Анатолий Каблуковский, Яков Кац, Александр Усачев ГНЦ РФ "ЦНИИчермет им. И.П. Бардина", АО "Стальпроект"
При росте мощностей по выплавке стали в мире (более 1 млрд. т в 1997 г.) потребление стальной металлопродукции в 1998 году начало падать (рис. 1). За 1998 год снижение объемов мировой торговли сталью составило приблизительно 10 млн. т, а экспорт из России упал по сравнению с 1997 годом примерно на 3 млн. т до 24,4 млн. т. Складывающаяся ситуация на мировом рынке стальной металлопродукции привела к резкому обострению конкурентной борьбы на рынках стран-импортеров, выразившейся в многочисленных антидемпинговых процессах против компаний производителей стали из России, Японии, Республики Корея и др.
Ужесточение конкуренции в мировой торговле стальной металлопродукцией приводит к уменьшению прибыльности компаний производителей во всем мире. Так, за 1998 год доходы сталелитейных компаний США снизились примерно на 20 %, а в 1999 году предполагается снижение еще на 4 %. Цены акций этих компаний снизились за тот же период в среднем на 22 %. Результаты деятельности крупнейших российских сталеплавильных компаний в прошедшем году также ухудшились. НЛМК снизил объемы производства стального проката на 13,6 %, "Северсталь" на 2,9 %, "НОСТА" на 7,7 %, ОЭМК на 5,5 %. В целом производство проката в России снизилось по сравнению с 1997 годом на 10,8 %.
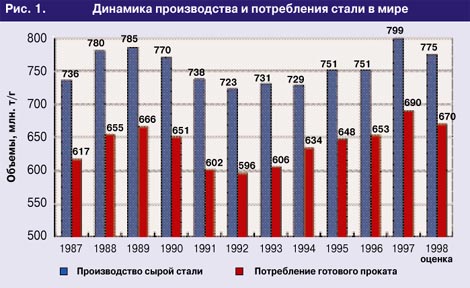 Для поддержания конкурентоспособности на рынке в условиях ужесточающейся конкуренции компании стремятся минимизировать издержки, в том числе и производственные затраты. Применение средств внепечной обработки стали открывает перед российскими компаниями производителями стального проката широкие возможности по снижению себестоимости продукции и увеличению доходности бизнеса. Резервы большие: многократно было констатировано, что энерго- и материалоемкость российской стальной продукции в среднем в 1,5 2 раза выше, чем ее западных аналогов.
I
Современная технология производства стали основывается на трех основополагающих принципах: темп, точность, стабильность.
Темп проведения всех операций в цикле сталеплавильного производства определяется производительностью машин непрерывного литья заготовок (МНЛЗ) наиболее производительных в настоящее время агрегатов. Скорость разливки на МНЛЗ за 20 лет увеличилась примерно в 2 раза и достигает на современных машинах 1,2 м/мин. Основополагающей причиной увеличения скорости непрерывной разливки является необходимость повышения производительности из-за очень высокой капиталоемкости сталеплавильного производства (т.е. снижения доли так называемых условно-постоянных затрат). По разным оценкам, удельные капитальные затраты в сталеплавильном производстве полного цикла составляют 900 1200 долл./т, а при производстве проката на мини-заводах 400 600 долл./т. Для повышения производительности сталеплавильных агрегатов увеличивают их единичную емкость (кислородных конвертеров до 400 т, а дуговых сталеплавильных печей до 250 т), удельную мощность трансформатора при электроплавке (до 1000 кВт.ч/т), интенсифицируют режим кислородной продувки при конвертировании чугуна, а также уменьшают количество технологических операций, проводимых в каждом из агрегатов.
Современная концепция технологии сталеплавильного передела предусматривает, что в сталеплавильном агрегате проводятся расплавление твердой шихты, окислительные обезуглероживание и дефосфорация расплава и нагрев ванны до температуры, обеспечивающей выпуск полупродукта в сталеразливочный ковш и передачу его на агрегат внепечной обработки. При конвертировании чугуна время выплавки полупродукта составляет около 30, а задолженность кислородного конвертера 35 45 мин (с учетом вспомогательных операций). При выплавке в ДСП время плавки составляет 40 55 мин, а задолженность дуговой печи 45 60 мин. Операции раскисления, легирования, восстановительного рафинирования, корректировки химического состава и температуры, а также глубокого рафинирования от углерода в вакууме и некоторые другие проводятся вне сталеплавильного агрегата в процессе внепечной обработки. Для соблюдения темпа сталеплавильного передела в целом и отдельных его стадий минимизируют длительность пребывания плавки на каждом из агрегатов. Для этого такие операции, как ожидание результатов химического анализа расплава, наведение шлака, гомогенизация расплава, совмещают с перемещением ковша с плавкой. При такой организации технологии важно, чтобы на каждой стадии имелась возможность скорректировать результаты процессов, проводимых на предыдущей стадии.
Результатом изложенной выше организации сталеплавильного передела является снижение времени обработки плавки на каждом из агрегатов внепечной обработки до 20 30 мин для синхронизации всех стадий с выплавкой полупродукта и непрерывной разливкой стали.
Развитие металлургической техники и технологии в последние 10 15 лет позволило существенно сузить диапазон колебаний содержания всех компонентов стали, как примесных, так и полезных. Причем в отечественных сталях обычно разброс содержания элементов выше, чем в зарубежных. Так, если в стали 3СП по ГОСТ 380 содержание углерода может изменяться в пределах 0,14 0,22 %, то в стали А36 по ASTM в диапазоне 0,16 0,22 %; в стали 20 по ГОСТ 1050 - в диапазоне 0,17 0,24, а в ее аналоге стали А29 по ASTM 0,18 0,23. Также следует учитывать, что зарубежные стандарты, в отличие от российских, выполняют только информативную функцию. Конкретный состав стали оговаривается отдельно в рамках каждого контракта, исходя из назначения металла, и в подавляющем числе случаев эти требования являются более жесткими, чем требования стандартов. Повышение точности попадания в заданный состав стали и сужение диапазона допустимых содержаний компонентов позволяют снизить расход дорогостоящих ферросплавов, уменьшить количество используемых шлакообразующих, оптимизировать режимы термообработки, увеличить точность предсказания эксплуатационных характеристик изделий из стали и, следовательно, уменьшить вес металлоконструкций и, значит, - расход стали при их изготовлении. Также существенно повысилась точность регулирования температуры жидкой стали перед непрерывной разливкой. Отклонение температуры расплава от заданных значений в промежуточном ковше МНЛЗ в ±7 ОС является обычной практикой, а некоторые новые технологии внепечной обработки, применяемые в промышленных масштабах, позволяют достигать точности ±2,5 ОС.
Важным достижением техники и технологии внепечной обработки в последнее десятилетие является высокая надежность получения необходимого результата в сталеплавильном производстве. Это обеспечивается как специальной организацией технологических операций, так и широким использованием средств автоматизации. Количество слитков, отбракованных по химическому составу, на современных предприятиях составляет 0,1 0,2 %, тогда как в 60-е годы такой брак составлял 1 2 %. Брак по температуре жидкой стали перед и в процессе непрерыной разливки, что еще имеет место на отечественных предприятиях, вообще не допускается. Причиной этого являются очень большие финансовые потери от простоя МНЛЗ. Так, по данным корпорации Nucor Steel, США, аварийное прерывание разливки на заводе в Норфоксе на один час приводит к потерям в 40 тыс. долл.
На основании сказанного выше можно сформулировать общую задачу внепечной обработки: обеспечить получение химического состава и температуры жидкой стали в заданных пределах за требуемое время (20 40 мин) с минимально возможными затратами.
II
Промышленное использование установок для внепечной обработки началось в начале 50-х годов. За прошедшие 45 лет было разработано большое количество способов и оборудования для их реализации, и этот процесс развития и совершенствования продолжается в настоящее время. Расширение масштабов применения средств внепечной обработки при производстве стали имеет место вплоть до настоящего времени. Например, количество стали, подвергнутой вакуумированию, растет более быстрыми темпами, чем ее суммарное мировое производство: в 1998 году ее доля составила около 9 % т, а в 2010 прогнозируется более 27 %. Если в первые десятилетия внепечная обработка применялась только при производстве высококачественных сталей, то в настоящее время средства вторичной металлургии используются при производстве всех сталей без исключения. Все вновь возводимые электросталеплавильные заводы обязательно имеют в своем составе установки "ковш-печь" (УКП). В настоящее время в мире эксплуатируется около 250 таких установок. При реконструкции действующих предприятий производители стали устанавливают агрегаты для внепечной обработки. Так, в сентябре 1998 года Voest-Alpine Industrieanlagenbau (VAI) объявила о начале расширения участка внепечной обработки в кислородно-конвертерном цехе № 3 завода Voest-Alpine Stahl в Линце. Программа реконструкции предусматривает установку второго вакууматора RH фирмой Tehnometal и второго агрегата "ковш-печь" фирмой Fuchs. Новое оборудование должно быть введено в эксплуатацию в марте 2000 года. Во втором квартале 2000 года также должен быть запущен новый завод фирмы Steel Dinamics Inc. в Whitley Country, штат Индиана, США. Сооружаемый фирмой Mannesmann Demag Corp. завод будет состоять из двух 120-тонных дуговых печей с трансформаторами по 120 mva и эксцентрическим донным выпуском стали и водоохлаждаемыми стеновыми панелями. Печи оснащаются кислородными горелками и фурмами для вдувания пылеугольного топлива в токе кислорода и для дожигания газов в подсводовом пространстве. Полный цикл плавки должен составить 48 мин. В сталеплавильном отделении также будут установлены два агрегата "ковш-печь" с трансформаторами мощностью по 22 mva, оснащенные системой весодозирования ферросплавов, системой продувки расплава аргоном и введения порошковой проволоки.
Германский концерн Schloemann-Siemag Aktiengesellschaft (SMS AG) в феврале текущего года ввел в опытную эксплуатацию 400-тонную установку "ковш-печь" в новом комплексе по производству горячекатаного листа на заводе в Дуйсбург-Брукхаузене фирмы Tissen-Krupp Stahl AG. УКП установлена в кислородно-конвертерном цехе с двумя 400-тонными кислородными конвертерами, двумя стендами для продувки плавки в ковше аргоном и вакууматором. Для синхронизации выплавки и непрерывной разливки специалистами SMS AG была выбрана двухпозиционная схема внепечной обработки на УКП, что позволило сократить такт непрерывной разливки в серии с 40 до 30 мин. Номинальная мощность трансформатора УКП 50 mva, что, по мнению германских специалистов, обеспечит нагрев 400-тонной плавки со скоростью не менее чем 4 ОС/мин. Заказ на поставку УКП был выдан заказчиком 13 марта 1998 года, а 28 февраля 1999 года начались горячие испытания.
Из-за уже упоминавшегося снижения прибыльности производства стального проката большинство зарубежных металлургических компаний в ходе реорганизации и оптимизации бизнеса ликвидировало свои научно-исследовательские подразделения. Новые процессы, технологии и оборудование для их реализации в настоящее время разрабатываются фирмами, являющимися поставщиками оборудования и технологий на сталеплавильные предприятия. Однако и фирмы поставщики оборудования для сталеплавильщиков также реструктурируются. Общее направление в большинстве случаев заключается в расширении охвата металлургических переделов и концентрации финансовых и интеллектуальных ресурсов на конкретных проектах.
Так, концерн SMS AG поставил своей целью обеспечить оборудованием и технологиями весь технологический цикл производства стального проката, начиная от доменной плавки и заканчивая финишными стадиями прокатки. Очевидно, что реализация такой стратегии требует некоторых серьезных корпоративных решений, одним из которых явилось фактическое приобретение концерном SMS AG сталеплавильного дивизиона Mannesmann-Demag AG, известного производителя оборудования для выплавки стали в электродуговых печах и ее внепечной обработки. В результате слияния, соглашение о котором было подписано 12 декабря 1998 года, образовано совместное предприятие SMS Demag AG, 72 % капитала в котором принадлежит SMS AG, а 28 % Mannesmann-Demag AG. Несколько лет назад концерн начал контролировать известного разработчика технологий и оборудования для вакуумирования стали фирму Vacmetal. Результатом двухлетних работ в этом направлении явилась разработка современной конструкции вакууматора циркуляционного типа, обозначенного как RD. Концепция вакууматоров RD включает увеличение диаметра вакуум-камеры относительно ее высоты для увеличения производительности, замену графитового нагревателя для подогрева футеровки на газокислородные горелки, использование кислородной фурмы для интенсификации обезуглероживания металла, уменьшение количества вакуум-плотных фланцев и замена их на сварные конструкции для ускорения операции по замене вакуум-камеры при текущих ремонтах футеровки.
Таким образом SMS AG становится одним из крупнейших в мире разработчиков и поставщиков оборудования и технологий для всего цикла сталеплавильного производства.
Аналогичную стратегию реализует австрийский концерн VAI. Около двух лет назад он приобрел крупный пакет акций фирмы Fuchs разработчика и поставщика дуговых сталеплавильных печей и установок "ковш-печь". В отличие от SMS, VAI имеет в своей структуре и сталеплавильный завод в Линце.
Западными фирмами также разрабатываются новые схемы внепечной обработки стали. Так, примерно с середины 80-х годов ряд фирм производителей стали начал эксперименты по электродуговому подогреву стали в промковше МНЛЗ в процессе непрерывной разливки. К середине 90-х годов уже эксплуатировалось около 20 таких установок. При дуговом подогреве стали в промковше удается стабилизировать температуру с точностью от 4 до 2,5 ОС, снизить температуру разливки на 10 20 ОС, улучшить качество непрерывно-литой заготовки, увеличить скорость разливки, снизить сквозной расход энергоресурсов на производство заготовки. Идеальным тепловым условием внепечной обработки является поддержание постоянной температуры плавки в ковше от момента завершения выпуска стали из плавильного агрегата до окончания разливки стали на МНЛЗ. Это возможно только при отсутствии теплопотерь сталью в стальковше. Приближением к такой идеальной схеме является использование промежуточных подогревов стали не только в стальковше, но и промковше МНЛЗ, т.е. увеличение количества нагревов снижает суммарные теплопотери при внепечной обработке (рис. 2). Экономический эффект от применения такой технологии подогрева стали в процессе внепечной обработки и непрерывной разливки иллюстрируют результаты, полученные фирмой Nucor Steel, США, в электросталеплавильном цехе № 1 завода в Норфоксе. За 1994 год на МНЛЗ с подогревом в промковше было разлито 372,6 тыс. т стали. Эксплуатационные затраты на плазменно-дуговой подогрев за этот период составили 132,6 тыс. долл. Экономия только вследствие уменьшения температуры разливки стали на 10 ОС составила немногим менее 190 тыс. долл. благодаря снижению расхода электроэнергии, электродов и огнеупоров.
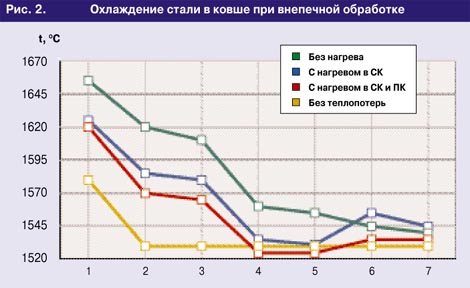 Альтернативой использованию установок "ковш-печь" для нагрева плавки в ковше является так называемый "химический подогрев". В 1982 году на одном из заводов фирмы Nippon Steel (Япония) был осуществлен подогрев стали за счет химического тепла реакции между газообразным кислородом и алюминием. Процесс получил название CAS-OB (Composition Adjusment by Sealed Argon Oxigen Blow). На заводе фирмы Weirton Steel Corp. в Великобритании на такого типа установке обрабатывают 365-тонные плавки в кислородно-конвертерном цехе. Достигнута очень высокая скорость нагрева (10 20 ОС/мин), которая регулируется скоростью подачи кислорода.
В начале 80-х годов в промышленно развитых странах получил распространение способ введения в жидкую сталь реагентов, упакованных в стальную оболочку, в виде так называемой "оболочковой" (от английского cored wire) или "порошковой" проволоки. Эта технология внепечной обработки стали, применяемая для ввода высокореактивных элементов (Ca, Mg, Ti, РЗМ и др.), позволяет существенно повысить точность дозирования, увеличивать степень их усвоения сталью, получить высокую воспроизводимость результатов микролегирования и модифицирования. Такую проволоку вводят не только в расплав в стальковше, но и в промковш и даже в кристаллизатор при непрерывной разливке. По разным оценкам, в мировой черной металлургии используется 40 60 тыс. т порошковой проволоки в год.
III
Оснащенность отечественных сталеплавильных компаний оборудованием для внепечной обработки существенно разнится. Компании, расположенные в европейской части России и успешно реализующие экспортные программы, имеют в составе сталеплавильных цехов весь необходимый набор средств внепечной обработки. Это электросталеплавильный цех ОЭМК, 1-й кислородно-конвертерный цех НЛМК, электросталеплавильный цех "Северстали". Причем парк оборудования для внепечной обработки в этих цехах существенно обновился после 1990 года. Аналогичные немногочисленные агрегаты, введенные в эксплуатацию во времена плановой экономики, морально устарели и физически изношены, поэтому не могут обеспечить экономически эффективного производства стали. Так, отечественные вакууматоры, установленные в 70 80-х годах в ККЦ "Мечел", на ММК и в электросталеплавильном цехе "НОСТА", практически не используются из-за неудовлетворительных эксплуатационных параметров.
Мартеновские цехи российских компаний в подавляющем большинстве не имеют средств для внепечной обработки металла.
До 1990 года на предприятиях России, выплавляющих сталь, действовала только одна УКП на Ижорских заводах. По состоянию на март 1999 года в России эксплуатируются уже 12 таких установок (табл. 1). Также реализуются контракты по созданию двух таких установок в ККЦ ММК и второго в электросталеплавильном цехе "НОСТА".
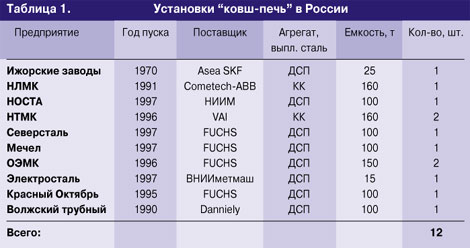 Как можно видеть из таблицы, подавляющее большинство установок "ковш-печь" (10 из 12) для российских компаний было поставлено зарубежными фирмами. Связано это, по нашему мнению, с рядом причин, главная из которых отсутствие в России организации, имеющей технические и финансовые возможности поставлять крупные агрегаты внепечной обработки "под ключ" и опыт коммерческой деятельности на специфическом рынке сталеплавильного оборудования.
Внедрение технологии ввода реагентов в порошковой проволоке в сталеплавильное производство России до середины 90-х годов сдерживалось отсутствием оборудования для ее изготовления и ввода в жидкую сталь. Эти вопросы были в течение последних шести лет успешно решены силами творческого коллектива ГНЦ "ЦНИИчермет", Магнитогорской горно-металлургической академии, МГТУ им. Н.Э. Баумана, ЦНИИТмаша, Чепецкого механического завода (ЧМЗ), "Северстали", Череповецкого сталепрокатного завода (ЧСПЗ), Магнитогорского и Западно-Сибирского металлургических комбинатов, а также ОЭМК.
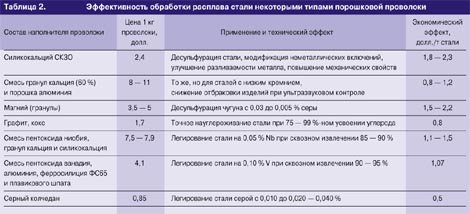 На предприятиях России был создан производственный комплекс для выпуска более 10 тыс. т в год оболочковой порошковой проволоки и агрегатов для ее применения при внепечной обработке стали и чугуна. Разработаны отечественные конструкции и изготовлены промышленные линии прокатно-волочильных станов, позволяющие изготовлять порошковую проволоку диаметром от 8 до 16 мм из холоднокатаной ленты стали 08КП, 08ПС с фальцевым замком в бухтах массой 800 1200 кг и внутренней размоткой витков в соответствии с требованиями ТУ 14-1-4923 90. На ЧМЗ организовано производство отечественных трайб-аппаратов, не уступающих известным зарубежным аналогам. Трайб-аппараты конструкции ЧМЗ установлены в сталеплавильных цехах "Северстали", ОЭМК, "НОСТА", "Мечел", НЛМК и др. Созданные на ЧМЗ мощности позволяют изготовлять до 30 трайб-аппаратов в год десяти различных модификаций, разработанных с учетом специфических условий работы сталеплавильных цехов. По техническим и качественным характеристикам отечественная порошковая проволока и трайб-аппараты соответствуют мировым стандартам, и сейчас проводится работа по их сертификации за рубежом. В настоящее время ЧМЗ, ЧСПЗ, "ТЕНАКС" (г. Ногинск) выпускают порошковую проволоку с силикокальцием, алюмокальцием, магнием, смеси магния с кальцием, графитом, титаном, серным колчеданом и др. ЦНИИчерметом также созданы новые виды наполнителей порошковой проволоки из оксидов ниобия или ванадия с восстановителями, позволяющие осуществить прямое микролегирование стали ниобием или ванадием в процессе внепечной обработки. Составы этих наполнителей и технология обработки металла защищены отечественными патентами. Частичная замена ферросплавов на оксидно-восстановительные смеси, вводимые в сталь в виде порошковой проволоки, обеспечивает снижение расходов энергетических и материальных ресурсов при внепечной обработке. В настоящий момент отечественные производители порошковой проволоки могут производить проволоку с любыми веществами-наполнителями фракцией не более 2,5 мм, представляющими интерес для ввода в жидкую сталь и получения новых качественных характеристик металла. Некоторые данные об экономической эффективности использования порошковой проволоки при внепечной обработке приведены в табл. 2.
|