо-прокатную линию спроектировала фирма SMS-Eumuco (подразделение SMS-Demag) один из ведущих мировых разработчиков и производителей подобного оборудования. Проект реализуется совместно с Новокраматорским машиностроительным заводом, где по немецким проектам изготавливаются прессы. Прокатный стан делают в Германии. Параллельно строится линия механической обработки колес, которая будет оснащена станками с ЧПУ, позволяющими обрабатывать колесо полнопрофильно. Пока на НТМК могут обрабатывать лишь часть поверхности колеса.
Линия механической обработки колес сооружается в содружестве с немецкой компанией Hueller Hille. Новая линия мехобработки сможет обрабатывать 180 тыс. шт. колес в год, т.е. совместно с имеющимся парком станков обеспечит обработку колес на уровне производительности нового прессопрокатного участка 630 тыс.шт.
С пуском новой прессо-прокатной линии тагильские колеса будут значительно превосходить продукцию, выпускавшуюся на прежнем оборудовании. Появится возможность формировать колеса с любым, как традиционным, так и S-образным диском, которые сейчас наиболее востребованы. Железнодорожники получат цельнокатаное полнопрофильно обработанное, качественное колесо.
В следующие два года на НТМК пройдет второй этап коренной реконструкции производства.
В настоящее время на НТМК готовится и реконструкция рельсобалочного производства с переходом на изготовление 50-метровых рельсов, а также рельсов с более высокой твердостью, низкотемпературных, повышенной прямолинейности. Предстоит также отказаться от неэффективной, устаревшей морально и физически системы термообработки рельсов.
Срок окупаемости всех проектов, входящих в программу реконструкции НТМК, - от 3 до 6 лет с момента начала строительства. Поэтому мы считаем, что пуск агрегатов, которые вводятся в эксплуатацию в 2004 году, уже в следующем году начнет приносить прибыль комбинату и компании «ЕвразХолдинг», позволит увеличить ее капитализацию и выйти на рынки с изделиями принципиально нового качества, с высокой добавленной стоимостью
|
|
|
|
|
текущий номер

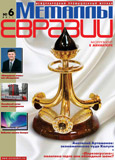
предыдущий номер

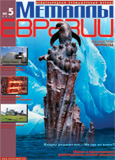
|
|