Виктор Семенов Заместитель министра путей сообщения РФ
Устойчивая работа железнодорожного транспорта во многом зависит от качества и объема рельсов, поставляемых металлургическими комбинатами. Рельсы являются наиболее дорогим элементом конструкции пути. Доля их стоимости в общем объеме работ по его капитальному ремонту составляет около 40 %. Учитывая протяженность отечественных железных дорог 124 тыс. км, их роль в народном хозяйстве, производство рельсов следует рассматривать как стратегическую задачу, обеспечивающую экономическую безопасность страны.
На путях российских железных дорог уложено около 21 млн. т рельсов. Определенное их количество ежегодно требует замены. План капитального ремонта 2000 года предусматривает сплошную замену более 4000 км рельсов на новые и более 2000 км на отремонтированные старогодные.
Отсюда вытекает первое требование к металлургическим комбинатам-производителям рельсов: неукоснительное выполнение ежемесячных объемов заказов. В 1999 году, как и в предыдущие годы, металлурги не сумели обеспечить ритмичную поставку рельсов. Хотя объем заказов железных дорог был значительно ниже производственных возможностей комбинатов, поставка рельсов с Кузнецкого металлургического комбината составила 82 % от плана, с Нижнетагильского 89 %. В отдельные месяцы производство рельсов падало до небывало низких объемов. Так, в феврале 1999 года на КМК произведено для железных дорог России только 10,9 тыс. т из запланированных 25 тыс. т, а на НТМК всего 6,4 тыс. т из 20 тыс. т. Чтобы выполнить план ремонта пути, железные дороги в отдельные месяцы были вынуждены закупать на НТМК до 10 %, а на КМК до 18 % рельсов нестандартной длины. В 2000 году поставка некондиционной продукции по-прежнему продолжается.
Потребность железных дорог России на 2000 год составляет 750 тыс. т новых рельсов. В ближайшие пять лет она останется на таком же уровне. В табл.1 показано распределение потребности в рельсах разных категорий по комбинатам-производителям с учетом их географического расположения.
Необходимо отметить, что в новых экономических условиях потребность железных дорог в получении рельсов будет определяться много строже, чем 20 лет назад. Не может быть и речи о возврате к старым цифрам ежегодных заказов на рельсы порядка 2 млн. т, о которых вспоминают А. Дерябин и Л. Смирнов в статье "Деньги на рельсы!" ("Металлы Евразии", №3, 2000 г.). Снижение ежегодных закупок связано с уменьшением грузооборота, увеличением объемов укладки старогодных рельсов после их реновации на рельсосварочных предприятиях МПС и необходимостью строгой экономии материальных средств для обеспечения рентабельности железнодорожного транспорта.
Экономическая целесообразность приведет в недалеком будущем к дифференцированному использованию рельсов в зависимости от плана пути, грузонапряженности участка, скорости движения поездов, климата района. Поэтому термоупрочненные рельсы (620 670 тыс. т), предназначенные для укладки при капитальном ремонте, подразделяются по их разновидностям следующим образом.
Для повышения скорости пассажирских поездов до 200 км в час на ряде направлений необходимы рельсы для скоростного движения, совмещенного с грузовым. Они должны обладать как повышенной прямолинейностью, так и достаточно высокими контактно-усталостной прочностью и износостойкостью. Ежегодная потребность в таких рельсах отечественных железных дорог, 90 % которых находится в Европейской части России, составляет 200 250 тыс. т.
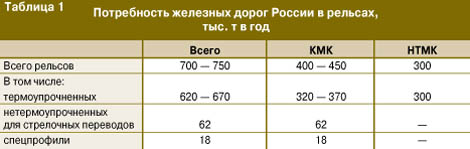
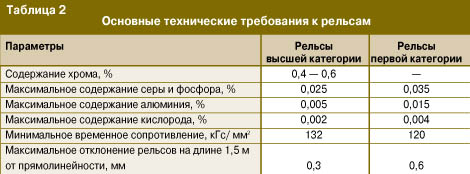 На ряде железных дорог имеются участки пути, где температура зимой опускается ниже минус 40о С. В этих условиях целесообразно укладывать специальные рельсы повышенной низкотемпературной надежности из стали с мелкозернистой структурой, получение которой обеспечивается повышенным содержанием азота, связанного в нитриды. Потребность в таких рельсах составляет 50 60 тыс. т.
В упорных нитях на кривых участках пути малого радиуса, которых особенно много на Горьковской, Куйбышевской, Свердловской, Южно-Уральской, Красноярской, Восточно-Сибирской, Забайкальской и Дальневосточной железных дорогах, нужно применять рельсы типа Р65 с измененным профилем головки и повышенной твердостью. Последнее достигается использованием заэвтектоидной стали с содержанием углерода 0,82 0,86 %. Ежегодная потребность в таких рельсах около 50 тыс. т.
Металлургическая промышленность России пока не обеспечила потребности железных дорог в рельсах повышенной прямолинейности для участков скоростного движения, а также в специальных рельсах для кривых участков пути и районов холодного климата.
Анализ показывает, что в последние три года поставки КМК и НТМК являлись недостаточными не только по количеству, но и по качеству. Объемы проката рельсов начали расти только в первом полугодии 2000 года благодаря устойчивой работе КМК.
Недостаточное соответствие рельсов условиям эксплуатации приводит к необходимости их частой замены, что требует больших затрат, вызывает задержки в движении поездов и создает значительные организационные трудности. В 1999 году на железных дорогах было изъято 107 тыс. дефектных рельсов, в том числе по дефектам контактной усталости около 17 тыс., по боковому износу более 15 тыс. и по трещинам в шейке около 5 тыс.
Еще более важной задачей является обеспечение безопасности движения поездов, для чего необходимо полностью исключить внезапные отказы в виде аварийно опасных изломов рельсов. В 1999 году 198 рельсов сломались под колесами подвижного состава, и только по счастливой случайности крушений по этой причине не было. В России железнодорожники вынуждены проводить дефектоскопный контроль рельсов на порядок чаще, чем это делается на зарубежных дорогах, для чего приходится содержать 10 тыс. человек и соответствующую дорогую технику.
Эксплуатационная стойкость рельсов определяется их структурой, неметаллическими включениями, наличием разнообразных внутренних и наружных дефектов металлургического происхождения, химическим составом, механическими свойствами, остаточными напряжениями, геометрическим качеством (прямолинейностью) и качеством механической обработки болтовых отверстий и торцев. Совокупность требований к этим параметрам и составляет содержание стандартов и технических условий на рельсы.
В настоящее время разработан проект нового единого стандарта России на рельсы высшей категории (В), термоупрочненные первой и второй категорий (Т1 и Т2) и нетермоупрочненные (Н). Отечественные металлургические комбинаты выпускают рельсы не выше первой категории качества (Т1), технические требования к которым близки действующим стандартам, и не могут производить рельсы высшей категории качества, необходимые для участков скоростного совмещенного движения. Поэтому МПС вынуждено закупать некоторое количество рельсов этой категории за рубежом. Основные технические требования к рельсам высшей и первой категории качества приведены в табл.2.
Требования к объему и качеству контроля рельсов высшей категории значительно возросли. Они должны быть подвергнуты сплошному неразрушающему контролю трех видов: на отсутствие недопустимых внутренних и наружных дефектов и на прямолинейность.
В настоящее время разработан комплект нормативно-технической документации по сертификации рельсов. Создана собственная Система сертификации всей продукции, поставляемой для Федерального железнодорожного транспорта (ССФЖТ). Рельсы производства КМК и НТМК сертифицированы в ССФЖТ. В табл.3 приведены основные показатели, определяющие эксплуатационную стойкость рельсов. Сравнение термоупрочненных рельсов производства КМК и НТМК (по качеству приблизительно одинаковых) с лучшими зарубежными образцами (японскими, французскими и др.) свидетельствует о том, что отечественные рельсы уступают по следующим параметрам:
прямолинейности (по всей длине и по концам рельсов);
качеству поверхности и отделки (торцы, болтовые отверстия, фаски);
количеству неметаллических включений и вредных примесей (сера, фосфор, водород, кислород);
прокаливаемости, обеспечивающей в зарубежных рельсах более высокий уровень твердости и прочности в зоне действия высоких контактных напряжений, а также высокую износостойкость;
остаточным напряжениям.
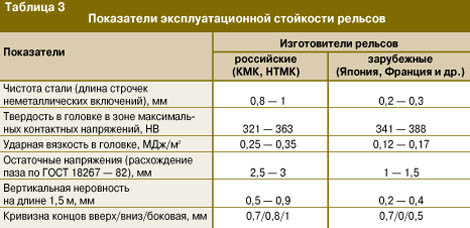 Вместе с тем зарубежные рельсы по сравнению с российскими имеют пониженную ударную вязкость, что требует более тщательного соблюдения технологии сварки. Высокие показатели качества импортных рельсов обеспечиваются благодаря наличию соответствующего оборудования. Это вакууматоры и оборудование для внепечной рафинирующей обработки жидкой рельсовой стали; современное нагревательное, прокатное и правильное оборудование, станки для механической обработки прокатных валков и отделки рельсов; установки для закалки с дифференцированным охлаждением по сечению сжатым воздухом; комплекс оборудования для сплошного контроля внутренних и поверхностных дефектов, а также прямолинейности рельсов; высокая степень компьютеризации производства.
Наиболее отчетливо преимущества лучших зарубежных рельсов перед отечественными проявились в полигонных испытаниях на Экспериментальном кольце ВНИИЖТ. Условия испытаний рельсов характеризуются следующими параметрами:
осевая нагрузка 27 т;
скорость движения поезда 65-70 км/ч;
верхнее строение пути костыльные скрепления, деревянные шпалы, гранитный щебень.
Полигонные испытания проходили многочисленные партии рельсов производства КМК и НТМК, а также рельсы завода "Хута Катовице" (1988 г., Польша), "Фест Альпине" (1987 г., Австрия), ММРА (1992 г., Люксембург), "Ниппон Стил" и "Ниппон Кокан" (1985 г., Япония), "Сожерай" (1992 г., Франция). В настоящее время на Экспериментальном кольце ВНИИЖТ проходят повторные полигонные испытания рельсы двух японских заводов и "Фест Альпине" (после проведенной там реконструкции). Впервые испытываются рельсы производства "Сидней Стил" (Канада). Полигонные испытания показали, что 80 %-ный ресурс лучших партий рельсов отечественного производства был равен 500 млн. т пропущенного груза брутто. Этот же показатель для лучших партий рельсов производства заводов "Ниппон Стил" (Япония) и "Сожерай" (Франция) был равен 1000 млн. т груза брутто. Такое отставание отечественных производителей вызвано тем, что в 80 90-х годах ведущие зарубежные фирмы провели коренную реконструкцию сталеплавильных и рельсопрокатных цехов, а комплексное обновление на отечественных металлургических комбинатах далеко от завершения.
По-настоящему крупными мероприятиями по реконструкции рельсового производства на российских металлургических комбинатах было: освоение производства термоупрочненных рельсов (НТМК в 1966 г., КМК в 1979 г.) и освоение производства рельсов из кислородно-конвертерной стали путем непрерывной разливки с вакуумированием части плавок (НТМК в 1997 г.). При этом железнодорожников беспокоит, что НТМК за прошедшие три года не наращивал производство рельсов из кислородно-конвертерной стали, а, наоборот, снижал его (табл. 4).
В соответствии с рекомендациями Межведомственной рельсовой комиссии на металлургических комбинатах был проведен ряд других полезных мероприятий. Так, в 70-е годы на КМК и НТМК было освоено производство рельсов без крупных скоплений глинозема и внедрен сплошной неразрушающий ультразвуковой контроль внутренних дефектов в проекции шейки. В последние годы на КМК в связи с увеличением дефицита ванадийсодержащих сплавов разработана и освоена технология выплавки рельсовой стали повышенной чистоты, раскисленной кальцийсодержащими сплавами и алюминием без использования ванадия (так называемые рельсы СВ).
В последние годы в России предприняты попытки выпустить опытные партии рельсов для скоростного совмещенного движения. На КМК усовершенствована технология правки термоупрочненных рельсов и разработано оригинальное устройство "Элекон" для контроля прямолинейности, что позволяет получать путем отбора некоторое количество рельсов с отклонениями от прямолинейности менее 0,3 мм на базе 1,5 м по всей длине рельсов и концевой прямолинейностью, приближающейся к требуемой. В 1999 году КМК поставил первые 3,1 тыс. т таких рельсов на Московскую железную дорогу. На НТМК прокатана опытная партия нетермоупрочненных рельсов из низколегированной стали. Отсутствие термоупрочнения позволяет при этом улучшить прямолинейность рельсов и исключить искривленность концов вниз за счет введения концевой обрези каждого рельса, а легирование рельсовой стали 0,5 % хрома обеспечивает необходимое повышение износостойкости и сопротивления контактной усталости.
Можно поэтому констатировать, что появление на железных дорогах России небольшого количества импортных рельсов высшего качества заметно ускорило процесс создания отечественных рельсов, у которых показатель, связанный с прямолинейностью по длине и концевой искривленностью, уже приближается к требованиям лучших мировых стандартов. При этом железнодорожники надеются, что металлурги понимают: по всем остальным критериям отечественные рельсы еще значительно уступают лучшим зарубежным аналогам.
Рельсы высшего качества не могут производиться из мартеновской стали. Она должна быть выплавлена в кислородных конвертерах или электропечах, подвергнута внепечной обработке, которая обеспечит однородность химического состава и высокую чистоту по неметаллическим включениям, отсутствие флокенов. Необходимы внедрение вакуумирования для всего объема рельсовой стали, переход на непрерывную разливку. Должен быть существенно повышен уровень компьютеризации управления и контроля за всеми операциями выплавки и разливки. Прокатка рельсов из непрерывнолитых заготовок должна начинаться с нагрева в методической печи с шагающими балками.
На НТМК намеченные еще на 1995 1996 годы работы по реконструкции печного участка в рельсобалочном цехе со строительством нагревательной печи с шагающими балками весьма затянулись. На КМК подобные работы пока вообще не ведутся. Ввод в действие печей прецизионного нагрева позволит внедрить гидросбив окалины при прокатке, что существенно улучшит чистоту поверхности рельсов, а также позволит пересмотреть всю калибровку. Требуется срочное обновление парка вальцетокарных станков для точной калибровки валков обжимных и рельсопрокатных станов. Весьма перспективным представляется применение универсальных клетей на последних стадиях прокатки рельсов.
Требуется разработать и внедрить более прогрессивную и гибкую технологию термической обработки рельсов взамен применяемой в настоящее время объемной закалки в масле. При анализе существующих за рубежом технических решений наиболее перспективной представляется закалка рельсов с прокатного нагрева с двусторонним дифференцированным охлаждением сжатым воздухом или водой, обеспечивающим получение достаточно прямых рельсов перед холодной правкой. Последняя должна производиться на новых роликоправильных машинах с большим, чем на существующих, числом валков. Правка должна обеспечивать получение не только прямолинейных рельсов, но и рельсов с благоприятной эпюрой остаточных напряжений. Наряду с внедрением новых роликоправильных машин, комбинаты необходимо оснастить гидравлическими прессами для правки рельсов в двух плоскостях без кантовки с лазерным технологическим измерителем величины и профиля местных неровностей.
Кардинального обновления требует оборудование для механической обработки и отделки термоупрочненных рельсов. Здесь и переход от фрезерования торцев к чистовой разрезке на агрегатных сверлильно-отрезных станках типа станков фирмы "Вагнер", и создание оборудования для упрочнения болтовых отверстий методами поверхностной пластической деформации, и внедрение нового оборудования для маркировки рельсов.
Cовершенно недостаточен на отечественных металлургических комбинатах объем сплошного неразрушающего контроля рельсов. Он сводится к ультразвуковому контролю внутренних дефектов только в проекции шейки, не распространяясь на концевые зоны рельсов. В перспективе каждый из рельсов должен быть подвергнут в производстве, по крайней мере, трем видам неразрушающего контроля: ультразвуковому на внутренние дефекты по всему поперечному сечению, токовихревому на поверхностные дефекты и лазерному на прямолинейность.
Таким образом, для участков скоростного совмещенного движения, кривых участков пути, а также малообслуживаемых участков, расположенных в зонах холодного климата, российским железным дорогам нужны рельсы повышенной прямолинейности с местными неровностями не более 0,3 мм на длине 1,5 м, с нулевыми концевыми искривлениями вниз и не превышающими 0,5 мм прогибами вверх. Для обеспечения необходимого уровня сопротивления контактной усталости и боковому износу эти рельсы должны быть изготовлены из чистой стали (содержание кислорода в ней не должно превышать 0,002 %, алюминия 0,005 %, серы и фосфора 0,025 %) и подвергнуты термическому упрочнению на большую глубину. При этом содержание хрома в рельсовой стали должно составлять 0,4 0,6 %, твердость на глубине вплоть до 10 15 мм должна составлять НВ 370 390, временное сопротивление не менее 130 кгс/мм2.
В сложившихся условиях МПС считает целесообразным разработать и реализовать программу реконструкции рельсового производства Кузнецкого и Нижнетагильского металлургических комбинатов с определением источников ее финансирования. Она может быть поэтапной, но обязательно комплексной, поскольку только в этом случае возможно получение максимального эффекта от капиталовложений. Эта программа должна иметь статус целевой федеральной.
Железнодорожники ждут от металлургов действительно лучших в мире рельсов.
|